Introduction to Thermal Vias
Thermal vias are an essential component in the design and manufacturing of printed circuit boards (PCBs). They play a crucial role in dissipating heat from high-power components, such as processors, power amplifiers, and Voltage Regulators, to prevent overheating and ensure optimal performance. In this article, we will explore the concept of thermal vias, their importance, design considerations, and best practices for implementing them in PCB Designs.
What are Thermal Vias?
Thermal vias are small, conductive holes drilled through a PCB to transfer heat from a component to the opposite side of the board or to a heatsink. These vias are typically filled with a conductive material, such as copper, to enhance their thermal conductivity. By providing a low-resistance path for heat to escape, thermal vias help to prevent the buildup of excessive heat in critical components, which can lead to performance degradation or even failure.
The Importance of Thermal Management in PCBs
As electronic devices continue to shrink in size and increase in functionality, the power density of PCBs has risen significantly. This trend has made effective thermal management a top priority for PCB designers. Without proper heat dissipation, high-power components can generate localized hot spots, leading to a range of issues, including:
- Reduced component lifespan
- Decreased performance and efficiency
- Increased risk of system failure
- Potential safety hazards
Thermal vias offer a cost-effective and reliable solution to mitigate these risks by providing an efficient means of transferring heat away from critical components.
Designing Thermal Vias
Thermal Via Placement
The placement of thermal vias is a critical aspect of PCB design. To maximize their effectiveness, thermal vias should be located as close as possible to the heat-generating component. This proximity minimizes the thermal resistance between the component and the vias, allowing for more efficient heat transfer.
When placing thermal vias, designers should also consider the layout of the PCB and the location of other components. Vias should not interfere with the routing of traces or the placement of other components, as this can lead to Signal Integrity issues or manufacturing difficulties.
Thermal Via Size and Quantity
The size and quantity of thermal vias play a significant role in their overall effectiveness. Larger vias have a greater cross-sectional area, which allows for better heat conduction. However, larger vias also consume more board space and can be more challenging to manufacture.
The number of thermal vias used depends on several factors, including the power dissipation requirements of the component, the available board space, and the desired thermal performance. A higher number of vias generally provides better heat dissipation, but designers must strike a balance between thermal performance and other design constraints.
Component Power Dissipation | Recommended Number of Thermal Vias |
---|---|
< 1 W | 4-6 |
1-2 W | 6-8 |
2-3 W | 8-10 |
> 3 W | 10+ |
Table 1: General recommendations for the number of thermal vias based on component power dissipation.
Thermal Via Patterns
Thermal vias are typically arranged in patterns to optimize heat dissipation. Some common patterns include:
- Grid pattern: Vias are evenly spaced in a grid around the component.
- Staggered pattern: Vias are arranged in an alternating pattern to maximize coverage.
- Circular pattern: Vias are placed in a circular arrangement around the component.
The choice of pattern depends on the specific component, available space, and thermal requirements. Designers may also use a combination of patterns to achieve the desired thermal performance.
Thermal Via Filling
To enhance the thermal conductivity of vias, they are often filled with a conductive material, such as copper or a specially formulated thermal epoxy. Filling the vias helps to eliminate air gaps, which can act as thermal insulators, and improves the overall heat transfer efficiency.
There are several methods for filling thermal vias, including:
- Electroplating: Copper is electroplated onto the walls of the via, gradually filling it.
- Conductive epoxy: A thermally conductive epoxy is injected into the via and cured.
- Copper plugging: A copper wire or rod is inserted into the via and soldered in place.
The choice of filling method depends on the specific requirements of the PCB, such as the desired thermal conductivity, cost, and manufacturing constraints.
Thermal Via Best Practices
To ensure the optimal performance of thermal vias, designers should adhere to the following best practices:
- Place thermal vias as close to the heat-generating component as possible.
- Use an appropriate number and size of vias based on the component’s power dissipation.
- Choose a via pattern that maximizes heat dissipation while minimizing interference with other components.
- Fill thermal vias with a conductive material to enhance thermal conductivity.
- Consider the use of thermal interface materials (TIMs) between the component and the PCB to further improve heat transfer.
- Conduct thorough thermal simulations and testing to validate the effectiveness of the thermal via design.
By following these best practices, designers can create PCBs with efficient thermal management, ensuring the reliability and longevity of the electronic devices they power.
