What is a Double Sided PCB?
A double-sided PCB, also known as a two-layer PCB, is a printed circuit board that has conductive copper layers on both sides of the insulating substrate. This allows for the placement of components and the routing of traces on both sides of the board, effectively doubling the available surface area for the circuit design. Double-sided PCBs offer several advantages over single-sided PCBs, including:
- Increased component density
- More complex circuit designs
- Improved signal integrity
- Better heat dissipation
- Reduced electromagnetic interference (EMI)
The Structure of a Double Sided PCB
A typical double-sided PCB consists of several layers, each serving a specific purpose. The main layers in a double-sided PCB include:
1. Substrate (Core) Material
The substrate, or core material, is the insulating layer that serves as the foundation of the PCB. It provides mechanical support and electrical insulation between the conductive layers. Common substrate materials include:
- FR-4: A glass-reinforced epoxy laminate, FR-4 is the most widely used substrate material for PCBs. It offers good mechanical strength, thermal stability, and electrical insulation properties.
- CEM-1 and CEM-3: Composite epoxy materials (CEM) are lower-cost alternatives to FR-4. They consist of a combination of woven glass and paper reinforcement impregnated with epoxy resin.
- Polyimide: Polyimide substrates are used in high-temperature applications due to their excellent thermal stability and low dielectric constant.
- PTFE (Teflon): PTFE substrates are used in high-frequency applications because of their low dielectric constant and low dissipation factor.
Substrate Material | Dielectric Constant | Dissipation Factor | Thermal Stability | Cost |
---|---|---|---|---|
FR-4 | 4.5 – 4.7 | 0.02 | Good | Low |
CEM-1 & CEM-3 | 4.5 – 4.7 | 0.02 – 0.03 | Moderate | Low |
Polyimide | 3.4 – 3.5 | 0.002 – 0.003 | Excellent | High |
PTFE (Teflon) | 2.0 – 2.1 | 0.0002 – 0.0008 | Excellent | High |
2. Copper Layers
The copper layers are the conductive parts of the PCB that carry electrical signals and provide a means for component interconnection. In a double-sided PCB, there are two copper layers, one on each side of the substrate. The thickness of the copper layers is typically measured in ounces per square foot (oz/ft²) and can range from 0.5 oz/ft² to 2 oz/ft² or more, depending on the application requirements.
The copper layers are usually electrodeposited or rolled onto the substrate material and then patterned using a photolithography process to create the desired circuit traces, pads, and vias.
3. Soldermask
The soldermask is a protective layer applied on top of the copper layers, leaving only the exposed pads and vias for component soldering. It serves several purposes, including:
- Protecting the copper traces from oxidation and corrosion
- Preventing solder bridges between closely spaced pads
- Providing electrical insulation between adjacent traces
- Improving the aesthetics of the PCB by providing a uniform color (often green, red, or blue)
Soldermask materials are typically made of epoxy or acrylic-based polymers and are applied using screen printing or photoimaging techniques.
4. Silkscreen
The silkscreen layer is a non-conductive layer printed on top of the soldermask that contains text, logos, and component outlines. It serves as a visual aid for component placement and identification during assembly and troubleshooting. Silkscreen ink is typically white, but other colors can be used for better contrast or aesthetics.
5. Surface Finish
The surface finish is a protective coating applied to the exposed copper pads and vias to prevent oxidation and improve solderability. Common surface finishes for double-sided PCBs include:
- Hot Air Solder Leveling (HASL): A tin-lead alloy is applied to the exposed copper using a hot air leveling process. HASL provides good solderability and is relatively inexpensive.
- Organic Solderability Preservative (OSP): A thin, organic coating is applied to the copper to protect it from oxidation. OSP is a low-cost, lead-free option but has a limited shelf life.
- Electroless Nickel Immersion Gold (ENIG): A layer of nickel is electrolessly plated onto the copper, followed by a thin layer of gold. ENIG provides excellent solderability, flatness, and shelf life, but is more expensive than HASL or OSP.
- Immersion Silver: A thin layer of silver is chemically deposited onto the copper. Immersion silver offers good solderability and is a cost-effective lead-free option.
