What is an SMT Stencil?
An SMT stencil, also known as a solder paste stencil, is a thin metal sheet with laser-cut apertures that correspond to the pads on a printed circuit board (PCB). The stencil is used to apply solder paste onto the PCB pads with precision and consistency before the placement of surface mount components.
Types of SMT Stencils
There are three main types of SMT stencils:
-
Framed Stencils: These stencils are mounted on a rigid frame, providing stability and durability. They are ideal for high-volume production and can be easily integrated into automated assembly lines.
-
Frameless Stencils: Also known as prototype stencils, these are more flexible and cost-effective than framed stencils. They are suitable for low-volume production or prototyping.
-
Step Stencils: These stencils have multiple levels or steps to accommodate PCBs with components of varying heights. They are used for more complex assemblies that require different solder paste thicknesses.
SMT Stencil Materials
SMT stencils can be made from various materials, each with its own advantages and disadvantages. The most common materials are:
-
Stainless Steel: Known for its durability and stability, stainless steel is the most widely used material for SMT stencils. It offers excellent paste release properties and can withstand multiple cleaning cycles.
-
Nickel: Nickel stencils are more expensive than stainless steel but offer superior paste release properties. They are ideal for fine-pitch applications and have a longer lifespan.
-
Polyimide: These stencils are made from a flexible, polymer material. They are suitable for low-volume production and can conform to slightly irregular PCB surfaces.
Material | Advantages | Disadvantages |
---|---|---|
Stainless Steel | – Durable – Stable – Good paste release |
– More expensive than polyimide |
Nickel | – Excellent paste release – Long lifespan |
– Higher cost than stainless steel |
Polyimide | – Flexible – Conforms to irregular surfaces |
– Less durable than metal stencils |
The Importance of SMT Stencils in the Assembly Process
Precise Solder Paste Deposition
One of the most critical aspects of SMT assembly is the accurate deposition of solder paste onto the PCB pads. Inconsistent or inadequate solder paste application can lead to defects such as bridging, tombstoning, or insufficient solder joints. SMT stencils ensure that the right amount of solder paste is applied to each pad, minimizing the risk of defects.
Consistency and Repeatability
In high-volume production, consistency and repeatability are essential. SMT stencils help maintain uniform solder paste deposition across multiple PCBs, ensuring that each board has the same solder joint quality. This consistency reduces the need for rework and improves overall production efficiency.
Accommodating Miniaturization
As electronic devices become smaller and more compact, the demand for miniaturized components and fine-pitch layouts increases. SMT stencils with high-precision laser-cut apertures can accommodate these challenges, enabling the assembly of densely packed PCBs with minimal defects.
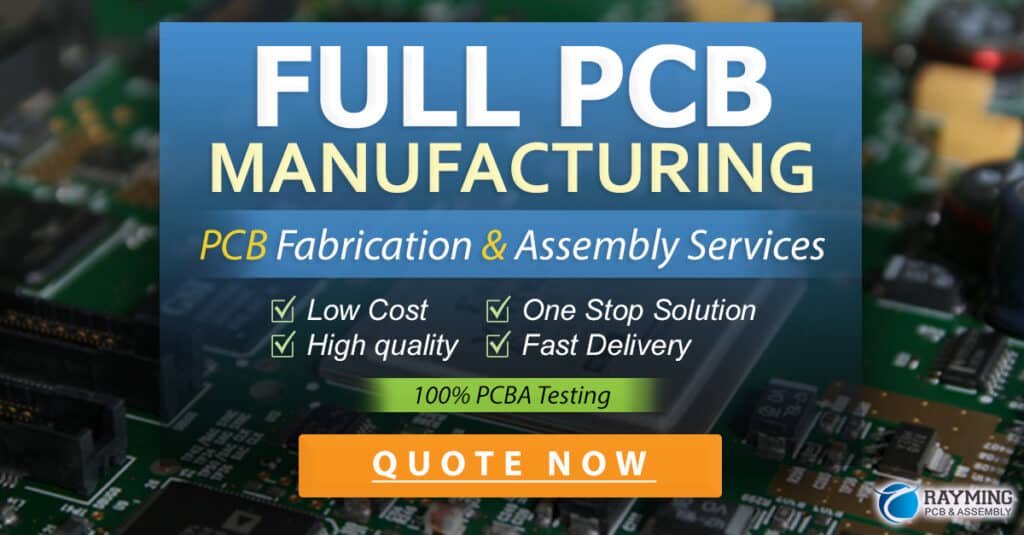
Factors Affecting SMT Stencil Performance
Several factors can influence the performance of an SMT stencil:
-
Aperture Design: The size, shape, and pitch of the stencil apertures must be carefully designed to ensure optimal solder paste release and prevent defects.
