Introduction to PCB SMT
Surface Mount Technology (SMT) has revolutionized the printed circuit board (PCB) manufacturing industry since its introduction in the 1960s. SMT is a method of mounting electronic components directly onto the surface of a PCB, unlike through-hole technology (THT) where components are inserted into drilled holes and soldered on the opposite side of the board. SMT has become the dominant assembly process for PCBs due to its numerous advantages over THT.
In this article, we will explore the various advantages of PCB SMT, including:
- Miniaturization and increased component density
- Improved reliability and performance
- Faster assembly and higher productivity
- Cost-effectiveness and reduced material consumption
- Enhanced design flexibility and innovation
Miniaturization and Increased Component Density
One of the most significant advantages of PCB SMT is its ability to enable miniaturization and increase component density on a circuit board. SMT components are much smaller than their through-hole counterparts, allowing for more components to be placed on a single board. This increased density leads to several benefits:
Smaller PCB Sizes
With SMT, PCBs can be designed to be much smaller than those using THT. The reduced size of SMT components allows for more efficient use of board space, resulting in compact and lightweight PCBs. This is particularly advantageous in applications where space is limited, such as mobile devices, wearable technology, and aerospace systems.
Increased Functionality
The higher component density achieved with SMT enables designers to incorporate more features and functions into a single PCB. This means that a smaller PCB can perform the same tasks as a larger THT board, or even more. The increased functionality per unit area is crucial in today’s electronics industry, where consumers demand ever-more sophisticated devices in smaller packages.
Improved Signal Integrity
As PCBs become more compact, the distance between components decreases, leading to improved signal integrity. Shorter traces between components result in reduced signal propagation delays, minimizing the risk of signal distortion and interference. This is especially important in high-frequency applications, such as telecommunications and networking equipment.
Parameter | THT | SMT |
---|---|---|
Component Size | Large | Small |
Component Density | Low | High |
PCB Size | Large | Small |
Signal Integrity | Moderate | High |
Improved Reliability and Performance
Another key advantage of PCB SMT is its superior reliability and performance compared to THT. SMT components are mounted directly onto the surface of the PCB, creating a stronger mechanical bond and better electrical connection. This leads to several benefits:
Reduced Mechanical Stress
SMT components are not subjected to the same mechanical stress as through-hole components during the assembly process. In THT, components are inserted into drilled holes, which can cause stress on the component leads and the PCB itself. With SMT, components are gently placed onto the surface of the board, minimizing the risk of mechanical damage.
Better Thermal Management
SMT components have a smaller thermal mass than through-hole components, allowing for better heat dissipation. The direct contact between the component and the PCB surface enables more efficient heat transfer, reducing the risk of component failure due to overheating. This is particularly important in high-power applications, such as power electronics and automotive systems.
Improved Shock and Vibration Resistance
The strong mechanical bond between SMT components and the PCB makes SMT assemblies more resistant to shock and vibration. This is crucial in applications where the PCB is subjected to harsh environmental conditions, such as in automotive, aerospace, and industrial systems. The improved reliability of SMT assemblies translates to longer product lifetimes and reduced maintenance costs.
Parameter | THT | SMT |
---|---|---|
Mechanical Stress | High | Low |
Thermal Management | Moderate | High |
Shock and Vibration Resistance | Moderate | High |
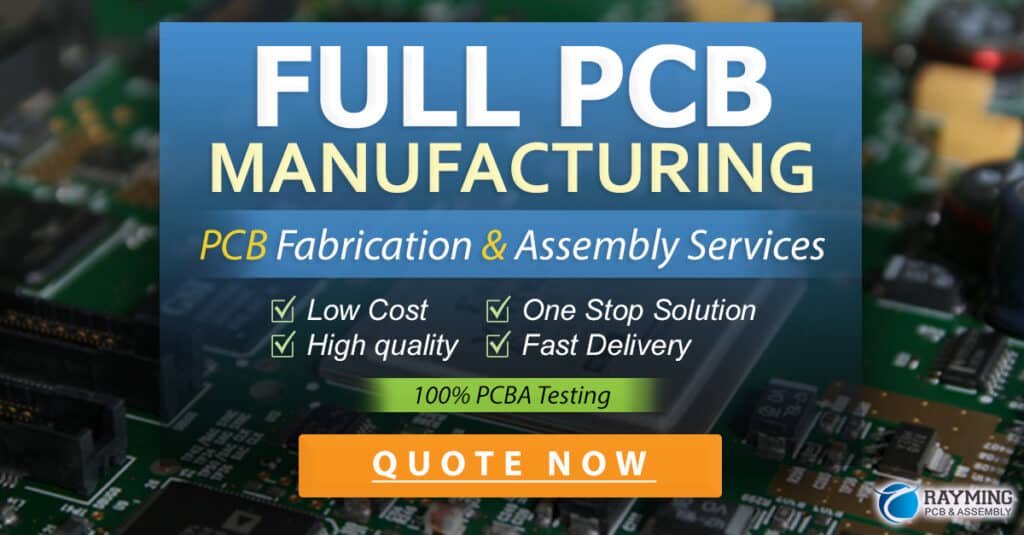
Faster Assembly and Higher Productivity
SMT offers significant advantages over THT in terms of assembly speed and productivity. The automated nature of the SMT process enables faster placement of components and higher throughput rates, resulting in several benefits:
Automated Pick-and-Place Machines
SMT assembly relies heavily on automated pick-and-place machines, which can rapidly and accurately place components onto the PCB surface. These machines can handle a wide range of component sizes and types, from tiny chip resistors to large ball grid array (BGA) packages. The high speed and precision of these machines greatly reduce assembly time compared to manual THT assembly.
