What is a Rigid PCB?
A Rigid PCB, short for Rigid Printed Circuit Board, is a type of circuit board that is made from a solid, non-flexible material, typically fiberglass or a composite of fiberglass and epoxy resin. This rigid construction provides a stable platform for electronic components and ensures reliable performance in various applications.
Rigid PCBs are the most common type of PCBs used in electronic devices, ranging from everyday consumer electronics to complex industrial equipment. They offer several advantages over flexible PCBs, including:
- Higher durability and resistance to physical stress
- Better heat dissipation properties
- Easier to design and manufacture
- Lower cost for high-volume production
Types of Rigid PCBs
Rigid PCBs can be classified based on the number of layers they contain:
- Single-layer PCBs
- Consist of a single conductive layer
- Used in simple, low-cost applications
-
Examples: LED lighting, power supplies, and basic electronic toys
-
Double-layer PCBs
- Have two conductive layers, one on each side of the substrate
- Allows for more complex circuits and higher component density
-
Examples: amplifiers, power monitoring systems, and automotive electronics
-
Multi-layer PCBs
- Feature three or more conductive layers
- Enable highly complex circuits and high component density
- Examples: computer motherboards, smartphones, and medical devices
Here’s a table comparing the different types of Rigid PCBs:
PCB Type | Layers | Complexity | Cost | Applications |
---|---|---|---|---|
Single-layer | 1 | Low | Low | Simple, low-cost electronics |
Double-layer | 2 | Medium | Medium | More complex circuits, higher density |
Multi-layer | 3+ | High | High | Highly complex, dense circuits |
Materials Used in Rigid PCBs
The choice of materials used in the construction of a Rigid PCB can greatly impact its performance, durability, and cost. The most common materials include:
Substrate Materials
- FR-4
- A composite of fiberglass and epoxy resin
- Offers excellent mechanical and electrical properties
-
Most widely used substrate material for Rigid PCBs
-
Ceramic
- Provides superior heat dissipation and thermal stability
- Ideal for high-temperature applications
-
More expensive than FR-4
-
Aluminum
- Offers excellent thermal conductivity
- Used in applications requiring efficient heat dissipation
- Can be more challenging to work with compared to FR-4
Conductive Materials
- Copper
- The most common conductive material used in Rigid PCBs
- Offers excellent electrical conductivity and thermal properties
-
Available in various thicknesses (denoted by weight, e.g., 1 oz, 2 oz)
-
Gold
- Used for specialized applications requiring high corrosion resistance
- Provides excellent electrical conductivity
-
More expensive than copper
-
Silver
- Offers the highest electrical conductivity among metals
- Used in high-frequency applications
- More expensive than copper and can tarnish over time
Rigid PCB Manufacturing Process
The manufacturing process for Rigid PCBs involves several steps, each critical to ensuring the quality and reliability of the final product. The main stages include:
- Design and Preparation
- Creating the PCB layout using CAD software
- Generating Gerber files for manufacturing
-
Selecting the appropriate materials and specifications
-
Printing and Etching
- Printing the circuit pattern onto the copper-clad substrate
-
Etching away the unwanted copper, leaving only the desired traces
-
Drilling and Plating
- Drilling holes for through-hole components and vias
-
Plating the holes with copper to establish electrical connections
-
Solder Mask Application
- Applying a protective solder mask to the PCB surface
-
Prevents solder bridges and provides insulation
-
Silkscreen Printing
- Adding text, logos, and component outlines to the PCB surface
-
