What is PCB Conformal Coating?
PCB conformal coating is a protective layer applied to printed circuit boards (PCBs) to shield them from environmental factors such as moisture, dust, chemicals, and extreme temperatures. This thin polymeric film “conforms” to the contours of the board, covering the components and exposed circuitry. Conformal coatings are essential for ensuring the reliability and longevity of electronic devices, particularly those exposed to harsh conditions.
Types of Conformal Coatings
There are five primary types of conformal coatings used in the electronics industry:
-
Acrylic (AR): Acrylic coatings offer excellent moisture and fungal resistance, making them suitable for general-purpose applications. They are easy to apply and remove, making repairs and modifications relatively simple.
-
Silicone (SR): Silicone coatings provide superior protection against extreme temperatures and vibrational stresses. They are highly flexible and have a wide operating temperature range, making them ideal for high-temperature applications.
-
Polyurethane (UR): Polyurethane coatings offer excellent chemical and abrasion resistance. They provide good moisture and insulation protection, making them suitable for a wide range of applications.
-
Epoxy (ER): Epoxy coatings are known for their high chemical and abrasion resistance. They offer excellent moisture and insulation protection but are more difficult to apply and remove compared to other coatings.
-
Parylene (XY): Parylene coatings are ultra-thin, uniform, and pinhole-free. They provide superior moisture, chemical, and dielectric barrier properties. However, they require specialized vacuum deposition equipment for application.
Coating Type | Moisture Resistance | Chemical Resistance | Temperature Range | Ease of Application | Ease of Repair |
---|---|---|---|---|---|
Acrylic | Good | Fair | -40°C to 125°C | Easy | Easy |
Silicone | Excellent | Good | -65°C to 200°C | Moderate | Moderate |
Polyurethane | Very Good | Very Good | -40°C to 125°C | Moderate | Difficult |
Epoxy | Excellent | Excellent | -40°C to 150°C | Difficult | Very Difficult |
Parylene | Excellent | Excellent | -200°C to 200°C | Very Difficult | Very Difficult |
When to Use Conformal Coating
Environmental Factors
Conformal coating is essential when your PCB Assembly is exposed to environmental factors that can compromise its performance and longevity. These factors include:
-
Moisture: Humidity, condensation, and water splash can cause corrosion, short circuits, and dendritic growth on PCBs. Conformal coatings provide a barrier against moisture ingress, preventing these issues.
-
Dust and Debris: Airborne particles can settle on PCBs, causing short circuits and interfering with the proper functioning of components. Conformal coatings prevent dust and debris from accumulating on the board surface.
-
Chemical Exposure: In industrial environments, PCBs may be exposed to chemicals such as oils, fuels, and cleaning agents. Conformal coatings protect against chemical contamination and corrosion.
-
Temperature Extremes: High temperatures can cause thermal stress, while low temperatures can lead to condensation. Conformal coatings help PCBs withstand extreme temperature fluctuations and thermal cycling.
-
Vibration and Shock: In automotive, aerospace, and military applications, PCBs are subject to vibration and mechanical shock. Conformal coatings provide a cushioning effect, reducing the risk of component damage and fatigue.
Application-Specific Requirements
Certain applications have specific requirements that necessitate the use of conformal coating:
-
Aerospace and Defense: PCBs used in aerospace and defense equipment must withstand extreme environmental conditions and meet stringent reliability standards. Conformal coating is mandatory for these applications.
-
Automotive Electronics: Automotive PCBs are exposed to harsh conditions, including temperature fluctuations, humidity, and vibration. Conformal coating is essential for ensuring the reliability and longevity of these components.
-
Medical Devices: Medical electronic devices must be protected against moisture, chemicals, and contamination to ensure patient safety and device reliability. Conformal coating is crucial for meeting regulatory requirements.
-
Industrial Control Systems: Industrial PCBs are often exposed to harsh environments, including dust, moisture, and chemical contaminants. Conformal coating is necessary for maintaining the reliability and performance of these systems.
-
Outdoor Electronics: PCBs used in outdoor applications, such as solar inverters and telecommunications equipment, must withstand exposure to moisture, UV radiation, and temperature extremes. Conformal coating is essential for protecting these components.
Choosing the Right Conformal Coating
When selecting a conformal coating for your PCB assembly, consider the following factors:
-
Environmental Conditions: Choose a coating that provides adequate protection against the specific environmental factors your PCB will be exposed to, such as moisture, chemicals, or extreme temperatures.
-
Material Compatibility: Ensure that the coating is compatible with the materials used in your PCB assembly, including the substrate, components, and soldering materials.
-
Application Method: Consider the available application methods, such as spray, brush, dip, or selective coating, and choose a coating that is compatible with your preferred method.
-
Reworkability: If your PCB assembly requires frequent repairs or modifications, choose a coating that is easy to remove and reapply, such as acrylic or silicone.
-
Cost: Evaluate the cost of the coating material, application equipment, and processing time to ensure that it fits within your budget constraints.
