What are PCB Manufacturing Tolerances?
PCB manufacturing tolerances are the acceptable ranges of variation in the physical dimensions, material properties, and manufacturing processes of a PCB. These tolerances are inevitable due to the limitations of manufacturing equipment, materials, and processes. Some common PCB tolerances include:
- Board dimensions (length, width, thickness)
- Hole sizes and positions
- Copper trace width and spacing
- Solder mask and silkscreen registration
- Material properties (dielectric constant, dissipation factor)
Designers must take these tolerances into account when creating PCB Layouts to ensure that the final product will meet the desired specifications and function properly.
Why are PCB Tolerances Important?
PCB tolerances are essential for several reasons:
-
Functionality: PCBs must be manufactured within specified tolerances to ensure proper functionality. Variations in trace width, spacing, or hole sizes can affect Signal Integrity, impedance matching, and component placement, potentially leading to malfunctions or failures.
-
Compatibility: PCBs often need to interface with other components or systems. Manufacturing tolerances ensure that the PCB will fit and function correctly within the larger assembly.
-
Reliability: Adhering to manufacturing tolerances helps maintain the reliability of the PCB over its intended lifespan. Deviations from the specified tolerances can lead to increased stress on components, reduced performance, or premature failure.
-
Cost: Tighter tolerances generally require more advanced manufacturing processes and quality control measures, which can increase production costs. By specifying appropriate tolerances based on the application requirements, designers can optimize the balance between performance and cost.
Common PCB Manufacturing Tolerances
Board Dimensions
The overall dimensions of a PCB, including its length, width, and thickness, are subject to manufacturing tolerances. These tolerances depend on factors such as the board material, layer count, and manufacturing process. Typical board dimension tolerances are:
Dimension | Tolerance |
---|---|
Length/Width | ±0.005 in (0.13 mm) |
Thickness | ±10% |
Hole Sizes and Positions
Drilled holes on a PCB, used for component leads, vias, and mounting, have tolerances for both their diameter and position. The hole size tolerance depends on the drill bit size and the material being drilled, while the position tolerance is affected by factors such as the drilling equipment and the artwork registration. Common hole tolerances are:
Hole Type | Diameter Tolerance | Position Tolerance |
---|---|---|
Component Holes | ±0.003 in (0.08 mm) | ±0.004 in (0.10 mm) |
Vias | ±0.002 in (0.05 mm) | ±0.003 in (0.08 mm) |
Copper Trace Width and Spacing
The width of copper traces and the spacing between them are critical for maintaining signal integrity and preventing short circuits. These dimensions are limited by the capabilities of the PCB Fabrication process, such as the minimum trace width and spacing that can be reliably etched. Typical trace width and spacing tolerances are:
Dimension | Tolerance |
---|---|
Trace Width | ±0.002 in (0.05 mm) |
Trace Spacing | ±0.002 in (0.05 mm) |
Solder Mask and Silkscreen Registration
Solder mask and silkscreen layers are subject to registration tolerances, which refer to the alignment of these layers with respect to the copper features on the PCB. Misregistration can lead to issues such as exposed copper, solder bridging, or inaccurate component placement. Common solder mask and silkscreen registration tolerances are:
Layer | Registration Tolerance |
---|---|
Solder Mask | ±0.005 in (0.13 mm) |
Silkscreen | ±0.010 in (0.25 mm) |
Material Properties
The electrical and mechanical properties of the PCB materials, such as the dielectric constant and dissipation factor of the substrate or the thickness and conductivity of the copper, can vary within certain tolerances. These variations can affect the performance of the PCB, particularly at high frequencies or in demanding environmental conditions. Material property tolerances are typically specified by the material manufacturer and should be accounted for in the PCB design.