Helps with component placement and identification
-
Surface Finish Application
- Applying a surface finish (e.g., HASL, ENIG, OSP) to the exposed copper
-
Protects the copper from oxidation and improves solderability
-
Electrical Testing and Inspection
- Performing electrical tests to ensure the PCB functions as intended
- Visually inspecting the PCB for defects or manufacturing issues
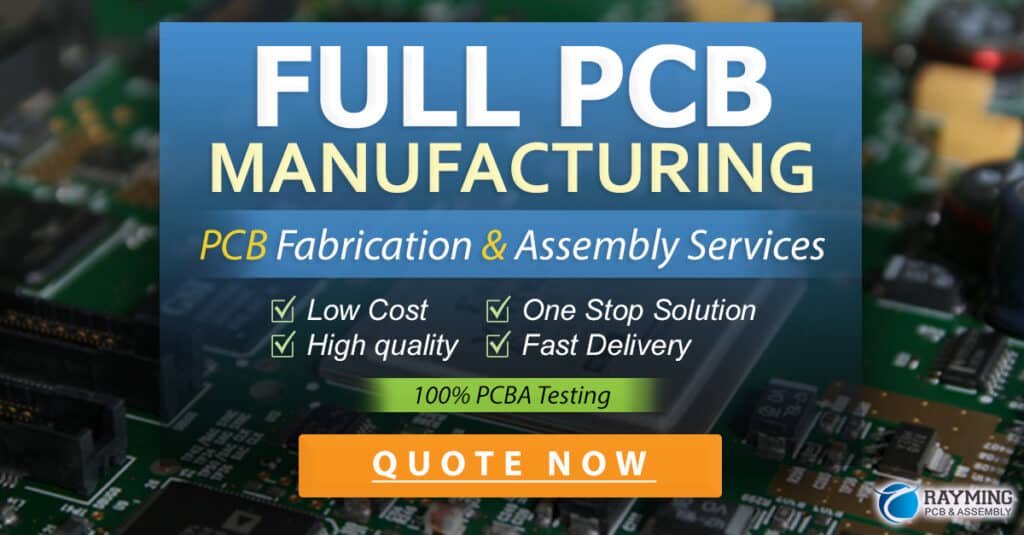
Designing a Rigid PCB
Designing a Rigid PCB requires careful consideration of several factors to ensure optimal performance, reliability, and manufacturability. Some key aspects to consider include:
Schematic Design
- Create a schematic diagram that represents the electrical connections between components
- Use CAD software (e.g., Eagle, KiCad, Altium) to create the schematic
- Verify the schematic for errors and ensure it meets the design requirements
Component Placement
- Arrange components on the PCB layout in a logical and efficient manner
- Consider factors such as signal integrity, heat dissipation, and mechanical constraints
- Ensure adequate spacing between components to facilitate manufacturing and assembly
Trace Routing
- Route the traces between components according to the schematic
- Consider factors such as trace width, spacing, and impedance matching
- Use CAD software’s auto-routing features or route traces manually
Design Rule Check (DRC)
- Perform a DRC to ensure the PCB layout meets the manufacturing specifications
- Check for issues such as minimum trace width, spacing, and hole sizes
- Resolve any DRC violations before proceeding to manufacturing
Gerber File Generation
- Generate Gerber files from the PCB layout software
- Gerber files contain the information needed for manufacturing, such as copper layers, solder mask, and silkscreen
- Verify the Gerber files for accuracy and completeness before sending them to the manufacturer
Applications of Rigid PCBs
Rigid PCBs find applications in a wide range of industries and products, including:
- Consumer Electronics
- Smartphones, tablets, and laptops
- Home appliances and smart home devices
-
Gaming consoles and peripherals
-
Automotive Electronics
- Engine control units (ECUs)
- Infotainment systems and GPS navigation
-
Sensor and control modules
-
Industrial Equipment
- Process control systems
- Automation and robotics
-
Power electronics and motor drives
-
Medical Devices
- Diagnostic and imaging equipment
- Patient monitoring systems
-
Implantable devices and wearables
-
Aerospace and Defense
- Avionics and flight control systems
- Radar and communication equipment
- Satellite and spacecraft electronics
Advantages of Rigid PCBs
Rigid PCBs offer several advantages over other types of circuit boards, making them the preferred choice for many applications:
- Durability and Reliability
- Rigid construction withstands physical stress and vibration
- Resistant to bending and flexing, which can cause component or trace damage
-
Suitable for harsh environmental conditions
-
Excellent Heat Dissipation
- Rigid substrates, such as FR-4 and aluminum, provide good thermal conductivity
- Efficiently dissipates heat generated by components, improving system reliability
-
Allows for higher power densities and increased component lifetimes
-
High Component Density
- Multi-layer Rigid PCBs enable high component density and complex circuits
- Allows for smaller form factors and reduced system size
-
Facilitates the design of compact, high-performance electronic devices
-
Cost-Effective for High-Volume Production
- Rigid PCBs are well-suited for automated assembly processes
- High-volume production leads to lower per-unit costs
- Economies of scale make Rigid PCBs an attractive option for mass-produced electronics
Challenges and Considerations
While Rigid PCBs offer numerous benefits, there are also some challenges and considerations to keep in mind:
