What is SMD?
SMD stands for Surface Mount Device. SMD components are mounted directly onto the surface of a printed circuit board (PCB). The components have small metal leads or terminals that are soldered onto solder pads on the PCB surface. SMD is a newer technology compared to through-hole mounting and enables much smaller component sizes and higher component density on the PCB.
Advantages of SMD
- Smaller component size allows for more compact PCB designs
- Components can be mounted on both sides of the PCB
- Faster and easier automated assembly
- Lower cost for high volume production
- Better mechanical performance under shake and vibration conditions
Disadvantages of SMD
- Requires specialized equipment for manual assembly and rework
- Some components are not available in SMD Packages
- Higher startup costs for low volume production
What is SMT?
SMT stands for Surface Mount Technology. It refers to the method of assembling PCBs where the components are mounted directly onto the PCB surface. SMT is basically the process of assembling PCBs using SMD components.
The typical SMT process involves the following steps:
1. Solder paste application – A thin layer of solder paste is applied to the PCB solder pads using a stencil.
2. Component placement – The SMD components are placed onto the solder paste deposits on the PCB. This is typically done by an automated pick-and-place machine.
3. Reflow soldering – The PCB is passed through a reflow oven. The solder paste melts, forming a permanent solder joint between the component leads and the PCB pads.
4. Inspection – The assembled PCB is inspected, typically using automated optical inspection (AOI) systems.
Advantages of SMT
- Enables high volume, low cost production
- Allows for smaller PCB sizes and higher component densities
- Suitable for most component types
- Reliable solder joints
Disadvantages of SMT
- High startup costs for equipment and setup
- Not suitable for all component types (e.g. some high power components)
- Requires careful PCB design for manufacturability
What is PTH?
PTH stands for Plated Through Hole. PTH components have long metal leads that are inserted into holes drilled in the PCB. The holes are electroplated with a metal, typically copper, to form an electrical connection between the layers of the PCB. After inserting the component leads, they are soldered to the PCB, typically using a wave soldering process.
PTH technology was the dominant PCB Assembly method before the widespread adoption of SMT in the 1980s. Today, PTH is still used for certain types of components, such as connectors, large transformers, and high power components.
Advantages of PTH
- Strong mechanical connection between component and PCB
- Suitable for high power and high heat dissipation components
- Easier manual assembly and rework compared to SMD
- Lower startup costs compared to SMT
Disadvantages of PTH
- Larger component size and PCB area required
- Holes required in PCB, limiting routing space on inner layers
- Slower assembly process compared to SMT
- Higher cost for high volume production
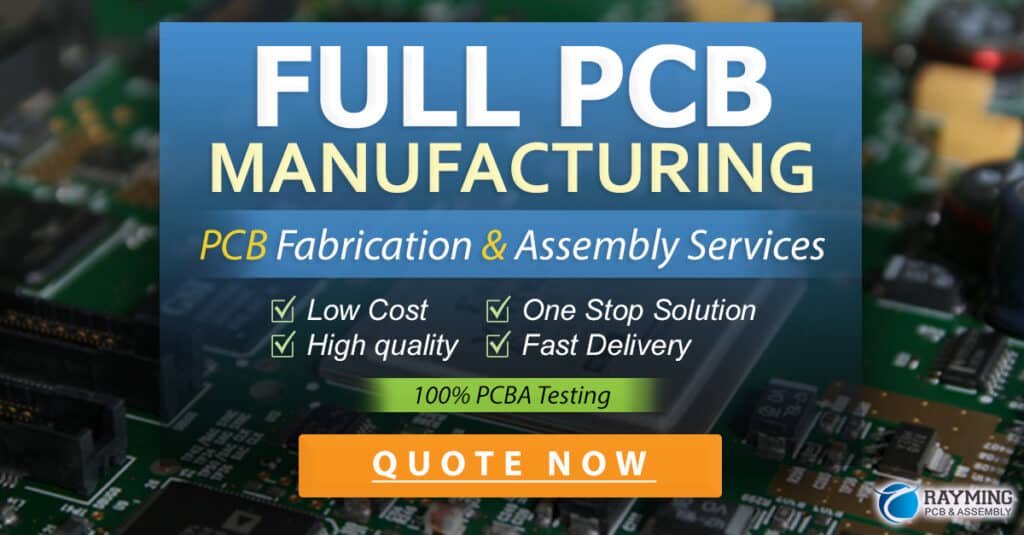
SMD vs SMT vs PTH Comparison
Feature | SMD | SMT | PTH |
---|---|---|---|
Component Mounting | Surface mount | Surface mount | Through hole |
Component Size | Small | Small | Large |
PCB Area Usage | Minimal | Minimal | Significant |
Assembly Process | Pick and place, reflow | Pick and place, reflow | Insert and wave solder |
Automotive Assembly | Yes | Yes | Limited |
Manual Assembly | Difficult | Difficult | Easier |
Rework | Specialized tools needed | Specialized tools needed | Simpler |
Component Availability | Wide | Wide | Limited |
Reliability | Good | Good | Excellent |
Cost for Low Volume | High | High | Low |
Cost for High Volume | Low | Low | High |
As can be seen from the comparison table, SMD/SMT and PTH each have their own advantages and disadvantages. The choice of technology depends on the specific requirements of the PCB design, such as component availability, power handling, size constraints, production volume, and cost.
