Introduction to Ceramic PCB
Ceramic PCBs, or printed circuit boards, are a type of substrate material used in the manufacturing of electronic devices. Unlike traditional PCBs that use glass-reinforced epoxy (FR4) as the base material, ceramic PCBs utilize ceramic materials such as alumina (Al2O3) or aluminum nitride (AlN). These materials offer unique properties that make them suitable for specific applications where conventional PCBs may not be adequate.
Advantages of Ceramic PCBs
Ceramic PCBs offer several advantages over their traditional counterparts:
- High thermal conductivity: Ceramic materials have excellent thermal conductivity, allowing for efficient heat dissipation from electronic components.
- Low dielectric constant: The low dielectric constant of ceramic materials minimizes signal loss and cross-talk, making them ideal for high-frequency applications.
- Dimensional stability: Ceramic PCBs maintain their shape and size under varying temperature conditions, ensuring consistent performance.
- High strength and durability: Ceramic materials are known for their strength and resistance to wear and tear, making them suitable for harsh environments.
Materials Used in Ceramic PCBs
Alumina (Al2O3)
Alumina, or aluminum oxide, is the most commonly used ceramic material in PCB manufacturing. It offers several benefits:
- Excellent electrical insulation properties
- High thermal conductivity
- Good mechanical strength
- Resistance to chemical corrosion
Alumina PCBs are available in various purities, typically ranging from 92% to 99.5%. The higher the purity, the better the thermal conductivity and dielectric properties.
Aluminum Nitride (AlN)
Aluminum nitride is another ceramic material used in PCB manufacturing. It offers some unique advantages over alumina:
- Higher thermal conductivity than alumina
- Lower thermal expansion coefficient, minimizing thermal stress on components
- High electrical resistivity
- Good mechanical strength
AlN PCBs are often used in high-power applications where efficient heat dissipation is critical.
Comparison of Alumina and Aluminum Nitride
Property | Alumina (Al2O3) | Aluminum Nitride (AlN) |
---|---|---|
Thermal Conductivity | Good | Excellent |
Dielectric Constant | Good | Good |
Mechanical Strength | Good | Good |
Thermal Expansion | Moderate | Low |
Electrical Resistivity | Good | Excellent |
Cost | Moderate | High |
Types of Ceramic PCBs
Single-Layer Ceramic PCBs
Single-layer ceramic PCBs consist of a single layer of ceramic substrate with conductive tracks on one side. They are the simplest and most cost-effective type of ceramic PCB. Single-Layer PCBs are suitable for basic applications with low circuit complexity.
Multilayer Ceramic PCBs
Multilayer ceramic PCBs consist of multiple layers of ceramic substrates bonded together with conductive tracks on each layer. The layers are interconnected using vias, allowing for more complex circuit designs. Multilayer PCBs offer several advantages:
- Increased circuit density
- Improved signal integrity
- Reduced overall board size
- Enhanced thermal management
Multilayer ceramic PCBs are commonly used in high-performance applications such as telecommunications, aerospace, and defense industries.
Thick-Film Ceramic PCBs
Thick-film ceramic PCBs are manufactured by screen printing conductive paste onto a ceramic substrate. The conductive paste, typically made of silver or copper, is fired at high temperatures to form a thick, robust layer. Thick-film PCBs offer several benefits:
- High current carrying capacity
- Resistance to high temperatures
- Good adhesion between the conductive layer and the substrate
- Cost-effective for low-volume production
Thick-film ceramic PCBs are often used in power electronics, automotive, and sensor applications.
Thin-Film Ceramic PCBs
Thin-film ceramic PCBs are manufactured by depositing a thin layer of conductive material, usually gold or copper, onto a ceramic substrate using physical vapor deposition (PVD) or chemical vapor deposition (CVD) techniques. Thin-film PCBs offer several advantages:
- High precision and fine feature sizes
- Excellent high-frequency performance
- Low resistivity and high conductivity
- Suitable for miniaturization
Thin-film ceramic PCBs are used in high-frequency applications such as radar systems, satellite communications, and medical devices.
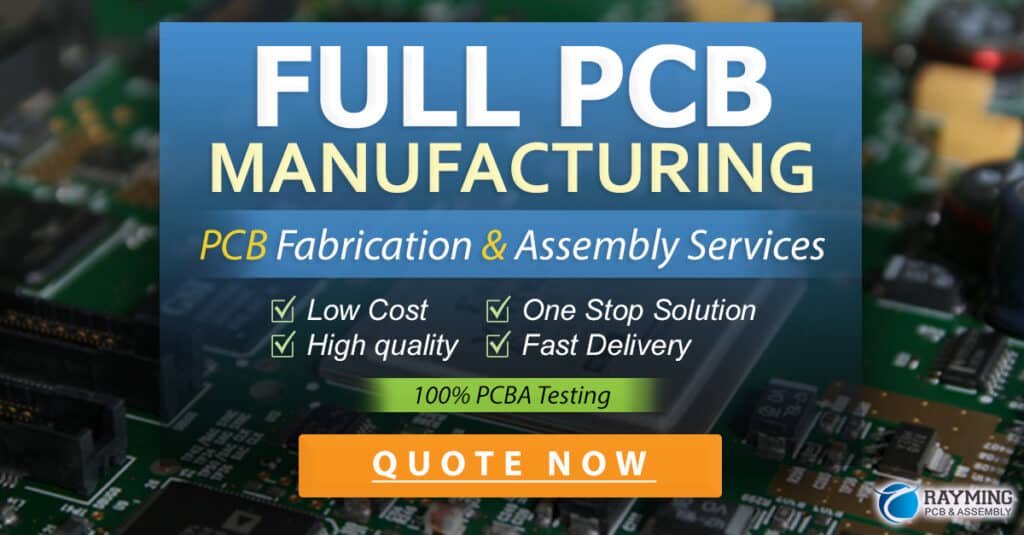
Applications of Ceramic PCBs
Ceramic PCBs find applications in various industries due to their unique properties:
- Aerospace and Defense:
- Radar systems
- Satellite communications
- Missile guidance systems
- Telecommunications:
- High-frequency radio systems
- Base stations
- Microwave devices
- Automotive:
- Engine control units
- Power electronics
- Sensor systems
- Medical Devices:
- Implantable devices
- High-frequency therapy equipment
- Diagnostic imaging systems
- Industrial:
- High-temperature sensors
- Power converters
- Motor drives
Manufacturing Process of Ceramic PCBs
The manufacturing process of ceramic PCBs involves several steps:
- Substrate Preparation:
- The ceramic substrate is cleaned and inspected for defects.
