Introduction to PCB Copper
Printed Circuit Boards (PCBs) are essential components in modern electronics. They provide a platform for mounting and interconnecting electronic components to create functional circuits. One of the critical elements of a PCB is the copper layer, which plays a vital role in conducting electricity and heat dissipation. In this article, we will delve into the world of PCB copper layers, exploring their types, properties, and manufacturing processes.
What are PCB Copper Layers?
PCB copper layers are thin sheets of Copper Foil that are laminated onto a non-conductive substrate, typically made of fiberglass or other dielectric materials. The copper layers are etched to create conductive traces, pads, and vias that allow electronic components to be connected and communicate with each other.
The Role of Copper in PCBs
Copper is the material of choice for PCB Layers due to its excellent electrical and thermal conductivity properties. It allows for efficient transfer of electrical signals and helps dissipate heat generated by components. Copper’s malleability and ductility also make it easy to etch and shape into the desired patterns.
Copper Thickness
The thickness of the copper layer is an important consideration in PCB design. It is measured in ounces per square foot (oz/ft²) or micrometers (μm). The most common copper thicknesses used in PCBs are:
Copper Weight (oz/ft²) | Thickness (μm) |
---|---|
0.5 | 17.5 |
1 | 35 |
2 | 70 |
3 | 105 |
The choice of copper thickness depends on the current carrying requirements, signal integrity, and manufacturing constraints of the PCB.
Types of PCB Copper Layers
PCBs can have different numbers and configurations of copper layers depending on the complexity and requirements of the circuit. Let’s explore the common types of PCB copper layers.
Single Layer PCBs
Single layer PCBs have copper on only one side of the substrate. They are the simplest and most cost-effective type of PCB, suitable for low-complexity circuits with few components. Single layer PCBs are commonly used in consumer electronics, such as remote controls and simple appliances.
Double Layer PCBs
Double layer PCBs have copper on both sides of the substrate, allowing for more complex routing and higher component density compared to single layer PCBs. The two copper layers are connected using vias, which are small holes drilled through the board and plated with copper. Double layer PCBs are widely used in a variety of applications, from smartphones to industrial control systems.
Multi-Layer PCBs
Multi-layer PCBs have three or more copper layers laminated together with insulating material in between. The inner layers are used for power and ground planes, while the Outer Layers are used for signal routing. Multi-layer PCBs offer several advantages:
- Increased routing density and complexity
- Improved signal integrity and reduced crosstalk
- Better power distribution and heat dissipation
- Reduced electromagnetic interference (EMI)
Multi-layer PCBs are essential for high-speed digital circuits, RF and microwave applications, and aerospace and defense systems.
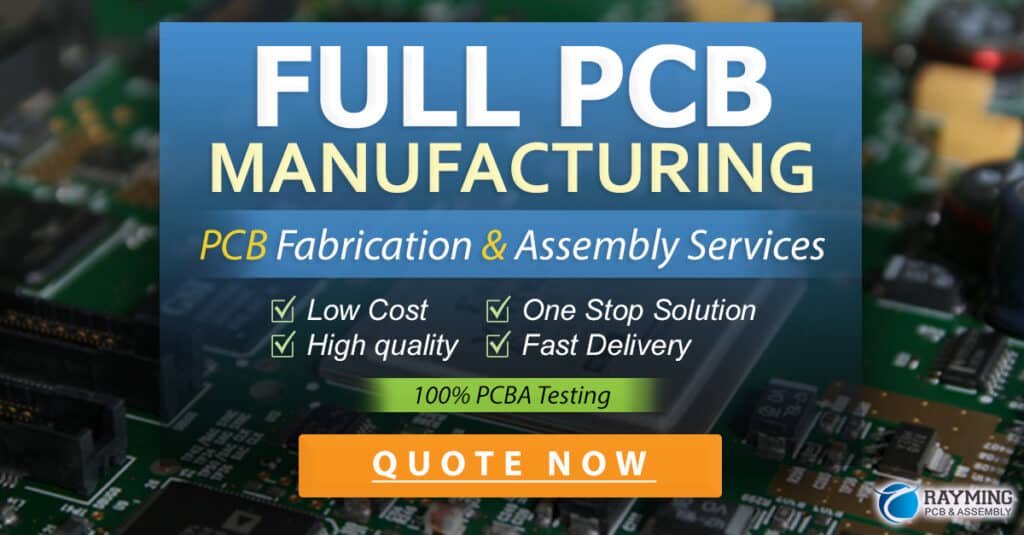
PCB Copper Manufacturing Process
The manufacturing process of PCB copper layers involves several steps to achieve the desired pattern and functionality. Let’s take a closer look at each step.
