Introduction to PCB Manufacturing
PCB (Printed Circuit Board) manufacturing is a complex process that involves multiple steps and techniques. This comprehensive guide will walk you through the various aspects of PCB manufacturing, from design to assembly, and provide you with the knowledge needed to create high-quality PCBs.
What is a PCB?
A PCB is a flat board made of insulating materials, such as fiberglass or plastic, with conductive copper traces printed on its surface. These traces connect various electronic components, such as resistors, capacitors, and integrated circuits, to form a complete electronic circuit.
Why are PCBs Important?
PCBs are essential in modern electronics because they provide a reliable and efficient way to interconnect electronic components. They offer several advantages over traditional point-to-point wiring, including:
- Reduced wiring errors
- Improved signal integrity
- Increased reliability
- Reduced size and weight
- Easier mass production
PCB Design
Schematic Design
The first step in PCB manufacturing is to create a schematic design. A schematic is a graphical representation of the electronic circuit, showing the connections between components using standardized symbols. Designers use Electronic Design Automation (EDA) software, such as Altium Designer or KiCad, to create schematics.
PCB Layout
Once the schematic is complete, the next step is to create a PCB layout. The layout determines the physical placement of components and the routing of copper traces on the PCB. Designers must consider factors such as component size, trace width, and spacing to ensure proper functionality and manufacturability.
PCB Layers
PCBs can have multiple layers, depending on the complexity of the circuit and the available space. The most common PCB layer configurations are:
Layers | Description |
---|---|
Single Layer | A PCB with conductive traces on one side only |
Double Layer | A PCB with conductive traces on both sides |
Multi-Layer | A PCB with conductive traces on multiple internal layers, sandwiched between insulating layers |
PCB Trace Width and Spacing
The width and spacing of copper traces on a PCB are critical factors in ensuring proper functionality and manufacturability. The trace width determines the current-carrying capacity of the trace, while the spacing between traces affects signal integrity and the risk of short circuits.
Trace Width (mm) | Current Capacity (A) |
---|---|
0.25 | 0.5 |
0.5 | 1.0 |
1.0 | 2.0 |
2.0 | 4.0 |
Design for Manufacturing (DFM)
To ensure that a PCB can be manufactured reliably and cost-effectively, designers must adhere to Design for Manufacturing (DFM) guidelines. These guidelines cover aspects such as minimum trace width and spacing, hole sizes, and component placement. Following DFM guidelines minimizes the risk of manufacturing defects and reduces production costs.
PCB Fabrication
PCB Material Selection
The choice of PCB material depends on the specific requirements of the application, such as temperature range, dielectric constant, and flame retardancy. The most common PCB materials are:
- FR-4: A glass-reinforced epoxy laminate, suitable for general-purpose applications
- High-Tg FR-4: An FR-4 variant with improved thermal stability, suitable for lead-free soldering processes
- Polyimide: A high-temperature material, suitable for aerospace and military applications
- Teflon: A low-dielectric-constant material, suitable for high-frequency applications
Copper Clad Laminate
The first step in PCB fabrication is to create a copper clad laminate, which consists of a thin layer of copper foil bonded to the surface of the insulating material. The copper foil thickness is typically expressed in ounces per square foot (oz/ft²), with common thicknesses being 0.5 oz/ft², 1 oz/ft², and 2 oz/ft².
Drilling
After the copper clad laminate is prepared, the next step is to drill holes for through-hole components and vias. Vias are small holes that connect different layers of the PCB. Drilling is typically done using Computer Numerical Control (CNC) machines, which ensure precise hole placement and size.
Copper Patterning
The copper patterning process creates the conductive traces on the PCB. There are two main methods for copper patterning:
-
Subtractive Method: In this method, the entire copper surface is coated with a photoresist, which is then selectively exposed to light through a photomask. The unexposed areas are removed, leaving the desired copper traces. The exposed copper is then etched away using a chemical solution.
-
Additive Method: In this method, the copper traces are selectively deposited onto the insulating material using techniques such as electroless plating or direct printing. This method is less common than the subtractive method but offers advantages such as reduced waste and the ability to create finer traces.
Solder Mask Application
After the copper patterning is complete, a solder mask is applied to the PCB. The solder mask is a protective coating that covers the copper traces, leaving only the areas intended for soldering exposed. The solder mask improves the PCB’s insulation properties and protects the copper from oxidation and damage during handling.
Silkscreen Printing
The final step in PCB fabrication is silkscreen printing, which adds text and symbols to the PCB for component identification and assembly guidance. The silkscreen is typically printed using white ink, although other colors are available for special applications.
