Introduction to Via covering
In the world of printed circuit board (PCB) design and manufacturing, via covering is a crucial technique that plays a significant role in ensuring the reliability and functionality of the final product. Vias are small holes drilled through the layers of a PCB to establish electrical connections between different conductive layers. While vias are essential for creating interconnects, they can also pose challenges in terms of Signal Integrity, mechanical stability, and protection against environmental factors. This is where via covering comes into play.
Via covering involves applying a protective material over the vias to shield them from potential issues and enhance the overall performance of the PCB. In this comprehensive article, we will delve into the concept of via covering, exploring its benefits, techniques, materials, and best practices. Whether you are a PCB Designer, manufacturer, or electronics enthusiast, understanding via covering is essential for creating high-quality and reliable PCBs.
The Importance of Via Covering
Signal Integrity
One of the primary reasons for implementing via covering is to maintain signal integrity within the PCB. Vias can act as small antennas, radiating electromagnetic energy and causing signal distortion, crosstalk, and electromagnetic interference (EMI). By covering the vias with a conductive material, such as copper or conductive epoxy, the radiation and coupling effects are minimized, resulting in cleaner and more stable signals.
Mechanical Stability
Vias are essentially holes in the PCB, and they can weaken the mechanical structure of the board. This is particularly critical in applications where the PCB is subjected to vibrations, shocks, or thermal stress. Via covering helps to reinforce the mechanical strength of the vias, preventing them from cracking or delaminating over time. By filling the vias with a solid material, the overall structural integrity of the PCB is enhanced.
Environmental Protection
PCBs are often exposed to various environmental factors, such as moisture, dust, and chemical contaminants. These elements can penetrate through the vias and cause corrosion, short circuits, or other reliability issues. Via covering acts as a barrier, sealing the vias and protecting the internal layers of the PCB from external contaminants. This is particularly important in applications where the PCB operates in harsh environments or is subject to stringent reliability requirements.
Via Covering Techniques
There are several techniques commonly used for via covering, each with its own advantages and considerations. Let’s explore some of the most popular methods:
Copper Filling
Copper filling is a widely used technique for via covering, especially in high-speed and high-frequency applications. In this method, the vias are filled with copper, creating a solid and conductive structure. Copper filling can be achieved through electroplating or a combination of electroplating and copper paste filling.
The electroplating process involves depositing a layer of copper onto the walls of the via until it is completely filled. This technique provides excellent electrical conductivity and thermal dissipation properties. However, it can be time-consuming and requires precise control over the plating parameters to ensure uniform filling.
Copper paste filling, on the other hand, involves applying a copper paste into the vias using a screen printing or stencil printing process. The paste is then cured and sometimes followed by a planarization step to level the surface. Copper paste filling is faster and more cost-effective compared to electroplating, but it may result in slightly lower conductivity and thermal performance.
Conductive Epoxy Filling
Conductive epoxy filling is another popular method for via covering, particularly in applications where electrical conductivity is not a critical requirement. In this technique, a conductive epoxy material is dispensed into the vias and then cured to form a solid and adherent filling.
Conductive epoxy fillings offer several advantages, including good mechanical strength, excellent adhesion to the via walls, and compatibility with a wide range of PCB materials. They also provide a certain level of electrical conductivity, although not as high as copper fillings.
One of the key considerations with conductive epoxy filling is the curing process. The epoxy must be properly cured to achieve optimal mechanical and electrical properties. Insufficient curing can lead to voids, poor adhesion, or degraded performance over time.
Non-Conductive Filling
In some cases, via covering may not require electrical conductivity, and non-conductive filling materials can be used. These materials, such as non-conductive epoxies or polymers, are applied to the vias to provide mechanical support and environmental protection.
Non-conductive fillings are typically used in applications where the vias are not part of the electrical circuit or where signal integrity is not a concern. They offer benefits such as improved mechanical stability, reduced moisture absorption, and enhanced thermal insulation.
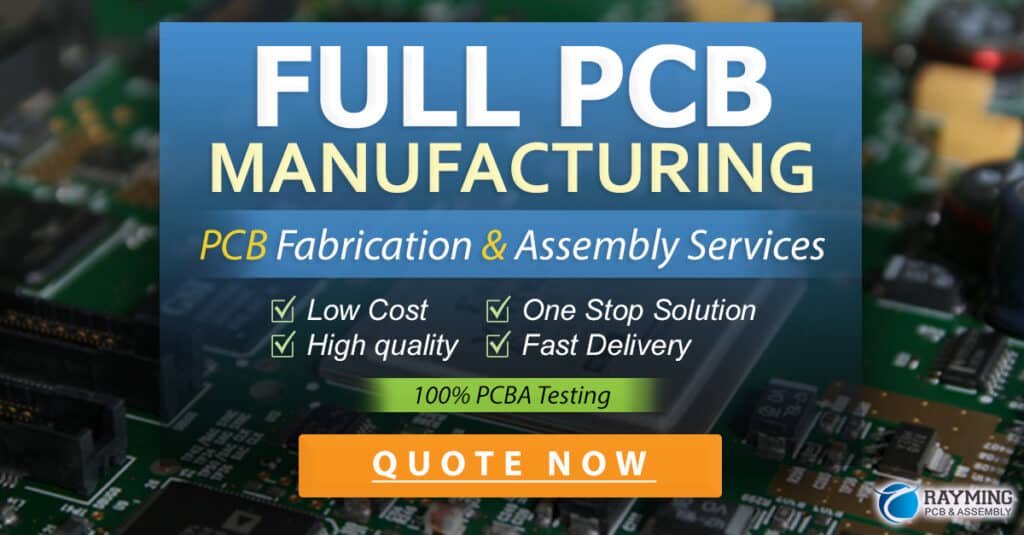
Via Covering Materials
The choice of via covering material depends on the specific requirements of the PCB and the desired properties. Here are some commonly used materials for via covering:
Copper
Copper is the most widely used material for Via Filling due to its excellent electrical conductivity and thermal dissipation properties. It is compatible with both electroplating and paste filling techniques and provides a solid and reliable connection between the layers of the PCB.