PCB Lamination
The first step in PCB copper manufacturing is lamination. The copper foil is bonded to the non-conductive substrate using heat and pressure. The most common lamination methods are:
-
Prepreg Lamination: Prepreg (pre-impregnated) is a glass fiber cloth pre-coated with a heat-curable resin. The copper foil and prepreg are stacked together and pressed under high temperature and pressure to form a solid board.
-
FR-4 Lamination: FR-4 (Flame Retardant 4) is a composite material made of woven fiberglass cloth and epoxy resin. The copper foil is laminated onto the FR-4 substrate using a similar process as prepreg lamination.
Drilling
After lamination, holes are drilled through the board to create vias and component mounting holes. The drilling process can be done using mechanical drills or laser drills, depending on the hole size and accuracy requirements.
Plating
The drilled holes are then plated with copper to create electrical connections between layers. The most common plating methods are:
-
Electroless Copper Plating: A thin layer of copper is deposited onto the hole walls using a chemical process without electrical current.
-
Electrolytic Copper Plating: A thicker layer of copper is deposited onto the hole walls using an electrical current in an electrolyte solution.
Patterning
The next step is to create the desired copper pattern on the board. This is done using a photolithography process:
- The board is coated with a light-sensitive photoresist.
- The photoresist is exposed to UV light through a photomask with the desired pattern.
- The exposed photoresist is developed, leaving the desired pattern on the copper.
- The unwanted copper is etched away using a chemical solution.
- The remaining photoresist is stripped off, leaving the final copper pattern.
Finishing
After patterning, the PCB copper layers undergo various finishing processes to protect the copper from oxidation and improve solderability. Some common finishing options are:
- HASL (Hot Air Solder Leveling): A thin layer of solder is applied to the copper surfaces using hot air.
- ENIG (Electroless Nickel Immersion Gold): A layer of nickel is deposited onto the copper, followed by a thin layer of gold.
- OSP (Organic Solderability Preservative): A thin organic coating is applied to the copper to prevent oxidation.
Copper Layer Design Considerations
When designing PCB copper layers, several factors need to be considered to ensure optimal performance and manufacturability.
Trace Width and Spacing
The width and spacing of copper traces determine the current carrying capacity and signal integrity of the PCB. Wider traces can carry more current and have lower resistance, but they also take up more space. Narrower traces allow for higher routing density but have higher resistance and are more susceptible to manufacturing defects.
The minimum trace width and spacing are limited by the PCB manufacturing capabilities and the design rules specified by the PCB fabricator. It is important to follow these design rules to ensure the manufacturability and reliability of the PCB.
Via Size and Placement
Vias are essential for connecting different copper layers in a multi-layer PCB. The size and placement of vias affect the signal integrity and manufacturability of the PCB.
Smaller vias allow for higher routing density and better signal integrity, but they are more challenging to manufacture and have lower current carrying capacity. Larger vias are easier to manufacture and can carry more current, but they take up more space and can cause signal integrity issues.
The placement of vias is also critical. Vias should be placed strategically to minimize the signal path length and avoid interference with other components and traces.
Copper Pour and Ground Planes
Copper pour and ground planes are large areas of copper on the PCB that serve various purposes:
- Power Distribution: Copper pour can be used to distribute power to components, reducing voltage drop and improving power integrity.
- Heat Dissipation: Copper has excellent thermal conductivity and can help dissipate heat generated by components.
- EMI Shielding: Copper pour can act as a shield against electromagnetic interference (EMI), reducing noise and crosstalk.
- Signal Return Path: Ground planes provide a low-impedance return path for signals, improving signal integrity and reducing crosstalk.
When designing copper pour and ground planes, it is important to consider the current carrying requirements, thermal management, and EMI shielding needs of the PCB.
PCB Copper Layer Testing and Inspection
After manufacturing, PCB copper layers need to be tested and inspected to ensure they meet the required specifications and quality standards.
Electrical Testing
Electrical testing is performed to verify the continuity and insulation of the copper traces and vias. Some common electrical tests are:
- Continuity Test: Checks if all the intended connections are intact and have low resistance.
- Isolation Test: Checks if there are any unintended short circuits between traces or layers.
- Impedance Test: Measures the impedance of the traces to ensure they match the designed values.