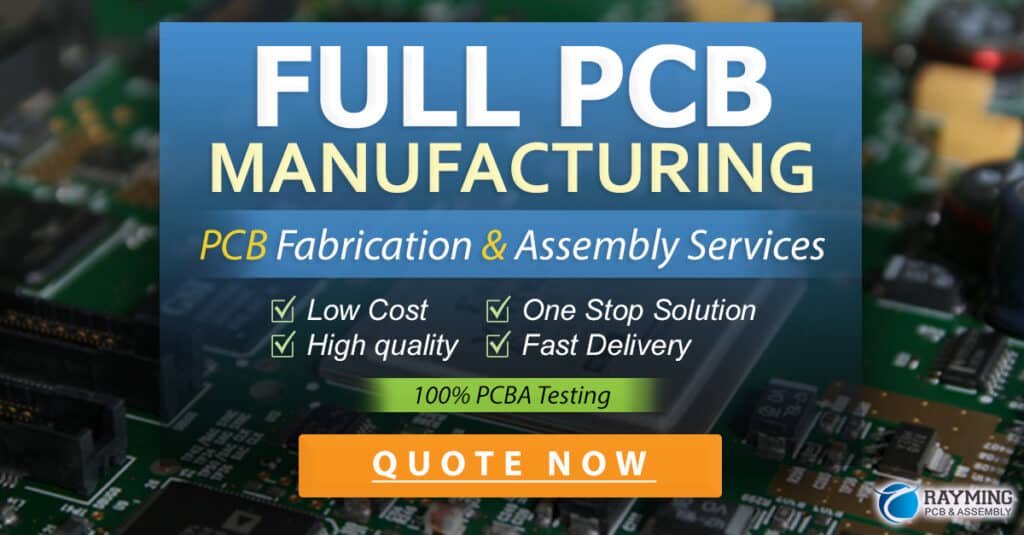
PCB Assembly
Surface Mount Technology (SMT)
Surface Mount Technology (SMT) is a method of assembling electronic components onto the surface of a PCB without the need for through-hole mounting. SMT components are smaller and lighter than through-hole components, allowing for higher component density and improved performance.
Solder Paste Printing
The first step in SMT Assembly is to print solder paste onto the PCB’s pads using a stencil. The stencil ensures that the correct amount of solder paste is deposited on each pad, ensuring reliable solder joints.
Component Placement
After the solder paste is printed, the SMT components are placed onto the PCB using a pick-and-place machine. The machine uses computer vision to accurately place the components on their respective pads.
Reflow Soldering
Once the components are placed, the PCB is sent through a reflow oven, which melts the solder paste and creates a permanent bond between the components and the PCB. The reflow soldering process is carefully controlled to ensure that the solder joints are formed correctly and that the components are not damaged by excessive heat.
Through-Hole Assembly
While SMT is the most common assembly method, some components still require through-hole mounting. Through-hole components are inserted into holes drilled in the PCB and soldered in place using wave soldering or manual soldering techniques.
Inspection and Testing
After assembly, the PCB undergoes thorough inspection and testing to ensure that it meets the required specifications. Common inspection and testing methods include:
- Visual inspection
- Automated Optical Inspection (AOI)
- X-ray inspection
- In-Circuit Testing (ICT)
- Functional testing
Frequently Asked Questions (FAQ)
-
What is the difference between a single-layer and a multi-layer PCB?
A Single-Layer PCB has conductive traces on one side only, while a multi-layer PCB has conductive traces on multiple internal layers, sandwiched between insulating layers. Multi-layer PCBs offer higher component density and improved signal integrity compared to single-layer PCBs. -
What is the purpose of a solder mask on a PCB?
A solder mask is a protective coating that covers the copper traces on a PCB, leaving only the areas intended for soldering exposed. The solder mask improves the PCB’s insulation properties and protects the copper from oxidation and damage during handling. -
What is the difference between SMT and through-hole assembly?
Surface Mount Technology (SMT) is a method of assembling electronic components onto the surface of a PCB without the need for through-hole mounting. Through-hole assembly involves inserting components into holes drilled in the PCB and soldering them in place. SMT offers higher component density and improved performance compared to through-hole assembly. -
What is the purpose of a reflow oven in PCB assembly?
A reflow oven is used in SMT assembly to melt the solder paste and create a permanent bond between the components and the PCB. The reflow soldering process is carefully controlled to ensure that the solder joints are formed correctly and that the components are not damaged by excessive heat. -
What are some common inspection and testing methods for PCBs?
Common inspection and testing methods for PCBs include visual inspection, Automated Optical Inspection (AOI), X-ray inspection, In-Circuit Testing (ICT), and functional testing. These methods ensure that the PCB meets the required specifications and functions as intended.
Conclusion
PCB manufacturing is a complex process that involves multiple steps, from design to assembly. Understanding the various aspects of PCB manufacturing is essential for creating high-quality, reliable electronic products. By following best practices in PCB design, fabrication, and assembly, manufacturers can minimize the risk of defects and ensure that their products meet the required specifications.
As electronic devices continue to become more complex and compact, the importance of advanced PCB manufacturing techniques will only increase. Staying up-to-date with the latest technologies and processes is crucial for companies looking to stay competitive in the rapidly evolving electronics industry.
No responses yet