Introduction to PCB Layers
Printed Circuit Boards (PCBs) are essential components in modern electronic devices, serving as the foundation for interconnecting various electronic components. PCBs are made up of multiple layers, each playing a crucial role in the overall functionality and performance of the board. In this comprehensive article, we will delve into the concept of PCB layers, exploring their types, functions, and the factors that influence the number of layers required for a specific design.
Understanding the Basics of PCB Layers
What is a PCB Layer?
A PCB layer is a thin, flat sheet of insulating material, typically made of fiberglass or other dielectric substrates, with conductive copper traces etched onto its surface. These layers are stacked and laminated together to form a complete PCB Assembly. Each layer serves a specific purpose, such as signal routing, power distribution, or ground plane.
Types of PCB Layers
PCB layers can be categorized into several types based on their function and location within the board stack-up. The most common types of PCB layers include:
-
Signal Layers: These layers are used for routing electrical signals between components on the PCB. They contain copper traces that interconnect various components, allowing for the flow of electrical signals.
-
Power Layers: Power layers are dedicated to distributing power to the components on the PCB. They provide a low-impedance path for the power supply, ensuring stable and reliable power delivery to all parts of the board.
-
Ground Layers: Ground layers serve as a reference plane for electrical signals and help to minimize electromagnetic interference (EMI) and crosstalk between signal layers. They provide a low-impedance return path for electrical currents.
-
Dielectric Layers: Dielectric layers, also known as insulating layers, are placed between conductive layers to prevent electrical shorts and provide insulation. They are typically made of materials such as FR-4, which is a glass-reinforced epoxy laminate.
The Importance of PCB Layers
PCB layers play a crucial role in the overall performance and reliability of electronic devices. By separating signals, power, and ground onto dedicated layers, designers can achieve several benefits:
-
Signal Integrity: Proper layer stackup and routing techniques help maintain signal integrity by minimizing crosstalk, reducing EMI, and ensuring proper impedance control.
-
Power Distribution: Dedicated power layers provide a low-impedance path for power delivery, minimizing voltage drops and ensuring stable power supply to all components.
-
EMI Reduction: Ground layers act as shields between signal layers, reducing electromagnetic interference and minimizing the impact of external noise sources.
-
Miniaturization: Multi-layer PCBs allow for higher component density and more compact designs, as signals can be routed on multiple layers, reducing the overall board size.
Factors Affecting the Number of PCB Layers
The number of layers in a PCB is determined by various factors, including the complexity of the circuit, the number of components, signal integrity requirements, and manufacturing constraints. Let’s explore these factors in more detail.
Circuit Complexity
The complexity of the circuit is one of the primary factors that influence the number of PCB layers required. As the number of components and interconnections increases, so does the need for additional layers to accommodate signal routing and power distribution. Complex designs with high component density, such as those found in smartphones or laptops, often require multi-layer PCBs with eight or more layers.
Signal Integrity Requirements
Signal integrity is a critical consideration in PCB Design, particularly for high-speed and high-frequency applications. To maintain signal integrity, designers must carefully plan the layer stackup and routing strategies. In some cases, additional layers may be necessary to provide adequate shielding, minimize crosstalk, and ensure proper impedance control. For example, high-speed digital circuits may require dedicated signal layers and ground planes to maintain signal quality.
Power Distribution Requirements
The power distribution requirements of a PCB also influence the number of layers needed. As the number of components and their power demands increase, additional power layers may be required to ensure stable and reliable power delivery. Power planes help minimize voltage drops and provide a low-impedance path for current flow. In some cases, multiple power layers may be necessary to distribute different voltage levels to various parts of the circuit.
Manufacturing Constraints
Manufacturing constraints, such as the available PCB fabrication technology and cost considerations, also play a role in determining the number of layers. While multi-layer PCBs offer numerous benefits, they also come with increased manufacturing complexity and cost. Designers must strike a balance between the required functionality and the manufacturing feasibility of the board. In some cases, alternative design techniques, such as high-density interconnect (HDI) or embedded components, may be employed to minimize the number of layers while still meeting the design requirements.
