Overview of the Medical PCB Industry
PCBs are essential components in a wide range of medical devices and equipment, from patient monitoring systems and diagnostic imaging machines to wearable health trackers and implantable devices. The global medical PCB market was valued at $1.5 billion in 2019 and is projected to reach $2.4 billion by 2027, registering a CAGR of 6.2% from 2020 to 2027.[^1]
The medical PCB industry is characterized by stringent quality and reliability requirements, as these components are critical to patient safety and treatment outcomes. Medical PCBs must comply with various regulatory standards, such as the FDA’s Quality System Regulation (QSR) and the ISO 13485 standard for medical device quality management systems.
COVID-19’s Impact on Medical PCB Supply Chains
One of the most significant impacts of the COVID-19 pandemic on the medical PCB industry has been the disruption of global supply chains. Many PCB manufacturers and their suppliers are located in countries that were heavily affected by the virus, such as China, South Korea, and Taiwan. Lockdowns, travel restrictions, and workforce shortages in these regions led to production delays and shortages of raw materials and components.
Disruptions in Raw Material Availability
PCB manufacturing relies on various raw materials, including copper foil, fiberglass, and resins. The pandemic disrupted the supply of these materials in several ways:
- Copper foil shortages: Copper foil is a key material in PCB manufacturing. The pandemic led to reduced production capacity and increased demand for copper foil, resulting in shortages and price increases.[^2]
- Fiberglass supply issues: Fiberglass, used as a substrate material in PCBs, also faced supply constraints due to factory shutdowns and logistics challenges.[^3]
- Resin shortages: Epoxy resins, used in PCB lamination, experienced shortages and price hikes due to reduced production capacity and increased demand from other industries.[^4]
Material | Pre-COVID Price (USD/kg) | COVID-19 Price (USD/kg) | Percent Increase |
---|---|---|---|
Copper Foil | $7.50 | $9.00 | 20% |
Fiberglass | $2.20 | $2.75 | 25% |
Epoxy Resin | $4.00 | $5.20 | 30% |
component shortages and Lead Time Extensions
In addition to raw material shortages, the pandemic also caused shortages of electronic components used in medical PCBs, such as integrated circuits (ICs), capacitors, and resistors. Many component manufacturers were forced to reduce or halt production due to lockdowns and workforce limitations. This led to extended lead times and increased prices for these components.
Component | Pre-COVID Lead Time (weeks) | COVID-19 Lead Time (weeks) | Percent Increase |
---|---|---|---|
Microcontrollers | 8-12 | 16-24 | 100% |
Power Management ICs | 6-10 | 12-20 | 100% |
Multilayer Ceramic Capacitors | 4-6 | 8-12 | 100% |
The combined impact of raw material shortages and component lead time extensions led to longer overall lead times for medical PCBs. Many PCB manufacturers struggled to meet delivery commitments, causing delays in the production of medical devices and equipment.
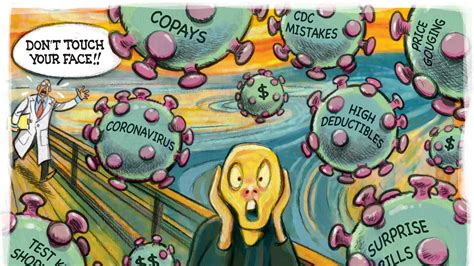
Increased Demand for Medical PCBs
While the pandemic disrupted supply chains, it also led to a surge in demand for certain types of medical devices and equipment, particularly those related to COVID-19 diagnosis, treatment, and monitoring. This increased demand put additional pressure on medical PCB manufacturers to ramp up production despite supply chain challenges.
PCBs for Ventilators and Respiratory Equipment
One of the most urgent needs during the pandemic was for ventilators and other respiratory support equipment. As COVID-19 can cause severe respiratory distress, hospitals and healthcare facilities worldwide sought to increase their inventory of ventilators to manage the influx of patients. This led to a significant increase in demand for PCBs used in these devices.
