Introduction to PCB Boards
A Printed Circuit Board (PCB) is the foundation of virtually all modern electronic devices. It is a thin board made of fiberglass or composite material that has conductive pathways printed or etched onto it to connect various electronic components. PCBs provide mechanical support and electrical connections for components like resistors, capacitors, and integrated circuits, enabling them to function as a complete electronic system.
In this comprehensive guide, we’ll dive deep into the world of PCBs, exploring their types, manufacturing process, design considerations, and applications. Whether you’re an electronics enthusiast, a student, or someone curious about how electronic devices work, this guide will provide you with a solid understanding of PCB Basics.
Types of PCB Boards
Single-Layer PCBs
Single-layer PCBs, also known as single-sided PCBs, have conductive traces on only one side of the board. These are the simplest and most cost-effective PCBs, suitable for basic electronic projects and low-density designs. However, single-layer PCBs have limitations in terms of circuit complexity and component density.
Double-Layer PCBs
Double-layer PCBs have conductive traces on both sides of the board, allowing for more complex circuits and higher component density compared to single-layer PCBs. The two layers are connected using through-hole vias, which are small holes drilled through the board and plated with conductive material. Double-layer PCBs are widely used in consumer electronics, such as smartphones, laptops, and televisions.
Multi-Layer PCBs
Multi-layer PCBs consist of three or more conductive layers separated by insulating layers. These boards offer the highest level of circuit complexity and component density, making them ideal for advanced electronic applications, such as aerospace, medical devices, and high-performance computing. Multi-layer PCBs can have as many as 50 layers or more, depending on the design requirements.
PCB Type | Layers | Complexity | Cost | Applications |
---|---|---|---|---|
Single-Layer | 1 | Low | Low | Basic projects, low-density designs |
Double-Layer | 2 | Medium | Medium | Consumer electronics, smartphones, laptops |
Multi-Layer | 3+ | High | High | Aerospace, medical devices, high-performance computing |
PCB Manufacturing Process
The PCB manufacturing process involves several steps, each of which is crucial for ensuring the quality and reliability of the final product.
1. Design and Layout
The first step in PCB manufacturing is designing the circuit and creating the PCB layout using specialized software, such as Altium Designer, Eagle, or KiCad. The layout defines the position and interconnection of components, as well as the placement of conductive traces, vias, and other features.
2. Printing the Circuit Pattern
Once the design is finalized, the circuit pattern is printed onto a transparent film or photomask. This film is used to transfer the circuit pattern onto the copper-clad laminate during the photoresist application process.
3. Applying Photoresist
The copper-clad laminate is coated with a light-sensitive photoresist material. The photomask is then placed on top of the photoresist, and the board is exposed to UV light. The areas of the photoresist that are exposed to light become soluble, while the unexposed areas remain insoluble.
4. Developing and Etching
After exposure, the board is developed, removing the soluble photoresist and revealing the copper traces underneath. The board is then placed in an etching solution, which removes the unwanted copper, leaving only the desired circuit pattern.
5. Drilling and Plating
Holes are drilled into the board for through-hole components and vias. These holes are then plated with a conductive material, typically copper, to ensure electrical connectivity between layers.
6. Solder Mask and Silkscreen
A solder mask, usually green in color, is applied to the board to protect the copper traces and prevent solder bridges. A silkscreen layer is then added to provide text and symbols for component identification and assembly guidance.
7. Surface Finish
Finally, a surface finish, such as HASL (Hot Air Solder Leveling), ENIG (Electroless Nickel Immersion Gold), or OSP (Organic Solderability Preservative), is applied to the exposed copper to prevent oxidation and enhance solderability.
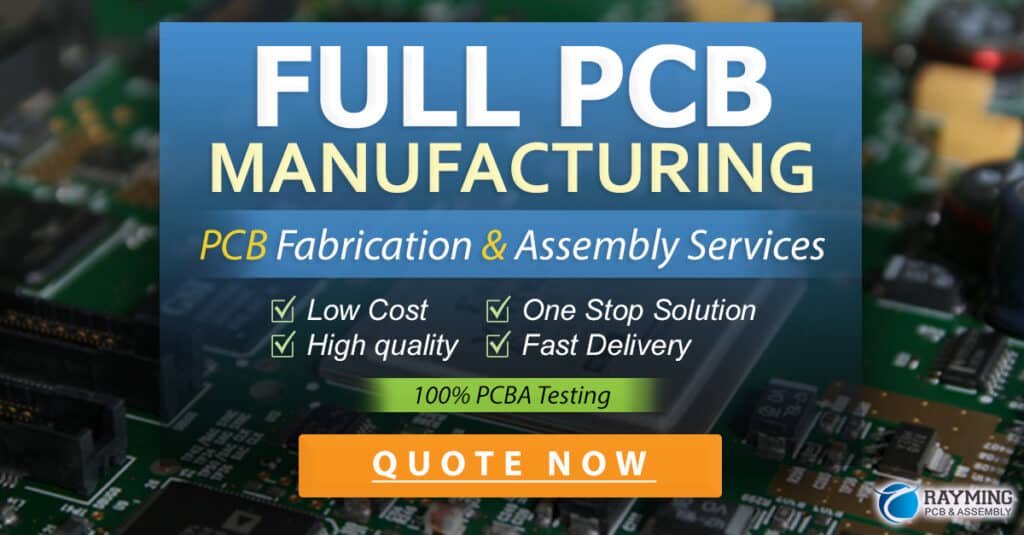
PCB Design Considerations
When designing a PCB, several factors must be considered to ensure optimal performance, reliability, and manufacturability.
