Introduction to Component Kitting
Component kitting is a critical process in the Electronics Manufacturing industry that involves organizing and preparing components for assembly on printed circuit boards (PCBs). This process ensures that the right components are available in the correct quantities and at the right time for the assembly process. By implementing an effective component kitting strategy, manufacturers can streamline their production, reduce errors, and improve overall efficiency.
Benefits of Component Kitting
- Increased efficiency: Kitting allows operators to focus on the assembly process rather than searching for components, leading to faster production times.
- Reduced errors: Pre-kitting components minimizes the risk of incorrect parts being used during assembly, resulting in fewer defects and rework.
- Improved inventory management: Kitting helps maintain accurate inventory levels and reduces the likelihood of stockouts or excess inventory.
- Space optimization: Kitting conserves space on the production floor by consolidating components into organized kits.
The Component Kitting Process
The component kitting process typically involves the following steps:
- Bill of Materials (BOM) review: The BOM is analyzed to determine the required components for each PCB Assembly.
- Component sourcing: Components are procured from suppliers or retrieved from inventory based on the BOM requirements.
- Kit preparation: Components are sorted, counted, and packaged into kits according to the BOM specifications.
- Kit verification: Kits are inspected to ensure accuracy and completeness before being released to the production floor.
- Kit storage and distribution: Kits are stored in a designated area and distributed to the assembly stations as needed.
Best Practices for Component Kitting
To optimize the component kitting process, consider the following best practices:
- Use barcodes or RFID tags to track kits and components throughout the process.
- Implement a lean manufacturing approach to minimize waste and improve efficiency.
- Utilize automated storage and retrieval systems (ASRS) to streamline kit storage and distribution.
- Regularly review and update BOMs to ensure accuracy and incorporate any changes in design or component specifications.
- Train employees on proper kitting procedures and maintain clear documentation of the process.
Feeder Preparation
Feeder preparation is another essential aspect of the electronics manufacturing process that goes hand-in-hand with component kitting. Feeders are used to hold and dispense components onto the PCB during the automated assembly process. Proper feeder preparation ensures that components are accurately placed and minimizes the risk of assembly errors.
Types of Feeders
There are several types of feeders used in electronics manufacturing, including:
- Tape and reel feeders: Components are packaged on a continuous tape and wound onto a reel for automated placement.
- Tube feeders: Components are stored in cylindrical tubes and fed into the assembly machine.
- Tray feeders: Components are organized in trays, and the assembly machine picks and places them onto the PCB.
- Stick feeders: Components are arranged on sticks or magazines, which are loaded into the assembly machine.
Feeder Preparation Process
The feeder preparation process typically involves the following steps:
- Feeder selection: The appropriate feeder type is selected based on the component packaging and the assembly machine requirements.
- Component loading: Components are loaded into the feeders according to the manufacturer’s specifications.
- Feeder calibration: Feeders are calibrated to ensure accurate component placement and to minimize the risk of jams or misfeeds.
- Feeder maintenance: Feeders are regularly cleaned and maintained to ensure optimal performance and to extend their lifespan.