Surface Finish | Solderability | Shelf Life | Flatness | Cost |
---|---|---|---|---|
HASL | Good | Moderate | Moderate | Low |
OSP | Moderate | Limited | Good | Low |
ENIG | Excellent | Excellent | Excellent | High |
Immersion Silver | Good | Good | Good | Moderate |
Materials Used in Double Sided PCBs
The choice of materials used in double-sided PCBs depends on various factors, such as the application requirements, operating environment, and cost constraints. Some of the key materials used in the construction of double-sided PCBs include:
1. Copper Foil
Copper foil is the most common conductor material used in PCBs due to its excellent electrical conductivity, thermal conductivity, and solderability. The thickness of the copper foil is typically expressed in ounces per square foot (oz/ft²), with common thicknesses ranging from 0.5 oz/ft² to 2 oz/ft² or more. Thicker copper foils are used in high-current applications or to improve heat dissipation.
2. Prepreg
Prepreg, short for pre-impregnated, is a type of composite material used in the construction of multi-layer PCBs. It consists of a woven glass fabric impregnated with a partially cured epoxy resin. Prepreg is used as an insulating layer between the copper layers and helps to bond them together during the lamination process.
3. Solder Mask Ink
Solder mask ink is a polymer-based material used to create the soldermask layer on the PCB. It is typically applied using screen printing or photoimaging techniques and cured using UV light or heat. Solder mask ink is available in various colors, with green being the most common.
4. Silkscreen Ink
Silkscreen ink is a non-conductive polymer-based material used to print text, logos, and component outlines on the PCB. It is typically white in color but can be available in other colors for improved contrast or aesthetics.
5. Surface Finish Materials
The materials used for the surface finish depend on the chosen finish type. For example:
- HASL: Tin-lead alloy
- OSP: Organic compounds, such as benzimidazole or imidazole
- ENIG: Electroless nickel and immersion gold
- Immersion Silver: Silver compounds, such as silver nitrate
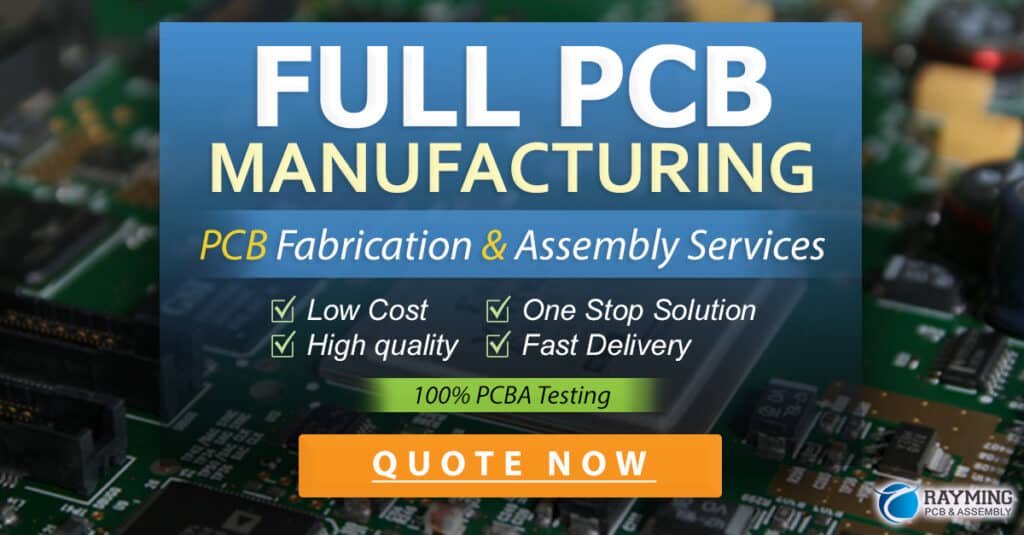
Manufacturing Process for Double Sided PCBs
The manufacturing process for double-sided PCBs involves several steps, each requiring specific materials and techniques. The main steps in the manufacturing process include:
-
Design and Layout: The PCB design is created using electronic design automation (EDA) software, which generates the necessary files for manufacturing, such as Gerber files and drill files.
