Introduction to PCB Assembly for Medical Devices
The medical device industry relies heavily on advanced electronics and precise manufacturing processes to create life-saving equipment. One critical aspect of medical device manufacturing is the assembly of printed circuit boards (PCBs). PCB assembly for medical devices requires strict adherence to quality standards, regulatory compliance, and specialized expertise to ensure the reliability and performance of the final product.
In this article, we will explore the intricacies of medical device PCB assembly and the benefits of partnering with an experienced electronics contract manufacturing service provider.
Understanding the Challenges of Medical Device PCB Assembly
Regulatory Compliance
Medical device PCB assembly must comply with various regulatory standards to ensure patient safety and device effectiveness. Some of the key regulations include:
- FDA 21 CFR Part 820: Quality System Regulation for Medical Devices
- ISO 13485: Medical Devices – Quality Management Systems
- IEC 60601: Medical Electrical Equipment – General Requirements for Basic Safety and Essential Performance
Compliance with these regulations requires strict documentation, traceability, and quality control measures throughout the PCB assembly process.
Complexity and Miniaturization
Medical devices often require complex and miniaturized PCB designs to fit within compact form factors and deliver advanced functionality. This complexity poses challenges for PCB assembly, including:
- Precise component placement and soldering
- Handling of delicate and high-density components
- Ensuring proper signal integrity and electromagnetic compatibility (EMC)
An experienced contract manufacturing service provider with expertise in medical device PCB assembly can navigate these challenges and deliver high-quality, reliable boards.
Reliability and Quality Control
Medical devices must operate reliably in critical situations, as any failure can have severe consequences for patient health and safety. Ensuring the highest levels of reliability and quality control in PCB assembly is essential. This includes:
- Rigorous testing and inspection procedures
- Use of high-quality components and materials
- Strict process controls and documentation
- Traceability and lot tracking for post-market surveillance
Partnering with a contract manufacturer that has a robust quality management system and experience in medical device PCB assembly can help mitigate risks and ensure the reliability of the final product.
Benefits of Outsourcing Medical Device PCB Assembly
Access to Specialized Expertise and Technology
Medical device PCB assembly requires specialized knowledge, skills, and equipment. By outsourcing to an experienced contract manufacturer, medical device companies can access:
- Industry-specific expertise in PCB design, assembly, and testing
- State-of-the-art manufacturing equipment and processes
- Experienced engineers and technicians familiar with medical device regulations and requirements
This access to specialized expertise and technology can help medical device companies accelerate development cycles, improve product quality, and reduce costs.
Scalability and Flexibility
Outsourcing medical device PCB assembly to a contract manufacturer provides scalability and flexibility to meet changing market demands. Contract manufacturers can:
- Quickly ramp up production to meet increased demand
- Accommodate design changes and product iterations
- Provide a range of manufacturing services, from prototyping to full-scale production
This scalability and flexibility allow medical device companies to focus on core competencies, such as research and development, while relying on the contract manufacturer to handle production needs.
Cost Efficiency and Time to Market
Outsourcing medical device PCB assembly can lead to significant cost savings and reduced time to market. Contract manufacturers can offer:
- Economies of scale through bulk purchasing and efficient production processes
- Reduced capital expenditure on manufacturing equipment and facilities
- Faster turnaround times through streamlined workflows and parallel processing
By leveraging the expertise and resources of a contract manufacturer, medical device companies can bring new products to market faster and more cost-effectively.
