Introduction
Surface Mount Technology (SMT) has revolutionized the electronics manufacturing industry by enabling the production of smaller, faster, and more reliable electronic devices. One of the critical components in the SMT assembly process is the SMT Stencil, which plays a crucial role in ensuring the accuracy and consistency of solder paste deposition on printed circuit boards (PCBs). This article will explore the various benefits of using SMT stencils in the electronics manufacturing process.
What is an SMT Stencil?
An SMT stencil is a thin, flat sheet of metal or polyester with precisely cut apertures that correspond to the pads on a PCB. The stencil is placed over the PCB, and solder paste is applied using a squeegee, forcing the paste through the apertures and onto the pads. The stencil ensures that the correct amount of solder paste is deposited on each pad, creating a consistent and reliable solder joint.
Types of SMT Stencils
There are two main types of SMT stencils: metal and polyester.
- Metal Stencils:
- Typically made from stainless steel or nickel alloys
- Offer high durability and precision
-
Suitable for high-volume production and fine-pitch components
-
Polyester Stencils:
- Made from a thin, flexible polyester film
- Lower cost compared to metal stencils
- Ideal for prototyping and low-volume production
Benefits of Using SMT Stencils
1. Improved Solder Paste Deposition Accuracy
One of the primary benefits of using an SMT stencil is the improved accuracy of solder paste deposition. The precisely cut apertures in the stencil ensure that the correct amount of solder paste is applied to each pad on the PCB. This accuracy is crucial for achieving reliable solder joints and preventing defects such as bridging, insufficient solder, or solder balls.
2. Increased Consistency and Repeatability
SMT stencils enable consistent and repeatable solder paste deposition across multiple PCBs. By using the same stencil for a given PCB design, manufacturers can ensure that each board receives an identical amount of solder paste on the pads. This consistency is essential for maintaining high product quality and reducing the risk of defects.
3. Enhanced Production Efficiency
Using SMT stencils can significantly improve production efficiency by reducing the time and effort required for solder paste application. Without a stencil, the solder paste would need to be applied manually or using a dispensing system, which is time-consuming and prone to errors. SMT stencils allow for the rapid and accurate application of solder paste, enabling faster throughput and higher production volumes.
4. Cost Savings
Implementing SMT stencils in the electronics manufacturing process can lead to cost savings in several ways:
- Reduced solder paste consumption: The accurate solder paste deposition achieved with stencils minimizes waste and optimizes solder paste usage.
- Fewer defects and rework: The consistency and accuracy provided by stencils result in fewer solder-related defects, reducing the need for costly rework and repair.
- Increased production speed: The improved efficiency offered by stencils allows for faster production rates, reducing overall manufacturing costs.
5. Compatibility with Diverse Component Sizes
SMT stencils are compatible with a wide range of component sizes, from large chips to fine-pitch components. The aperture size and shape can be customized to match the specific requirements of each component, ensuring optimal solder paste deposition. This versatility makes SMT stencils suitable for various PCB designs and applications.
6. Facilitates Automated SMT Assembly
SMT stencils are an essential part of automated SMT assembly lines. The stencil is integrated into the solder paste printing machine, which automatically aligns the stencil with the PCB and applies the solder paste. This automation further enhances the accuracy, consistency, and speed of the assembly process, enabling high-volume production with minimal human intervention.
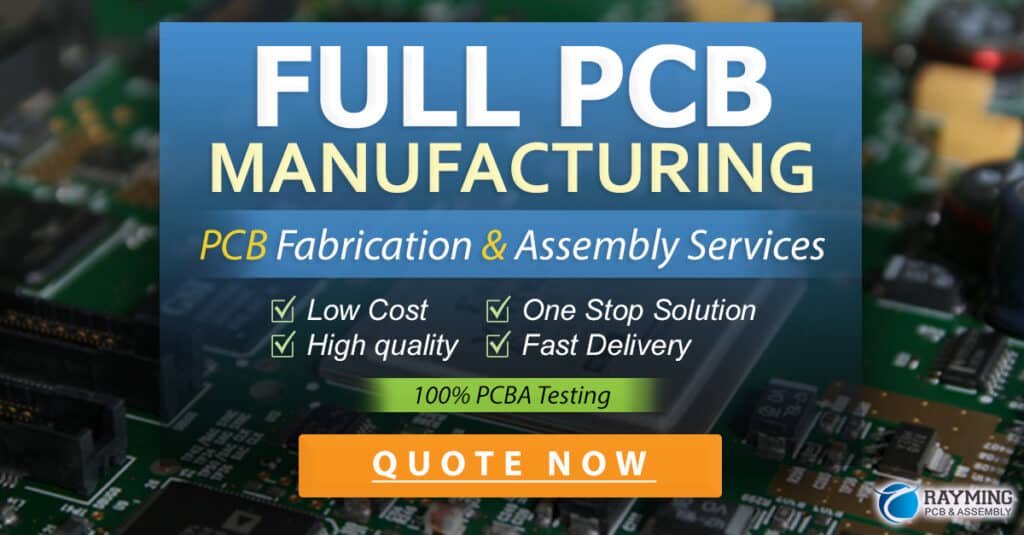
Stencil Design Considerations
To maximize the benefits of SMT stencils, it is essential to consider several factors during the stencil design process:
1. Aperture Size and Shape
The size and shape of the apertures in the stencil should be optimized based on the component pads and the desired solder paste volume. Factors such as pad size, pitch, and solder paste rheology should be taken into account when determining the appropriate aperture dimensions.