-
Stencil Thickness: The thickness of the stencil determines the amount of solder paste deposited. Thinner stencils are used for fine-pitch components, while thicker stencils are suitable for larger components.
-
Material Quality: The quality of the stencil material affects its durability, paste release properties, and overall performance. High-quality materials ensure consistent results and a longer stencil lifespan.
-
Cleaning and Maintenance: Regular cleaning and maintenance of the SMT stencil are crucial to prevent clogging of apertures and ensure consistent solder paste deposition.
Choosing the Right SMT Stencil
When selecting an SMT stencil, consider the following factors:
-
PCB Design: The stencil must be compatible with the PCB layout, component sizes, and pitch.
-
Production Volume: For high-volume production, a durable, framed stencil is recommended. For low-volume or prototype runs, a frameless or polyimide stencil may suffice.
-
Budget: Stainless steel stencils offer a good balance between cost and performance. Nickel stencils are more expensive but provide superior paste release properties.
-
Supplier Reputation: Choose a reputable SMT stencil supplier with experience in producing high-quality stencils and offering reliable customer support.
SMT Stencil Maintenance and Storage
Proper maintenance and storage of SMT stencils are essential to ensure their longevity and consistent performance:
-
Cleaning: Clean the stencil regularly using a compatible solvent and a lint-free cloth. Ensure that all apertures are free from solder paste residue.
-
Inspection: Inspect the stencil for signs of wear, damage, or clogged apertures. Replace the stencil if necessary.
-
Storage: Store the stencil in a dry, dust-free environment. Use a protective cover or store the stencil in a vertical position to prevent damage.
Frequently Asked Questions (FAQ)
-
What is the difference between a framed and frameless SMT stencil?
A framed stencil is mounted on a rigid frame, providing stability and durability, making it suitable for high-volume production. A frameless stencil, also known as a prototype stencil, is more flexible and cost-effective, making it ideal for low-volume production or prototyping. -
How often should I clean my SMT stencil?
It is recommended to clean your SMT stencil after every use or at regular intervals during production. The frequency of cleaning depends on the solder paste type, production volume, and the stencil’s condition. -
Can I reuse an SMT stencil for different PCB designs?
No, each SMT stencil is designed specifically for a particular PCB layout. Using a stencil designed for a different PCB can result in incorrect solder paste deposition and lead to defects. -
How long does an SMT stencil last?
The lifespan of an SMT stencil depends on various factors, such as the material, usage frequency, and maintenance. On average, a well-maintained stencil can last for 20,000 to 50,000 prints. -
Can I use the same SMT stencil for both lead-free and leaded solder pastes?
It is not recommended to use the same stencil for both lead-free and leaded solder pastes. Lead-free solder pastes require different aperture designs and stencil thicknesses compared to leaded solder pastes. Using the wrong stencil can result in defects and compromise the solder joint quality.
Conclusion
SMT stencils are a critical component in the surface mount technology assembly process. They ensure precise, consistent solder paste deposition, which is essential for achieving high-quality solder joints and minimizing defects. By understanding the types, materials, and factors affecting SMT stencil performance, you can choose the right stencil for your production needs and maintain it properly for optimal results.
Investing in a high-quality SMT stencil and partnering with a reputable supplier can significantly improve your SMT assembly process’s efficiency, reliability, and overall product quality. As the electronics industry continues to evolve and demand more miniaturized, high-density assemblies, the importance of SMT stencils will only continue to grow.
No responses yet