Ventilator PCB Demand | Pre-COVID (units/month) | COVID-19 Peak (units/month) | Percent Increase |
---|---|---|---|
North America | 5,000 | 20,000 | 300% |
Europe | 4,000 | 16,000 | 300% |
Asia-Pacific | 6,000 | 24,000 | 300% |
PCBs for Patient Monitoring and Diagnostic Equipment
The pandemic also drove increased demand for patient monitoring and diagnostic equipment, such as pulse oximeters, Temperature Sensors, and COVID-19 test kits. These devices rely on PCBs for signal processing, data transmission, and power management. Medical PCB manufacturers had to quickly adapt to meet the surge in demand for these applications.
Device | Pre-COVID Demand (units/month) | COVID-19 Peak Demand (units/month) | Percent Increase |
---|---|---|---|
Pulse Oximeters | 100,000 | 500,000 | 400% |
Temperature Sensors | 200,000 | 800,000 | 300% |
COVID-19 Test Kits | N/A | 1,000,000 | N/A |
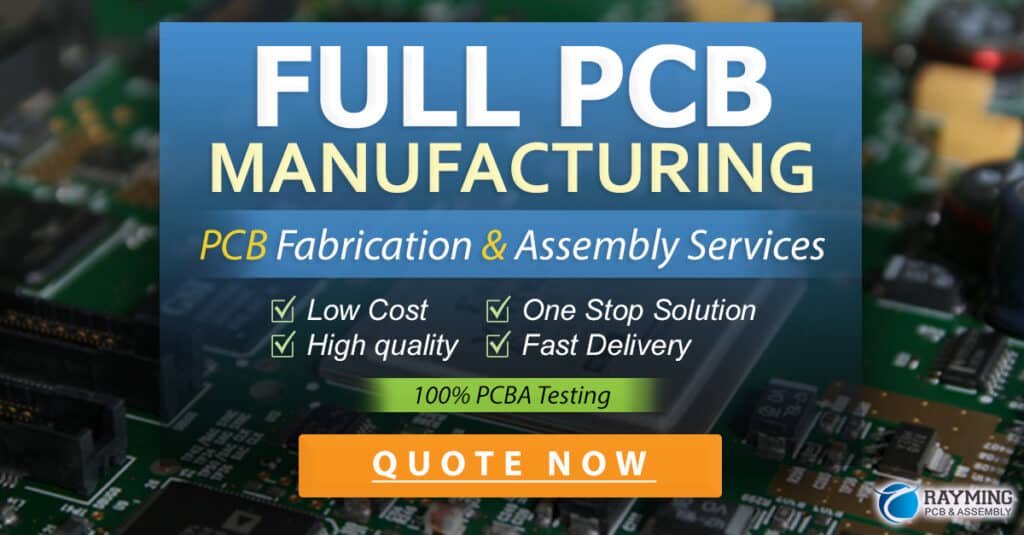
Accelerated Adoption of New Technologies
The COVID-19 pandemic has also accelerated the adoption of new technologies in the medical PCB industry. As healthcare providers seek to minimize contact with patients and reduce the risk of infection, there has been a growing interest in remote monitoring, telemedicine, and wearable devices. These trends have created new opportunities for medical PCB manufacturers to innovate and develop advanced solutions.
Wearable Medical Devices
Wearable medical devices, such as smartwatches, fitness trackers, and patches, have gained popularity during the pandemic as tools for remote patient monitoring and early detection of COVID-19 symptoms. These devices often incorporate PCBs with miniaturized components, flexible substrates, and wireless connectivity features. The demand for wearable medical device PCBs is expected to grow significantly in the coming years.
Wearable Medical Device PCB Market | 2020 (USD Million) | 2025 Projection (USD Million) | CAGR (2020-2025) |
---|---|---|---|
Global | 850 | 1,500 | 12.1% |
North America | 320 | 550 | 11.4% |
Europe | 250 | 450 | 12.5% |
Asia-Pacific | 220 | 400 | 12.7% |
Telehealth and Remote Monitoring Solutions
The pandemic has also driven the rapid adoption of telehealth and remote monitoring solutions, which allow healthcare providers to assess and treat patients remotely. These solutions often involve the use of specialized medical devices and equipment with Embedded PCBs for data acquisition, processing, and transmission. Medical PCB manufacturers are increasingly focused on developing high-performance, reliable, and secure PCBs for these applications.