PCB Design Considerations for SMD/SMT
When designing a PCB for SMD/SMT assembly, there are several key factors to consider:
Component Selection
- Choose components that are available in SMD packages whenever possible.
- Consider the size of the component package and the pitch (spacing) of the leads. Smaller packages and finer pitches require more precise manufacturing equipment.
- For high power or high heat dissipation components, choose packages with exposed pads or heat slugs for better thermal performance.
Footprint Design
- Use the correct footprint for each component based on the manufacturer’s datasheet.
- Pay attention to the solder pad size and spacing. Pads that are too small can result in poor solder joints, while pads that are too large can lead to short circuits.
- Include solder mask openings around the pads to prevent solder bridges.
- For fine pitch components, consider using solder mask defined (SMD) pads instead of copper defined pads.
Layout and Routing
- Group related components together to minimize routing complexity.
- Provide adequate space between components for the placement machine nozzle.
- Route traces on the top and bottom layers whenever possible to maximize routing space.
- Use ground planes and power planes to improve signal integrity and reduce electromagnetic interference (EMI).
Manufacturability
- Follow the design for manufacturability (DFM) guidelines provided by your PCB manufacturer and assembly house.
- Avoid using components that are too small or have too fine a pitch for the capabilities of your manufacturing partners.
- Provide adequate Fiducial Markers and testing points for automated assembly and inspection.
- Consider the use of panelization to reduce manufacturing costs for high volume production.
FAQ
1. Can SMD and PTH components be used on the same PCB?
Yes, it is possible to use both SMD and PTH components on the same PCB. This is often done to accommodate specific component types or to meet the design requirements. However, using both types of components can increase the complexity and cost of the assembly process.
2. What is the smallest component size that can be used with SMT?
The smallest commonly used SMD component package is 0201 (0.6mm x 0.3mm). Smaller packages, such as 01005 (0.4mm x 0.2mm), are available but require very precise manufacturing equipment and are not widely used.
3. Can PTH components be soldered using reflow?
PTH components are typically not suitable for reflow soldering due to the risk of solder wicking up the through holes and creating short circuits. However, some specialized PTH components, such as press-fit connectors, are designed to be used in a reflow process.
4. What is the difference between lead-free and leaded solder in SMT?
Lead-free solder, such as SAC305 (Sn96.5/Ag3.0/Cu0.5), has a higher melting point compared to leaded solder (Sn63/Pb37). This requires higher reflow temperatures and can stress some components. However, lead-free solder is required for RoHS compliance and is becoming the industry standard.
5. How can I reduce the cost of SMT assembly?
There are several ways to reduce the cost of SMT assembly:
– Use standard component packages and avoid custom or specialty components whenever possible.
– Minimize the number of unique components used in the design.
– Use larger component packages and pitches if the design allows.
– Design the PCB for ease of manufacturing, following DFM guidelines.
– Consider panelization for high volume production.
– Choose a reputable PCB manufacturer and assembly house with experience in your type of product.
Conclusion
SMD, SMT, and PTH are key terms related to PCB assembly technology. SMD and SMT refer to the use of surface mounted components and the associated assembly processes, while PTH refers to the older through-hole technology. Each technology has its own advantages and disadvantages in terms of component size, PCB area usage, assembly process, reliability, and cost.
When designing a PCB for SMD/SMT assembly, it is important to consider factors such as component selection, footprint design, layout and routing, and manufacturability. By following best practices and working closely with experienced manufacturing partners, designers can create PCBs that are reliable, cost-effective, and suitable for their intended application.
As electronic products continue to become smaller, more complex, and more ubiquitous, the use of SMD/SMT technology will continue to grow. By understanding the fundamentals of these technologies, PCB designers can create products that meet the demands of today’s fast-paced, highly competitive electronics industry.
No responses yet