Introduction to PCB Assembly
Printed Circuit Board (PCB) assembly is a crucial process in the manufacturing of electronic devices. It involves the placement and soldering of electronic components onto a PCB to create a functional circuit. There are two primary methods of PCB assembly: Through Hole (THT) and Surface Mount Technology (SMT). In this article, we will explore the ten key differences between these two assembly techniques.
What is Through Hole Assembly?
Through Hole Assembly, also known as THT (Through Hole Technology), is a traditional method of PCB assembly where component leads are inserted through drilled holes in the PCB and soldered onto the opposite side. This method has been used for decades and is still prevalent in certain applications.
Advantages of Through Hole Assembly
- Stronger mechanical bonds due to the leads passing through the board
- Easier to inspect and repair manually
- Better suited for high-power and high-voltage applications
- More tolerant of temperature fluctuations
Disadvantages of Through Hole Assembly
- Larger component size and board space requirements
- Slower assembly process compared to SMT
- Higher labor costs due to manual insertion and soldering
- Limited component density on the PCB
What is SMT Assembly?
Surface Mount Technology (SMT) Assembly is a modern method of PCB assembly where components are placed directly onto the surface of the PCB and soldered using a reflow oven. SMT has gained popularity due to its numerous advantages over through hole assembly.
Advantages of SMT Assembly
- Smaller component size and higher component density
- Faster assembly process using automated pick-and-place machines
- Lower labor costs due to automation
- Improved electrical performance due to shorter lead lengths
- Better suited for high-volume production
Disadvantages of SMT Assembly
- Higher initial setup costs for equipment and tooling
- More sensitive to temperature fluctuations during soldering
- Requires specialized training for operators and technicians
- More difficult to inspect and repair manually
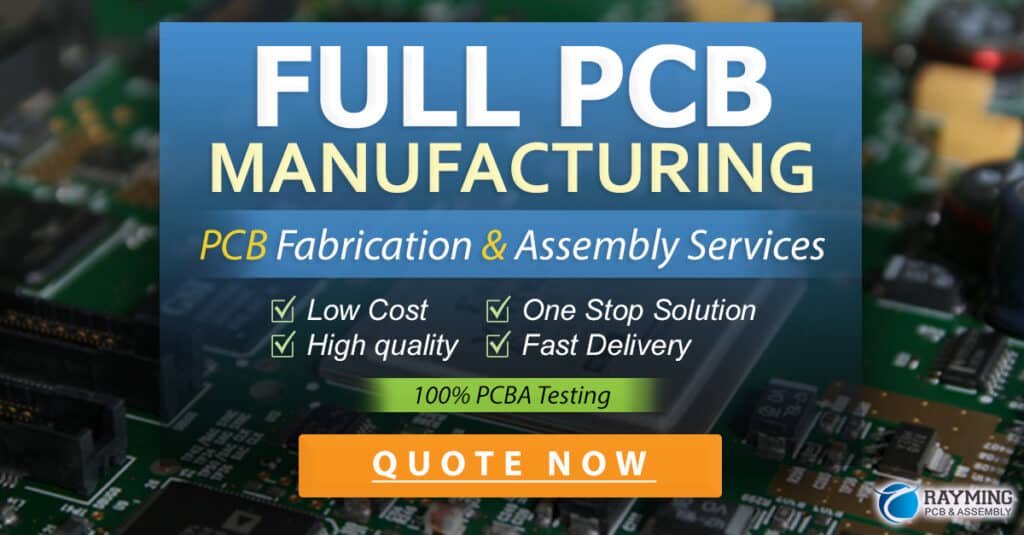
10 Key Differences Between Through Hole and SMT Assembly
1. Component Size and Density
One of the most significant differences between through hole and SMT assembly is the size of the components and the density at which they can be placed on the PCB.
Assembly Method | Component Size | Component Density |
---|---|---|
Through Hole | Larger | Lower |
SMT | Smaller | Higher |
SMT components are much smaller than their through hole counterparts, allowing for higher component density on the PCB. This enables the design of more compact and lightweight electronic devices.
2. Board Space Utilization
The way components are mounted on the PCB directly affects the amount of board space required.
Assembly Method | Board Space Utilization |
---|---|
Through Hole | Less efficient |
SMT | More efficient |
Through hole components require drilled holes and additional space for lead bending and soldering, resulting in less efficient board space utilization. SMT components, on the other hand, are placed directly onto the surface of the PCB, allowing for more efficient use of board space.
3. Assembly Speed
The speed at which PCBs can be assembled is a critical factor in determining production efficiency and cost.
Assembly Method | Assembly Speed |
---|---|
Through Hole | Slower |
SMT | Faster |
SMT assembly is significantly faster than through hole assembly due to the use of automated pick-and-place machines. These machines can place hundreds of components per minute, greatly reducing the overall assembly time.
4. Labor Costs
The amount of manual labor required for each assembly method directly impacts the associated labor costs.
