What is Flexible PCB Coverlay?
Flexible PCB coverlay is a thin, insulating material that is laminated onto the surface of a flexible PCB to protect the exposed copper traces and provide electrical insulation. Coverlay is typically made from polyimide or polyester materials, which offer excellent thermal stability, chemical resistance, and mechanical properties. The coverlay acts as a barrier against environmental factors such as moisture, dust, and abrasion, ensuring the integrity of the electronic circuit.
Properties of Flexible PCB Coverlay
Flexible PCB coverlay materials possess several key properties that make them suitable for use in a wide range of applications:
-
Electrical Insulation: Coverlay materials have high dielectric strength, which prevents electrical leakage and short circuits between adjacent copper traces.
-
Thermal Stability: Polyimide and polyester coverlays can withstand high temperatures, making them suitable for use in high-temperature environments.
-
Chemical Resistance: Coverlay materials are resistant to a wide range of chemicals, including acids, alkalis, and solvents, ensuring the protection of the PCB in harsh environments.
-
Mechanical Properties: Flexible PCB coverlay materials have excellent mechanical properties, such as high tensile strength, tear resistance, and flexibility, which allow the PCB to withstand repeated bending and flexing without damage.
Coverlay Materials
There are two main types of materials used for flexible PCB coverlay:
-
Polyimide: Polyimide is the most commonly used material for flexible PCB coverlay due to its excellent thermal stability, chemical resistance, and mechanical properties. It can withstand temperatures up to 300°C and has a dielectric strength of 3500 V/mil.
-
Polyester: Polyester coverlay is a lower-cost alternative to polyimide and is suitable for applications that do not require high-temperature resistance. It has a maximum operating temperature of 105°C and a dielectric strength of 2500 V/mil.
Property | Polyimide Coverlay | Polyester Coverlay |
---|---|---|
Maximum Operating Temperature | 300°C | 105°C |
Dielectric Strength | 3500 V/mil | 2500 V/mil |
Chemical Resistance | High | Moderate |
Mechanical Properties | Excellent | Good |
Cost | Higher | Lower |
Coverlay Application Methods
There are two primary methods for applying coverlay to Flexible PCBs: adhesive-based lamination and adhesiveless lamination.
Adhesive-Based Lamination
In adhesive-based lamination, a layer of adhesive is applied to the coverlay material before it is laminated onto the flexible PCB. The adhesive layer ensures a strong bond between the coverlay and the PCB surface. The lamination process typically involves the following steps:
- The adhesive is applied to the coverlay material using a roller or spray coating method.
- The coverlay is then placed onto the flexible PCB, with the adhesive side facing the PCB surface.
- The assembly is then subjected to heat and pressure using a lamination press, which activates the adhesive and bonds the coverlay to the PCB.
Adhesive-based lamination offers a strong and reliable bond between the coverlay and the PCB, but it can add thickness to the overall assembly and may not be suitable for applications that require very thin PCBs.
Adhesiveless Lamination
Adhesiveless lamination, also known as thermal bonding, involves directly laminating the coverlay material onto the flexible PCB without the use of an adhesive layer. This process relies on the thermoplastic properties of the coverlay material, which allows it to bond directly to the PCB surface under heat and pressure. The adhesiveless lamination process typically involves the following steps:
- The coverlay material is placed onto the flexible PCB, with the bondable side facing the PCB surface.
- The assembly is then subjected to heat and pressure using a lamination press, which causes the coverlay material to melt and bond directly to the PCB surface.
Adhesiveless lamination results in a thinner overall assembly compared to adhesive-based lamination, as there is no additional adhesive layer. This method is preferred for applications that require very thin and lightweight PCBs.
Coverlay Patterning and Openings
After the coverlay is laminated onto the flexible PCB, it is often necessary to create openings or patterns in the coverlay to expose certain areas of the PCB, such as contact pads, vias, or component mounting locations. There are several methods for creating openings in the coverlay, including:
Laser Cutting
Laser cutting is a precise and efficient method for creating openings in the coverlay. A high-powered laser beam is used to ablate the coverlay material, creating clean and accurate openings. Laser cutting is suitable for creating small, intricate patterns and can be easily automated for high-volume production.
Mechanical Drilling
Mechanical drilling involves using a CNC drill to create holes in the coverlay material. This method is suitable for creating larger openings, such as those required for component mounting or connectors. Mechanical drilling is slower than laser cutting but can be more cost-effective for smaller production volumes.
Photolithography
Photolithography is a process that uses light-sensitive photoresist and a photomask to create patterns in the coverlay material. The photoresist is applied to the coverlay surface, and then exposed to UV light through the photomask, which hardens the exposed areas. The unexposed areas are then chemically etched away, leaving the desired pattern in the coverlay. Photolithography is suitable for creating high-resolution patterns and can be used for large-scale production.