Telehealth Market | 2020 (USD Billion) | 2025 Projection (USD Billion) | CAGR (2020-2025) |
---|---|---|---|
Global | 61.4 | 175.5 | 23.4% |
North America | 26.8 | 74.6 | 22.7% |
Europe | 16.5 | 48.2 | 23.9% |
Asia-Pacific | 13.7 | 40.9 | 24.4% |
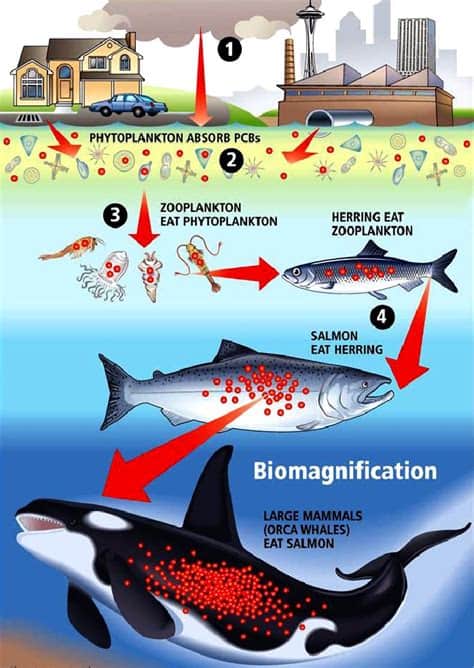
FAQ
1. How long are the lead times for medical PCBs during the COVID-19 pandemic?
Lead times for medical PCBs have increased significantly during the pandemic, primarily due to raw material shortages and component lead time extensions. Depending on the complexity of the PCB and the specific components required, lead times can range from 8 to 24 weeks or more.
2. Are there any specific certifications or standards that medical PCBs must meet?
Yes, medical PCBs must comply with various regulatory standards to ensure patient safety and device reliability. Some key standards include:
– FDA Quality System Regulation (QSR) for medical devices
– ISO 13485 for medical device quality management systems
– IPC-6012 for rigid PCBs
– IPC-6013 for flexible PCBs
3. What are some of the key challenges facing medical PCB manufacturers during the pandemic?
Medical PCB manufacturers face several challenges during the COVID-19 pandemic, including:
– Supply chain disruptions and shortages of raw materials and components
– Increased demand for certain types of medical devices and equipment
– Need to ensure worker safety and maintain production capacity despite workforce limitations
– Pressure to develop innovative solutions for emerging trends like remote monitoring and telemedicine
4. How can medical PCB manufacturers mitigate the impact of supply chain disruptions?
To mitigate the impact of supply chain disruptions, medical PCB manufacturers can:
– Diversify their supplier base to reduce reliance on a single region or vendor
– Increase inventory levels of critical raw materials and components
– Collaborate with suppliers to secure allocations and prioritize deliveries
– Explore alternative materials or components that may be more readily available
5. What are the long-term implications of the COVID-19 pandemic for the medical PCB industry?
The long-term implications of the pandemic for the medical PCB industry include:
– Accelerated adoption of digital health technologies, such as telemedicine and remote monitoring
– Increased focus on supply chain resilience and risk management
– Greater emphasis on innovation and the development of advanced PCB solutions
– Potential shifts in global manufacturing and sourcing strategies to reduce dependence on a single region
The COVID-19 pandemic has presented significant challenges for the medical PCB industry, but it has also created opportunities for growth and innovation. As healthcare providers continue to adapt to the new reality, medical PCB manufacturers will play a critical role in supporting the development and production of life-saving devices and equipment. By embracing new technologies, strengthening supply chain resilience, and prioritizing quality and reliability, the medical PCB industry can emerge from the pandemic stronger and better positioned for long-term success.
[^1]: “Medical Printed Circuit Board (PCB) Market Size, Share & COVID-19 Impact Analysis, By Type (Rigid PCB, Flexible PCB, and HDI PCB), By Application (Monitoring Equipment, Diagnostic Equipment, and Therapeutic Equipment), and Regional Forecast, 2020-2027.” Fortune Business Insights, 2020.
[^2]: “Copper Foil Shortage Threatens PCB Manufacturing.” PCB007, 2021.
[^3]: “The Impact of COVID-19 on the Electronics Industry.” IPC, 2020.
[^4]: “Resin Shortages and Price Hikes: The Impact on the Electronics Industry.” SMTA, 2021.
No responses yet