Introduction to PCB Design Optimization
Printed Circuit Board (PCB) design is a complex process that involves multiple steps and considerations. Optimizing the PCB design flow is crucial for ensuring the reliability, functionality, and cost-effectiveness of the final product. In this article, we will explore the key aspects of the optimum PCB design flow, focusing on achieving a “right first time” approach.
Understanding the PCB Design Process
PCB Design Stages
The PCB design process can be divided into several stages:
- Schematic Design
- Component Placement
- Routing
- Design Rule Check (DRC)
- Manufacturing Preparation
Each stage plays a critical role in the overall success of the PCB design.
Importance of PCB Design Optimization
Optimizing the PCB design process offers several benefits:
- Reduced design iterations and time-to-market
- Improved product reliability and performance
- Lower manufacturing costs
- Enhanced collaboration between design teams
By focusing on PCB design optimization, companies can achieve a competitive edge in their respective markets.
Best Practices for PCB Design Optimization
1. Define Clear Design Requirements
Clearly defining the design requirements is the foundation of a successful PCB design. This includes specifying the following:
- Functionality and performance criteria
- Physical dimensions and constraints
- Environmental factors (temperature, humidity, vibration, etc.)
- Regulatory compliance requirements
2. Choose the Right PCB Design Software
Selecting the appropriate PCB design software is crucial for streamlining the design process. Consider the following factors when choosing a PCB design tool:
- Ease of use and learning curve
- Integration with other design tools (e.g., CAD, simulation)
- Availability of libraries and component information
- Support for advanced features (e.g., high-speed design, RF design)
Some popular PCB design software options include Altium Designer, Cadence OrCAD, and KiCad.
3. Optimize Component Placement
Proper component placement is essential for achieving optimal PCB performance and manufacturability. Consider the following guidelines:
- Group related components together
- Minimize the distance between connected components
- Consider thermal management and heat dissipation
- Ensure proper clearance for manufacturing and assembly
4. Implement Efficient Routing Strategies
Routing is the process of connecting components on the PCB using conductive traces. Efficient routing strategies can improve signal integrity and reduce manufacturing costs. Consider the following tips:
- Use appropriate trace widths and spacing based on signal requirements
- Minimize the number of vias and layer changes
- Avoid sharp angles and maintain consistent trace geometry
- Implement proper grounding and shielding techniques
5. Perform Thorough Design Rule Checks (DRC)
Design Rule Checks (DRC) help identify potential issues in the PCB design before manufacturing. Perform thorough DRC to ensure the following:
- Compliance with manufacturing constraints (e.g., minimum trace width, clearance)
- Absence of short circuits, open circuits, and other connectivity issues
- Proper silk screen and solder mask placement
- Correct Component Orientation and footprint mapping
6. Collaborate with Manufacturing Partners
Collaborating closely with manufacturing partners can help optimize the PCB design for manufacturability and cost-effectiveness. Consider the following:
- Engage with manufacturers early in the design process
- Understand their capabilities and limitations
- Provide clear and comprehensive manufacturing files
- Incorporate their feedback and suggestions into the design
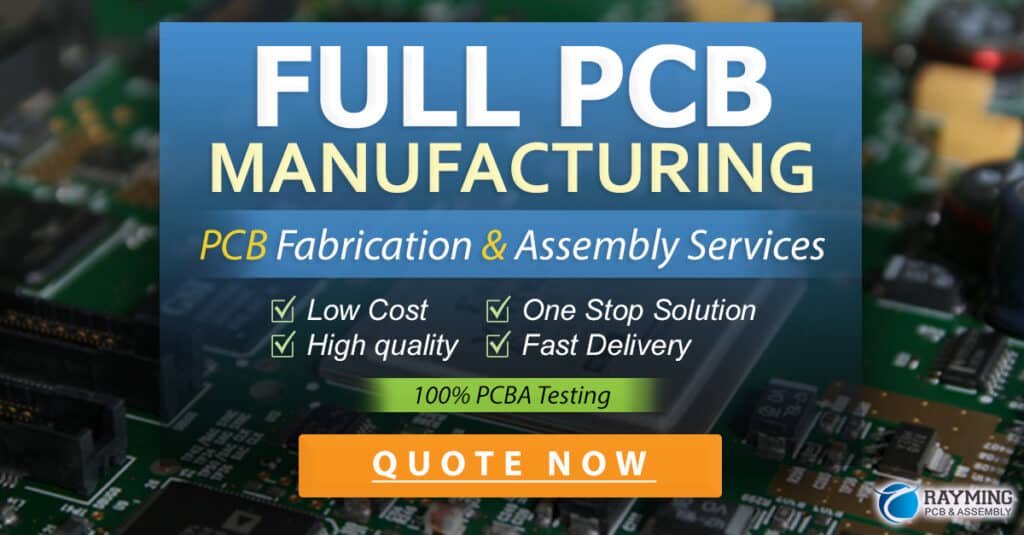
Advanced PCB Design Optimization Techniques
High-Speed Design Considerations
When designing high-speed PCBs, additional considerations come into play to ensure signal integrity and minimize electromagnetic interference (EMI). Some key techniques include:
- Impedance matching and controlled impedance routing
- Differential pair routing
- Proper termination and damping techniques
- Signal integrity simulation and analysis
Thermal Management Strategies
Effective thermal management is crucial for ensuring the reliability and longevity of PCBs, especially those with high-power components. Consider the following strategies:
- Implement proper heat sinking and cooling mechanisms
- Use thermal vias and planes to dissipate heat
- Consider the thermal properties of PCB Materials
- Perform thermal simulations to identify hotspots and optimize the design
Design for Manufacturing (DFM) and Assembly (DFA)
Designing PCBs with manufacturing and assembly in mind can significantly reduce costs and improve yields. Some DFM and DFA techniques include:
- Adhering to manufacturing tolerances and constraints
- Minimizing the number of unique components and footprints
- Ensuring proper component placement for automated assembly
- Considering the accessibility and orientation of components for manual assembly
