Introduction to OSP PCB Finish
OSP, which stands for Organic Solderability Preservatives, is a type of surface finish applied to printed circuit boards (PCBs) to protect the exposed copper circuitry from oxidation and ensure good solderability during the assembly process. OSP-PCB-Finish has gained popularity in recent years as a cost-effective and environmentally friendly alternative to other surface finishes like HASL (Hot Air Solder Leveling), ENIG (Electroless Nickel Immersion Gold), and Immersion Silver.
In this comprehensive guide, we will delve into the details of OSP PCB Surface Finish, its advantages, disadvantages, and applications. We will also compare OSP to other common surface finishes and provide answers to frequently asked questions about this technology.
What is OSP PCB Finish?
OSP is a chemical process that involves applying a thin layer of organic compounds, typically azoles, to the exposed copper surfaces of a PCB. These organic compounds form a protective barrier that prevents the copper from oxidizing and maintains its solderability for a limited period.
The OSP coating is applied through a series of steps:
- Cleaning: The PCB is thoroughly cleaned to remove any contaminants or residues.
- Microetching: A mild etching solution is used to remove any oxide layer on the copper surface and create a uniform surface texture.
- OSP Application: The PCB is immersed in an OSP solution, which contains the organic compounds that will form the protective layer.
- Drying: The PCB is dried using hot air to evaporate any remaining moisture and ensure a uniform coating.
The resulting OSP layer is extremely thin, typically between 0.2 and 0.5 microns, and is transparent or slightly tinted. This thin layer provides adequate protection against oxidation while still allowing for easy soldering during the assembly process.
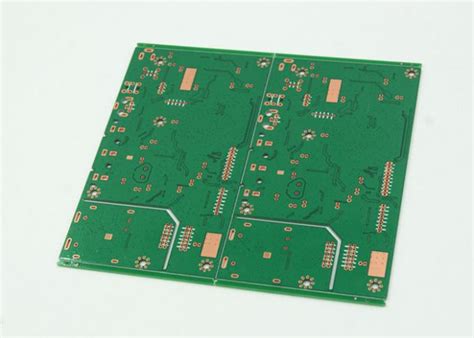
Advantages of OSP-PCB-Finish
OSP offers several advantages over other surface finishes:
-
Cost-effective: OSP is one of the most economical surface finishes available, as it requires fewer processing steps and materials compared to other finishes like ENIG or HASL.
-
Environmentally friendly: The organic compounds used in OSP are non-toxic and biodegradable, making it a more eco-friendly option compared to finishes that use heavy metals or lead.
-
Flat surface: OSP provides a flat and uniform surface, which is essential for fine-pitch components and high-density designs.
-
Good solderability: OSP maintains good solderability for a limited period, typically up to 12 months under proper storage conditions.
-
Easy to inspect: The transparent nature of the OSP coating allows for easy visual inspection of the PCB for any defects or anomalies.
-
Suitable for multiple soldering processes: OSP is compatible with various soldering processes, including reflow soldering, wave soldering, and hand soldering.
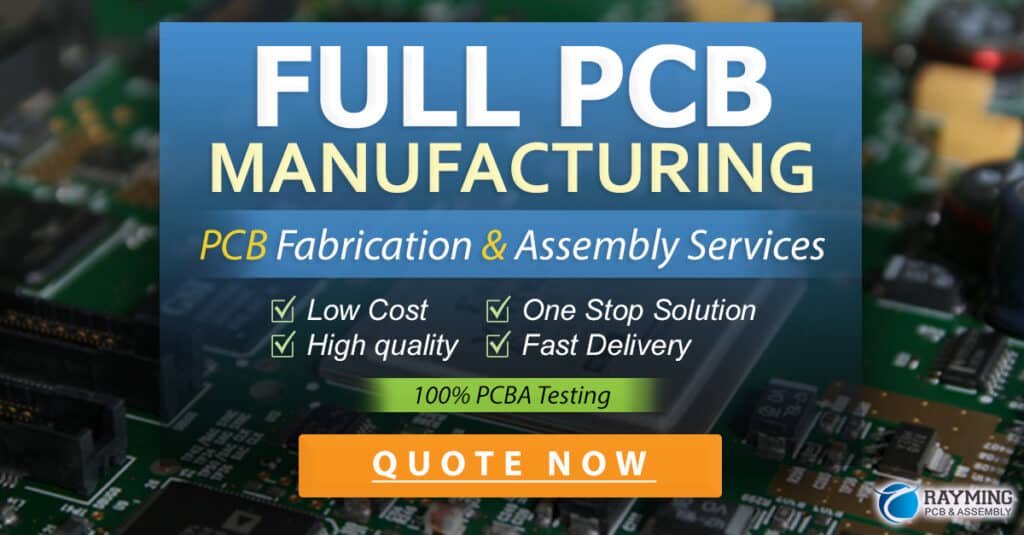
Disadvantages of OSP PCB Finish
Despite its many advantages, OSP also has some limitations:
-
Limited shelf life: The protective properties of OSP degrade over time, typically within 12 months, after which the solderability of the PCB may be compromised.
