Introduction to Components Tombstoning
Components tombstoning is a phenomenon that occurs in electronic devices when a component unexpectedly stops functioning, often resulting in the failure of the entire system. This issue can be frustrating for both manufacturers and consumers, as it can lead to costly repairs or replacements. In this article, we will explore the causes of components tombstoning, how to prevent it, and what to do if it occurs.
What is Components Tombstoning?
Components tombstoning, also known as “chip standing” or “Manhattan effect,” is a manufacturing defect that occurs when a surface-mounted component (SMC) lifts off the printed circuit board (PCB) during the soldering process. This causes the component to stand vertically on one end, resembling a tombstone, hence the name.
The most common components affected by tombstoning are passive components, such as resistors and capacitors, due to their small size and lightweight. However, larger components like integrated circuits (ICs) can also experience tombstoning under certain conditions.
Causes of Components Tombstoning
Several factors can contribute to components tombstoning during the manufacturing process:
-
Uneven heating: If the PCB and components are not heated evenly during the soldering process, it can cause the solder to melt at different rates, leading to tombstoning.
-
Improper solder paste application: Applying too much or too little solder paste can cause tombstoning. Excessive solder paste can create an imbalance in surface tension, while insufficient solder paste may not provide enough adhesion.
-
Component placement issues: Misaligned or poorly placed components can result in tombstoning. If a component is not seated properly on the solder pads, it may lift off during the soldering process.
-
PCB Design flaws: The PCB layout and design can also contribute to tombstoning. Inadequate pad size, incorrect pad spacing, or unbalanced Copper Distribution can create conditions that promote tombstoning.
-
Incorrect reflow profile: The Reflow Soldering process involves carefully controlled heating and cooling cycles. If the reflow profile is not optimized for the specific components and PCB, it can lead to tombstoning.
Prevention Strategies for Components Tombstoning
To minimize the occurrence of components tombstoning, manufacturers can implement several prevention strategies:
1. Optimize PCB Design
Proper PCB design is crucial in preventing tombstoning. Consider the following guidelines:
- Ensure adequate pad size and spacing for each component
- Maintain balanced copper distribution to promote even heating
- Avoid placing components too close to large copper areas or heat sinks
- Use tear-drop shaped pads to improve solder joint strength
2. Control Solder Paste Application
Consistent and precise solder paste application is essential for preventing tombstoning:
- Use stencils with the appropriate thickness and aperture size
- Regularly inspect and maintain solder paste printing equipment
- Implement solder paste inspection (SPI) systems to detect inconsistencies
- Optimize solder paste composition for the specific application
3. Ensure Proper Component Placement
Accurate component placement helps reduce the risk of tombstoning:
- Use pick-and-place machines with high precision and repeatability
- Implement vision systems to verify component alignment
- Regularly calibrate and maintain placement equipment
- Use component packaging that minimizes handling and placement issues
4. Optimize Reflow Profile
A well-designed reflow profile is critical for minimizing tombstoning:
- Determine the optimal reflow profile for each component and PCB combination
- Use thermocouples or profiling systems to monitor actual temperatures during reflow
- Implement controlled heating and cooling ramps to minimize thermal stress
- Consider using nitrogen atmosphere to improve solder joint quality
Troubleshooting Components Tombstoning
Despite implementing prevention strategies, tombstoning may still occur. If tombstoning is detected, consider the following troubleshooting steps:
-
Identify the affected components: Visually inspect the PCB to identify which components have tombstoned. Use magnification tools if necessary.
-
Determine the root cause: Analyze the manufacturing process to identify the likely cause of tombstoning. Review PCB design, solder paste application, component placement, and reflow profile.
-
Rework the affected components: Carefully remove the tombstoned components using a soldering iron or hot air rework station. Clean the pads and reapply solder paste if necessary. Replace the components and resolder them using the appropriate techniques.
-
Implement corrective actions: Based on the identified root cause, implement the necessary changes to prevent tombstoning from recurring. This may involve modifying the PCB design, adjusting solder paste application, improving component placement accuracy, or optimizing the reflow profile.