PCB Design Optimization Tools and Resources
There are various tools and resources available to support PCB design optimization efforts:
Simulation and Analysis Tools
- Signal integrity simulation (e.g., Mentor Graphics HyperLynx, Cadence Sigrity)
- Thermal simulation (e.g., Ansys Icepak, Mentor Graphics FloTHERM)
- Electromagnetic compatibility (EMC) simulation (e.g., CST Studio Suite, Ansys HFSS)
Component Libraries and Databases
- Manufacturer-provided component libraries
- Online component databases (e.g., Digi-Key, Mouser)
- Collaborative component management systems (e.g., Altium Vault, Cadence OrCAD CIS)
Design Guidelines and Standards
- IPC Standards (e.g., IPC-2221, IPC-7351)
- Manufacturer-specific design guidelines
- Industry-specific standards (e.g., automotive, aerospace, medical)
Case Studies and Success Stories
Real-world examples of successful PCB design optimization can provide valuable insights and inspiration. Some notable case studies include:
- Company A: Reduced time-to-market by 30% through efficient PCB design optimization
- Company B: Achieved 95% first-pass yield by implementing DFM and DFA principles
- Company C: Mitigated EMI issues and passed regulatory compliance tests through advanced high-speed design techniques
Frequently Asked Questions (FAQ)
1. What is the most critical aspect of PCB design optimization?
The most critical aspect of PCB design optimization is defining clear design requirements upfront. This lays the foundation for all subsequent design decisions and ensures that the final product meets the intended functionality and performance criteria.
2. How can I ensure my PCB design is manufacturable?
To ensure manufacturability, collaborate closely with your manufacturing partners, adhere to their design guidelines, and perform thorough Design Rule Checks (DRC). Incorporating Design for Manufacturing (DFM) principles can also help optimize the design for cost-effective and reliable production.
3. What are the key considerations for high-speed PCB design?
Key considerations for high-speed PCB design include impedance matching, controlled impedance routing, differential pair routing, proper termination and damping, and signal integrity simulation. These techniques help maintain signal integrity and minimize electromagnetic interference (EMI).
4. How can I optimize my PCB design for thermal management?
To optimize your PCB design for thermal management, consider implementing proper heat sinking and cooling mechanisms, using thermal vias and planes, selecting appropriate PCB materials with good thermal properties, and performing thermal simulations to identify and address hotspots.
5. What resources are available to support PCB design optimization efforts?
There are various resources available to support PCB design optimization, including simulation and analysis tools, component libraries and databases, design guidelines and standards, and industry-specific forums and communities. Leveraging these resources can help streamline the design process and ensure compliance with best practices.
Conclusion
Optimizing the PCB design flow is essential for achieving a “right first time” approach, reducing design iterations, and improving overall product quality and cost-effectiveness. By following best practices, leveraging advanced optimization techniques, and collaborating with manufacturing partners, designers can streamline the PCB design process and deliver reliable and high-performing products to market faster.
As the electronics industry continues to evolve, staying up-to-date with the latest PCB design optimization strategies and tools will be crucial for staying competitive and meeting the ever-increasing demands for functionality, reliability, and efficiency.
PCB Design Stage | Key Considerations |
---|---|
Schematic Design | – Functionality and performance criteria – Component selection and specification – Signal integrity and power management |
Component Placement | – Grouping related components – Minimizing distances between connected components – Thermal management and heat dissipation – Manufacturing and assembly clearances |
Routing | – Appropriate trace widths and spacing – Minimizing vias and layer changes – Consistent trace geometry – Grounding and shielding techniques |
Design Rule Check (DRC) | – Manufacturing constraint compliance – Short circuits, open circuits, and connectivity issues – Silk screen and solder mask placement – Component orientation and footprint mapping |
Manufacturing Preparation | – Collaboration with manufacturing partners – Clear and comprehensive manufacturing files – Incorporation of manufacturer feedback and suggestions |
Table 1: Key considerations for each stage of the PCB design process.
By addressing these key considerations at each stage of the PCB design process, designers can optimize their designs for reliability, performance, and manufacturability, ultimately achieving a successful “right first time” approach.
No responses yet