Introduction to Flexible Printed Circuit Board Assembly (FPCBA)
Flexible Printed Circuit Board Assembly (FPCBA) is a cutting-edge technology that has revolutionized the electronics industry. FPCBA involves the assembly of flexible printed circuit boards, which are thin, lightweight, and highly flexible substrates that can be bent, twisted, and folded without damaging the circuitry. This technology has enabled the development of smaller, more compact, and more reliable electronic devices that can withstand harsh environments and extreme conditions.
In recent years, the demand for FPCBA has grown exponentially due to the increasing popularity of wearable devices, medical equipment, automotive electronics, and aerospace applications. As a result, the global FPCBA market is expected to reach $27.7 billion by 2024, growing at a CAGR of 11.2% from 2019 to 2024.
Benefits of FPCBA
FPCBA offers several benefits over traditional Rigid PCBs, including:
-
Flexibility: FPCBA can be bent, twisted, and folded without damaging the circuitry, making it ideal for applications that require flexibility and durability.
-
Lightweight: FPCBA is much lighter than traditional rigid PCBs, making it ideal for applications that require weight reduction, such as aerospace and automotive electronics.
-
Space-saving: FPCBA can be designed to fit into tight spaces and conform to irregular shapes, making it ideal for applications that require miniaturization and space optimization.
-
High-density interconnects: FPCBA can accommodate high-density interconnects, enabling the development of more complex and sophisticated electronic devices.
-
Improved reliability: FPCBA is more reliable than traditional rigid PCBs due to its ability to withstand vibration, shock, and thermal stress.
Applications of FPCBA
FPCBA is used in a wide range of applications, including:
-
Wearable devices: FPCBA is used in the development of wearable devices, such as smartwatches, fitness trackers, and medical monitoring devices.
-
Medical equipment: FPCBA is used in the development of medical equipment, such as implantable devices, surgical instruments, and diagnostic tools.
-
Automotive electronics: FPCBA is used in the development of automotive electronics, such as infotainment systems, advanced driver assistance systems (ADAS), and electric vehicle (EV) batteries.
-
Aerospace applications: FPCBA is used in the development of aerospace applications, such as avionics, satellite communications, and space exploration equipment.
-
Consumer electronics: FPCBA is used in the development of consumer electronics, such as smartphones, tablets, and laptops.
FPCBA Manufacturing Process
The FPCBA manufacturing process involves several steps, including:
1. Substrate Selection
The first step in the FPCBA manufacturing process is substrate selection. The substrate is the base material on which the circuit is printed, and it must be flexible, durable, and able to withstand the intended application environment. Common substrate materials include polyimide, polyester, and polyethylene naphthalate (PEN).
2. Circuit Design
The next step is circuit design, which involves creating a schematic diagram of the circuit and laying out the components and interconnects on the substrate. This step requires the use of specialized software tools, such as EDA (electronic design automation) software.
3. Printing
Once the circuit design is complete, the next step is printing the circuit onto the substrate. This is typically done using a screen printing process, where a stencil is used to apply conductive ink onto the substrate in the desired pattern. The ink is then cured using heat or UV light to create a permanent circuit.
4. Component Placement
After the circuit is printed, the next step is component placement. This involves placing the electronic components, such as resistors, capacitors, and integrated circuits, onto the substrate in the appropriate locations. This step is typically automated using pick-and-place machines.
5. Soldering
Once the components are placed, the next step is soldering, which involves attaching the components to the substrate using a conductive adhesive or solder paste. This step is typically done using a reflow oven, which heats the substrate and components to melt the solder paste and create a permanent bond.
6. Inspection and Testing
After soldering, the FPCBA undergoes inspection and testing to ensure that it meets the required specifications and functionality. This step may involve visual inspection, electrical testing, and functional testing.
7. Finishing
Finally, the FPCBA undergoes finishing, which may involve applying a protective coating, laminating the circuit, or adding connectors or other hardware. The finished FPCBA is then packaged and shipped to the customer.
FPCBA Design Considerations
Designing an FPCBA requires careful consideration of several factors, including:
1. Flexibility Requirements
The flexibility requirements of the FPCBA must be carefully considered during the design process. This includes determining the required bend radius, the number of flex cycles, and the expected environmental conditions.
2. Material Selection
The selection of materials for the FPCBA is critical to its performance and reliability. This includes selecting the appropriate substrate material, conductive ink, and component materials.
