Introduction to PCB tolerance
Printed Circuit Boards (PCBs) are essential components in modern electronics, providing a platform for interconnecting electronic components. The manufacturing process of PCBs involves various steps, each with its own set of tolerances. PCB tolerance refers to the acceptable range of variation in the dimensions, spacing, and positioning of features on a PCB. Understanding and adhering to these tolerances is crucial for ensuring the functionality, reliability, and manufacturability of the final product.
Why is PCB Tolerance Important?
PCB tolerance plays a vital role in several aspects of PCB design and manufacturing:
-
Functionality: Proper tolerances ensure that components fit correctly and make reliable connections, guaranteeing the desired electrical performance of the circuit.
-
Manufacturability: Adhering to tolerance standards allows for consistent and efficient production of PCBs, reducing the likelihood of defects and improving yield.
-
Cost: Tighter tolerances often require more precise manufacturing processes, which can increase production costs. Understanding the necessary tolerances helps optimize the balance between cost and quality.
-
Reliability: Maintaining appropriate tolerances contributes to the long-term reliability of the PCB by ensuring robust connections and preventing issues such as short circuits or open connections.
Factors Affecting PCB Tolerance
Several factors influence the tolerances achievable in PCB manufacturing:
1. Manufacturing Process
The choice of manufacturing process significantly impacts the achievable tolerances. The two primary methods for PCB Fabrication are:
a. Subtractive Process: This traditional method involves removing unwanted copper from a fully copper-clad board using etching techniques. Subtractive processes typically have larger minimum feature sizes and wider tolerances compared to additive processes.
b. Additive Process: Additive manufacturing, such as inkjet printing or 3D printing, selectively deposits conductive material onto the substrate. These processes offer finer feature sizes and tighter tolerances but may have limitations in terms of materials and layer count.
2. PCB Material
The choice of PCB material affects the dimensional stability and the ability to maintain tight tolerances. Factors to consider include:
a. Coefficient of Thermal Expansion (CTE): Materials with lower CTE, such as glass-reinforced epoxy (FR-4), exhibit better dimensional stability under temperature changes.
b. Moisture Absorption: Some materials, like polyimide, have higher moisture absorption rates, which can cause dimensional changes and affect tolerances.
c. Thickness: Thinner PCBs are more susceptible to warping and dimensional variations, making it more challenging to maintain tight tolerances.
3. Feature Size and Complexity
The size and complexity of the PCB features directly influence the achievable tolerances:
a. Trace Width and Spacing: Narrower traces and smaller spacing between features require tighter tolerances to ensure proper electrical isolation and prevent short circuits.
b. Via Size and Placement: Smaller vias and more precise via placement demand higher accuracy in drilling and registration.
c. Component Footprints: The tolerance requirements for component footprints vary depending on the package type and pitch of the components.
4. Layer Count
As the number of layers in a PCB increases, maintaining tight tolerances becomes more challenging due to the accumulation of variations across multiple layers. Higher layer count PCBs often require more precise alignment and registration techniques.
Industry Standards for PCB Tolerance
To ensure consistency and reliability in PCB manufacturing, various industry standards provide guidelines for PCB Tolerances. Some widely recognized standards include:
- IPC-6012: Generic Performance Specification for Rigid Printed Boards
- IPC-6013: Qualification and Performance Specification for Flexible/Rigid-Flexible Printed Boards
- IPC-2221: Generic Standard on Printed Board Design
- IPC-2222: Sectional Design Standard for Rigid Organic Printed Boards
These standards define different classes of PCBs based on the level of complexity and the required tolerances. For example, IPC-6012 defines three classes:
- Class 1: General Electronic Products
- Class 2: Dedicated Service Electronic Products
- Class 3: High Reliability Electronic Products
Each class has specific requirements for various aspects of PCB manufacturing, including tolerances for trace width, spacing, hole size, and more.