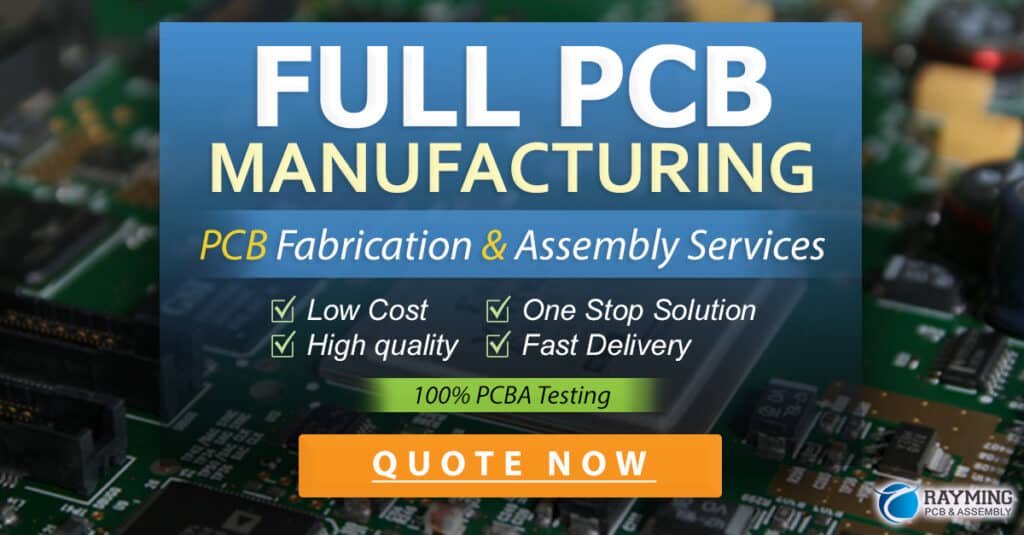
Challenges and Considerations
When working with flexible PCB coverlay, there are several challenges and considerations to keep in mind:
Adhesion
Ensuring proper adhesion between the coverlay and the flexible PCB is critical for the long-term reliability of the assembly. Factors such as surface cleanliness, lamination temperature, and pressure must be carefully controlled to achieve optimal adhesion.
Thickness Control
Controlling the thickness of the coverlay is important for maintaining the overall thickness and flexibility of the PCB Assembly. Thicker coverlay can provide better protection but may reduce the flexibility of the PCB.
Material Selection
Choosing the appropriate coverlay material depends on the specific application requirements, such as temperature resistance, chemical compatibility, and mechanical properties. Polyimide and polyester are the most common choices, but other materials such as fluoropolymers may be used for specialized applications.
Openings and Patterning
Creating accurate and reliable openings in the coverlay is essential for proper functionality of the PCB. The choice of patterning method depends on factors such as the size and complexity of the openings, production volume, and cost considerations.
Conclusion
Coverlay is an essential component of flexible PCBs, providing protection, insulation, and mechanical support to the delicate copper traces. Understanding the properties, materials, and application methods of coverlay is crucial for designing and manufacturing reliable and high-performance flexible PCBs. By carefully considering factors such as adhesion, thickness control, material selection, and patterning, engineers and manufacturers can ensure the optimal performance and longevity of their flexible PCB assemblies.
Frequently Asked Questions (FAQ)
-
What is the primary purpose of coverlay in flexible PCBs?
Coverlay serves as a protective layer for the exposed copper traces on a flexible PCB, providing electrical insulation, mechanical support, and protection against environmental factors such as moisture, dust, and abrasion. -
What are the most common materials used for flexible PCB coverlay?
The two most common materials used for flexible PCB coverlay are polyimide and polyester. Polyimide is known for its excellent thermal stability, chemical resistance, and mechanical properties, while polyester is a lower-cost alternative suitable for applications with less demanding requirements. -
What are the main methods for applying coverlay to flexible PCBs?
The two primary methods for applying coverlay to flexible PCBs are adhesive-based lamination and adhesiveless lamination (thermal bonding). Adhesive-based lamination involves using an adhesive layer to bond the coverlay to the PCB surface, while adhesiveless lamination relies on the thermoplastic properties of the coverlay material to bond directly to the PCB under heat and pressure. -
How are openings or patterns created in the coverlay?
Openings or patterns in the coverlay can be created using various methods, such as laser cutting, mechanical drilling, or photolithography. The choice of method depends on factors such as the size and complexity of the openings, production volume, and cost considerations. -
What are some key challenges and considerations when working with flexible PCB coverlay?
Some key challenges and considerations when working with flexible PCB coverlay include ensuring proper adhesion between the coverlay and the PCB, controlling the thickness of the coverlay to maintain flexibility, selecting the appropriate coverlay material based on application requirements, and creating accurate and reliable openings or patterns in the coverlay.
No responses yet