3. Circuit Layout
The circuit layout must be carefully designed to ensure proper functioning and reliability. This includes placing components in the appropriate locations, routing traces to minimize crosstalk and interference, and designing for manufacturability.
4. Thermal Management
Thermal management is critical in FPCBA design, as the flexible substrate may not dissipate heat as effectively as a rigid PCB. This includes selecting components with appropriate power ratings, designing for adequate airflow, and using thermal management techniques such as heat sinks or thermal vias.
5. Mechanical Stress
Mechanical stress is a major consideration in FPCBA design, as the flexible substrate may be subjected to bending, twisting, and stretching. This includes designing for strain relief, using appropriate adhesives and coatings, and testing for mechanical durability.
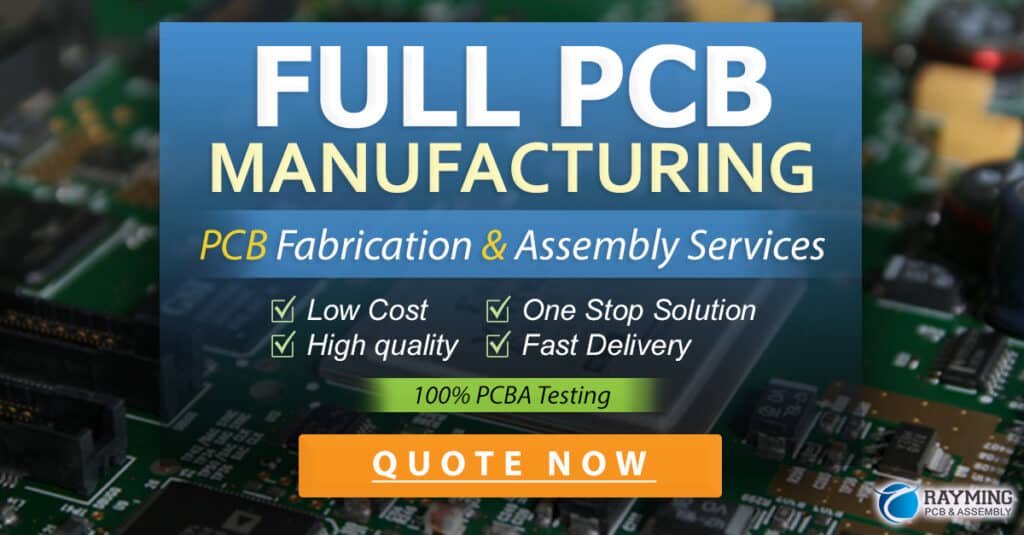
FPCBA Testing and Inspection
Testing and inspection are critical steps in the FPCBA manufacturing process to ensure the quality and reliability of the finished product. Common testing and inspection methods include:
1. Visual Inspection
Visual inspection is the first step in FPCBA testing and involves visually examining the FPCBA for defects such as misaligned components, poor soldering, or damaged traces.
2. Electrical Testing
Electrical testing involves testing the FPCBA for proper functioning and performance. This may include continuity testing, resistance testing, and functional testing.
3. Environmental Testing
Environmental testing involves subjecting the FPCBA to simulated environmental conditions to ensure its durability and reliability. This may include temperature cycling, humidity testing, and vibration testing.
4. Mechanical Testing
Mechanical testing involves subjecting the FPCBA to mechanical stress to ensure its durability and reliability. This may include bending, twisting, and stretching the FPCBA to simulate real-world conditions.
5. X-Ray Inspection
X-ray inspection involves using X-ray imaging to examine the internal structure of the FPCBA for defects such as voids, cracks, or delamination.
FPCBA Market Trends and Forecasts
The global FPCBA market is expected to experience significant growth in the coming years, driven by several key trends and factors:
1. Increasing Demand for Wearable Devices
The increasing popularity of wearable devices, such as smartwatches and fitness trackers, is driving demand for FPCBA. These devices require lightweight, flexible, and durable circuits that can withstand the rigors of daily use.
2. Growing Adoption of IoT Devices
The growing adoption of Internet of Things (IoT) devices, such as smart home appliances and industrial sensors, is also driving demand for FPCBA. These devices require small, flexible circuits that can be easily integrated into the device design.
3. Advancements in FPCBA Technology
Advancements in FPCBA technology, such as the development of new substrate materials and printing techniques, are enabling the development of more complex and sophisticated circuits. This is opening up new applications and market opportunities for FPCBA.
4. Increasing Demand for Miniaturization
The increasing demand for miniaturization in electronic devices is driving the adoption of FPCBA. FPCBA enables the development of smaller, more compact devices that can be easily integrated into a wide range of applications.
