What is PCB Conformal Coating?
PCB conformal coating is a protective layer applied to printed circuit boards (PCBs) to shield them from environmental factors such as moisture, dust, chemicals, and extreme temperatures. This coating acts as a barrier, preventing contaminants from reaching the sensitive electronic components on the PCB, thus extending its lifespan and ensuring reliable performance.
Types of PCB Conformal Coatings
There are several types of conformal coatings available, each with its own unique properties and advantages. The most common types include:
Type | Advantages | Disadvantages |
---|---|---|
Acrylic | Easy to apply and remove, cost-effective | Limited chemical and moisture resistance |
Silicone | High flexibility, wide temperature range | Difficult to repair, limited adhesion to some surfaces |
Polyurethane | Excellent abrasion and chemical resistance | Requires specialized equipment for application |
Epoxy | Superior chemical and moisture resistance | Brittle, difficult to remove for repairs |
Parylene | Uniform coverage, excellent dielectric properties | Expensive, requires specialized equipment |
Choosing the Right Conformal Coating
When selecting a conformal coating for your PCB, consider the following factors:
- Environmental conditions: Determine the expected exposure to moisture, chemicals, and temperature extremes.
- Application method: Consider the available equipment and expertise for applying the coating.
- Repairability: Assess the likelihood of needing to repair or rework the PCB in the future.
- Cost: Evaluate the cost of the coating material and application process in relation to the project budget.
Benefits of PCB Conformal Coating
Applying a conformal coating to your PCB offers several key benefits:
1. Protection from Moisture and Humidity
Conformal coatings provide a barrier against moisture and humidity, preventing corrosion and short circuits caused by water ingress. This is particularly important for PCBs operating in high-humidity environments or exposed to condensation.
2. Resistance to Chemicals and Solvents
Certain conformal coatings, such as epoxy and polyurethane, offer excellent resistance to chemicals and solvents. This protection is crucial for PCBs used in industrial settings or exposed to cleaning agents.
3. Enhanced Mechanical Strength
Conformal coatings add a layer of mechanical protection to the PCB, guarding against physical damage from vibration, impact, and abrasion. This is especially beneficial for PCBs in mobile or high-vibration applications.
4. Improved Dielectric Properties
Some conformal coatings, like parylene, have excellent dielectric properties, providing insulation between conductive traces and components. This can help prevent electrical leakage and improve the overall performance of the PCB.
5. Extended Lifespan
By protecting the PCB from environmental factors and physical damage, conformal coatings can significantly extend the lifespan of the board. This translates to reduced maintenance costs and improved reliability over time.
Conformal Coating Application Methods
There are several methods for applying conformal coatings to PCBs, each with its own advantages and limitations.
Spray Coating
Spray coating involves using a spray gun to apply the coating material evenly across the PCB surface. This method is fast and efficient for covering large areas but may result in uneven coverage or overspray.
Advantages:
– Fast application
– Suitable for large PCBs
– Cost-effective
Disadvantages:
– Uneven coverage
– Overspray
– Masking required for selective coating
Brush Coating
Brush coating is a manual application method using a brush to apply the coating material to specific areas of the PCB. This method offers precise control but is time-consuming and labor-intensive.
Advantages:
– Precise control
– Suitable for small areas
– Low setup costs
Disadvantages:
– Time-consuming
– Labor-intensive
– Inconsistent thickness
Dip Coating
Dip coating involves immersing the entire PCB in a tank of coating material and then slowly withdrawing it, allowing the excess to drip off. This method provides uniform coverage but may result in thick coatings and requires masking for selective coating.
Advantages:
– Uniform coverage
– Fast application
– Suitable for high-volume production
Disadvantages:
– Thick coatings
– Masking required for selective coating
– Potential for drips and runs
Selective Coating
Selective coating is a specialized application method that targets specific areas of the PCB, leaving other areas uncoated. This can be achieved through various techniques, such as robotic dispensing or laser-cut masking.