- Vias and other features are drilled or punched into the substrate.
- Metallization:
- A conductive layer, usually copper, is applied to the substrate using techniques such as screen printing, PVD, or CVD.
- The conductive layer is patterned using photolithography or laser ablation.
- Insulation and Lamination:
- For multilayer PCBs, additional ceramic layers are stacked and laminated together under high pressure and temperature.
- Insulating materials, such as glass or polymer, may be used between layers.
- Sintering:
- The laminated board is fired in a high-temperature furnace to bond the layers together and form a dense, strong structure.
- Post-Processing:
- Surface finishing, such as plating or coating, is applied to protect the conductive layers and improve solderability.
- Electrical testing is performed to ensure the functionality and reliability of the PCB.
Challenges and Considerations
While ceramic PCBs offer numerous benefits, there are some challenges and considerations to keep in mind:
- Cost: Ceramic materials and manufacturing processes are generally more expensive than traditional PCBs.
- Fragility: Ceramic materials are brittle and prone to cracking under mechanical stress, requiring careful handling during assembly and use.
- Design Complexity: The high thermal conductivity and low dielectric constant of ceramic materials may require specialized design considerations for optimal performance.
- Manufacturing Expertise: The manufacturing of ceramic PCBs requires specialized equipment and expertise, which may limit the number of available suppliers.
Future Trends and Developments
As electronic devices continue to push the boundaries of performance and miniaturization, ceramic PCBs are expected to play an increasingly important role. Some future trends and developments include:
- Advanced Ceramic Materials: Researchers are exploring new ceramic materials with enhanced properties, such as higher thermal conductivity and lower dielectric loss.
- 3D Printing: Additive manufacturing techniques, such as 3D printing, are being investigated for the fabrication of ceramic PCBs, enabling more complex geometries and faster prototyping.
- Integration with Other Technologies: Ceramic PCBs are being integrated with other advanced technologies, such as embedded components and micro-electromechanical systems (MEMS), to create highly integrated and multifunctional devices.
- High-Frequency Applications: As the demand for high-frequency communication systems grows, ceramic PCBs are expected to find increasing use in 5G networks, millimeter-wave devices, and satellite communications.
Frequently Asked Questions (FAQ)
- What are the main advantages of ceramic PCBs over traditional PCBs?
-
Ceramic PCBs offer high thermal conductivity, low dielectric constant, dimensional stability, and high strength and durability compared to traditional PCBs.
-
What are the most common ceramic materials used in PCB manufacturing?
-
The most common ceramic materials used in PCB manufacturing are alumina (Al2O3) and aluminum nitride (AlN).
-
What are the different types of ceramic PCBs?
-
The main types of ceramic PCBs are single-layer, multilayer, thick-film, and thin-film PCBs, each with their own unique characteristics and manufacturing processes.
-
In which industries are ceramic PCBs commonly used?
-
Ceramic PCBs are commonly used in industries such as aerospace, defense, telecommunications, automotive, medical devices, and industrial applications.
-
What are some of the challenges and considerations when using ceramic PCBs?
- Ceramic PCBs are generally more expensive than traditional PCBs, brittle and prone to cracking under mechanical stress, may require specialized design considerations, and require specialized manufacturing expertise.
Conclusion
Ceramic PCBs offer a range of unique properties that make them suitable for demanding applications where traditional PCBs may not suffice. With their high thermal conductivity, low dielectric constant, and excellent mechanical strength, ceramic PCBs are finding increasing use in industries such as aerospace, telecommunications, automotive, and medical devices.
As electronic devices continue to evolve and push the boundaries of performance, ceramic PCBs are expected to play a crucial role in enabling the next generation of high-frequency, high-power, and miniaturized systems. However, the higher cost and specialized manufacturing requirements of ceramic PCBs must be carefully considered when selecting the appropriate substrate material for a given application.
With ongoing research and development in advanced ceramic materials, manufacturing processes, and integration with other technologies, the future of ceramic PCBs looks promising. As designers and manufacturers continue to innovate and push the limits of what is possible, ceramic PCBs will undoubtedly remain a key enabling technology in the ever-evolving landscape of electronic devices.
No responses yet