What is Through-Hole Technology?
Through-hole technology involves mounting components on a PCB by inserting their leads through drilled holes in the board and soldering them to pads on the opposite side. This method has been used since the early days of PCB manufacturing and remains a reliable choice for many applications.
Advantages of Through-Hole Technology
-
Mechanical Strength: Through-hole components offer superior mechanical strength compared to SMT components. The leads extending through the board and the solder joint on the opposite side create a strong physical connection, making the assembly more resistant to vibration and mechanical stress.
-
Ease of Prototyping: Through-hole components are often easier to work with during prototyping and manual assembly. The larger size of the components and the visible leads make them easier to handle and solder, which can be advantageous for low-volume production or hobby projects.
-
Reliability in Harsh Environments: Through-hole technology is often preferred in applications that are subject to extreme temperatures, high vibration, or other harsh environmental conditions. The robust mechanical connection provided by through-hole mounting helps ensure the reliability of the assembly in these challenging situations.
-
High Power Handling: Through-hole components, such as power resistors and capacitors, are often better suited for high-power applications. The larger size and greater surface area of through-hole components allow for better heat dissipation, which is critical in power-intensive designs.
Disadvantages of Through-Hole Technology
-
Lower Component Density: Through-hole components require more space on the PCB compared to SMT components. The drilled holes and larger component sizes limit the achievable component density, which can be a drawback in applications where board space is limited.
-
Increased Manufacturing Cost: Through-hole assembly typically involves more manual labor compared to SMT assembly, which can increase manufacturing costs. Additionally, the drilling process required for through-hole boards adds an extra step to the manufacturing process, further increasing costs.
-
Limited Miniaturization: As electronic devices continue to shrink in size, through-hole technology may not be suitable for designs that require extreme miniaturization. SMT components can be much smaller than their through-hole counterparts, allowing for more compact PCB designs.
Applications Where Through-Hole Remains Relevant
Despite the growing popularity of SMT, through-hole technology continues to be relevant in various applications. Some examples include:
-
High-Reliability Applications: In industries such as aerospace, military, and medical devices, where reliability is paramount, through-hole technology is often preferred due to its superior mechanical strength and resistance to environmental stresses.
-
Power Electronics: Through-hole components are commonly used in power electronics applications, such as power supplies and Motor Controllers, due to their ability to handle high currents and dissipate heat effectively.
-
Prototyping and Low-Volume Production: Through-hole technology is often the choice for prototyping and low-volume production runs, as it allows for easier manual assembly and rework compared to SMT.
-
Educational and Hobby Projects: Through-hole components are frequently used in educational settings and hobby projects, as they are easier to handle and solder for beginners.
Comparison of Through-Hole and Surface Mount Technology
To better understand the relevance of through-hole technology, let’s compare it with surface mount technology across various factors:
Factor | Through-Hole | Surface Mount |
---|---|---|
Component Density | Lower | Higher |
Manufacturing Cost | Higher | Lower |
Assembly Process | Manual or wave soldering | Automated pick-and-place and reflow soldering |
Mechanical Strength | Higher | Lower |
Heat Dissipation | Better | Worse |
Miniaturization | Limited | Excellent |
Rework and Repair | Easier | More challenging |
Suitability for Harsh Environments | Better | Worse |
As evident from the comparison, both through-hole and SMT have their strengths and weaknesses. The choice between the two depends on the specific requirements of the application, such as the need for high component density, mechanical strength, or ease of assembly.