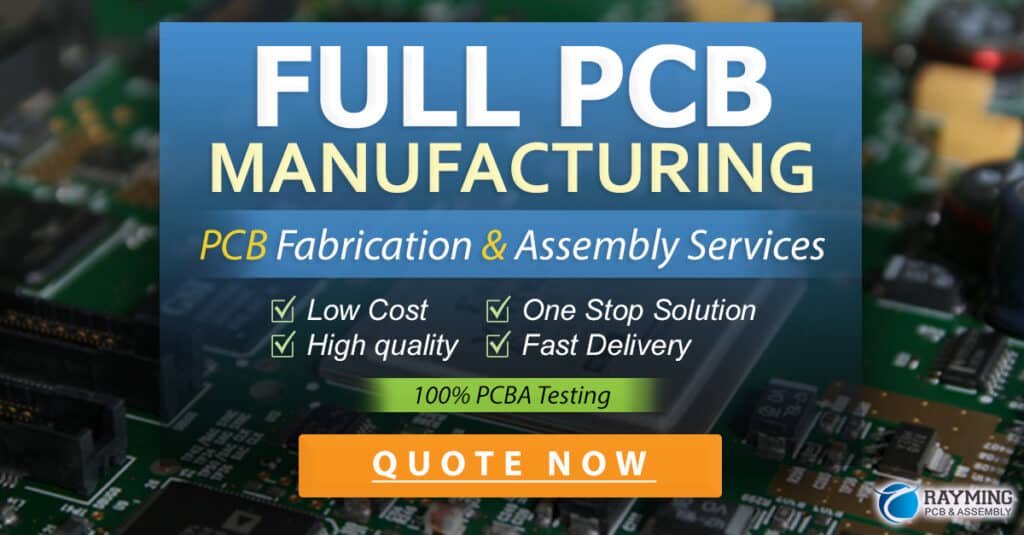
Common PCB Layer Stackups
PCB layer stackups refer to the arrangement and order of the layers within a PCB. The choice of layer stackup depends on various factors, including the circuit requirements, signal integrity considerations, and manufacturing constraints. Let’s explore some common PCB layer stackups.
2-Layer PCB Stackup
A 2-layer PCB is the simplest and most cost-effective stackup, consisting of a single core dielectric layer with copper traces on both sides. The top layer is typically used for component placement and signal routing, while the bottom layer is used for additional routing and ground plane. 2-layer PCBs are suitable for simple, low-density designs with minimal power and signal integrity requirements.
4-Layer PCB Stackup
A 4-layer PCB stackup is a common choice for many applications, offering a good balance between cost and performance. A typical 4-layer stackup consists of the following arrangement:
Layer | Function |
---|---|
Top Layer | Signal routing and component placement |
Ground Layer | Ground plane and signal return path |
Power Layer | Power distribution and signal return path |
Bottom Layer | Signal routing and component placement |
The ground and power layers in a 4-layer stackup provide shielding between the signal layers, reducing crosstalk and EMI. This stackup is suitable for moderate-complexity designs with reasonable signal integrity and power distribution requirements.
6-Layer and 8-Layer PCB Stackups
For more complex designs with higher component density and signal integrity requirements, 6-layer and 8-layer PCB stackups are commonly used. These stackups provide additional signal, power, and ground layers, allowing for more flexible routing and better signal integrity control. A typical 6-layer stackup may include:
Layer | Function |
---|---|
Top Layer | Signal routing and component placement |
Ground Layer | Ground plane and signal return path |
Signal Layer 1 | Signal routing |
Power Layer | Power distribution and signal return path |
Signal Layer 2 | Signal routing |
Bottom Layer | Signal routing and component placement |
An 8-layer stackup extends this further by adding additional signal and ground layers, providing even more routing flexibility and signal integrity control.
Advanced PCB Layer Techniques
In addition to the basic layer stackups, several advanced techniques can be employed to enhance the performance and functionality of PCBs. These techniques involve specialized layer arrangements and manufacturing processes.
High-Density Interconnect (HDI)
High-Density Interconnect (HDI) is a PCB manufacturing technique that enables the creation of very fine pitch traces and vias, allowing for higher component density and more compact designs. HDI PCBs typically involve multiple layers of micro-vias, which are small, laser-drilled holes that interconnect adjacent layers. This technique enables the routing of signals on multiple layers, reducing the overall board size and improving signal integrity.
Embedded Components
Embedded components are another advanced technique used in PCB design. This involves embedding passive components, such as resistors and capacitors, within the PCB substrate itself. By embedding components, designers can save space on the board surface, reduce the overall board size, and improve signal integrity by minimizing the distance between components. Embedded component technology is particularly useful in applications where miniaturization and high performance are critical.
