What is Copper Thickness in PCBs?
Copper thickness refers to the thickness of the copper layer deposited on the PCB substrate. The copper layer is responsible for carrying electrical signals and providing a conductive path for current flow. The thickness of the copper layer is typically measured in ounces per square foot (oz/ft²) or microns (µm).
Common copper thicknesses used in PCB Manufacturing include:
– 0.5 oz/ft² (17.5 µm)
– 1 oz/ft² (35 µm)
– 2 oz/ft² (70 µm)
– 3 oz/ft² (105 µm)
– 4 oz/ft² (140 µm)
Importance of Copper Thickness in PCBs
The copper thickness plays a vital role in the performance and reliability of a PCB. Some of the key reasons why copper thickness is important include:
-
Current Carrying Capacity: Thicker copper layers can carry more current without overheating or experiencing voltage drops. This is particularly important for power-hungry applications or high-current circuits.
-
Signal Integrity: Copper thickness affects the impedance of the traces on the PCB. Consistent copper thickness is essential for maintaining the desired impedance and minimizing signal integrity issues, such as reflections and crosstalk.
-
Thermal Management: Thicker copper layers have better Thermal Conductivity, which helps dissipate heat generated by components on the PCB. This can prevent overheating and improve the overall reliability of the PCB.
-
Mechanical Strength: Copper thickness contributes to the mechanical strength of the PCB. Thicker copper layers can provide better support for heavy components and improve the overall durability of the PCB.
Factors Affecting Copper Thickness Tolerances
Several factors can influence the copper thickness tolerances during the PCB manufacturing process. Understanding these factors can help designers and manufacturers minimize variations and ensure consistent copper thickness across the board.
-
Plating Process: The copper plating process used during PCB manufacturing can impact the thickness tolerances. Different plating methods, such as electroplating or electroless plating, have varying levels of control over the copper thickness distribution.
-
Board Size: Larger PCBs may experience greater variations in copper thickness compared to smaller boards. This is due to the increased distance the plating solution needs to travel and the potential for uneven current distribution during the plating process.
-
Copper Foil Type: The type of copper foil used as the starting material for the PCB can affect the thickness tolerances. Some copper foils have tighter thickness tolerances than others, which can result in more consistent copper thickness on the final PCB.
-
Etching Process: The etching process used to remove unwanted copper from the PCB can also impact the thickness tolerances. Over-etching or under-etching can lead to variations in the final copper thickness.
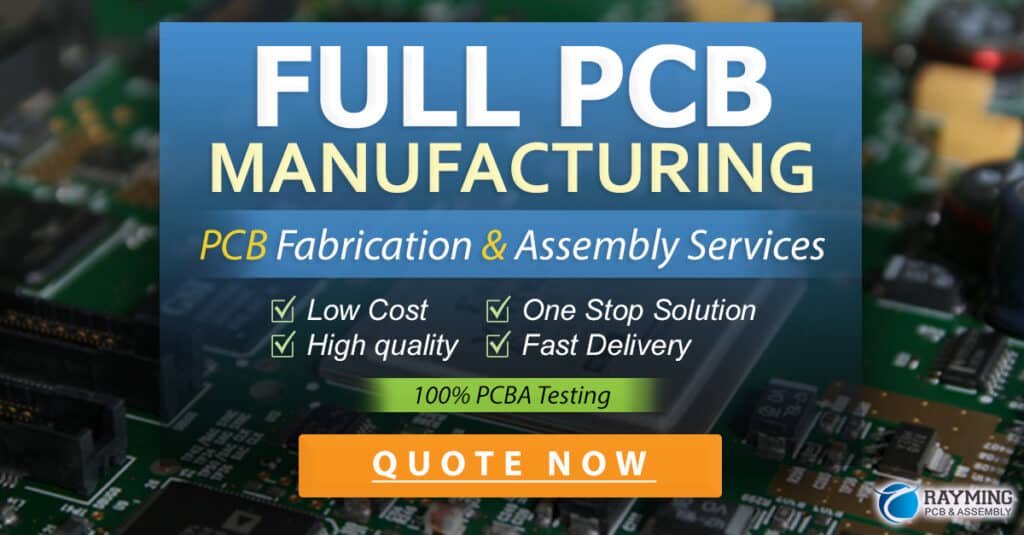
Industry Standards for Copper Thickness Tolerances
To ensure consistency and reliability in PCB manufacturing, industry standards have been established for copper thickness tolerances. The two most widely recognized standards are:
-
IPC-6012: This standard, developed by the Association Connecting Electronics Industries (IPC), specifies the requirements for the qualification and performance of rigid printed boards. It defines the copper thickness tolerances for various classes of PCBs.
-
IPC-6013: This standard focuses on the qualification and performance of flexible and rigid-flex printed boards. It outlines the copper thickness tolerances specific to flexible and Rigid-Flex PCBs.
The copper thickness tolerances specified in these standards vary depending on the copper weight and the class of the PCB. Here is a table summarizing the typical copper thickness tolerances according to IPC-6012 for Class 2 (general electronic products) and Class 3 (high-reliability electronic products) PCBs:
Copper Weight (oz/ft²) | Class 2 Tolerance | Class 3 Tolerance |
---|---|---|
0.5 | ±20% | ±10% |
1 | ±10% | ±10% |
2 | ±10% | ±7% |
3 | ±10% | ±7% |
4 | ±10% | ±5% |
It is important to note that these tolerances are general guidelines, and specific PCB designs or applications may require tighter tolerances. Designers should consult with their PCB Manufacturer to determine the achievable copper thickness tolerances for their specific project.
