Importance of PCB Assembly Preparation
Preparing for PCB assembly is critical for several reasons:
- Cost-effectiveness: Proper preparation helps minimize errors and rework, reducing overall production costs.
- Time-saving: By having all the necessary components, tools, and documentation ready, the assembly process can be streamlined, saving time.
- Quality assurance: Adequate preparation ensures that the assembLED PCBs meet the required quality standards and specifications.
Steps to Prepare for PCB Assembly
1. Design Finalization
Before starting the assembly process, it is essential to finalize the PCB design. This includes:
- Schematic design: Ensure that the schematic is complete, accurate, and has undergone thorough review and verification.
- PCB layout: Verify that the PCB layout is optimized for manufacturability, considering factors such as component placement, routing, and design rules.
- Bill of Materials (BOM): Create a comprehensive BOM that lists all the required components, their quantities, and specifications.
2. Component Procurement
Once the design is finalized, the next step is to procure the necessary components. This involves:
- Sourcing components: Identify reliable suppliers and place orders for the required components based on the BOM.
- Lead time management: Consider the lead times for each component and plan accordingly to avoid delays in the assembly process.
- Component inspection: Upon receipt, inspect the components for quality, quantity, and conformance to specifications.
3. PCB Fabrication
With the design finalized and components procured, the PCBs can be fabricated. This step includes:
- Choosing a PCB manufacturer: Select a reputable PCB manufacturer that can meet your requirements in terms of quality, turnaround time, and cost.
- Providing manufacturing files: Supply the necessary files to the manufacturer, including Gerber files, drill files, and fabrication drawings.
- Quality control: Ensure that the fabricated PCBs undergo thorough quality control checks, such as visual inspection and electrical testing.
4. Assembly Preparation
Before starting the assembly process, several preparatory steps need to be taken:
- Workstation setup: Prepare the assembly workstation with the necessary tools, equipment, and safety gear.
- Solder paste stencil: If using surface mount components, obtain a solder paste stencil that matches the PCB layout.
- Solder paste application: Apply solder paste to the PCB pads using the stencil and a solder paste printer or manual methods.
- Component placement: Organize the components according to the BOM and placement diagram to facilitate efficient assembly.
5. Documentation and Instructions
Proper documentation and instructions are crucial for a successful assembly process. This includes:
- Assembly instructions: Create clear and detailed assembly instructions that outline the step-by-step process, including component placement, soldering techniques, and any special considerations.
- Inspection and testing procedures: Document the procedures for inspecting and testing the assembled PCBs to ensure they meet the required quality standards.
- Rework and repair guidelines: Provide guidelines for handling any rework or repairs that may be necessary during the assembly process.
Tools and Equipment for PCB Assembly
To carry out PCB assembly efficiently, certain tools and equipment are essential. Some of the key items include:
Tool/Equipment | Purpose |
---|---|
Soldering iron | Used for hand soldering through-hole components and making minor repairs. |
Solder paste printer | Applies solder paste to the PCB pads for surface mount components. |
Pick-and-place machine | Automates the placement of surface mount components on the PCB. |
Reflow oven | Melts the solder paste and forms a permanent connection between components and the PCB. |
Inspection microscope | Allows for visual inspection of solder joints and component placement. |
Multimeter | Used for electrical testing and troubleshooting of the assembled PCB. |
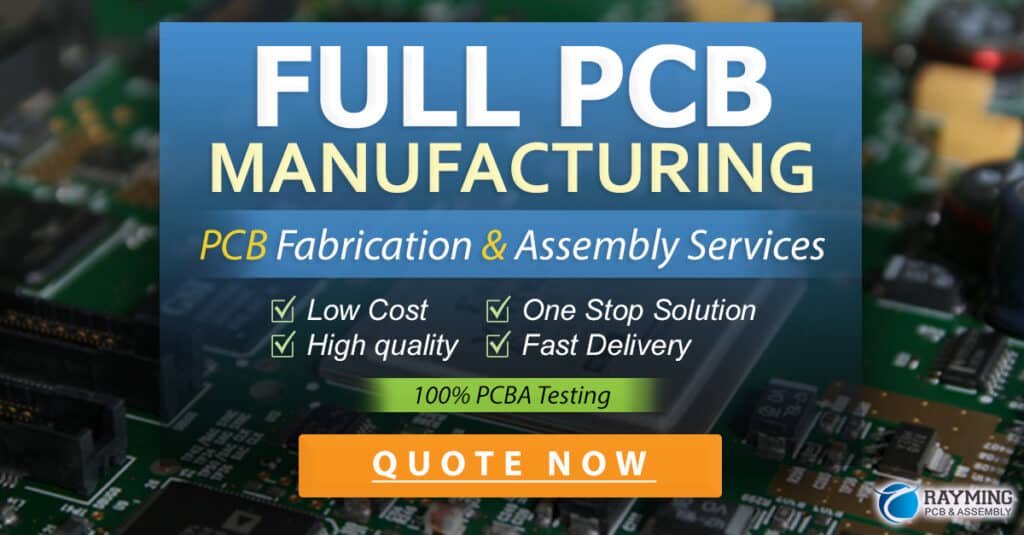
Common Challenges in PCB Assembly
Despite thorough preparation, challenges can arise during the PCB assembly process. Some common issues include:
- Component availability: Long lead times or unexpected shortages of components can delay the assembly process.
