Introduction to Motor Controllers
Motor controllers are electronic devices that regulate the performance of electric motors. They are essential components in a wide range of applications, from simple household appliances to complex industrial machinery. Motor controllers work by manipulating the electrical power supplied to the motor, allowing for precise control over the motor’s speed, torque, and direction of rotation.
The primary purpose of a motor controller is to ensure that the motor operates efficiently and safely. By controlling the motor’s performance, the controller can optimize energy consumption, prolong the motor’s lifespan, and prevent damage caused by overloading or overheating.
Types of Motor Controllers
There are several types of motor controllers, each designed for specific applications and motor types. Some of the most common types include:
1. DC Motor Controllers
DC motor controllers are used to control the speed and direction of DC motors. They work by varying the voltage or current supplied to the motor, which in turn changes the motor’s speed and torque. DC motor controllers are commonly used in applications such as robotics, automotive systems, and industrial automation.
2. AC Motor Controllers
AC motor controllers are designed to control the speed and torque of AC motors. They work by adjusting the frequency and voltage of the AC power supplied to the motor. AC motor controllers are used in a wide range of applications, including HVAC systems, pumps, and conveyor belts.
3. Stepper Motor Controllers
Stepper motor controllers are used to control the precise positioning and movement of stepper motors. These controllers send a sequence of electrical pulses to the motor, causing it to rotate in small, incremental steps. Stepper motor controllers are commonly used in 3D printers, CNC machines, and other applications requiring high precision and repeatability.
4. Servo Motor Controllers
Servo motor controllers are designed to control the position, speed, and torque of servo motors. They work by sending a control signal to the motor, which adjusts its position based on the signal’s voltage or pulse width. Servo motor controllers are used in applications such as robotics, automotive systems, and industrial automation.
How Motor Controllers Work
Motor controllers use various techniques to regulate the performance of electric motors. Some of the most common methods include:
1. Pulse Width Modulation (PWM)
Pulse Width Modulation (PWM) is a technique used by motor controllers to vary the average voltage supplied to the motor. In PWM, the controller rapidly switches the power supply on and off, creating a series of pulses. By adjusting the width of these pulses, the controller can effectively control the motor’s speed and torque.
2. Frequency Control
Frequency control is a method used by AC motor controllers to regulate the speed of AC motors. By adjusting the frequency of the AC power supplied to the motor, the controller can change the motor’s synchronous speed. This technique is commonly used in variable frequency drives (VFDs) for applications such as pumps, fans, and conveyors.
3. Voltage and Current Control
Voltage and current control are techniques used by DC motor controllers to regulate the speed and torque of DC motors. By varying the voltage or current supplied to the motor, the controller can adjust the motor’s performance. This method is often used in conjunction with PWM to achieve more precise control.
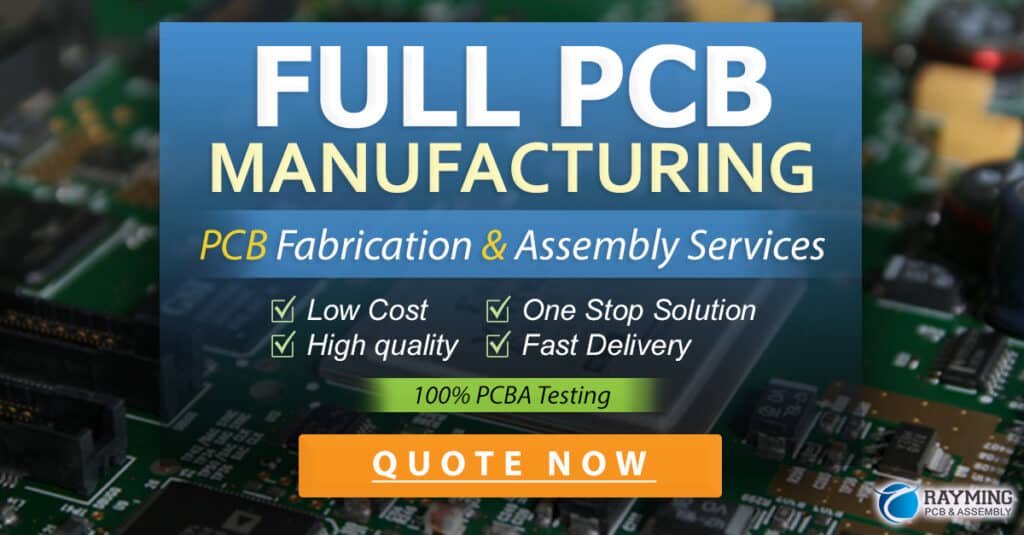
Choosing the Right Motor Controller
When selecting a motor controller for a specific application, there are several factors to consider:
1. Motor Type
The first step in choosing a motor controller is to identify the type of motor being used. Different motor types require different types of controllers, so it’s essential to select a controller that is compatible with the motor.