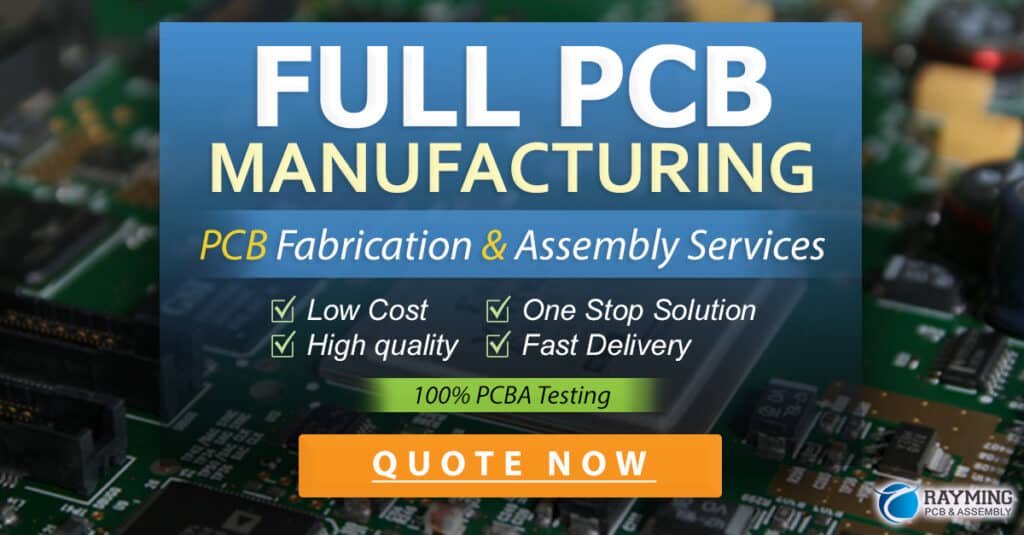
Applying Conformal Coating
Preparation
Before applying conformal coating, ensure that your PCB assembly is clean, dry, and free from contaminants. Follow these steps:
-
Clean the PCB: Use a solvent cleaner to remove any flux residue, oils, or dirt from the board surface. Ensure that the cleaner is compatible with the PCB materials and components.
-
Dry the PCB: Allow the board to dry completely, either by air drying or using a baking oven. Moisture trapped under the coating can cause corrosion and other issues.
-
Mask off areas: Use masking tape or latex to cover any areas that should not be coated, such as connectors, test points, or adjustable components.
Application Methods
There are several methods for applying conformal coating:
-
Spraying: Spraying is the most common method for applying conformal coatings. It provides a uniform coating thickness and is suitable for large-volume production. However, it requires careful masking and overspray control.
-
Brushing: Brushing is a manual method suitable for small-volume production or touch-up work. It allows for precise application but may result in an uneven coating thickness.
-
Dipping: Dipping involves immersing the PCB assembly in a tank of coating material. It provides a uniform coating thickness but may require additional processing steps, such as draining and curing.
-
Selective Coating: Selective coating uses automated dispensing equipment to apply coating only to specific areas of the PCB. This method minimizes masking requirements and reduces material waste.
Curing
After application, the conformal coating must be cured to achieve its full protective properties. Curing methods include:
-
Air Drying: Some coatings, such as acrylics, can be cured by simply allowing them to air dry at room temperature for a specified time.
-
Heat Curing: Other coatings, such as epoxies and polyurethanes, require elevated temperatures for proper curing. This can be achieved using a convection oven or infrared heating.
-
UV Curing: Some specialized coatings are formulated to cure rapidly when exposed to ultraviolet (UV) light, allowing for faster processing times.
Inspection and Quality Control
After curing, the conformal coating should be inspected to ensure proper coverage, thickness, and adhesion. Common inspection methods include:
-
Visual Inspection: A visual examination can reveal any areas of incomplete coverage, bubbles, or other defects.
-
Thickness Measurement: Coating thickness can be measured using non-destructive methods such as eddy current testing or ultrasonic thickness gauges.
-
Adhesion Testing: Adhesion can be tested using methods such as the cross-hatch test or the tape test, which involve scoring the coating and applying pressure-sensitive tape to assess adhesion strength.
-
Dielectric Withstand Testing: Dielectric withstand testing involves applying a high voltage to the coated PCB to ensure that the coating provides adequate insulation and protection against electrical breakdown.
Regular quality control checks should be performed to ensure that the conformal coating process consistently meets the required specifications and standards.
Frequently Asked Questions (FAQ)
-
Q: Is conformal coating always necessary for PCB assemblies?
A: Not all PCB assemblies require conformal coating. It depends on the environmental conditions and application-specific requirements. PCBs exposed to harsh environments or critical applications typically need conformal coating for reliable operation. -
Q: Can conformal coating be removed for repairs or modifications?
A: Yes, conformal coating can be removed using various methods, such as solvent stripping, mechanical abrasion, or thermal removal. However, some coatings, like epoxies and parylene, are more difficult to remove than others, like acrylics and silicones. -
Q: How does conformal coating affect the thermal performance of a PCB?
A: Conformal coating can act as a thermal insulator, which may impact the heat dissipation of components on the PCB. However, this effect is usually minimal, and the benefits of environmental protection often outweigh any thermal considerations. -
Q: Can conformal coating be applied selectively to specific areas of a PCB?
A: Yes, selective coating methods, such as robotic dispensing or laser masking, can be used to apply coating only to specific areas of a PCB. This approach minimizes masking requirements and reduces material waste. -
Q: How long does conformal coating last, and does it need to be reapplied periodically?
A: The lifespan of a conformal coating depends on various factors, such as the coating material, environmental conditions, and handling. In general, conformal coatings can last several years without needing reapplication. However, periodic inspections should be performed to assess the coating’s condition and determine if touch-ups or recoating are necessary.
In conclusion, conformal coating is a crucial step in protecting PCB assemblies from environmental factors and ensuring reliable operation in harsh conditions. By understanding the types of coatings, application methods, and inspection techniques, you can choose the right conformal coating solution for your specific needs. Proper application and quality control are essential for achieving the full benefits of conformal coating and ensuring the long-term performance of your electronic devices.
No responses yet