- Solder defects: Issues such as bridging, insufficient solder, or Cold Solder Joints can affect the functionality and reliability of the assembled PCB.
- Component misalignment: Improper placement of components can lead to electrical shorting or mechanical interference.
- Electrostatic discharge (ESD): ESD can damage sensitive electronic components during handling and assembly.
- Thermal management: Improper thermal management during soldering can cause component damage or poor solder joint formation.
To mitigate these challenges, it is essential to have well-defined processes, skilled personnel, and appropriate equipment in place. Regular training and adherence to best practices can also help minimize the occurrence of these issues.
Quality Control and Testing
After the PCB assembly is complete, quality control and testing procedures should be carried out to ensure the functionality and reliability of the assembled PCBs. Some common methods include:
- Visual inspection: Inspect the solder joints, component placement, and overall PCB condition for any visible defects or anomalies.
- Automated optical inspection (AOI): Use AOI machines to detect solder defects, component misalignment, and other surface-level issues.
- In-circuit testing (ICT): Perform electrical tests on the assembled PCB to verify the connectivity and functionality of the components.
- Functional testing: Test the assembled PCB under real-world operating conditions to ensure it performs as intended.
- Burn-in testing: Subject the assembled PCB to elevated temperatures and extended operating periods to identify any early-life failures.
Documenting the results of these quality control and testing procedures is important for traceability and continuous improvement of the assembly process.
Best Practices for PCB Assembly
To ensure a successful PCB assembly process, consider the following best practices:
- Design for manufacturability (DFM): Incorporate DFM principles during the PCB design phase to minimize assembly challenges and improve yield.
- Component standardization: Use standardized components whenever possible to simplify procurement and assembly processes.
- Supplier management: Establish strong relationships with reliable suppliers to ensure timely delivery of high-quality components.
- Process control: Implement robust process controls, including documented work instructions, quality checks, and statistical process control (SPC) techniques.
- Training and skill development: Invest in regular training and skill development for assembly personnel to keep them updated with the latest techniques and best practices.
By following these best practices, manufacturers can optimize their PCB assembly processes, reduce defects, and improve overall product quality.
Frequently Asked Questions (FAQ)
- What is the difference between through-hole and surface mount assembly?
-
Through-Hole Assembly involves inserting component leads through holes drilled in the PCB and soldering them on the opposite side. Surface mount assembly, on the other hand, involves placing components directly on the surface of the PCB and soldering them using solder paste and a reflow oven.
-
How can I ensure the quality of the components used in PCB assembly?
-
To ensure component quality, source from reputable suppliers, request certificates of conformance (COCs), and perform incoming inspections to verify the quality and specifications of the components.
-
What are some common soldering defects to look out for?
-
Common soldering defects include bridging (solder connecting adjacent pads), insufficient solder, cold solder joints (dull and grainy appearance), and solder balls or splatter.
-
How can I prevent electrostatic discharge (ESD) during PCB assembly?
-
To prevent ESD, use ESD-safe workstations, wrist straps, and grounding mats. Handle sensitive components using ESD-safe packaging and tools, and ensure proper grounding of personnel and equipment.
-
What should I do if a component is damaged during the assembly process?
- If a component is damaged during assembly, assess the extent of the damage and determine if it can be safely removed and replaced. Follow the manufacturer’s guidelines for component removal and replacement, and use appropriate tools and techniques to minimize further damage to the PCB.
Conclusion
Preparing for PCB assembly is a critical step in ensuring a smooth and efficient manufacturing process. By finalizing the design, procuring components, fabricating the PCBs, and setting up the assembly workstation, manufacturers can minimize delays and errors. Proper documentation, quality control, and adherence to best practices are also essential for producing high-quality assembled PCBs.
By understanding the importance of preparation, following the necessary steps, and being aware of common challenges and best practices, manufacturers can optimize their PCB assembly processes and deliver reliable electronic products to their customers.
No responses yet