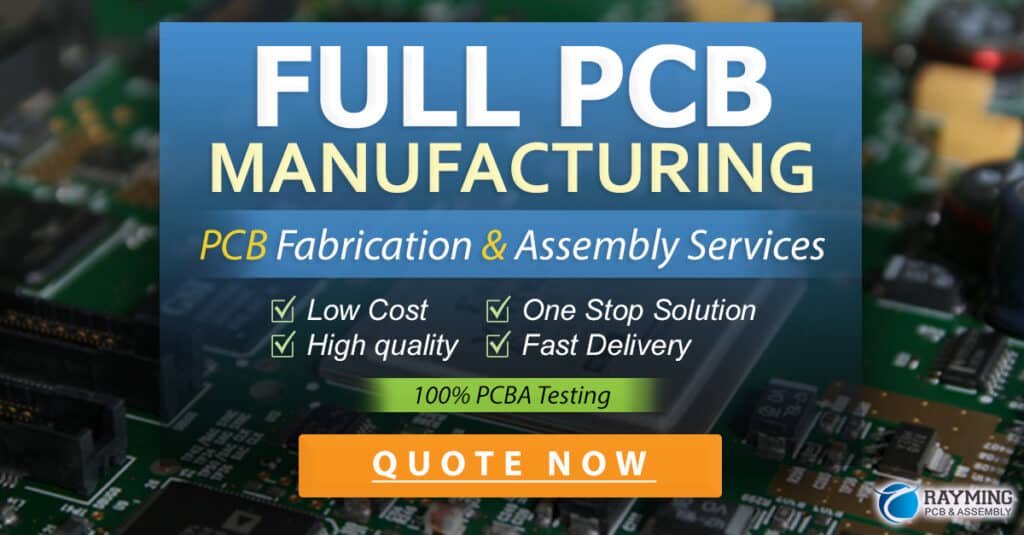
Combining Through-Hole and SMT in PCB Design
In some cases, it may be advantageous to use a combination of through-hole and SMT components in a single PCB design. This hybrid approach allows designers to leverage the benefits of both technologies while mitigating their drawbacks.
For example, a PCB design may use SMT components for the majority of the circuitry to achieve high component density and lower manufacturing costs, while using through-hole components for power handling, mechanical support, or connectors. This combination ensures that the design meets the specific requirements of the application while optimizing cost and performance.
Future of Through-Hole Technology
While SMT has become the dominant technology in PCB manufacturing, through-hole technology is likely to remain relevant in the foreseeable future. As long as there are applications that require high mechanical strength, reliability in harsh environments, or ease of manual assembly, through-hole will continue to have a place in PCB design.
However, it is essential for PCB designers to stay updated with the latest advancements in both through-hole and SMT technologies. Manufacturers are continuously developing new components and assembly techniques that can improve the performance, reliability, and cost-effectiveness of both technologies.
Frequently Asked Questions (FAQ)
-
Q: Can through-hole and SMT components be used on the same PCB?
A: Yes, it is possible to use a combination of through-hole and SMT components on a single PCB. This hybrid approach allows designers to leverage the benefits of both technologies while mitigating their drawbacks. -
Q: Is through-hole technology more expensive than SMT?
A: In general, through-hole assembly is more expensive than SMT assembly due to the increased manual labor and the additional drilling process required for through-hole boards. However, the cost difference may be less significant for low-volume production or prototype runs. -
Q: Are through-hole components larger than SMT components?
A: Yes, through-hole components are typically larger than their SMT counterparts. This is because through-hole components need to have leads that can be inserted through the drilled holes in the PCB, while SMT components are designed to be mounted directly on the surface of the board. -
Q: Is through-hole technology suitable for high-frequency applications?
A: Through-hole technology may not be the best choice for high-frequency applications, as the leads of through-hole components can introduce unwanted inductance and parasitic effects. SMT components are often preferred for high-frequency designs due to their smaller size and shorter lead lengths. -
Q: Can through-hole components be replaced with SMT equivalents?
A: In many cases, through-hole components can be replaced with SMT equivalents. However, it is essential to consider factors such as power handling, mechanical strength, and heat dissipation when making the switch. Some applications may still require the use of through-hole components for optimal performance and reliability.
Conclusion
Through-hole technology remains relevant in PCB design despite the growing popularity of surface mount technology. Through-hole components offer superior mechanical strength, reliability in harsh environments, and ease of manual assembly, making them the preferred choice for certain applications such as high-reliability systems, power electronics, and prototyping.
While SMT has its advantages in terms of component density, manufacturing cost, and miniaturization, it is essential for PCB designers to consider the specific requirements of their application when choosing between through-hole and SMT. In some cases, a hybrid approach combining both technologies may provide the best balance of performance, reliability, and cost-effectiveness.
As PCB technology continues to evolve, it is crucial for designers to stay informed about the latest advancements in both through-hole and SMT components and assembly techniques. By understanding the strengths and limitations of each technology, designers can make informed decisions that optimize the performance and reliability of their PCB designs while meeting the specific needs of their applications.
No responses yet