Advantages:
– Precise control
– Targeted protection
– Reduced material consumption
Disadvantages:
– Specialized equipment required
– Higher setup costs
– Slower than other methods
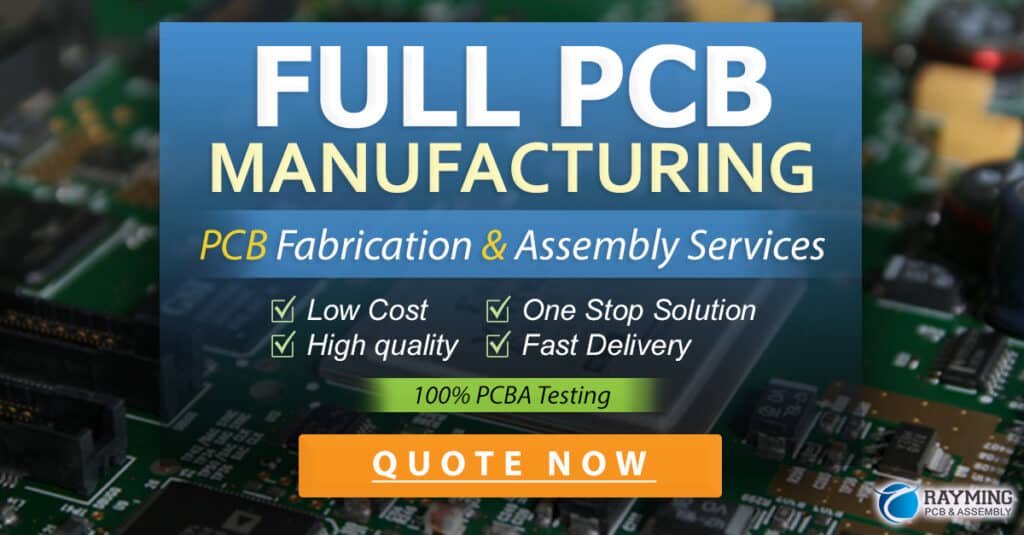
Inspection and Quality Control
After applying the conformal coating, it is crucial to inspect the PCB to ensure proper coverage and identify any defects or inconsistencies. Common inspection methods include:
Visual Inspection
Visual inspection involves examining the coated PCB under magnification to check for coverage, thickness, and any visible defects such as bubbles, pinholes, or delamination.
Thickness Measurement
Measuring the thickness of the conformal coating is important to ensure it meets the specified requirements. This can be done using techniques such as eddy current testing or ultrasonic thickness gauges.
Adhesion Testing
Adhesion testing evaluates the bond strength between the conformal coating and the PCB surface. Common methods include cross-hatch testing and pull-off testing.
Dielectric Strength Testing
Dielectric strength testing involves applying a high voltage across the conformal coating to assess its insulating properties and identify any weak points or Breakthroughs.
Troubleshooting and Repair
Despite the protective benefits of conformal coatings, PCBs may still experience issues that require troubleshooting and repair. Some common problems and their solutions include:
Delamination
Delamination occurs when the conformal coating separates from the PCB surface, often due to poor adhesion or incompatible materials. To repair delamination:
- Remove the affected coating using solvents or abrasion.
- Clean the PCB surface thoroughly.
- Reapply the conformal coating, ensuring proper adhesion.
Pinholes and Bubbles
Pinholes and bubbles in the conformal coating can compromise its protective properties. To address these issues:
- Identify the affected areas using visual inspection.
- Remove the defective coating using solvents or abrasion.
- Reapply the conformal coating, taking care to avoid trapping air or creating pinholes.
Cracking
Cracking in the conformal coating can occur due to mechanical stress or thermal cycling. To repair cracks:
- Remove the damaged coating using solvents or abrasion.
- Clean the PCB surface thoroughly.
- Reapply the conformal coating, ensuring adequate flexibility to accommodate thermal expansion and contraction.
FAQ
1. How long does conformal coating last?
The lifespan of a conformal coating depends on various factors, including the type of coating, environmental conditions, and the application process. Generally, conformal coatings can last several years to decades when applied correctly and under appropriate conditions.
2. Can conformal coating be removed?
Yes, conformal coatings can be removed using various methods, such as solvents, abrasion, or specialized removal agents. The ease of removal depends on the type of coating and the removal method employed.
3. Does conformal coating affect PCB performance?
Conformal coatings can have a slight impact on PCB performance, particularly in terms of high-frequency signal transmission and heat dissipation. However, these effects are typically minimal and can be mitigated through proper material selection and application techniques.
4. How much does conformal coating cost?
The cost of conformal coating depends on factors such as the type of coating material, the application method, and the volume of PCBs being coated. In general, acrylic and silicone coatings are more cost-effective than specialized materials like parylene.
5. Can conformal coating be applied to populated PCBs?
Yes, conformal coatings can be applied to populated PCBs, but care must be taken to avoid coating components that should remain uncoated, such as connectors or adjustable parts. Selective coating methods, such as robotic dispensing or laser-cut masking, can be used to target specific areas of the PCB.
Conclusion
PCB conformal coating is an essential process for protecting printed circuit boards from environmental factors, extending their lifespan, and ensuring reliable performance. By understanding the types of coatings available, their benefits, and the application methods, you can make informed decisions when implementing conformal coating in your PCB design and manufacturing process.
Proper inspection, quality control, and troubleshooting techniques are also crucial for maintaining the integrity of the conformal coating and addressing any issues that may arise. By following best practices and staying up-to-date with the latest developments in conformal coating technology, you can ensure your PCBs are well-protected and perform optimally in their intended applications.
No responses yet