Introduction to Nitrogen Reflow Soldering
Nitrogen reflow soldering is a process used in PCB Assembly to improve the quality and reliability of solder joints. By using nitrogen gas during the reflow process, oxidation of the solder is minimized, resulting in stronger and more consistent solder connections. This guide will provide an in-depth look at nitrogen reflow soldering, including its benefits, the process, and best practices for implementation.
What is Nitrogen Reflow Soldering?
Nitrogen reflow soldering is a variation of the standard reflow soldering process, where nitrogen gas is used to create an inert atmosphere during the soldering process. The nitrogen gas displaces the oxygen in the reflow oven, preventing oxidation of the solder and ensuring a higher quality solder joint.
Benefits of Nitrogen Reflow Soldering
- Reduced oxidation: Nitrogen reflow soldering minimizes the formation of oxides on the solder surface, resulting in stronger and more reliable solder joints.
- Improved wetting: The absence of oxygen allows the solder to flow more easily, ensuring better wetting of the component leads and PCB pads.
- Reduced voiding: Nitrogen reflow soldering helps reduce the formation of voids in the solder joints, which can weaken the connection and lead to failures.
- Increased process window: The use of nitrogen allows for a wider range of acceptable reflow profiles, making the process more forgiving and easier to control.
The Nitrogen Reflow Soldering Process
Equipment and Materials
To implement nitrogen reflow soldering, you will need the following equipment and materials:
- Reflow oven with nitrogen capability
- Nitrogen gas supply
- PCBs and components
- Solder paste
- Stencils for solder paste application
Process Steps
- PCB Preparation: The PCB is cleaned and inspected to ensure it is free of contaminants and defects.
- Solder Paste Application: Solder paste is applied to the PCB pads using a stencil. The stencil ensures the correct amount of solder paste is deposited on each pad.
- Component Placement: The components are placed on the PCB, either manually or using an automated pick-and-place machine.
- Nitrogen Reflow Soldering: The PCB is placed in the reflow oven, and the nitrogen gas is introduced. The oven follows a predetermined temperature profile, which typically includes the following stages:
- Preheat: The PCB is gradually heated to activate the flux and remove any moisture.
- Soak: The temperature is maintained to allow the components to reach thermal equilibrium.
- Reflow: The temperature is increased to melt the solder and form the solder joints.
- Cooling: The PCB is cooled to solidify the solder joints.
- Inspection: The soldered PCB is inspected for any defects or issues, such as bridging, insufficient solder, or misaligned components.
Reflow Profile Considerations
Developing an appropriate reflow profile is crucial for successful nitrogen reflow soldering. The profile should be tailored to the specific solder paste and components used. Key factors to consider include:
- Ramp rate: The rate at which the temperature increases during the preheat and reflow stages.
- Soak time and temperature: The duration and temperature of the soak stage, which allows the components to reach thermal equilibrium.
- Peak temperature: The maximum temperature reached during the reflow stage, which must be high enough to melt the solder but not so high as to damage the components.
- Time above liquidus (TAL): The amount of time the solder is above its melting point, which is necessary for proper wetting and joint formation.
Best Practices for Nitrogen Reflow Soldering
- Nitrogen Purity: Use high-purity nitrogen gas (99.999% or better) to ensure minimal oxidation during the reflow process.
- Nitrogen Flow Rate: Maintain a consistent nitrogen flow rate throughout the reflow process to ensure an inert atmosphere. The ideal flow rate depends on the size of the reflow oven and the PCB being soldered.
- Moisture Control: Ensure the PCBs and components are properly stored and handled to minimize moisture absorption, which can lead to defects during reflow.
- Stencil Design: Use a well-designed stencil for solder paste application to ensure the correct amount of solder is deposited on each pad. Consider factors such as aperture size, shape, and pitch.
- Reflow Profile Optimization: Continuously monitor and optimize the reflow profile to ensure it is suitable for the specific PCB and components being soldered. Use thermal profiling equipment to verify the actual temperatures achieved during the process.