2. Application Requirements
Consider the specific requirements of the application, such as the required speed range, torque, and precision. The motor controller should be capable of meeting these requirements while ensuring safe and efficient operation.
3. Environment
The operating environment can have a significant impact on the performance and longevity of the motor controller. Factors such as temperature, humidity, and exposure to dust or other contaminants should be taken into account when selecting a controller.
4. Cost
Motor controllers can vary significantly in price, depending on their features and capabilities. It’s important to balance the cost of the controller with the specific needs of the application to ensure the best value for money.
Motor Controller Applications
Motor controllers are used in a wide range of applications across various industries. Some common applications include:
1. Industrial Automation
Motor controllers are essential components in industrial automation systems, where they are used to control the motion of machinery, robots, and conveyor systems. In these applications, motor controllers ensure precise and reliable operation, improving productivity and reducing downtime.
Application | Motor Type | Controller Type |
---|---|---|
Conveyor Systems | AC Motors | VFDs |
CNC Machines | Stepper Motors | Stepper Motor Controllers |
Robotics | Servo Motors | Servo Motor Controllers |
2. Automotive Systems
Motor controllers are used in various automotive applications, such as electric power steering, throttle control, and cruise control. In these systems, motor controllers ensure smooth and responsive operation, improving vehicle performance and safety.
Application | Motor Type | Controller Type |
---|---|---|
Electric Power Steering | DC Motors | DC Motor Controllers |
Throttle Control | DC Motors | DC Motor Controllers |
Cruise Control | DC Motors | DC Motor Controllers |
3. HVAC and Refrigeration
Motor controllers are used in heating, ventilation, air conditioning (HVAC), and refrigeration systems to control the speed and efficiency of compressors, fans, and pumps. By optimizing the performance of these components, motor controllers can help reduce energy consumption and improve system reliability.
Application | Motor Type | Controller Type |
---|---|---|
Compressors | AC Motors | VFDs |
Fans | AC Motors | VFDs |
Pumps | AC Motors | VFDs |
Frequently Asked Questions (FAQ)
1. What is the difference between a motor controller and a drive?
A motor controller is a general term for a device that regulates the performance of an electric motor. A drive, such as a variable frequency drive (VFD), is a specific type of motor controller that controls the speed and torque of an AC motor by adjusting the frequency and voltage of the power supplied to the motor.
2. Can a DC motor controller be used with an AC motor?
No, a DC motor controller cannot be used with an AC motor. DC and AC motors have different operating principles and require specific types of controllers. Using the wrong type of controller can result in poor performance, damage to the motor, or even safety hazards.
3. How does a motor controller help save energy?
Motor controllers can help save energy by optimizing the performance of the motor based on the specific requirements of the application. By controlling the motor’s speed, torque, and other parameters, the controller can ensure that the motor operates at its most efficient point, reducing energy consumption and costs.
4. What is the role of a motor controller in a closed-loop control system?
In a closed-loop control system, a motor controller receives feedback from sensors that monitor the motor’s performance. The controller then uses this feedback to adjust the motor’s operation, ensuring that it meets the desired setpoints for speed, position, or torque. This continuous feedback loop allows for precise and accurate control of the motor.
5. How do I determine the appropriate size of a motor controller for my application?
To determine the appropriate size of a motor controller, you need to consider factors such as the motor’s rated power, voltage, and current, as well as the specific requirements of the application, such as the required speed range and torque. It’s essential to consult the motor and controller manufacturer’s specifications and guidelines to ensure proper sizing and compatibility.
Conclusion
Motor controllers are critical components in a wide range of applications, from industrial automation to automotive systems and HVAC. By regulating the performance of electric motors, these controllers ensure efficient, reliable, and safe operation. Understanding the different types of motor controllers, their working principles, and the factors to consider when selecting a controller is essential for anyone working with electric motors.
As technology advances, motor controllers are becoming increasingly sophisticated, with features such as network communication, advanced control algorithms, and built-in safety functions. These developments are enabling new applications and improving the performance and efficiency of existing systems.
In conclusion, motor controllers play a vital role in the operation of electric motors, and their importance will only continue to grow as industries seek to optimize their processes and reduce energy consumption. By staying informed about motor controller theory and applications, engineers and technicians can design and maintain systems that are efficient, reliable, and safe.
No responses yet