-
Sensitivity to handling: OSP-coated PCBs are more susceptible to contamination from handling, as the organic layer can easily absorb oils and moisture from skin contact.
-
Not suitable for multiple reflow cycles: OSP may not withstand multiple reflow soldering cycles, as the organic layer can degrade under repeated exposure to high temperatures.
-
Incompatible with some fluxes: Certain aggressive fluxes can strip away the OSP coating, reducing its effectiveness in protecting the copper surface.
-
Not ideal for wire bonding: OSP may not provide a suitable surface for wire bonding, as the organic layer can interfere with the bonding process.
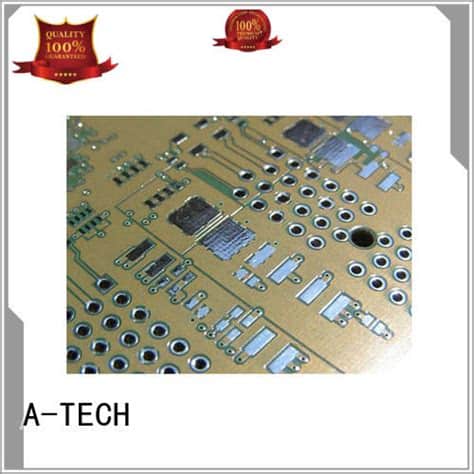
Applications of OSP PCB Finish
OSP is widely used in various electronics industries, including:
-
Consumer electronics: OSP is a popular choice for consumer electronics, such as smartphones, tablets, and laptops, where cost and environmental considerations are important factors.
-
Automotive electronics: OSP is used in automotive PCBs, particularly for interior applications where the PCBs are not exposed to harsh environmental conditions.
-
Industrial electronics: OSP is employed in industrial control systems, sensors, and other applications where cost-effectiveness and good solderability are crucial.
-
Medical devices: Some medical devices, such as disposable sensors and monitoring equipment, use OSP-coated PCBs for their cost-effectiveness and environmental friendliness.
Comparison of OSP with Other Surface Finishes
To better understand the advantages and limitations of OSP, it is essential to compare it with other common surface finishes:
Surface Finish | Advantages | Disadvantages |
---|---|---|
OSP | – Cost-effective – Environmentally friendly – Flat surface – Good solderability |
– Limited shelf life – Sensitive to handling – Not suitable for multiple reflow cycles |
HASL | – Excellent solderability – Long shelf life – Low cost |
– Uneven surface – Contains lead (in some cases) – Thermal shock to PCB |
ENIG | – Flat surface – Excellent solderability – Long shelf life – Suitable for wire bonding |
– Expensive – Complex process – Sensitive to contamination |
Immersion Silver | – Good solderability – Flat surface – Quick process |
– Limited shelf life – Prone to tarnishing – Not suitable for high-sulfur environments |
As evident from the table, each surface finish has its own set of advantages and disadvantages. The choice of surface finish depends on various factors, such as the specific application, budget, environmental requirements, and the desired shelf life of the PCB.
FAQ
1. How long does the OSP coating last?
Under proper storage conditions, the OSP coating can maintain good solderability for up to 12 months. However, the actual shelf life may vary depending on factors such as the specific OSP formulation used, storage temperature, and humidity.
2. Can OSP be used for high-temperature applications?
OSP may not be the best choice for high-temperature applications, as the organic layer can degrade under repeated exposure to high temperatures during multiple reflow soldering cycles. For such applications, surface finishes like ENIG or HASL may be more suitable.
3. Is OSP suitable for PCBs with fine-pitch components?
Yes, OSP is well-suited for PCBs with fine-pitch components, as it provides a flat and uniform surface that facilitates the accurate placement and soldering of these components.
4. How does OSP compare to HASL in terms of cost?
OSP is generally more cost-effective than HASL, as it requires fewer processing steps and materials. Additionally, OSP is a lead-free process, which eliminates the need for the more expensive lead-free HASL process.
5. Can OSP-coated PCBs be reworked?
Yes, OSP-coated PCBs can be reworked, but the rework process may be more challenging compared to other surface finishes. The OSP coating may be damaged during the rework process, which can affect the solderability of the repaired area. It is essential to follow proper rework procedures and use compatible fluxes to ensure the best results.
Conclusion
OSP PCB surface finish is a cost-effective and environmentally friendly option that offers good solderability, a flat surface, and compatibility with various soldering processes. While it has some limitations, such as a limited shelf life and sensitivity to handling, OSP remains a popular choice for many electronics applications.
When deciding on the most suitable surface finish for a PCB, it is essential to consider factors such as the specific application requirements, budget, environmental considerations, and the desired shelf life. By understanding the advantages and disadvantages of OSP and other surface finishes, PCB Designers and manufacturers can make informed decisions that balance cost, performance, and reliability.
As technology continues to advance, it is likely that new developments in OSP and other surface finishes will emerge, offering even better protection, solderability, and compatibility with evolving electronics manufacturing processes.
No responses yet