- Limited Flexibility
- Rigid PCBs are not suitable for applications requiring flexibility or conformity to irregular shapes
-
Flexible PCBs or hybrid Rigid-Flex PCBs may be necessary for certain designs
-
Higher Initial Setup Costs
- The tooling and setup costs for Rigid PCBs can be higher compared to other technologies
-
This can be a barrier for low-volume production or prototyping
-
Design Complexity
- As circuits become more complex, designing Rigid PCBs can be challenging
- Ensuring signal integrity, managing EMI/EMC, and optimizing component placement require expertise
-
Specialized CAD software and skilled designers are necessary for successful Rigid PCB design
-
Manufacturing Limitations
- Rigid PCBs have certain manufacturing limitations, such as minimum trace widths and spacing
- Designers must adhere to the manufacturing capabilities of the chosen fabrication house
- Communication between the designer and manufacturer is crucial to ensure successful production
Frequently Asked Questions (FAQ)
- What is the difference between a Rigid PCB and a Flexible PCB?
-
Rigid PCBs are made from a solid, non-flexible substrate, while Flexible PCBs use a flexible polymer material. Rigid PCBs are more durable and offer better heat dissipation, while Flexible PCBs are suitable for applications requiring flexibility or conformity to irregular shapes.
-
How do I choose the right material for my Rigid PCB?
-
The choice of material depends on factors such as the application, environmental conditions, and budget. FR-4 is the most common substrate material and is suitable for most general-purpose applications. Ceramic and aluminum substrates are used for high-temperature or high-power applications that require better heat dissipation.
-
What is the maximum number of layers possible in a Rigid PCB?
-
The maximum number of layers in a Rigid PCB is typically limited by the manufacturing capabilities of the fabrication house. Most manufacturers can produce Rigid PCBs with up to 20 layers, while some specialized facilities can handle even higher layer counts. However, as the number of layers increases, so does the complexity and cost of the PCB.
-
Can Rigid PCBs be used in high-frequency applications?
-
Yes, Rigid PCBs can be used in high-frequency applications, such as RF and microwave circuits. However, careful design considerations must be made to ensure signal integrity and minimize losses. This may involve using specialized substrate materials, such as PTFE or Rogers laminates, and employing advanced design techniques, such as impedance matching and controlled impedance routing.
-
How can I ensure the manufacturability of my Rigid PCB design?
- To ensure the manufacturability of your Rigid PCB design, follow these best practices:
- Adhere to the design rules and guidelines provided by your chosen fabrication house
- Use CAD software to perform Design Rule Checks (DRC) and resolve any violations
- Communicate with your manufacturer early in the design process to discuss any specific requirements or constraints
- Provide clear and accurate documentation, including Gerber files, drill files, and assembly drawings
- Consider the manufacturing capabilities and limitations when making design decisions, such as minimum trace widths and spacing
In conclusion, Rigid PCBs are a versatile and reliable choice for a wide range of electronic applications. By understanding the fundamentals of Rigid PCBs, including materials, manufacturing processes, design considerations, and applications, beginners can make informed decisions when developing their electronic projects. As with any complex engineering task, successful Rigid PCB design and manufacturing require a combination of technical knowledge, practical skills, and effective communication between designers and fabrication houses.
No responses yet