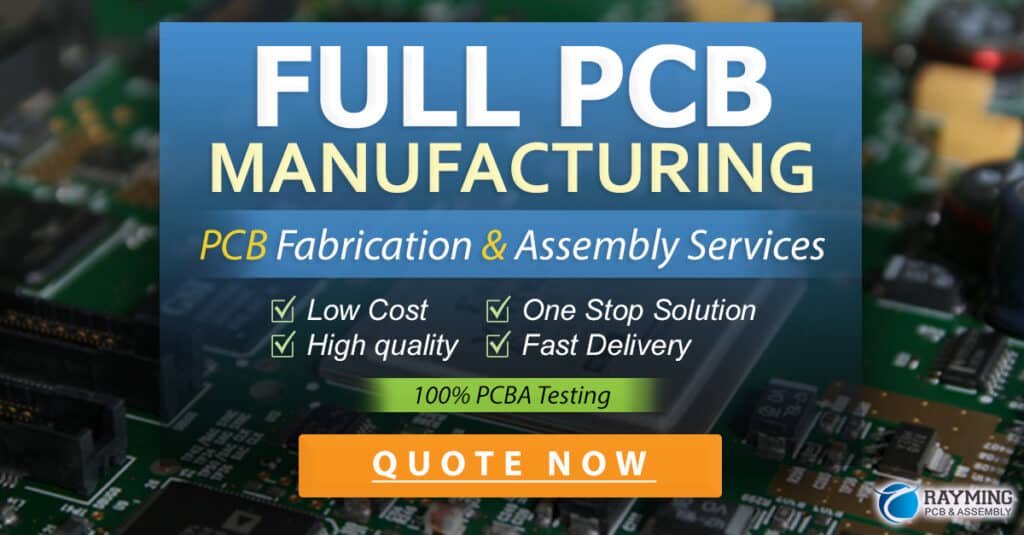
Thermal Via Limitations and Alternatives
While thermal vias are an effective solution for heat dissipation in many applications, they do have some limitations. One significant limitation is the amount of board space they consume. In high-density PCB designs, the space required for thermal vias may be limited, making it challenging to achieve the desired thermal performance.
Another limitation is the potential for manufacturing issues. Thermal vias can be difficult to drill and fill consistently, especially in high-volume production. This can lead to increased manufacturing costs and reduced yields.
In cases where thermal vias are not practical or sufficient, designers may consider alternative heat dissipation methods, such as:
- Heat spreaders: Thin, thermally conductive sheets that are attached to the component and spread heat over a larger area.
- Heatsinks: Finned metal structures that are attached to the component and dissipate heat through convection and radiation.
- Thermal planes: Dedicated copper layers within the PCB that are used to spread heat across a larger area.
These alternatives can be used in conjunction with thermal vias or as standalone solutions, depending on the specific requirements of the PCB design.
Frequently Asked Questions (FAQ)
-
Q: What is the purpose of thermal vias in PCBs?
A: Thermal vias are used to transfer heat from high-power components to the opposite side of the PCB or to a heatsink, helping to prevent overheating and ensure optimal performance. -
Q: How does the size of thermal vias affect their performance?
A: Larger thermal vias have a greater cross-sectional area, which allows for better heat conduction. However, larger vias also consume more board space and can be more challenging to manufacture. -
Q: What are some common patterns used for arranging thermal vias?
A: Common patterns for thermal vias include grid, staggered, and circular arrangements. The choice of pattern depends on the specific component, available space, and thermal requirements. -
Q: Why are thermal vias often filled with a conductive material?
A: Filling thermal vias with a conductive material, such as copper or a thermal epoxy, helps to eliminate air gaps and improve heat transfer efficiency. -
Q: What are some alternatives to thermal vias for heat dissipation in PCBs?
A: Alternatives to thermal vias include heat spreaders, heatsinks, and thermal planes. These can be used in conjunction with thermal vias or as standalone solutions, depending on the specific requirements of the PCB design.
Conclusion
Thermal vias are a critical component in the design and manufacturing of PCBs, providing an efficient means of dissipating heat from high-power components. By understanding the principles of thermal via design, placement, size, and filling, designers can create PCBs with optimal thermal performance, ensuring the reliability and longevity of electronic devices.
As electronic systems continue to increase in complexity and power density, effective thermal management will remain a top priority for PCB designers. By staying up-to-date with the latest thermal management techniques and best practices, designers can overcome the challenges posed by heat generation and create innovative, high-performance electronic products.
No responses yet