What is PCB Assembly?
PCB assembly is the process of soldering or mounting electronic components onto a printed circuit board (PCB). The PCB serves as the base and provides electrical connections between the various components. PCB assembly can be done manually for small batches and prototypes, or automated for high volume production.
The key steps in the PCB assembly process include:
- Solder Paste Application
- Component Placement
- Reflow Soldering
- Inspection and Testing
Solder Paste Application
Solder paste, a mixture of tiny solder balls and flux, is applied to the pads on the PCB where components will be mounted. For small Batch assembly, this is often done using a stencil and manually spreading the paste. The stencil has holes that align with the pads, allowing the correct amount of solder paste to be deposited.
Component Placement
Next, the electronic components are placed onto the PCB, with their leads or pins aligned with the solder paste covered pads. For prototypes and small batches, this is usually done by hand using tweezers, though there are semi-automated machines that can assist with component placement.
The most common types of components are:
Component | Placement |
---|---|
Surface Mount (SMD) | Placed directly on pads on the PCB surface |
Through-Hole (THT) | Leads are inserted through holes in the PCB |
Reflow Soldering
After the components are placed, the PCB goes through a reflow soldering process. It’s heated in an oven following a specific temperature profile, which melts the solder balls in the paste, forming permanent electrical connections between the component leads and PCB pads as it cools.
Typical reflow temperature profiles have several stages:
Stage | Temperature | Time |
---|---|---|
Preheat | 150-180°C | 60-120 sec |
Soak | 150-180°C | 60-120 sec |
Reflow | 220-250°C | 30-60 sec |
Cooling | < 100°C | 30-90 sec |
Inspection and Testing
Finally, the assembled PCBs are inspected and tested to ensure proper connections were made and the board functions as intended. For low volume runs, this is often done visually and with multimeters or other basic test equipment. More complex designs may require custom test jigs or functional testing.
Common defects that are checked for include:
- Solder bridges
- Cold solder joints
- Missing or misaligned components
- Damaged components
- Incorrect component values/types
Advantages of Small Batch PCB Assembly
Speed and Flexibility
One of the biggest advantages of small batch PCB assembly is the speed and flexibility it provides for prototyping and low volume production. Turnaround times can be much faster than with high volume assembly, as there is less setup and programming required.
Design changes can also be implemented quicker and more easily with small batch assembly. Whereas large production runs require extensive planning and are difficult to change once in motion, prototypes assembled in small batches can be tweaked and modified as needed with each iteration.
Cost Effective for Low Quantities
For low quantities, small batch PCB assembly is often more cost effective than mass production. The high upfront costs associated with setting up automated assembly lines aren’t justified when only a small number of boards are needed.
With small batch assembly, those setup and NRE (non-recurring engineering) costs are minimal or non-existent. The tradeoff is that the per-unit cost is higher than with large volume production, but for prototypes and low quantities, the total cost is still usually lower with small batch.
Accessible for Smaller Companies and Startups
The lower costs and barrier to entry for small batch PCB assembly make it more accessible to smaller companies, startups, and even individual makers and hobbyists. Many PCB assembly services cater specifically to these lower volume customers.
Whereas mass production often requires large minimum order quantities and significant investment, small batch assembly allows these companies to prototype their designs and produce boards in quantities that align with their needs and budgets.
Challenges of Small Batch PCB Assembly
Manual Processes are Time Consuming
While small batch assembly is faster in terms of overall turnaround time, the actual assembly process is more time consuming than automated production. Manual placement of components and other tasks are slower and more tedious than using pick-and-place machines and conveyors.
This limits the number of boards that can be produced in a given time frame. As quantities increase, small batch assembly becomes less and less efficient compared to automated lines. The exact point at which automation becomes more viable varies depending on the complexity of the PCB design and the specific manufacturer’s capabilities.
Prone to Human Error
With more manual processes comes greater risk of human errors during small batch PCB assembly. Whereas automated systems are very precise and consistent, humans are more prone to mistakes like misplaced components, solder bridges, etc.
This is especially true for very small or very complex PCB designs. Fine pitch components and dense PCB layouts are difficult to assemble by hand and errors are more likely. Thorough inspection and testing become even more critical to catch any defects.
Less Suitable for Complex PCBs
Very complex PCBs with high component counts, fine pitch parts, and tight tolerances are often not suitable for complete manual assembly. The risk of errors is too high and the process would be extremely tedious and time consuming.
For these types of designs, a common compromise is to use a combination of automated and manual assembly. The bulk of the components, especially smaller SMD parts, are placed by machine, while larger or more complicated parts are placed by hand. This hybrid approach can provide a good balance of efficiency and flexibility for low volume complex PCBs.