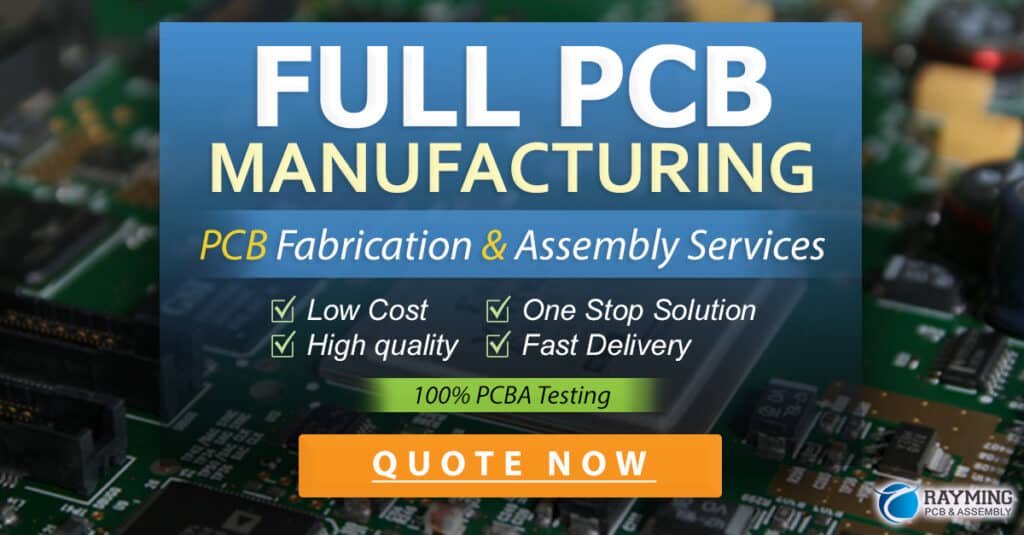
Choosing the Right Medical Device PCB Assembly Partner
Experience and Expertise
When selecting a contract manufacturing partner for medical device PCB assembly, it is essential to consider their experience and expertise in the industry. Look for a partner with:
- A proven track record of successful medical device PCB assembly projects
- Deep understanding of medical device regulations and quality standards
- Skilled engineers and technicians with experience in complex PCB designs
An experienced contract manufacturer can provide valuable insights and guidance throughout the development process, helping to optimize designs for manufacturability and reliability.
Quality Management System
A robust quality management system is critical for medical device PCB assembly. Ensure that your chosen contract manufacturer has:
- ISO 13485 certification for medical device quality management systems
- Documented processes and procedures for quality control and assurance
- Rigorous testing and inspection protocols, including automated optical inspection (AOI), X-ray inspection, and functional testing
- Traceability and lot tracking capabilities for post-market surveillance
A strong quality management system helps to ensure the consistency, reliability, and safety of the assembled PCBs.
Communication and Collaboration
Effective communication and collaboration are key to successful medical device PCB assembly outsourcing. Look for a contract manufacturer that:
- Provides clear and responsive communication channels
- Encourages open dialogue and collaboration throughout the development process
- Offers flexibility and adaptability to accommodate design changes and iterations
- Provides regular progress updates and project status reports
A partnership built on open communication and collaboration can help to streamline the development process, minimize errors, and ensure a successful outcome.
FAQ
Q1: What regulations govern medical device PCB assembly?
A1: Medical device PCB assembly is subject to various regulations, including FDA 21 CFR Part 820, ISO 13485, and IEC 60601. These regulations ensure patient safety, device effectiveness, and quality management.
Q2: Why is reliability so critical in medical device PCB assembly?
A2: Medical devices must operate reliably in critical situations, as any failure can have severe consequences for patient health and safety. Ensuring the highest levels of reliability in PCB assembly is essential to mitigate risks and ensure the effectiveness of the final product.
Q3: What are the benefits of outsourcing medical device PCB assembly?
A3: Outsourcing medical device PCB assembly provides access to specialized expertise and technology, scalability and flexibility, cost efficiency, and reduced time to market. Contract manufacturers can help medical device companies accelerate development cycles, improve product quality, and reduce costs.
Q4: What should I look for in a medical device PCB assembly partner?
A4: When choosing a medical device PCB assembly partner, consider their experience and expertise in the industry, quality management system, and communication and collaboration capabilities. An experienced contract manufacturer with a robust quality management system and open communication can help ensure the success of your PCB assembly project.
Q5: How can I ensure the quality and reliability of outsourced medical device PCB assembly?
A5: To ensure the quality and reliability of outsourced medical device PCB assembly, choose a contract manufacturer with ISO 13485 certification, a strong quality management system, and rigorous testing and inspection protocols. Maintain open communication and collaboration throughout the development process to minimize errors and ensure a successful outcome.
Conclusion
Medical device PCB assembly is a critical aspect of creating life-saving equipment that requires specialized expertise, strict regulatory compliance, and a commitment to quality and reliability. By outsourcing PCB assembly to an experienced electronics contract manufacturing service provider, medical device companies can access the knowledge, technology, and resources needed to bring innovative products to market faster and more cost-effectively.
When selecting a medical device PCB assembly partner, prioritize experience, quality management, and communication to ensure a successful collaboration. By working closely with a trusted contract manufacturer, medical device companies can focus on their core competencies while relying on their partner to deliver high-quality, reliable PCBs that meet the strictest standards of the industry.
As the medical device industry continues to evolve and advance, the importance of specialized PCB assembly services will only grow. By embracing outsourcing and partnering with experienced contract manufacturers, medical device companies can position themselves for success in an increasingly competitive and demanding market.
No responses yet