Feeder Type | Advantages | Disadvantages |
---|---|---|
Tape and Reel | High-speed placement, compact storage | Limited component sizes, higher material costs |
Tube | Suitable for larger components, easy to load | Lower placement speed, larger storage space |
Tray | Flexibility in component sizes and shapes | Manual loading, lower placement speed |
Stick | High-density storage, easy to load | Limited component sizes, potential for damage |
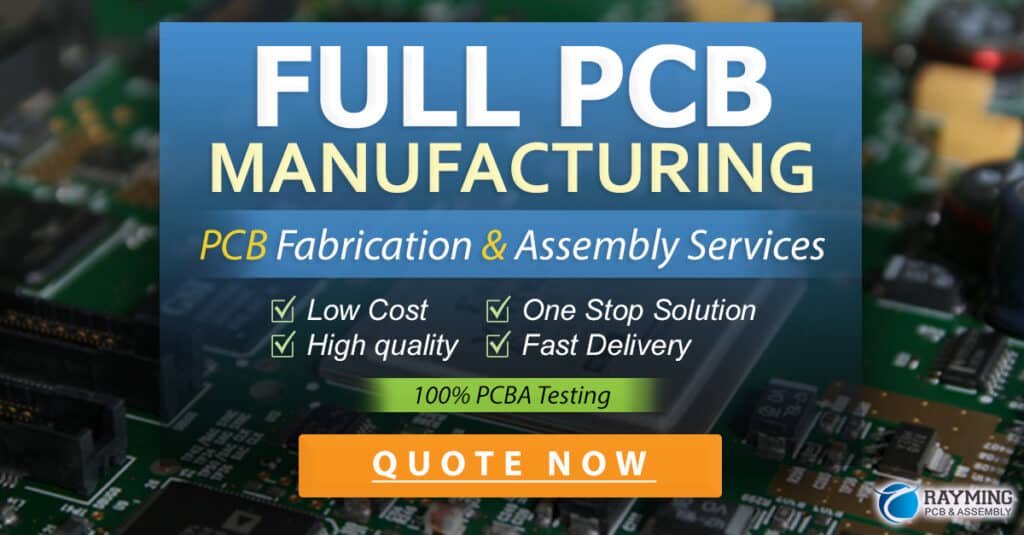
Integration of Component Kitting and Feeder Preparation
Effective integration of component kitting and feeder preparation is crucial for a smooth and efficient electronics manufacturing process. By ensuring that the right components are kitted and loaded into the appropriate feeders, manufacturers can minimize changeover times, reduce the risk of assembly errors, and improve overall production throughput.
Strategies for Integration
- Synchronize kitting and feeder preparation schedules to ensure that kits are available when needed for feeder loading.
- Use a centralized database to manage component inventory, BOM requirements, and feeder assignments.
- Implement a visual management system, such as color-coding or labeling, to easily identify kits and corresponding feeders.
- Establish clear communication channels between kitting and feeder preparation teams to address any issues or changes in production schedules.
- Continuously monitor and analyze the performance of the kitting and feeder preparation processes to identify areas for improvement.
Case Study: ABC Electronics
ABC Electronics, a leading manufacturer of consumer electronics, implemented a comprehensive component kitting and feeder preparation strategy to improve their production efficiency. By investing in automated storage and retrieval systems, standardizing their kitting procedures, and optimizing their feeder management, they achieved the following results:
- 25% reduction in assembly errors
- 15% increase in production throughput
- 10% reduction in inventory carrying costs
- 20% improvement in changeover times
ABC Electronics’ success demonstrates the tangible benefits of a well-executed component kitting and feeder preparation strategy in the electronics manufacturing industry.
Frequently Asked Questions (FAQ)
- What is the difference between kitting and feeder preparation?
-
Kitting involves organizing and packaging components according to the BOM requirements, while feeder preparation focuses on loading components into feeders for the automated assembly process.
-
How can I determine the best feeder type for my components?
-
The choice of feeder type depends on factors such as component size, shape, packaging, and the requirements of your assembly machine. Consult with your equipment manufacturer or a process engineer to determine the most suitable feeder type for your specific needs.
-
What are the most common challenges in component kitting?
-
Some of the most common challenges in component kitting include inaccurate BOMs, Component Shortages, inadequate storage space, and human error in the kitting process. Addressing these challenges requires a combination of process improvements, technology investments, and employee training.
-
How often should I calibrate my feeders?
-
The frequency of feeder calibration depends on factors such as the type of feeder, the components being used, and the overall usage of the equipment. As a general rule, feeders should be calibrated at least once per shift or as recommended by the manufacturer to ensure optimal performance.
-
What are the key metrics to monitor in component kitting and feeder preparation?
- Some of the key metrics to monitor include kitting accuracy, feeder performance (e.g., jams, misfeeds), changeover times, inventory levels, and overall equipment effectiveness (OEE). By tracking these metrics, manufacturers can identify areas for improvement and make data-driven decisions to optimize their processes.
Conclusion
Component kitting and feeder preparation are critical processes in electronics manufacturing that directly impact production efficiency, quality, and cost. By implementing best practices, leveraging technology, and fostering a culture of continuous improvement, manufacturers can optimize these processes and gain a competitive edge in the market. As the electronics industry continues to evolve, investing in effective component kitting and feeder preparation strategies will remain essential for success.
No responses yet