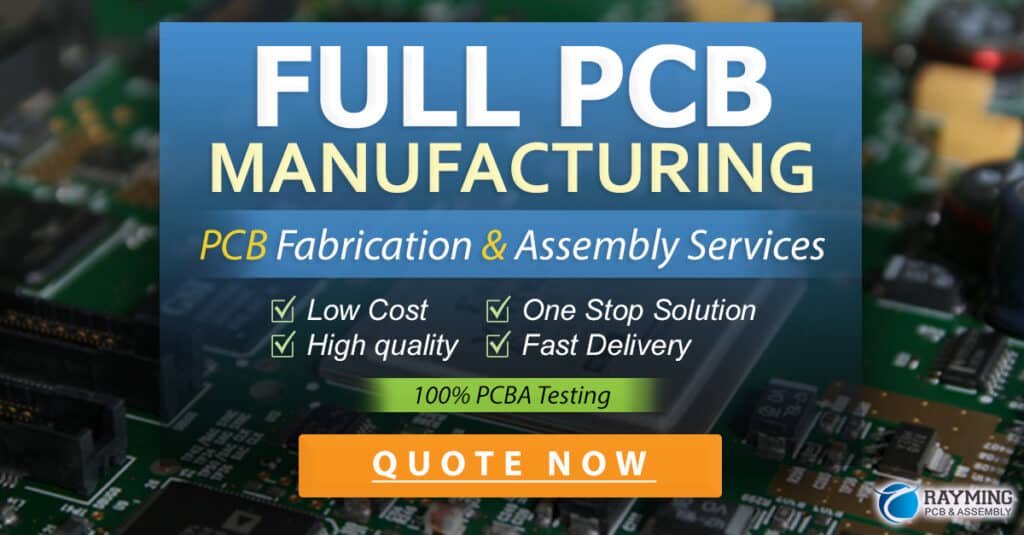
Designing with PCB Tolerances in Mind
To ensure that a PCB will function as intended and meet the required quality standards, designers must consider manufacturing tolerances throughout the design process:
-
Design Rules: Establish and adhere to design rules that specify minimum trace widths, spacings, hole sizes, and other critical dimensions based on the capabilities of the intended manufacturing process and the tolerance requirements of the application.
-
Layout Techniques: Use layout techniques that minimize the impact of manufacturing tolerances, such as avoiding long parallel traces, providing sufficient clearance around holes and components, and using symmetrical or self-compensating designs where possible.
-
Tolerance Analysis: Perform tolerance analysis to determine the worst-case scenarios for critical dimensions and ensure that the design will still function correctly under those conditions. This may involve using simulation tools or statistical methods to assess the impact of tolerances on signal integrity, impedance, or other performance parameters.
-
Communication with Manufacturers: Clearly communicate the tolerance requirements to the PCB manufacturer and discuss any potential issues or limitations. Work with the manufacturer to select appropriate materials, processes, and quality control measures to meet the specified tolerances.
FAQ
1. What are the most critical PCB tolerances to consider?
The most critical PCB tolerances depend on the specific application and design requirements, but generally include:
- Trace width and spacing, which affect signal integrity and impedance
- Hole sizes and positions, which impact component placement and reliability
- Board dimensions, which determine the fit and compatibility with other components or systems
2. How can I ensure that my PCB design meets the required tolerances?
To ensure that your PCB design meets the required tolerances:
- Establish and follow design rules based on the manufacturing capabilities and application requirements
- Use layout techniques that minimize the impact of tolerances, such as providing adequate clearances and using symmetrical designs
- Perform tolerance analysis to assess the worst-case scenarios and verify that the design will still function correctly
- Communicate clearly with the PCB manufacturer and select appropriate materials and processes
3. What happens if a PCB is manufactured outside the specified tolerances?
If a PCB is manufactured outside the specified tolerances, it may experience issues such as:
- Malfunctions or failures due to signal integrity problems, short circuits, or component misalignment
- Reduced reliability or premature failure due to increased stress on components or materials
- Incompatibility with other components or systems, leading to assembly or integration issues
In some cases, PCBs that are outside the tolerances may need to be reworked or scrapped, increasing production costs and delays.
4. Can I request tighter tolerances for my PCB?
Yes, you can request tighter tolerances for your PCB, but keep in mind that this may increase production costs and lead times. Tighter tolerances often require more advanced manufacturing processes, materials, and quality control measures. It’s essential to balance the tolerance requirements with the cost and schedule constraints of your project and to discuss the feasibility of tighter tolerances with your PCB manufacturer.
5. How do PCB manufacturing tolerances compare to other industries?
PCB manufacturing tolerances are generally tighter than those in many other industries, such as mechanical engineering or construction, due to the small scale and high precision required for electronic components and circuits. However, the specific tolerances achievable in PCB manufacturing depend on the materials, processes, and equipment used, as well as the complexity and requirements of the design. As technology advances, PCB manufacturers are continually improving their capabilities to produce boards with tighter tolerances and finer features.
Conclusion
Understanding and managing manufacturing tolerances is essential for designing and producing high-quality, reliable PCBs. By considering tolerances throughout the design process, from establishing design rules to performing tolerance analysis and communicating with manufacturers, designers can ensure that their PCBs will function as intended and meet the required quality standards. While tighter tolerances may be necessary for some applications, it’s important to balance the tolerance requirements with the cost and feasibility constraints of the project. As PCB manufacturing technologies continue to advance, designers will have even greater opportunities to push the boundaries of what’s possible while still maintaining the necessary tolerances for their designs.
No responses yet