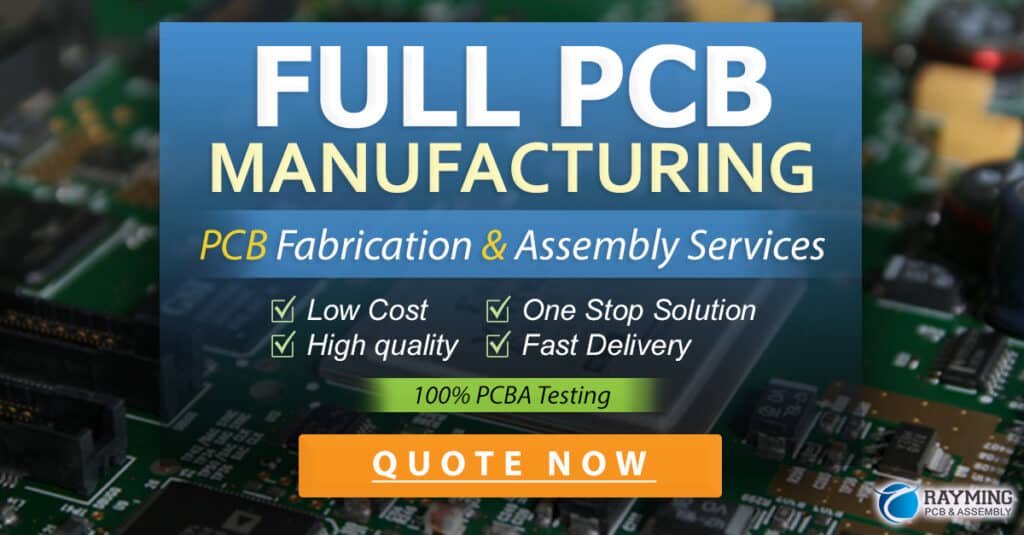
Frequently Asked Questions (FAQ)
-
Q: Can tombstoning be detected visually?
A: Yes, tombstoning can often be detected through visual inspection of the PCB. Tombstoned components will appear to be standing vertically on one end, rather than lying flat against the PCB surface. -
Q: Does tombstoning always result in a non-functional component?
A: Not always. In some cases, a tombstoned component may still maintain electrical contact and function correctly. However, the reliability and long-term performance of the component may be compromised. -
Q: Can tombstoning be repaired?
A: Yes, tombstoned components can often be repaired through rework processes. This involves removing the affected component, cleaning the pads, and resoldering the component using the appropriate techniques. -
Q: Are certain types of components more prone to tombstoning?
A: Yes, small and lightweight components, such as chip resistors and capacitors, are more susceptible to tombstoning due to their low mass and high surface tension forces. -
Q: Can tombstoning be completely eliminated?
A: While it may not be possible to completely eliminate tombstoning, implementing proper prevention strategies and maintaining tight process controls can significantly reduce its occurrence.
Conclusion
Components tombstoning is a manufacturing defect that can lead to product failures and increased production costs. By understanding the causes of tombstoning and implementing appropriate prevention strategies, manufacturers can minimize its occurrence and improve overall product quality.
Effective prevention strategies include optimizing PCB design, controlling solder paste application, ensuring proper component placement, and optimizing the reflow profile. If tombstoning does occur, careful troubleshooting and rework processes can often resolve the issue.
By staying vigilant and continuously improving manufacturing processes, manufacturers can overcome the challenges posed by components tombstoning and deliver reliable, high-quality electronic products to their customers.
Cause of Tombstoning | Prevention Strategy |
---|---|
Uneven heating | Optimize reflow profile, use thermocouples or profiling systems |
Improper solder paste application | Use stencils with appropriate thickness and aperture size, implement SPI systems |
Component placement issues | Use high-precision pick-and-place machines, implement vision systems |
PCB design flaws | Ensure adequate pad size and spacing, maintain balanced copper distribution |
Incorrect reflow profile | Determine optimal reflow profile for each component and PCB combination |
Table 1: Common causes of tombstoning and their corresponding prevention strategies.
By addressing these key areas and implementing the appropriate prevention strategies, manufacturers can significantly reduce the occurrence of components tombstoning and improve the overall quality and reliability of their electronic products.
No responses yet