Plastic BGA (PBGA) Packages
Plastic BGA packages are the most widely used type of BGA. They have a plastIC Substrate and encapsulate the die and wire bonds in a plastic resin compound. PBGAs offer a good balance of performance, cost, and reliability.
Key characteristics of PBGA packages include:
- Low cost compared to ceramic BGAs
- Lighter weight than ceramic
- Not hermetically sealed
- Typical ball pitch of 0.5mm, 0.8mm, 1.0mm or 1.27mm
- Ball counts ranging from 100 to over 1000
Fine-Pitch Ball Grid Array (FBGA)
FBGA is a plastic BGA package with a ball pitch of 1.0mm or less, typically 0.8mm, 0.75mm, or 0.5mm. The finer ball pitch allows for higher pin counts in a smaller package size compared to standard PBGA.
Low-Profile Fine-Pitch BGA (LFBGA)
LFBGA is a thinner version of the standard FBGA package. It has the same ball pitch options but a lower profile, with a typical package thickness of 0.9-1.7mm. The reduced height makes LFBGA ideal for slim devices like smartphones.
Very-Very Thin Profile FBGA (VFBGA)
VFBGA takes the concept of low-profile packaging even further, with a package height of just 0.5-0.8mm. This extremely thin profile is well-suited for ultra-slim consumer electronics.
Ceramic BGA Packages
Ceramic BGA packages have a ceramic substrate rather than plastic. They provide superior thermal performance and reliability compared to plastic BGAs. The trade-offs are higher cost and weight.
Types of ceramic BGA packages include:
Ceramic Column Grid Array (CCGA)
CCGA packages use cylindrical columns of high-temperature solder instead of balls to connect the package to the PCB. The columns are non-collapsible, which makes CCGA more resistant to thermal stress than ball grid arrays. CCGA is often used for high-reliability applications like supercomputers and aerospace systems.
Ceramic Ball Grid Array (CBGA)
CBGA is similar to plastic BGA but with a ceramic substrate. The ceramic material provides better CTE matching to PCB Materials, improved thermal conductivity, and lower moisture absorption compared to plastic. CBGA packages are hermetically sealed. Typical applications include military, medical, and RF devices.
Package-on-Package (PoP)
Package-on-Package refers to vertically stacking multiple BGA packages on top of each other. This 3D packaging technique allows for greater functionality and component density in a small footprint.
PoP types include:
Through Mold Via Package-on-Package (TMV-PoP)
In TMV-PoP, the bottom package has through mold vias that enable the top package to be connected to the PCB. This provides a direct signal path from the top package to the board, reducing inductance compared to perimeter connections used in other PoP types.
Moulded Laser Package-on-Package (MLP-PoP)
MLP-PoP uses a laser drilling process to create micro vias in the mold compound of the bottom package. The top package is then mounted and connected to the bottom package through these laser-drilled vias. MLP-PoP accommodates finer pitch than TMV-PoP.
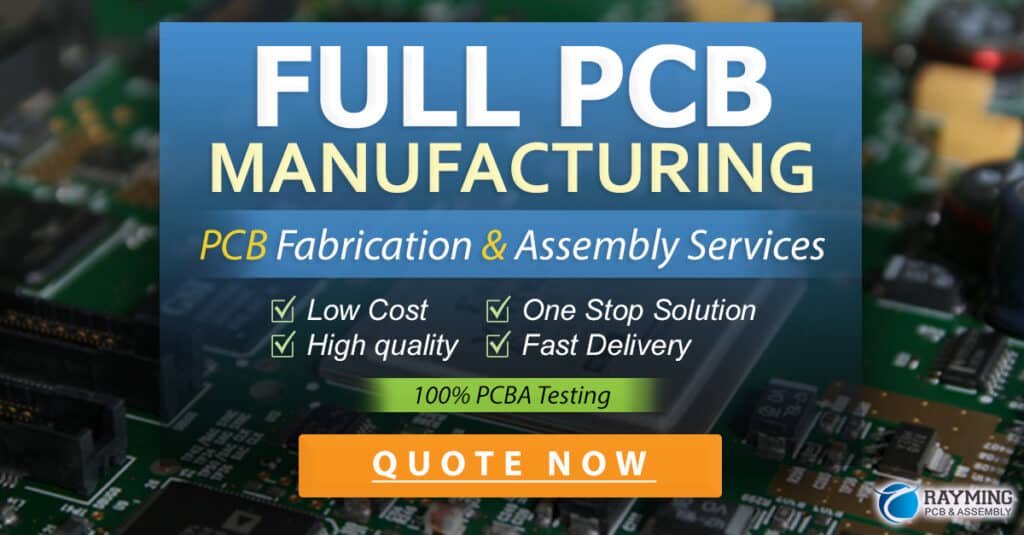
System-in-Package (SiP)
System-in-Package refers to packaging multiple die into a single package. The dies can be stacked vertically, placed side-by-side, or both. SiP allows heterogenous integration, i.e. combining different types of die like processors, memory, sensors, etc. into one highly integrated package.