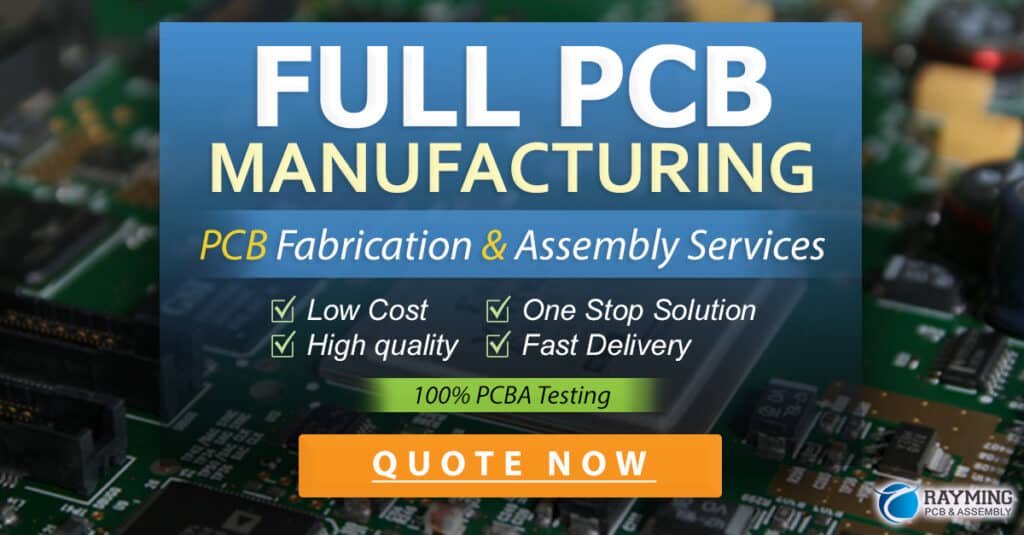
Troubleshooting Common Issues
Despite best efforts, issues can still arise during nitrogen reflow soldering. Some common problems and their potential solutions include:
- Solder Bridging: Caused by excessive solder paste or incorrect stencil design. Solutions include adjusting the stencil aperture size or using a finer pitch stencil.
- Insufficient Solder: Caused by inadequate solder paste deposition or incorrect reflow profile. Solutions include increasing the stencil aperture size or adjusting the reflow profile to ensure proper solder melting.
- Component Shifting: Caused by improper component placement or incorrect reflow profile. Solutions include using a pick-and-place machine for accurate component placement and optimizing the reflow profile to minimize component movement.
- Voiding: Caused by moisture in the PCB or components, or incorrect reflow profile. Solutions include proper moisture control and optimizing the reflow profile to minimize voiding.
FAQ
-
What are the main advantages of using nitrogen in reflow soldering?
The main advantages of using nitrogen in reflow soldering are reduced oxidation, improved wetting, reduced voiding, and an increased process window. -
How pure should the nitrogen gas be for reflow soldering?
For optimal results, use high-purity nitrogen gas (99.999% or better) in the reflow soldering process. -
Can nitrogen reflow soldering be used for all types of PCBs and components?
Yes, nitrogen reflow soldering can be used for a wide range of PCBs and components. However, the reflow profile must be tailored to the specific materials and components used. -
What equipment is needed for nitrogen reflow soldering?
The main equipment needed for nitrogen reflow soldering includes a reflow oven with nitrogen capability, a nitrogen gas supply, and stencils for solder paste application. -
How can I optimize the nitrogen reflow soldering process?
To optimize the nitrogen reflow soldering process, focus on maintaining high nitrogen purity, controlling the nitrogen flow rate, minimizing moisture in the PCBs and components, using well-designed stencils, and continuously monitoring and adjusting the reflow profile.
Conclusion
Nitrogen reflow soldering is a powerful technique for improving the quality and reliability of solder joints in PCB assembly. By creating an inert atmosphere during the reflow process, nitrogen reflow soldering minimizes oxidation, improves wetting, reduces voiding, and increases the process window. Implementing best practices, such as using high-purity nitrogen gas, controlling moisture, and optimizing the reflow profile, can help ensure successful and consistent results. With the information provided in this guide, you should be well-equipped to implement nitrogen reflow soldering in your PCB assembly process.
No responses yet