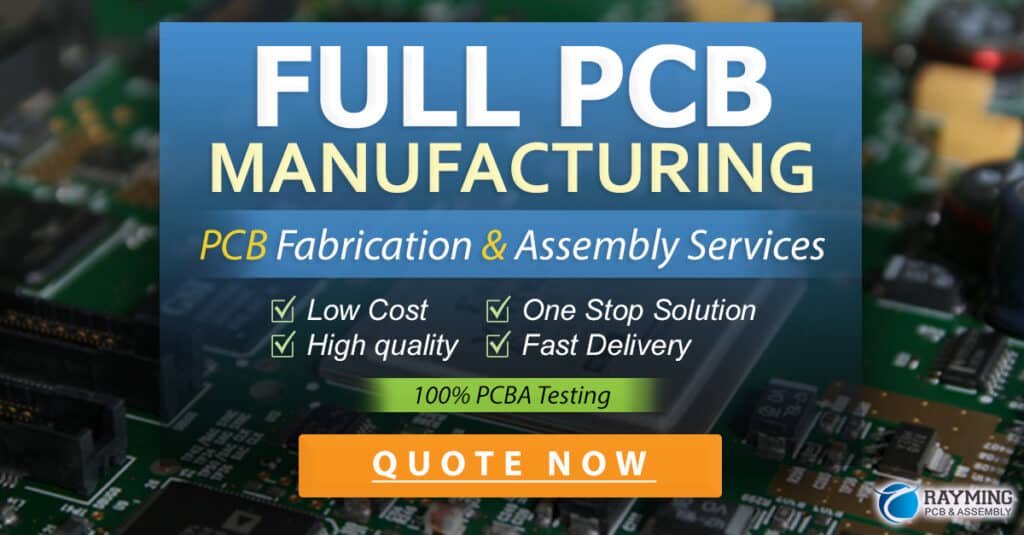
Common PCB Tolerance Specifications
The following table provides an overview of some common PCB tolerance specifications based on IPC-6012 Class 2 requirements:
Feature | Tolerance |
---|---|
Conductor Width and Spacing | ±10% |
Hole Size (Plated) | ±0.1 mm |
Hole Size (Non-Plated) | ±0.2 mm |
Hole-to-Hole Spacing | ±0.1 mm |
Solder Mask Aperture | ±0.05 mm |
Solder Mask Registration to Copper | ±0.1 mm |
Silk Screen Registration to Copper | ±0.2 mm |
Board Outline | ±0.2 mm |
Board Thickness | ±10% |
It’s important to note that these tolerances are general guidelines, and specific requirements may vary depending on the application, design, and manufacturing capabilities.
Designing for PCB Tolerances
To ensure a successful PCB design that meets the required tolerances, consider the following best practices:
-
Understand the Manufacturing Capabilities: Collaborate with your PCB Manufacturer to understand their specific capabilities and limitations in terms of tolerances. This knowledge will help you design within their manufacturing constraints.
-
Use Appropriate Design Rules: Establish design rules in your PCB design software that reflect the desired tolerances. This includes setting minimum trace widths, spacings, drill sizes, and other relevant parameters.
-
Consider Annular Ring Requirements: Ensure that the annular ring (the copper pad surrounding a drilled hole) is sufficient to accommodate the tolerances in hole placement and size. Adequate annular rings provide a margin for error and improve the reliability of the plated through-hole connections.
-
Implement DFM Checks: Utilize Design for Manufacturability (DFM) checks in your PCB design software or engage a third-party DFM service to analyze your design and identify potential tolerance issues before sending it for manufacturing.
-
Communicate Clearly with Manufacturers: Provide clear and detailed fabrication drawings and specifications to your PCB manufacturer. Include the required tolerances, materials, and any special requirements to avoid ambiguity and ensure that the manufactured PCBs meet your expectations.
Frequently Asked Questions (FAQ)
- What is the difference between absolute and relative tolerances in PCB design?
- Absolute tolerance refers to the maximum allowable deviation from a specified dimension, regardless of the nominal value. For example, ±0.1 mm.
-
Relative tolerance is expressed as a percentage of the nominal dimension. For example, ±10% of the specified width.
-
How do I choose the appropriate tolerances for my PCB design?
- Consider the requirements of your specific application, including the component sizes, pin pitch, and electrical performance needs.
- Consult with your PCB manufacturer to understand their capabilities and recommendations based on your design complexity and volume.
-
Refer to industry standards, such as IPC-6012, for guidance on tolerance specifications for different classes of PCBs.
-
What are the consequences of not adhering to PCB tolerances?
- Violating PCB tolerances can lead to various issues, such as component misalignment, poor solderability, short circuits, open connections, and reduced reliability.
-
Non-compliant PCBs may require rework, resulting in increased costs and delays in production.
-
How can I minimize the impact of tolerances on my PCB design?
- Design with appropriate margins and clearances to accommodate potential variations in dimensions and placement.
- Use larger feature sizes, such as wider traces and larger vias, when possible to provide more tolerance for manufacturing variations.
-
Follow recommended design rules and guidelines provided by your PCB manufacturer and industry standards.
-
What should I do if my PCB design requires tighter tolerances than the manufacturer’s standard capabilities?
- Discuss your specific requirements with the PCB manufacturer and explore alternative manufacturing processes or materials that can achieve the desired tolerances.
- Be prepared for potential increases in cost and lead time associated with non-standard or high-precision manufacturing.
- Consider design optimizations or alternative component selections that can relax the tolerance requirements without compromising functionality.
Conclusion
PCB tolerance is a critical aspect of PCB design and manufacturing, ensuring the proper functionality, reliability, and manufacturability of electronic products. Understanding the factors that influence tolerances, such as manufacturing processes, materials, feature sizes, and layer count, is essential for designing PCBs that meet the required specifications.
By adhering to industry standards, collaborating with PCB manufacturers, and following best practices in PCB design, engineers can effectively manage tolerances and produce high-quality PCBs. Striking the right balance between cost, performance, and manufacturability is key to successful PCB Development.
As technology advances and miniaturization continues to drive the electronics industry, the importance of PCB tolerances will only increase. Staying informed about the latest manufacturing capabilities, design techniques, and industry standards will enable engineers to navigate the challenges and opportunities presented by PCB tolerance requirements in the ever-evolving world of electronics design and manufacturing.
No responses yet