Land Grid Array (LGA)
Land Grid Array packages are similar to BGA but use pads (lands) on the bottom of the package instead of balls. The lands connect to pads on the PCB. LGA requires a socket or spring-loaded mechanism to hold the package in compression against the board and maintain contact. LGA is commonly used for processors in mobile devices.
Lead-Free BGAs
Historically, the solder balls used in BGA packages contained lead. However, with the RoHS directive restricting hazardous substances, lead-free BGA packages have become the norm. SAC305 and SAC405 are common Lead-Free Solder alloys used for BGA balls, comprised of tin (Sn), silver (Ag) and copper (Cu).
Comparison of BGA Types
The table below summarizes the key characteristics of the major BGA package types:
Package Type | Substrate Material | Ball Pitch | Package Height | Hermetically Sealed | Relative Cost |
---|---|---|---|---|---|
PBGA | Plastic | 0.5-1.27mm | 1.7mm+ | No | Low |
FBGA | Plastic | 0.5-1.0mm | 1.7mm+ | No | Low-Medium |
LFBGA | Plastic | 0.5-1.0mm | 0.9-1.7mm | No | Low-Medium |
VFBGA | Plastic | 0.4-0.5mm | 0.5-0.8mm | No | Medium |
CBGA | Ceramic | 1.27mm | 2.5mm+ | Yes | High |
CCGA | Ceramic | 1.27mm | 2.5mm+ | Yes | High |
Choosing the Right BGA Package
With the wide variety of BGA package types available, selecting the most appropriate one depends on the specific requirements of the application. Key factors to consider include:
- Required I/O count and density
- Footprint and height constraints
- Thermal performance needs
- Environment and reliability requirements
- Signal integrity
- Cost target
In general, plastic BGAs like PBGA and FBGA are the most cost-effective and are suitable for many commercial and consumer applications. Low-profile versions like LFBGA and VFBGA are used where device slimness is a priority.
Ceramic BGAs provide the highest reliability and best thermal and signal integrity performance, but at an increased cost. They are used in harsh environments and high-performance applications.
PoP and SiP BGAs enable high levels of integration and functionality in the smallest form factor, making them ideal for mobile and handheld devices.
Frequently Asked Questions
Q1: What does BGA stand for?
A1: BGA stands for Ball Grid Array. It refers to a surface-mount package that uses a grid of solder balls on the bottom side for external electrical connections.
Q2: What are the advantages of BGA packages?
A2: BGA packages offer several advantages:
– High I/O density due to the array of contacts
– Smaller footprint compared to leaded packages
– Lower inductance and better electrical performance
– Good thermal dissipation
Q3: How are BGA packages attached to the PCB?
A3: BGA packages are soldered to the PCB using a reflow soldering process. The package is placed on the board with the solder balls aligned to the pads. During reflow, the solder melts and forms an electrical and mechanical connection between the package and board.
Q4: What is the difference between BGA and LGA?
A4: BGA packages have solder balls while LGA packages have flat contact pads (lands). LGA does not have solderable balls pre-attached. Instead, an LGA socket or spring pins are used to compress the package against the mating pads on the PCB.
Q5: Are BGA packages repairable?
A5: Reworking BGA packages is possible but more challenging than with leaded packages. Specialized equipment and processes are required to remove and replace BGA components. The high heat required for BGA Rework can cause damage to the PCB and neighboring components if not done properly. It’s best to avoid rework when possible through careful design and assembly processes.
Conclusion
BGA packages are widely used across many electronics applications due to their high interconnect density, compact size, and good electrical and thermal performance. There is a diverse range of BGA package types optimized for different requirements, from low-cost plastic BGAs to high-reliability ceramic ones and multi-die options like PoP and SiP.
Selecting the appropriate BGA package requires carefully evaluating the demands of the application and balancing trade-offs between size, performance, reliability, and cost. By understanding the characteristics of the various BGA package styles, PCB Designers and engineers can make informed decisions and optimize their designs.
As electronic devices continue to push the boundaries of performance and miniaturization, innovations in BGA packaging technologies will be critical to enabling the next generation of advanced systems. Emerging trends like finer ball pitch, 2.5D and 3D integration, and embedded components will further expand the capabilities and use cases for BGA components.
No responses yet