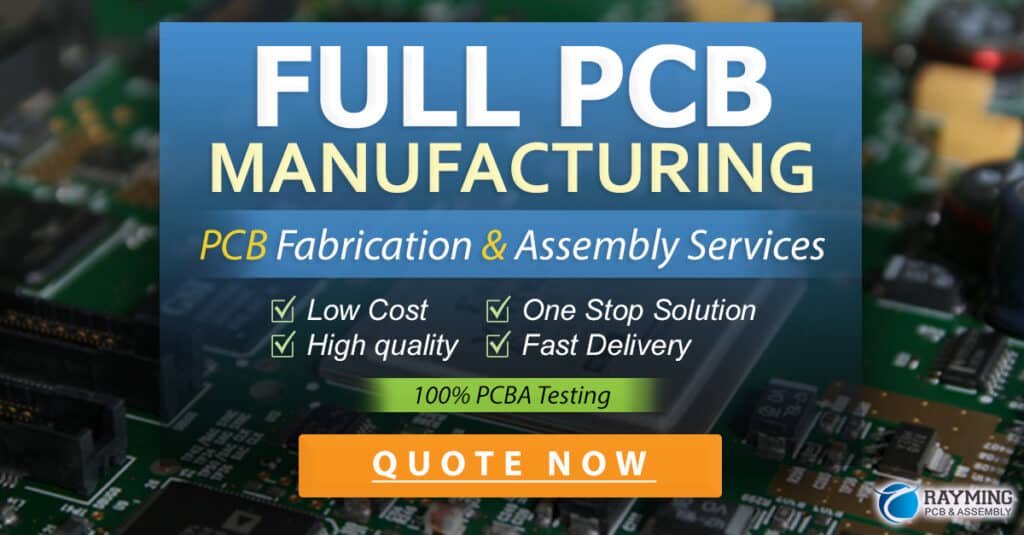
Choosing a Small Batch PCB Assembly Partner
When selecting a partner for small batch PCB assembly, there are several key factors to consider:
Technical Capabilities
Most importantly, the assembler must have the technical capabilities to produce your specific PCB design. This includes the ability to handle the required component types and sizes, meet the necessary tolerances and quality standards, and perform any special processes like conformal coating or potting.
Minimum Order Quantity (MOQ)
For small batch production, the assembler’s minimum order quantity is a key consideration. Some may have MOQs of a few dozen or hundred, while others specialize in even smaller batches or individual prototypes. Matching the assembler’s MOQ to your needs is critical for cost and efficiency.
Turnaround Time
Turnaround time is another important factor, especially for time-sensitive prototyping and low volume production. Some assemblers offer expedited services for quicker delivery, while others may have longer standard lead times. Understanding their timelines and how they align with your schedule is essential.
Quality Control and Testing
Robust quality control and testing are always important, but even more so with the higher risk of errors in manual assembly. Look for an assembler with strict inspection protocols, equipment like 3D AOI and X-ray machines for catching defects, and comprehensive testing capabilities to validate board function.
Design for Manufacturability (DFM) Support
Especially for complex designs, having a manufacturing partner that provides Design for Manufacturability (DFM) support can be invaluable. They can review your design files and provide feedback to improve manufacturability, reduce errors, and optimize the assembly process. This can save significant time and cost in the long run.
FAQ
What is the typical turnaround time for small batch PCB assembly?
Turnaround times for small batch PCB assembly can vary depending on the complexity of the design and the specific assembler, but are often in the range of 2-5 days for simple designs. More complex boards or higher quantities may take a week or more. Many assemblers offer expedited services for even faster turnaround.
What are the minimum order quantities for small batch PCB assembly?
Minimum order quantities (MOQs) for small batch PCB assembly vary between manufacturers. Some specialize in prototype quantities as low as 1-5 pieces, while others may have MOQs of 50-100 or more. It’s best to check with the specific assembler to confirm their MOQ aligns with your needs.
How much does small batch PCB Assembly Cost?
The cost of small batch PCB assembly depends on several factors including the PCB complexity, component types, quantities, and turnaround time. Setup fees and NRE Costs are often minimal compared to high volume production. Per-unit costs are higher than mass production, but for low quantities, the total cost is usually lower with small batch assembly.
What files are needed for small batch PCB assembly?
To start a small batch PCB assembly order, you’ll typically need to provide:
- Gerber files for the PCB
- Bill of Materials (BOM)
- Component placement file (Centroid/XY data)
- Assembly drawings or instructions
Some assemblers may have additional requirements or preferences for file formats.
Is small batch PCB assembly suitable for complex designs?
Small batch PCB assembly can be used for complex designs, but very dense or fine-pitch designs may not be suitable for full manual assembly. A common approach is to use a combination of automated placement for the majority of components and manual placement for larger or more specialized parts. The specific capabilities will vary by assembler.
No responses yet