Designing PCBs with Copper Thickness Tolerances in Mind
When designing PCBs, it is essential to consider the copper thickness tolerances to ensure the design is manufacturable and meets the required performance criteria. Here are some tips for designing PCBs with copper thickness tolerances in mind:
-
Choose the Appropriate Copper Weight: Select the copper weight that best suits your application’s requirements for current carrying capacity, signal integrity, and thermal management. Keep in mind that thicker copper layers may have tighter tolerances, but they also increase the overall cost of the PCB.
-
Use Consistent Copper Thickness: Maintain consistent copper thickness throughout the PCB design to minimize variations in impedance and signal integrity. Avoid sudden changes in copper thickness, as they can lead to manufacturing challenges and potential reliability issues.
-
Consider the Manufacturer’s Capabilities: Consult with your PCB manufacturer early in the design process to understand their capabilities and limitations regarding copper thickness tolerances. Some manufacturers may have better control over the plating process or use higher-quality copper foils, resulting in tighter tolerances.
-
Incorporate Design for Manufacturing (DFM) Principles: Follow DFM guidelines to ensure your PCB design is optimized for manufacturability. This includes adhering to recommended trace widths and spacing, avoiding sharp corners or angles, and providing adequate clearances between copper features.
-
Perform Tolerance Analysis: Conduct a tolerance analysis on your PCB design to identify potential areas where copper thickness variations may impact performance or reliability. This analysis can help you make informed decisions about adjusting your design or specifying tighter tolerances in critical areas.
Testing and Verification of Copper Thickness
To ensure the copper thickness on a manufactured PCB meets the specified tolerances, various testing and verification methods can be employed. Some common methods include:
-
Cross-Sectional Analysis: This destructive testing method involves cutting a sample of the PCB and examining the cross-section under a microscope. The copper thickness can be measured directly from the cross-section image.
-
X-Ray Fluorescence (XRF) Spectroscopy: XRF is a non-destructive testing method that uses X-rays to measure the thickness of the copper layer. It provides accurate and precise measurements without damaging the PCB.
-
Electrical Resistance Testing: This method involves measuring the electrical resistance of the copper traces on the PCB. The resistance value can be correlated to the copper thickness using known material properties and trace geometry.
-
Micro-Sectioning: Similar to cross-sectional analysis, micro-sectioning involves cutting a small sample of the PCB and examining it under a microscope. This method allows for a more detailed examination of the copper thickness and the plating quality.
Regular testing and verification of copper thickness help ensure the consistency and reliability of the manufactured PCBs. It is important to work closely with your PCB manufacturer to establish an appropriate testing and verification plan that meets your specific requirements.
FAQ
-
What is the most common copper thickness used in PCBs?
The most common copper thickness used in PCBs is 1 oz/ft² (35 µm). This thickness provides a good balance between current carrying capacity, signal integrity, and cost. -
Can I use different copper thicknesses on the same PCB?
Yes, it is possible to use different copper thicknesses on the same PCB. This is often done to optimize the design for specific requirements, such as using thicker copper for power planes and thinner copper for signal traces. However, it is important to consider the manufacturing implications and ensure proper communication with your PCB manufacturer. -
How does copper thickness affect the impedance of PCB traces?
Copper thickness is one of the factors that influence the impedance of PCB traces. Thicker copper layers result in lower impedance, while thinner copper layers result in higher impedance. It is important to control the copper thickness to maintain the desired impedance and ensure proper signal integrity. -
What happens if the copper thickness is out of tolerance?
If the copper thickness is out of tolerance, it can lead to various issues, such as: - Deviation from the designed impedance, leading to signal integrity problems
- Inadequate current carrying capacity, causing overheating or voltage drops
- Reduced mechanical strength, making the PCB more susceptible to damage
- Inconsistent etching, resulting in unintended trace widths or shorts/opens
To mitigate these issues, it is crucial to work with a reliable PCB manufacturer that can maintain tight copper thickness tolerances and implement appropriate quality control measures.
- How can I ensure my PCB design is within the copper thickness tolerances?
To ensure your PCB design is within the copper thickness tolerances, follow these steps: - Choose the appropriate copper weight based on your application’s requirements
- Use consistent copper thickness throughout the design
- Follow the manufacturer’s guidelines and capabilities
- Incorporate DFM principles to optimize the design for manufacturability
- Perform a tolerance analysis to identify and address potential issues
- Communicate clearly with your PCB manufacturer and provide them with comprehensive design files and specifications
By understanding and considering copper thickness tolerances throughout the PCB design and manufacturing process, you can ensure the production of high-quality, reliable PCBs that meet your application’s requirements.
Conclusion
Copper thickness tolerances play a crucial role in the performance, reliability, and manufacturability of PCBs. Understanding the factors that affect copper thickness, industry standards, and design considerations is essential for creating robust PCB designs. By working closely with your PCB manufacturer, implementing appropriate testing and verification methods, and following best practices for PCB design, you can ensure your PCBs meet the specified copper thickness tolerances and perform optimally in their intended applications.
No responses yet