What is PCB Assembly?
PCB assembly is the process of attaching electronic components to a printed circuit board. The components are placed on the board and then soldered in place to create electrical connections. The process can be done manually or using automated machines, depending on the complexity of the board and the volume of production.
Types of PCB Assembly
There are three main types of PCB assembly:
-
Through-hole assembly (THA): This is the traditional method of PCB assembly, where components with long leads are inserted into holes drilled in the board and soldered in place.
-
Surface mount assembly (SMT): This is a more modern method of PCB assembly, where components are placed directly on the surface of the board and soldered in place using a reflow oven.
-
Mixed assembly: This is a combination of through-hole and surface mount assembly, where both types of components are used on the same board.
PCB Assembly Process
The PCB assembly process typically involves the following steps:
-
Solder paste application: A thin layer of solder paste is applied to the pads on the PCB where the components will be placed.
-
Component placement: The components are placed on the board using a pick-and-place machine or by hand.
-
Reflow soldering: The board is heated in a reflow oven to melt the solder paste and create a strong bond between the components and the board.
-
Inspection and testing: The assembled board is inspected for defects and tested to ensure that it functions correctly.
Advantages of Automated PCB Assembly
Automated PCB assembly offers several advantages over manual assembly, including:
-
Increased speed and efficiency: Automated machines can place components much faster than human operators, resulting in higher production volumes and shorter lead times.
-
Improved accuracy and consistency: Automated machines are programmed to place components with high precision, reducing the risk of errors and ensuring consistent quality.
-
Reduced labor costs: Automated assembly requires fewer human operators, reducing labor costs and freeing up resources for other tasks.
Choosing the Right PCB Assembly Service
When choosing a PCB assembly service, there are several factors to consider:
-
Experience and expertise: Look for a service provider with a proven track record of success and expertise in your specific industry or application.
-
Quality control processes: Ensure that the service provider has robust quality control processes in place to catch defects and ensure consistent quality.
-
Turnaround time and pricing: Consider the service provider’s turnaround time and pricing to ensure that they align with your project timeline and budget.
Factor | Consideration |
---|---|
Experience & Expertise | Look for a service provider with a proven track record of success in your industry or application |
Quality Control | Ensure the service provider has robust quality control processes to catch defects |
Turnaround & Pricing | Consider the service provider’s turnaround time and pricing to align with your project needs |
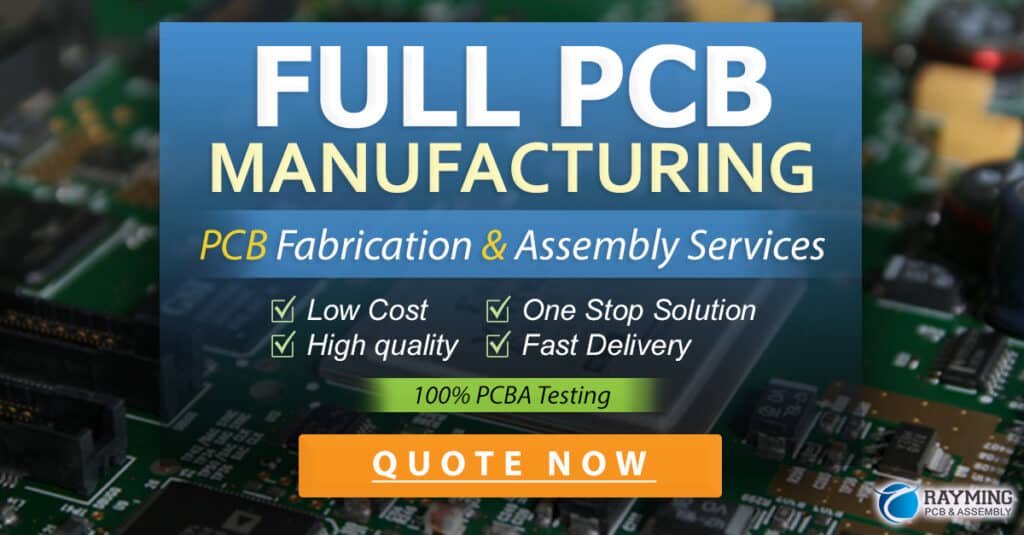
Common PCB Assembly Defects and How to Avoid Them
PCB assembly defects can lead to malfunctions and failures in the final product. Some common defects include:
-
Solder bridges: This occurs when excess solder creates an unintended connection between two or more pads or traces.
-
Cold solder joints: This happens when the solder does not melt completely, resulting in a weak and unreliable connection.
-
Component misalignment: This occurs when components are not placed accurately on the board, leading to poor connections or short circuits.
To avoid these defects, it is important to:
- Use high-quality components and materials
- Follow proper soldering techniques and temperature profiles
- Implement robust quality control processes, including automated optical inspection (AOI) and x-ray inspection
- Work with experienced and reputable PCB assembly service providers
Best Practices for PCB Assembly
To ensure successful PCB assembly, follow these best practices:
-
Design for manufacturability (DFM): Design your PCB with assembly in mind, following guidelines for component placement, spacing, and orientation.
-
Use standardized components: Whenever possible, use standardized components to simplify the assembly process and reduce the risk of errors.
-
Communicate clearly with your service provider: Provide clear and detailed documentation, including bill of materials (BOM), Gerber files, and assembly drawings.
-
Plan for testing and validation: Incorporate testing and validation processes into your project plan to catch defects early and ensure that the final product meets your specifications.
FAQ
-
What is the difference between through-hole and surface mount assembly?
Through-hole assembly involves inserting component leads into holes drilled in the PCB and soldering them in place, while surface mount assembly involves placing components directly on the surface of the board and soldering them using a reflow oven. -
How long does the PCB assembly process typically take?
The turnaround time for PCB assembly varies depending on the complexity of the board, the volume of production, and the service provider. Generally, lead times range from a few days to several weeks. -
What factors should I consider when choosing a PCB assembly service provider?
When choosing a PCB assembly service provider, consider their experience and expertise in your industry or application, their quality control processes, turnaround time, and pricing. -
What are some common defects in PCB assembly, and how can they be avoided?
Common defects in PCB assembly include solder bridges, cold solder joints, and component misalignment. These defects can be avoided by using high-quality materials, following proper soldering techniques, implementing robust quality control processes, and working with experienced service providers. -
What are some best practices for ensuring successful PCB assembly?
Best practices for successful PCB assembly include designing for manufacturability, using standardized components, communicating clearly with your service provider, and planning for testing and validation processes.
Conclusion
PCB assembly is a critical process in the electronics manufacturing industry, requiring careful planning, attention to detail, and adherence to best practices. By understanding the different types of PCB assembly, the advantages of automated assembly, and the factors to consider when choosing a service provider, you can ensure successful and high-quality PCB assembly for your projects. Additionally, by following best practices such as designing for manufacturability, using standardized components, and implementing robust quality control processes, you can avoid common defects and ensure that your final product meets your specifications.
No responses yet