Conductive Epoxies
Conductive epoxies are polymer-based materials that contain conductive fillers, such as silver or carbon. They offer good mechanical strength, adhesion, and a certain level of electrical conductivity. Conductive epoxies are available in various formulations to suit different application requirements.
Non-Conductive Epoxies
Non-conductive epoxies are used for via covering when electrical conductivity is not required. They provide mechanical support, environmental protection, and insulation properties. Non-conductive epoxies are often used in combination with other via covering techniques to achieve the desired performance.
Other Materials
Apart from copper and epoxies, other materials such as solder mask, dry film solder mask, and organic solderability preservatives (OSP) can also be used for via covering. These materials are applied as a coating over the vias to provide protection and enhance the solderability of the PCB.
Best Practices for Via Covering
To achieve optimal results with via covering, consider the following best practices:
-
Design Considerations: During the PCB design phase, carefully consider the placement and size of vias. Minimize the number of vias whenever possible and ensure adequate spacing between them to facilitate effective via covering.
-
Material Selection: Choose the appropriate via covering material based on the specific requirements of your application. Consider factors such as electrical conductivity, mechanical strength, thermal properties, and compatibility with the PCB manufacturing process.
-
Process Control: Ensure proper process control during via covering. This includes maintaining the correct temperature, pressure, and curing conditions for the selected material. Regularly monitor and adjust the process parameters to achieve consistent and reliable results.
-
Inspection and Testing: Implement thorough inspection and testing procedures to verify the quality of the via covering. Conduct visual inspections, electrical tests, and cross-sectional analysis to ensure proper filling, adhesion, and performance of the covered vias.
-
Collaboration with Manufacturers: Work closely with your PCB Manufacturer to discuss your via covering requirements and ensure they have the necessary capabilities and expertise to meet your needs. Provide clear specifications and communicate any special considerations to ensure a successful outcome.
FAQ
-
Q: What is the purpose of via covering in PCBs?
A: Via covering serves multiple purposes, including improving signal integrity, enhancing mechanical stability, and providing environmental protection to the vias and internal layers of the PCB. -
Q: What are the most common via covering techniques?
A: The most common via covering techniques include copper filling (electroplating or paste filling), conductive epoxy filling, and non-conductive filling. -
Q: When should I choose copper filling over conductive epoxy filling?
A: Copper filling is preferred when high electrical conductivity and thermal dissipation are critical requirements, such as in high-speed and high-frequency applications. Conductive epoxy filling is suitable when a balance of mechanical strength and moderate conductivity is needed. -
Q: Can via covering be used in combination with other PCB manufacturing processes?
A: Yes, via covering can be used in combination with other processes, such as solder mask application, surface finishing, and assembly. It is important to consider the compatibility and sequence of these processes to ensure optimal results. -
Q: How can I ensure the quality and reliability of via covering in my PCBs?
A: To ensure the quality and reliability of via covering, follow best practices such as careful design considerations, appropriate material selection, proper process control, thorough inspection and testing, and close collaboration with your PCB manufacturer.
Conclusion
Via covering is a critical technique in PCB design and manufacturing that offers numerous benefits, including improved signal integrity, mechanical stability, and environmental protection. By understanding the various via covering techniques, materials, and best practices, you can make informed decisions and ensure the reliability and performance of your PCBs.
Whether you opt for copper filling, conductive epoxy filling, or non-conductive filling, the key is to select the appropriate method based on your specific application requirements. Proper process control, inspection, and testing are essential to achieve consistent and reliable via covering results.
As PCB technology continues to advance, via covering techniques and materials will evolve to meet the ever-increasing demands for high-performance and reliable electronic devices. By staying up to date with the latest developments and collaborating with experienced PCB manufacturers, you can leverage the benefits of via covering to create PCBs that excel in both functionality and durability.
Via Covering Technique | Advantages | Considerations |
---|---|---|
Copper Filling | – High electrical conductivity – Excellent thermal dissipation |
– Time-consuming process – Requires precise plating control |
Conductive Epoxy Filling | – Good mechanical strength – Excellent adhesion – Wide compatibility |
– Lower conductivity compared to copper – Proper curing is critical |
Non-Conductive Filling | – Mechanical support – Environmental protection – Thermal insulation |
– No electrical conductivity – Used in combination with other techniques |
By embracing via covering as an integral part of your PCB design and manufacturing process, you can unlock new possibilities for creating high-quality, reliable, and performance-driven electronic products. So, whether you are a seasoned PCB designer or a newcomer to the field, make sure to leverage the power of via covering to take your PCBs to the next level.
No responses yet