Rigid-Flex PCBs
Rigid-Flex PCBs combine the benefits of both rigid and flexible PCBs, allowing for more complex and compact designs. These PCBs consist of rigid layers bonded to flexible layers, enabling the board to bend or fold in specific areas. Rigid-Flex PCBs are commonly used in applications where space is limited, such as wearable devices, aerospace systems, and medical equipment. The flexible portions of the board can be used for interconnections between rigid sections, reducing the need for cables and connectors.
Designing PCBs with Multiple Layers
Designing PCBs with multiple layers requires careful planning and consideration of various factors. Let’s explore some key aspects of multi-layer PCB design.
Layer Stackup Planning
Layer stackup planning is a critical step in multi-layer PCB design. Designers must carefully consider the arrangement of signal, power, and ground layers to ensure optimal performance and manufacturability. Factors such as the dielectric material properties, layer thicknesses, and copper weights must be taken into account when defining the layer stackup. Proper layer stackup planning helps minimize signal integrity issues, such as crosstalk and EMI, and ensures reliable power distribution.
Signal Routing Techniques
Signal routing is a crucial aspect of multi-layer PCB design. Designers must follow best practices to ensure signal integrity and minimize interference. Some key signal routing techniques include:
-
Trace Width and Spacing: Trace width and spacing should be carefully chosen based on the signal requirements, such as impedance control and current carrying capacity. Proper trace width and spacing help minimize crosstalk and ensure reliable signal transmission.
-
Via Placement: Vias are used to interconnect traces on different layers. Proper via placement is essential to minimize signal integrity issues and ensure manufacturability. Designers should follow guidelines for via size, spacing, and placement to avoid signal degradation and manufacturing defects.
-
Length Matching: In high-speed designs, it is important to match the lengths of critical signal paths to ensure proper timing and minimize skew. Length matching techniques, such as serpentine routing or delay lines, can be used to achieve equal path lengths.
-
Impedance Control: Controlling the impedance of signal traces is crucial for maintaining signal integrity, especially in high-speed designs. Impedance control involves carefully selecting trace width, spacing, and dielectric material properties to achieve the desired characteristic impedance.
Power and Ground Plane Design
Power and ground planes play a vital role in multi-layer PCB design. These planes provide a low-impedance path for power distribution and serve as a reference for signals. When designing power and ground planes, consider the following factors:
-
Plane Thickness: The thickness of the power and ground planes should be sufficient to handle the required current and minimize voltage drop. Thicker planes provide lower impedance and better power distribution.
-
Plane Separation: Adequate separation between power and ground planes helps reduce electromagnetic interference and minimize the coupling between signals. The separation distance depends on the dielectric material properties and the signal frequencies involved.
-
Decoupling Capacitors: Decoupling capacitors should be placed close to the power pins of components to minimize power supply noise and provide a stable reference voltage. Proper placement and sizing of decoupling capacitors are essential for optimal power integrity.
Electromagnetic Compatibility (EMC) Considerations
Electromagnetic Compatibility (EMC) is a critical consideration in multi-layer PCB design. EMC involves ensuring that the PCB does not generate excessive electromagnetic interference (EMI) and is not susceptible to external electromagnetic disturbances. Some key EMC considerations include:
-
Shielding: Shielding techniques, such as the use of ground planes and shielding cans, can be employed to reduce EMI and improve EMC. Proper shielding helps contain electromagnetic radiation and prevents interference with other components or systems.
-
Grounding: Proper grounding is essential for EMC. Ground planes should be carefully designed to provide a low-impedance return path for signals and minimize ground loops. Techniques such as split ground planes or star grounding can be used to optimize grounding performance.
-
Filtering: Filtering techniques, such as the use of ferrite beads or capacitive filters, can be employed to suppress high-frequency noise and improve EMC. Filters help attenuate unwanted signals and prevent them from propagating throughout the system.
Manufacturing Considerations for Multi-Layer PCBs
Manufacturing multi-layer PCBs involves several considerations to ensure the board’s reliability, quality, and cost-effectiveness. Let’s explore some key manufacturing aspects.
PCB Fabrication Process
The PCB fabrication process for multi-layer boards typically involves the following steps:
-
Layer Preparation: Each layer of the PCB is prepared by applying a photoresist coating and exposing it to a pattern using photolithography. The exposed areas are then etched to remove the unwanted copper, leaving the desired traces and pads.
