What is PCB Solder Mask Opening (SMO)?
PCB Solder Mask Opening, often abbreviated as SMO, refers to the openings or exposed areas on a printed circuit board (PCB) where the solder mask layer is removed to allow for soldering of components. The solder mask is a thin lacquer-like layer applied to the copper traces of a PCB. It serves as an insulating and protective layer, preventing solder bridges and accidental short circuits.
SMOs are strategically placed on a PCB to expose the copper pads where components will be soldered. The size, shape, and location of the SMOs are crucial for ensuring proper soldering and functionality of the PCB Assembly.
Key Functions of Solder Mask Openings
-
Solderability: SMOs expose the copper pads, allowing solder to adhere and create a strong electrical and mechanical connection between components and the PCB.
-
Insulation: The solder mask layer surrounding the SMOs acts as an insulator, preventing solder bridging and short circuits between adjacent pads or traces.
-
Protection: SMOs help protect the exposed copper from oxidation, contamination, and damage during the assembly process and throughout the life of the PCB.
Types of Solder Mask Openings
There are several types of solder mask openings used in PCB design, each serving specific purposes and accommodating different component packages.
1. Non-Solder Mask Defined (NSMD) Pads
NSMD pads are the most common type of SMO. In this design, the copper pad is larger than the solder mask opening, exposing a portion of the copper around the perimeter of the SMO. This allows for some tolerance in the solder mask alignment and helps ensure a good solder joint.
Advantage | Disadvantage |
---|---|
Allows for solder mask misalignment | Slightly less precise than SMD pads |
Provides good solder joint strength | May require larger pad sizes |
2. Solder Mask Defined (SMD) Pads
SMD pads have solder mask openings that are the same size or slightly smaller than the copper pads. This results in the solder mask defining the exact location and size of the solderable area. SMD pads offer more precision but require tighter tolerances in the solder mask alignment process.
Advantage | Disadvantage |
---|---|
Precise solderable area definition | Requires tighter solder mask alignment tolerances |
Allows for smaller pad sizes | Less forgiving of misalignment |
3. Via Solder Mask Openings
Via SMOs are used to expose the copper plating inside via holes, allowing for soldering of through-hole components or creating conductive paths between PCB Layers. The solder mask opening around a via is typically larger than the via diameter to ensure proper solder wicking and coverage.
Advantage | Disadvantage |
---|---|
Allows soldering of through-hole components | Consumes more PCB real estate |
Creates conductive paths between layers | Requires additional processing steps |
Designing Solder Mask Openings
When designing solder mask openings for a PCB, several factors must be considered to ensure optimal performance and manufacturability.
1. Solder Mask Opening Size
The size of the SMO depends on the component package, pad size, and the desired amount of exposed copper. A general rule of thumb is to have the SMO slightly larger than the copper pad to allow for some solder mask misalignment.
For example, a typical SMO for a surface-mount resistor or capacitor might be 0.1 mm larger than the copper pad on all sides. This means that for a 1.0 mm x 0.5 mm pad, the SMO would be 1.2 mm x 0.7 mm.
Component Package | Typical Pad Size (mm) | Recommended SMO Size (mm) |
---|---|---|
0201 | 0.25 x 0.125 | 0.45 x 0.325 |
0402 | 0.5 x 0.25 | 0.7 x 0.45 |
0603 | 0.8 x 0.4 | 1.0 x 0.6 |
0805 | 1.0 x 0.5 | 1.2 x 0.7 |
1206 | 1.6 x 0.8 | 1.8 x 1.0 |
2. Solder Mask Clearance
Solder mask clearance refers to the distance between the edge of the copper pad and the edge of the solder mask opening. Adequate clearance is necessary to prevent solder bridging and ensure proper insulation between adjacent pads.
The minimum solder mask clearance depends on the PCB manufacturer’s capabilities and the solder mask material used. Typically, a clearance of 0.1 mm to 0.15 mm is sufficient for most PCB designs.
Solder Mask Material | Minimum Clearance (mm) |
---|---|
Liquid Photoimageable (LPI) | 0.1 |
Dry Film | 0.15 |
3. Solder Mask Sliver
A solder mask sliver is a thin strip of solder mask between two adjacent SMOs. If the sliver is too thin, it may break off during the solder mask application process or during soldering, leading to solder bridges.
To prevent this, maintain a minimum solder mask sliver width of 0.15 mm to 0.2 mm between SMOs. This ensures the integrity of the solder mask layer and helps prevent solder bridging.