Visual Inspection
Visual inspection is done to check for any visible defects or anomalies on the PCB copper layers. Some common visual inspection methods are:
- Automated Optical Inspection (AOI): Uses cameras and image processing algorithms to detect defects such as broken traces, missing pads, or short circuits.
- Manual Visual Inspection: Trained operators visually inspect the PCB under magnification to identify any defects or workmanship issues.
Microsectioning
Microsectioning is a destructive testing method used to evaluate the internal structure and quality of the PCB copper layers. A small section of the PCB is cut, polished, and examined under a microscope to check for any defects or deviations from the specified dimensions and tolerances.
Frequently Asked Questions (FAQ)
1. What is the difference between copper weight and thickness?
Copper weight is expressed in ounces per square foot (oz/ft²) and represents the amount of copper deposited on the PCB substrate. Copper thickness, on the other hand, is the actual thickness of the copper layer measured in micrometers (μm) or mils (1 mil = 25.4 μm). The relationship between copper weight and thickness is as follows:
Copper Weight (oz/ft²) | Thickness (μm) | Thickness (mils) |
---|---|---|
0.5 | 17.5 | 0.7 |
1 | 35 | 1.4 |
2 | 70 | 2.8 |
3 | 105 | 4.2 |
2. Can I mix different copper weights on the same PCB?
Yes, it is possible to have different copper weights on different layers of the same PCB. This is commonly done in high-power applications where thicker copper is used on the power and ground layers to handle higher currents, while thinner copper is used on the signal layers to achieve finer pitch and higher routing density.
However, mixing copper weights on the same layer is generally not recommended as it can cause manufacturing issues and affect the impedance and current carrying capacity of the traces.
3. What is the maximum number of copper layers in a PCB?
The maximum number of copper layers in a PCB is limited by the manufacturing capabilities of the PCB fabricator and the design requirements of the application. Some PCB manufacturers can produce boards with up to 50 layers or more, but such high layer counts are rare and expensive.
In practice, most PCBs have between 2 and 12 layers, with 4 and 6 layers being the most common for complex designs. The number of layers is determined by factors such as the size and complexity of the circuit, the signal integrity and power delivery requirements, and the cost and manufacturability constraints.
4. How do I choose the right copper thickness for my PCB?
The choice of copper thickness depends on several factors, including:
- Current Carrying Requirements: Thicker copper can carry more current and has lower resistance, which is important for power delivery and high-current applications.
- Signal Integrity: Thinner copper can achieve finer trace widths and spacing, which is beneficial for high-speed signals and dense routing.
- Thermal Management: Thicker copper has better thermal conductivity and can help dissipate heat from power components.
- Manufacturing Constraints: Thinner copper is easier to etch and has better yield, while thicker copper is more challenging to manufacture and has higher cost.
As a general guideline, 1 oz copper (35 μm) is sufficient for most signal layers, while 2 oz (70 μm) or thicker copper is recommended for power and ground layers. However, the actual copper thickness should be determined based on the specific requirements and constraints of the PCB design, in consultation with the PCB fabricator.
5. What is the difference between copper foil and copper-clad laminate?
Copper foil is a thin sheet of pure copper that is used to create the conductive layers of a PCB. It is available in various thicknesses and grades, and is typically supplied in rolls or sheets.
Copper-clad laminate (CCL) is a composite material consisting of a non-conductive substrate (such as FR-4) bonded with copper foil on one or both sides. The copper foil is laminated onto the substrate using heat and pressure, forming a solid board that can be further processed to create the PCB.
In other words, copper foil is the raw material that is used to create the copper layers of a PCB, while copper-clad laminate is the semi-finished product that is used as the starting point for PCB fabrication.
Conclusion
PCB copper layers are a critical component of modern electronics, providing the conductive pathways that allow components to communicate and function together. Understanding the types, properties, and manufacturing processes of PCB copper layers is essential for designing and producing reliable and high-performance electronic devices.
From choosing the right copper thickness and designing optimal trace and via layouts, to ensuring proper testing and inspection, every aspect of PCB copper layer engineering requires careful consideration and attention to detail.
As technology advances and electronic devices become more complex and compact, the demands on PCB copper layers will continue to grow. Innovations in materials, manufacturing processes, and design tools will be needed to meet these challenges and enable the next generation of electronic products.
By staying up-to-date with the latest developments and best practices in PCB copper layer engineering, designers and manufacturers can create PCBs that are not only functional and reliable, but also cost-effective and environmentally sustainable.
No responses yet