2. Stencil Thickness
The thickness of the stencil directly affects the amount of solder paste deposited on the pads. Thicker stencils deposit more solder paste, while thinner stencils deposit less. The optimal stencil thickness depends on the component size, pitch, and the required solder joint profile.
3. Stencil Material
The choice of stencil material depends on the specific requirements of the manufacturing process. Metal stencils offer high durability and precision, making them suitable for high-volume production and fine-pitch components. Polyester stencils, on the other hand, are more cost-effective and ideal for prototyping and low-volume production.
4. Aperture Walls and Edges
The quality of the aperture walls and edges in the stencil can impact the release of solder paste during the printing process. Smooth aperture walls and tapered edges facilitate better solder paste release, reducing the risk of clogging and ensuring consistent deposition.
Stencil Maintenance and Cleaning
To ensure consistent performance and long-term durability of SMT stencils, proper maintenance and cleaning practices should be implemented:
1. Regular Inspection
Stencils should be regularly inspected for signs of wear, damage, or contamination. Any issues should be addressed promptly to prevent them from affecting the solder paste deposition process.
2. Cleaning
After each use, the stencil should be cleaned to remove any residual solder paste or contaminants. Various cleaning methods can be employed, such as manual cleaning with solvents or automated stencil cleaning systems. Proper cleaning helps maintain the accuracy and consistency of solder paste deposition.
3. Storage
When not in use, SMT stencils should be stored in a clean, dry environment to prevent damage or contamination. Stencils should be stored flat or hung vertically to avoid warping or deformation.
Frequently Asked Questions (FAQ)
- What is the difference between metal and polyester SMT stencils?
-
Metal stencils, typically made from stainless steel or nickel alloys, offer high durability and precision. They are suitable for high-volume production and fine-pitch components. Polyester stencils, made from a thin, flexible polyester film, are lower in cost and ideal for prototyping and low-volume production.
-
How does the stencil thickness affect solder paste deposition?
-
The thickness of the stencil determines the amount of solder paste deposited on the pads. Thicker stencils deposit more solder paste, while thinner stencils deposit less. The optimal stencil thickness depends on factors such as component size, pitch, and the desired solder joint profile.
-
Can SMT stencils be used for both standard and fine-pitch components?
-
Yes, SMT stencils can be customized to accommodate a wide range of component sizes, including standard and fine-pitch components. The aperture size and shape can be tailored to match the specific requirements of each component, ensuring optimal solder paste deposition.
-
How often should SMT stencils be cleaned?
-
SMT stencils should be cleaned after each use to remove any residual solder paste or contaminants. Regular cleaning helps maintain the accuracy and consistency of solder paste deposition and prolongs the life of the stencil.
-
What are the signs that an SMT stencil needs to be replaced?
- Signs that an SMT stencil may need replacement include excessive wear, damage to apertures, warping, or persistent contamination that cannot be removed through cleaning. If the stencil no longer produces consistent and accurate solder paste deposition, it may be time to consider a replacement.
Conclusion
SMT stencils play a vital role in the electronics manufacturing process, offering numerous benefits that contribute to the production of high-quality, reliable electronic devices. By improving solder paste deposition accuracy, increasing consistency and repeatability, enhancing production efficiency, and enabling cost savings, SMT stencils have become an indispensable tool in modern PCB Assembly.
To fully leverage the advantages of SMT stencils, it is crucial to consider factors such as aperture size and shape, stencil thickness, material selection, and proper maintenance and cleaning practices. By optimizing these elements, manufacturers can ensure optimal solder paste deposition and achieve the desired results in their SMT assembly processes.
As the electronics industry continues to evolve, with growing demands for miniaturization and higher performance, the importance of SMT stencils will only continue to increase. By understanding and utilizing the benefits of SMT stencils, manufacturers can stay competitive, improve product quality, and meet the ever-changing needs of the market.
No responses yet