Assembly Method | Labor Costs |
---|---|
Through Hole | Higher |
SMT | Lower |
Through hole assembly requires more manual labor for component insertion and soldering, resulting in higher labor costs. SMT assembly, being largely automated, requires less manual labor and thus has lower associated labor costs.
5. Equipment and Tooling Costs
The initial investment in equipment and tooling differs between through hole and SMT assembly.
Assembly Method | Equipment and Tooling Costs |
---|---|
Through Hole | Lower |
SMT | Higher |
SMT assembly requires more advanced and expensive equipment, such as pick-and-place machines and reflow ovens, resulting in higher initial setup costs. Through hole assembly, being more manual, requires less expensive equipment and tooling.
6. Electrical Performance
The electrical performance of the assembled PCB can be affected by the choice of assembly method.
Assembly Method | Electrical Performance |
---|---|
Through Hole | Good |
SMT | Better |
SMT components have shorter lead lengths, which reduces parasitic inductance and capacitance, resulting in better electrical performance compared to through hole components.
7. Mechanical Strength
The mechanical strength of the solder joints and component attachments varies between through hole and SMT assembly.
Assembly Method | Mechanical Strength |
---|---|
Through Hole | Stronger |
SMT | Weaker |
Through hole components have leads that pass through the PCB and are soldered on the opposite side, creating stronger mechanical bonds. SMT components, being soldered only on the surface, have weaker mechanical strength.
8. Temperature Sensitivity
The sensitivity to temperature fluctuations during the soldering process differs between through hole and SMT assembly.
Assembly Method | Temperature Sensitivity |
---|---|
Through Hole | More tolerant |
SMT | More sensitive |
SMT components are more sensitive to temperature fluctuations during the reflow soldering process, as the entire PCB is subjected to high temperatures. Through hole components are more tolerant of temperature fluctuations, as the soldering is performed on a point-to-point basis.
9. Inspection and Repair
The ease of inspection and repair varies between through hole and SMT assembled PCBs.
Assembly Method | Inspection and Repair |
---|---|
Through Hole | Easier |
SMT | More difficult |
Through hole assembled PCBs are easier to inspect and repair manually, as the components and solder joints are more accessible. SMT assembled PCBs, with their smaller components and more complex layouts, are more difficult to inspect and repair manually.
10. Application Suitability
The choice between through hole and SMT assembly often depends on the specific requirements of the application.
Assembly Method | Application Suitability |
---|---|
Through Hole | High-power, high-voltage, and high-reliability applications |
SMT | High-volume, compact, and lightweight applications |
Through hole assembly is better suited for applications that require high power, high voltage, or high reliability, such as automotive and aerospace electronics. SMT assembly is more suitable for high-volume production of compact and lightweight devices, such as smartphones and wearables.
Frequently Asked Questions (FAQ)
1. Can through hole and SMT components be used together on the same PCB?
Yes, it is possible to use both through hole and SMT components on the same PCB. This is called a mixed assembly or hybrid assembly. Mixed assemblies are common in situations where certain components are not available in SMT packages or when specific design requirements necessitate the use of through hole components.
2. Is it possible to convert a through hole PCB design to SMT?
In most cases, it is possible to convert a through hole PCB design to SMT. However, this process may require modifications to the PCB layout, component selection, and manufacturing processes. It is essential to consider factors such as component availability, board space, and assembly equipment when converting a design from through hole to SMT.
3. Which assembly method is more cost-effective for low-volume production?
For low-volume production, through hole assembly is generally more cost-effective. This is because SMT assembly requires higher initial setup costs for equipment and tooling, which can be prohibitive for low-volume runs. Through hole assembly, being more manual and requiring less expensive equipment, is better suited for low-volume production.
4. Are SMT components more expensive than through hole components?
In general, SMT components are less expensive than their through hole counterparts. This is due to the smaller size and higher production volumes of SMT components. However, the cost difference may vary depending on the specific component and its availability in different package types.
5. Can SMT assembled PCBs be repaired manually?
While it is possible to repair SMT assembled PCBs manually, it is more challenging than repairing through hole assembled PCBs. SMT components are smaller and more closely spaced, making manual soldering and desoldering more difficult. Specialized tools, such as tweezers, magnifying lenses, and hot air soldering stations, may be required for effective manual repair of SMT assembled PCBs.
Conclusion
Through hole and SMT assembly are two distinct methods of PCB assembly, each with its own advantages and disadvantages. The choice between these two methods depends on various factors, such as component size, board space, assembly speed, labor costs, electrical performance, and application requirements.
Understanding the key differences between through hole and SMT assembly is crucial for electronics designers, manufacturers, and engineers to make informed decisions when developing and producing PCBs. By considering the specific needs of the project and weighing the pros and cons of each assembly method, it is possible to optimize the PCB design and manufacturing process for the best possible outcome.
No responses yet