-
Lamination: The prepared layers are stacked and aligned, with dielectric material placed between them. The stack is then subjected to heat and pressure in a lamination press, bonding the layers together to form a solid board.
-
Drilling: Holes are drilled through the laminated board to create vias and component mounting holes. The drilling process can be done mechanically or using laser drilling for smaller, more precise holes.
-
Plating: The drilled holes are plated with copper to create electrical connections between layers. This process involves electroless copper deposition followed by electrolytic copper plating.
-
Solder Mask and Silkscreen: A solder mask layer is applied to the Outer Layers of the board to protect the copper traces and prevent solder bridging. A silkscreen layer is then added to provide component placement indicators and labels.
Design for Manufacturability (DFM)
Design for Manufacturability (DFM) is a crucial consideration in multi-layer PCB design. DFM involves designing the board in a way that ensures efficient and reliable manufacturing. Some key DFM guidelines include:
-
Minimum Feature Sizes: Adhering to the minimum feature sizes specified by the PCB manufacturer, such as minimum trace width, spacing, and hole size, helps ensure manufacturability and reduces the risk of defects.
-
Pad and Via Design: Pads and vias should be designed with appropriate sizes and shapes to ensure reliable soldering and prevent manufacturing issues such as tombstoning or solder bridging.
-
Panelization: Panelization involves grouping multiple PCBs on a single panel for efficient manufacturing. Proper panelization techniques, such as the use of breakaway tabs or mouse bites, help ensure smooth depanelization and minimize board damage.
-
Testability: Designing the PCB with testability in mind, such as providing test points and access to critical signals, facilitates automated testing and troubleshooting during manufacturing and assembly.
Cost Considerations
The cost of manufacturing multi-layer PCBs is influenced by several factors, including:
-
Number of Layers: As the number of layers increases, so does the manufacturing cost. Each additional layer adds complexity to the fabrication process and requires more materials and processing steps.
-
Board Size: Larger board sizes generally result in higher manufacturing costs due to increased material usage and processing time.
-
Material Selection: The choice of PCB materials, such as the dielectric substrate and copper weight, affects the overall cost. High-performance materials, such as low-loss dielectrics or thicker copper layers, tend to be more expensive.
-
Quantity: The quantity of boards manufactured also influences the cost per unit. Higher quantities often result in lower per-unit costs due to economies of scale and more efficient manufacturing processes.
Designers must carefully consider these cost factors and optimize the design to strike a balance between performance, reliability, and cost-effectiveness.
Frequently Asked Questions (FAQ)
- What is the purpose of having multiple layers in a PCB?
Multiple layers in a PCB serve several purposes, including: - Allowing for more complex routing and interconnections between components
- Providing dedicated layers for power distribution and ground planes
- Improving signal integrity by separating signals and reducing crosstalk
-
Enabling higher component density and more compact board sizes
-
How does the number of layers affect the cost of a PCB?
Generally, as the number of layers in a PCB increases, so does the manufacturing cost. Each additional layer adds complexity to the fabrication process, requiring more materials and processing steps. However, the exact cost impact depends on various factors, such as the board size, material selection, and manufacturing quantity. -
What is the difference between signal layers and power/ground layers?
Signal layers are used for routing electrical signals between components on the PCB. They contain copper traces that interconnect various components, allowing for the flow of electrical signals. Power and ground layers, on the other hand, are dedicated to distributing power and providing a low-impedance return path for electrical currents. They help ensure stable power delivery and minimize electromagnetic interference. -
Can I use different materials for different layers in a PCB?
Yes, it is possible to use different materials for different layers in a PCB. This is known as a hybrid stackup. Hybrid stackups allow designers to optimize the performance and cost of the board by selectively using high-performance materials for critical layers while using standard materials for non-critical layers. However, the use of hybrid stackups requires careful design and manufacturing considerations to ensure compatibility and reliability. -
What are the challenges in designing and manufacturing multi-layer PCBs?
Designing and manufacturing multi-layer PCBs come with several challenges, including: - Ensuring proper layer stackup and signal routing to maintain signal integrity
- Managing power distribution and minimizing voltage drops across the board
- Addressing electromagnetic compatibility (EMC) issues and minimizing interference
- Adhering to design for manufacturability (DFM) guidelines to ensure reliable fabrication
- Balancing performance, reliability,
No responses yet