5. Growing Automotive Electronics Market
The growing automotive electronics market is also driving demand for FPCBA. Automotive electronics require reliable, durable circuits that can withstand harsh environmental conditions, and FPCBA is well-suited for these applications.
According to a recent market research report, the global FPCBA market is expected to reach $27.7 billion by 2024, growing at a CAGR of 11.2% from 2019 to 2024. The report segments the market by application, material, and region, and provides a detailed analysis of the market trends, drivers, and challenges.
Application | 2019 Market Size ($ Billion) | 2024 Market Size ($ Billion) | CAGR (2019-2024) |
---|---|---|---|
Consumer Electronics | 7.2 | 12.3 | 11.3% |
Automotive Electronics | 4.1 | 7.5 | 12.8% |
Medical Devices | 2.3 | 4.2 | 12.7% |
Aerospace & Defense | 1.8 | 3.1 | 11.5% |
Others | 0.6 | 1.1 | 12.9% |
Total | 16.0 | 27.7 | 11.2% |
The report also highlights the key players in the FPCBA market, including:
- Nippon Mektron
- Zhen Ding Technology
- Fujikura
- M-Flex
- Interflex
- Flexium
- Xiamen Hongxin Electron-Tech
- Flexcom
- MFLEX
- Sumitomo Electric Industries
These companies are investing heavily in R&D and product innovation to stay ahead of the competition and capture a larger share of the growing FPCBA market.
Conclusion
FPCBA is a cutting-edge technology that is transforming the electronics industry. Its unique properties, such as flexibility, lightweight, and high-density interconnects, make it ideal for a wide range of applications, from wearable devices to automotive electronics. As the demand for smaller, more compact, and more reliable electronic devices continues to grow, the adoption of FPCBA is expected to accelerate in the coming years.
However, designing and manufacturing FPCBA requires careful consideration of several factors, including flexibility requirements, material selection, circuit layout, thermal management, and mechanical stress. Testing and inspection are also critical steps in the FPCBA manufacturing process to ensure the quality and reliability of the finished product.
As the FPCBA market continues to evolve and grow, we can expect to see new innovations and applications emerge, driven by advancements in technology and changing market demands. Companies that can stay ahead of the curve and deliver high-quality, reliable FPCBA Solutions will be well-positioned to capture a significant share of this growing market.
Frequently Asked Questions (FAQ)
1. What is Flexible Printed Circuit Board Assembly (FPCBA)?
Flexible Printed Circuit Board Assembly (FPCBA) is a process of assembling electronic components onto a flexible substrate to create a functional circuit board. The flexible substrate allows the circuit board to bend and flex without damaging the electronic components.
2. What are the advantages of FPCBA over traditional rigid PCBs?
FPCBA offers several advantages over traditional rigid PCBs, including:
- Flexibility: FPCBA can be bent, twisted, and folded without damaging the circuitry.
- Lightweight: FPCBA is much lighter than traditional rigid PCBs.
- Space-saving: FPCBA can be designed to fit into tight spaces and conform to irregular shapes.
- High-density interconnects: FPCBA can accommodate high-density interconnects, enabling the development of more complex and sophisticated electronic devices.
- Improved reliability: FPCBA is more reliable than traditional rigid PCBs due to its ability to withstand vibration, shock, and thermal stress.
3. What are the common applications of FPCBA?
FPCBA is used in a wide range of applications, including:
- Wearable devices, such as smartwatches and fitness trackers
- Medical equipment, such as implantable devices and surgical instruments
- Automotive electronics, such as infotainment systems and advanced driver assistance systems (ADAS)
- Aerospace applications, such as avionics and satellite communications
- Consumer electronics, such as smartphones and tablets
4. What are the key steps in the FPCBA manufacturing process?
The key steps in the FPCBA manufacturing process include:
- Substrate selection
- Circuit design
- Printing
- Component placement
- Soldering
- Inspection and testing
- Finishing
5. What are the key market trends and forecasts for the FPCBA industry?
The global FPCBA market is expected to experience significant growth in the coming years, driven by several key trends and factors, including:
- Increasing demand for wearable devices
- Growing adoption of IoT devices
- Advancements in FPCBA technology
- Increasing demand for miniaturization
- Growing automotive electronics market
According to a recent market research report, the global FPCBA market is expected to reach $27.7 billion by 2024, growing at a CAGR of 11.2% from 2019 to 2024.
No responses yet