Parallel Processing
SMT allows for parallel processing of PCBs, where multiple boards can be assembled simultaneously on a single production line. This is made possible by the use of panel PCBs, where multiple identical circuits are fabricated on a single large board. The panel is then populated with components using SMT and later divided into individual PCBs. This parallel processing capability significantly increases productivity and reduces overall assembly time.
Reduced Human Intervention
The automated nature of SMT assembly reduces the need for human intervention, minimizing the risk of human error and increasing consistency in the final product. Automated optical inspection (AOI) systems can quickly and accurately detect assembly defects, ensuring that only high-quality PCBs leave the production line. This reduced reliance on manual labor also contributes to faster assembly times and higher productivity.
Parameter | THT | SMT |
---|---|---|
Assembly Speed | Slow | Fast |
Automation | Low | High |
Parallel Processing | Limited | Extensive |
Human Intervention | High | Low |
Cost-Effectiveness and Reduced Material Consumption
SMT offers several cost advantages over THT, making it a more economical choice for PCB Assembly. The cost benefits of SMT stem from its reduced material consumption and increased efficiency:
Reduced PCB Real Estate
The smaller size of SMT components and the increased component density achieved with SMT result in smaller PCBs. This reduction in PCB real estate translates to lower material costs, as less PCB substrate is required for a given circuit design. The cost savings are particularly significant in high-volume production runs.
Lower Component Costs
SMT components are generally less expensive than their through-hole counterparts due to their smaller size and the economies of scale achieved in their production. The widespread adoption of SMT has led to a vast ecosystem of component suppliers, further driving down costs through competition and innovation.
Reduced Drilling Costs
SMT eliminates the need for drilling holes in the PCB, which is a significant cost factor in THT assembly. Drilling is a time-consuming process that requires specialized equipment and tooling, adding to the overall cost of THT PCBs. With SMT, these drilling costs are eliminated, resulting in a more cost-effective assembly process.
Less Material Waste
SMT components have shorter leads than through-hole components, resulting in less material waste during the assembly process. In THT, the excess lead material must be trimmed after soldering, creating waste that must be disposed of properly. With SMT, there is minimal excess material, reducing waste and the associated disposal costs.
Parameter | THT | SMT |
---|---|---|
PCB Real Estate | High | Low |
Component Costs | High | Low |
Drilling Costs | High | None |
Material Waste | High | Low |
Enhanced Design Flexibility and Innovation
SMT offers designers greater flexibility and the ability to innovate in ways that were previously not possible with THT. The increased design freedom provided by SMT has led to the development of new technologies and applications:
Advanced Component Packaging
SMT has enabled the development of advanced component packaging techniques, such as chip-scale packaging (CSP) and wafer-level packaging (WLP). These packaging methods allow for even smaller component sizes and higher integration levels, further pushing the boundaries of miniaturization and functionality.
Flexible and Rigid-Flex PCBs
SMT is well-suited for the assembly of flexible and rigid-flex PCBs, which are increasingly used in applications where space is limited, and conformity to irregular shapes is required. The small size and low profile of SMT components make them ideal for use on flexible substrates, enabling the development of new form factors and product designs.
High-Frequency Applications
The improved signal integrity and reduced parasitics associated with SMT make it the preferred choice for high-frequency applications, such as 5G telecommunications, automotive radar, and high-speed networking. SMT enables the design of high-performance circuits that can operate at higher frequencies and with greater reliability than THT assemblies.
Internet of Things (IoT)
The proliferation of IoT devices has been largely enabled by the advantages of SMT. The small size, low power consumption, and high functionality of SMT components are essential for the development of compact, wireless sensor nodes and other IoT devices. SMT has played a crucial role in making IoT a reality and will continue to drive innovation in this rapidly growing field.
Frequently Asked Questions (FAQ)
1. What is the difference between SMT and THT?
SMT (Surface Mount Technology) is a method of mounting electronic components directly onto the surface of a PCB, while THT (Through-Hole Technology) involves inserting component leads through drilled holes in the PCB and soldering them on the opposite side.
2. Can SMT and THT be used together on the same PCB?
Yes, SMT and THT can be used together on the same PCB in a process called mixed assembly. This is often done when certain components are not available in SMT packages or when through-hole mounting is required for mechanical strength.
3. What are the challenges associated with SMT?
Some challenges associated with SMT include the need for precise component placement, the potential for tombstoning (where small components stand up on one end due to uneven soldering), and the difficulty of manual rework and repair compared to THT.
4. Is SMT suitable for high-power applications?
Yes, SMT is suitable for high-power applications. The improved thermal management and heat dissipation characteristics of SMT components make them well-suited for use in power electronics and other high-power systems.
5. How has SMT contributed to the growth of the electronics industry?
SMT has contributed to the growth of the electronics industry by enabling the development of smaller, more functional, and more reliable electronic devices. The advantages of SMT have driven innovation in various fields, from consumer electronics to automotive systems and aerospace applications.
Conclusion
In conclusion, PCB SMT offers numerous advantages over traditional through-hole technology, including miniaturization, increased reliability, faster assembly, cost-effectiveness, and enhanced design flexibility. These advantages have made SMT the dominant assembly process in the electronics industry, driving innovation and enabling the development of new technologies and applications.
As electronic devices continue to become smaller, more complex, and more ubiquitous, the importance of SMT will only continue to grow. By understanding and leveraging the advantages of SMT, PCB designers and manufacturers can create products that are more compact, reliable, and cost-effective, ultimately benefiting end-users and driving the growth of the electronics industry as a whole.
No responses yet