-
Substrate Preparation: The substrate material is cut to the required size and cleaned to remove any contaminants.
-
Copper Lamination: Copper foil is laminated onto both sides of the substrate using heat and pressure.
-
Drilling: Holes are drilled through the substrate and copper layers to accommodate through-hole components and vias.
-
Patterning: The copper layers are patterned using a photolithography process, which involves applying a photoresist, exposing it to UV light through a photomask, and then etching away the unwanted copper.
-
Soldermask Application: The soldermask ink is applied to the PCB using screen printing or photoimaging techniques and then cured.
-
Silkscreen Printing: The silkscreen layer is printed onto the soldermask using a screen printing process.
-
Surface Finish Application: The chosen surface finish is applied to the exposed copper pads and vias using the appropriate process (e.g., HASL, OSP, ENIG, or Immersion Silver).
-
Electrical Testing: The completed PCB is electrically tested to ensure that all connections are correct and there are no short circuits or open connections.
Advantages of Double Sided PCBs
Double-sided PCBs offer several advantages over single-sided PCBs, making them a popular choice for a wide range of electronic applications. Some of the key advantages include:
-
Increased Component Density: Double-sided PCBs allow for the placement of components on both sides of the board, enabling higher component density and more compact designs.
-
More Complex Circuit Designs: With the ability to route traces on both sides of the board, double-sided PCBs can accommodate more complex circuit designs compared to single-sided PCBs.
-
Improved Signal Integrity: Double-sided PCBs offer better signal integrity due to the ability to create shorter and more direct trace routes, reducing the impact of crosstalk and electromagnetic interference (EMI).
-
Better Heat Dissipation: The additional copper layer on the bottom side of the PCB helps to dissipate heat more effectively, which can improve the overall performance and reliability of the circuit.
-
Cost-Effective: While double-sided PCBs are more expensive than single-sided PCBs, they offer a cost-effective solution for applications that require higher component density or more complex circuitry.
Applications of Double Sided PCBs
Double-sided PCBs are used in a wide range of electronic applications, from consumer electronics to industrial control systems. Some common applications include:
- Smartphones and tablets
- Laptops and desktop computers
- Televisions and displays
- Automotive electronics
- Medical devices
- Industrial control systems
- Telecommunications equipment
- Aerospace and defense electronics
Frequently Asked Questions (FAQ)
- What is the difference between a single-sided and a double-sided PCB?
-
A single-sided PCB has conductive copper on only one side of the substrate, while a double-sided PCB has copper layers on both sides, allowing for higher component density and more complex circuit designs.
-
Can double-sided PCBs be used for high-frequency applications?
-
Yes, double-sided PCBs can be used for high-frequency applications, but the choice of substrate material and surface finish is critical. Materials like PTFE (Teflon) and low-loss prepregs are often used in high-frequency PCBs to minimize signal loss and distortion.
-
What is the most common substrate material used in double-sided PCBs?
-
FR-4, a glass-reinforced epoxy laminate, is the most widely used substrate material for double-sided PCBs due to its good mechanical strength, thermal stability, and electrical insulation properties.
-
How does the thickness of the copper layers affect the performance of a double-sided PCB?
-
Thicker copper layers can handle higher currents and provide better heat dissipation, but they also make the PCB more expensive and can affect the impedance of high-frequency signals. The choice of copper thickness depends on the specific application requirements.
-
What is the purpose of the soldermask layer in a double-sided PCB?
- The soldermask layer serves several purposes, including protecting the copper traces from oxidation and corrosion, preventing solder bridges between closely spaced pads, providing electrical insulation between adjacent traces, and improving the aesthetics of the PCB by providing a uniform color.
In conclusion, double-sided PCBs are a crucial component in modern electronics, offering numerous advantages over single-sided PCBs in terms of component density, circuit complexity, signal integrity, and heat dissipation. Understanding the structure, materials, and manufacturing process of double-sided PCBs is essential for anyone involved in the design, production, or use of electronic devices. As technology continues to advance, the demand for high-quality, reliable double-sided PCBs will only continue to grow, making it an exciting and dynamic field for professionals in the electronics industry.
No responses yet