Component Placement
Proper component placement is crucial for minimizing signal interference, reducing noise, and optimizing circuit performance. Components should be placed in a logical and organized manner, considering factors such as signal flow, heat dissipation, and mechanical constraints.
Trace Width and Spacing
The width and spacing of conductive traces on a PCB depend on factors such as the current carrying capacity, voltage, and signal frequency. Wider traces can carry more current and are less susceptible to signal integrity issues, while narrower traces allow for higher component density. Proper spacing between traces is essential to prevent crosstalk and signal interference.
Grounding and Shielding
Effective grounding and shielding techniques are essential for minimizing electromagnetic interference (EMI) and ensuring signal integrity. Ground planes, power planes, and shielding layers can be incorporated into the PCB design to provide a low-impedance return path for signals and to shield sensitive circuits from external interference.
Thermal Management
Thermal management is critical for ensuring the longevity and reliability of electronic components. PCB designs should incorporate features such as thermal vias, heat sinks, and adequate copper pours to dissipate heat efficiently and prevent components from overheating.
PCB Applications
PCBs find applications in virtually every aspect of modern life, from consumer electronics to industrial equipment and beyond.
Consumer Electronics
PCBs are the backbone of consumer electronic devices, such as smartphones, laptops, televisions, and home appliances. These devices rely on PCBs for their compact size, reliability, and functionality.
Industrial Automation
In industrial automation, PCBs are used in control systems, sensors, actuators, and communication devices. They enable the monitoring and control of industrial processes, ensuring efficiency, safety, and productivity.
Automotive Electronics
Modern vehicles incorporate numerous electronic systems, such as engine control units, infotainment systems, and advanced driver assistance systems (ADAS). PCBs play a vital role in enabling these systems, providing reliable and robust performance in demanding automotive environments.
Medical Devices
PCBs are essential components in various medical devices, such as patient monitors, imaging equipment, and implantable devices. They enable the precise monitoring and control of vital functions, contributing to improved patient care and outcomes.
Frequently Asked Questions
1. What is the difference between a PCB and a printed wiring board (PWB)?
PCB and PWB are often used interchangeably, but there is a slight difference. A PCB refers to a board with printed conductive traces and components mounted on it, while a PWB refers to a board with only the conductive traces, without any components.
2. Can PCBs be recycled?
Yes, PCBs can be recycled. The recycling process involves separating the various materials, such as copper, fiberglass, and precious metals, which can then be used to manufacture new PCBs or other products. Recycling PCBs helps reduce electronic waste and conserve natural resources.
3. What is the difference between through-hole and surface-mount components?
Through-hole components have leads that are inserted into holes drilled in the PCB and soldered on the opposite side. Surface-mount components, on the other hand, are mounted directly onto the surface of the PCB and soldered in place. Surface-mount components are smaller and allow for higher component density, while through-hole components are more robust and easier to replace.
4. How do I choose the right PCB manufacturer?
When choosing a PCB manufacturer, consider factors such as their experience, capabilities, quality control processes, and customer support. Look for manufacturers with industry certifications, such as ISO 9001, and those who can provide a wide range of services, from prototyping to full-scale production. Reading reviews and requesting quotes from multiple manufacturers can help you make an informed decision.
5. What is the typical turnaround time for PCB fabrication?
The turnaround time for PCB fabrication depends on various factors, such as the complexity of the design, the number of layers, and the selected manufacturing options. For simple designs, the turnaround time can be as short as 24-48 hours, while more complex designs may take several weeks. Many PCB manufacturers offer expedited services for an additional fee, which can significantly reduce the turnaround time.
Conclusion
PCBs are the unsung heroes of the modern electronic world, enabling the development of increasingly complex and powerful devices. By understanding the basics of PCBs, including their types, manufacturing process, design considerations, and applications, you can better appreciate the technology that surrounds us and make informed decisions when developing electronic projects.
As technology continues to advance, the role of PCBs will only become more crucial. Staying up-to-date with the latest trends and best practices in PCB design and manufacturing will help you create innovative, reliable, and efficient electronic devices that can shape the future.
No responses yet