4. Solder Mask Registration
Solder mask registration refers to the alignment accuracy of the solder mask layer relative to the copper layer. Misalignment can result in exposed copper where it should be covered, or solder mask covering areas that should be exposed.
To accommodate for potential misalignment, designers should incorporate solder mask expansion or contraction into their SMO designs. This involves slightly oversizing or undersizing the SMOs relative to the copper pads, depending on the type of pads used (NSMD or SMD).
Pad Type | Solder Mask Expansion/Contraction |
---|---|
NSMD | Expansion (0.05 mm to 0.1 mm) |
SMD | Contraction (0.025 mm to 0.05 mm) |
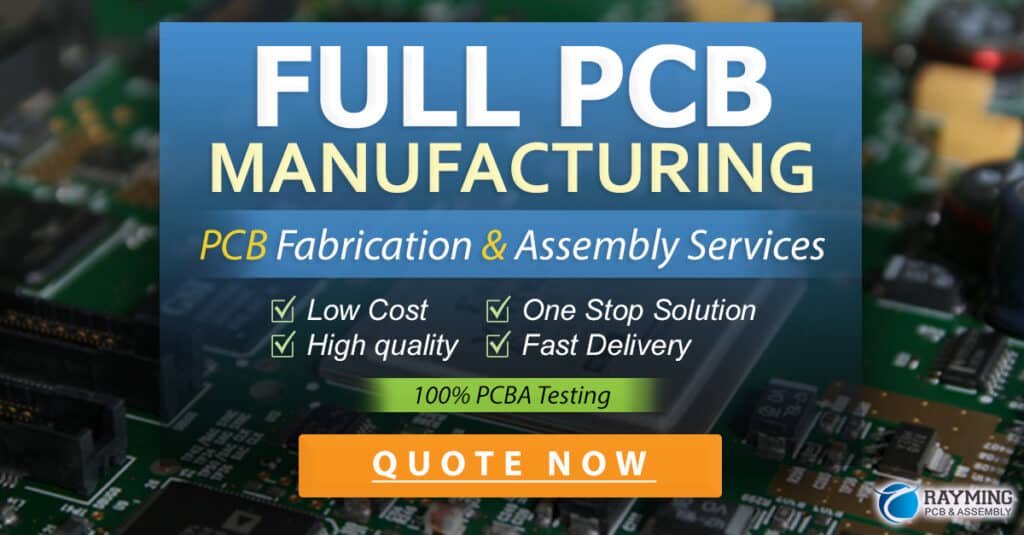
Solder Mask Opening Design Tips
To optimize your PCB solder mask opening designs, consider the following tips:
- Use NSMD pads whenever possible for better solder mask alignment tolerance and improved solder joint strength.
- Maintain consistent SMO sizes for similar component packages to ensure uniform soldering results.
- Adhere to the minimum solder mask clearance and sliver width guidelines to prevent solder bridging and ensure solder mask integrity.
- Incorporate solder mask expansion or contraction based on the pad type to account for potential misalignment.
- Communicate your SMO requirements clearly with your PCB manufacturer, including any specific tolerances or design constraints.
FAQ
1. What is the difference between NSMD and SMD pads?
NSMD (Non-Solder Mask Defined) pads have copper pads larger than the solder mask opening, exposing a portion of the copper around the perimeter. SMD (Solder Mask Defined) pads have solder mask openings the same size or slightly smaller than the copper pads, with the solder mask defining the solderable area.
2. How do I determine the appropriate solder mask opening size for a component?
The SMO size depends on the component package, pad size, and desired exposed copper. A general rule is to have the SMO slightly larger than the copper pad, typically 0.1 mm larger on all sides, to allow for solder mask misalignment.
3. What is the minimum solder mask clearance, and why is it important?
The minimum solder mask clearance is the distance between the edge of the copper pad and the edge of the solder mask opening. It is typically 0.1 mm to 0.15 mm, depending on the solder mask material. Adequate clearance prevents solder bridging and ensures proper insulation between adjacent pads.
4. What is a solder mask sliver, and what is the recommended minimum width?
A solder mask sliver is a thin strip of solder mask between two adjacent SMOs. To prevent the sliver from breaking off during solder mask application or soldering, maintain a minimum width of 0.15 mm to 0.2 mm between SMOs.
5. How can I account for potential solder mask misalignment in my PCB design?
To accommodate potential solder mask misalignment, incorporate solder mask expansion or contraction into your SMO designs. For NSMD pads, expand the SMO by 0.05 mm to 0.1 mm relative to the copper pad. For SMD pads, contract the SMO by 0.025 mm to 0.05 mm.
No responses yet