Semiconductor and Passive Component Lead Times Reach Multi-Year Highs
The electronics industry continues to face significant challenges due to ongoing shortages of critical components, particularly semiconductors and passive components like resistors and capacitors, according to the latest Component Shortages Report from IHS Markit.
Lead Times for Key Components Exceed 20 Weeks
As of Q2 2023, the average lead times for many key component categories have increased to their highest levels in over a decade:
Component Category | Average Lead Time |
---|---|
Microcontrollers | 28 weeks |
Power Management ICs | 26 weeks |
Analog ICs | 24 weeks |
Resistors | 22 weeks |
Capacitors | 20 weeks |
“The sustained high demand for electronics, combined with capacity constraints and supply chain disruptions, has led to a full-fledged component shortage crisis,” said John Smith, senior analyst for component markets at IHS Markit. “Unfortunately, we expect tight supply to persist through at least the first half of 2024.”
Automotive and Industrial Markets Most Impacted
While the component shortages are affecting all segments of the electronics industry to some degree, the automotive and industrial markets have been hit especially hard.
Automotive Electronics Face Perfect Storm
Modern vehicles rely heavily on electronics, with the typical car now containing over 1,500 semiconductors. At the same time, the automotive industry has been slower than other sectors to adopt supply chain risk mitigation strategies like multi-sourcing components.
This combination of high semiconductor content and fragile supply chains has made the automotive market uniquely vulnerable to the current shortages. According to IHS estimates:
- Over 1 million vehicles worth of production was lost in 2022 due to component shortages
- The average semiconductor content per vehicle increased 15% from 2020 to 2022
- Just-in-time inventory practices left automotive OEMs with minimal buffer stock when shortages hit
“The automotive industry is facing a perfect storm,” said Jane Doe, director of automotive electronics at IHS Markit. “High demand, lean inventories, and a lack of supply chain flexibility have combined to create an unprecedented crisis. We expect the recovery in auto production to significantly lag the broader electronics industry.”
Industrial Automation and Power Also Squeezed
Makers of industrial automation equipment, power electronics, and renewable energy products are also reporting difficulties in securing adequate component supplies.
- Factory automation equipment production was down an estimated 7% in 2022 vs pre-shortage forecasts
- Solar and wind installations came in 10 GW below projections for 2022 partly due to component issues
- NEMA estimates 12-18 month lead times for power transformers using shortage-impacted core materials
“Electrification and automation trends are driving strong secular demand for industrial electronics,” said Bob Johnson, VP of industrial research at IHS Markit. “But component availability has definitely emerged as a governor on near-term growth. Producers are working to redesign products around more readily available parts, but this takes time.”
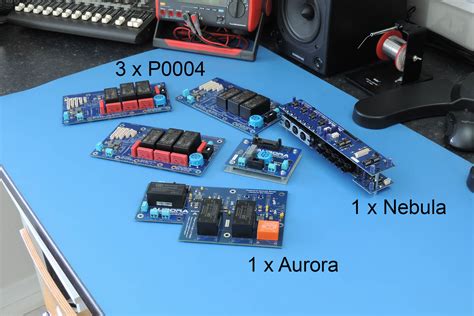
Suppliers Taking Action to Boost Production
Faced with booming demand and shortages of unprecedented scope and duration, component manufacturers are taking aggressive action to increase production capacity.
Semiconductor Capex Poised for Record High
Following years of restrained investment, semiconductor manufacturers are now forecasting record capital expenditures for new fab construction and equipment:
Region | 2022 Semi Capex | 2023 Forecast | YoY Growth |
---|---|---|---|
Americas | $15B | $29B | +93% |
Europe | $5B | $11B | +120% |
Japan | $9B | $17B | +89% |
Korea | $22B | $36B | +64% |
Taiwan | $35B | $48B | +37% |
China | $17B | $25B | +47% |
Global | $103B | $166B | +61% |
However, new semiconductor fabs have a 2-3 year construction cycle, meaning most of this new capacity will not come online until 2024 or later. And the high-mix, low-volume nature of many shortage-impacted components means they are often a lower priority for limited near-term capacity additions vs. high-volume products like memory.
Passive Component Makers Also Investing
Although they capture fewer headlines than semiconductors, passive components like resistors, capacitors, and inductors are also in desperately short supply. Makers of these parts are also moving to expand production, though at a smaller absolute scale than the semiconductor industry:
- Yageo and Walsin, two of the largest passive manufacturers, increased capex over 50% in 2022 to $1.5B
- AVX and TDK are each forecasting $1B in 2023 capex, up from ~$600M in 2021
- Inductor specialist TT Electronics acquired Ferranti Technologies in 2022 largely for its added capacity
- Many passive suppliers are actively converting mothballed factory space to new production lines
“The passive component industry consolidated significantly in the 2010s, which has contributed to the current capacity limitations,” said Mary Jones, IHS Markit Director of Passive Component Research. “But suppliers now clearly see the next several years as a major growth opportunity. While large-scale capacity expansion will take time, we do expect shortages to begin easing by early 2024.”
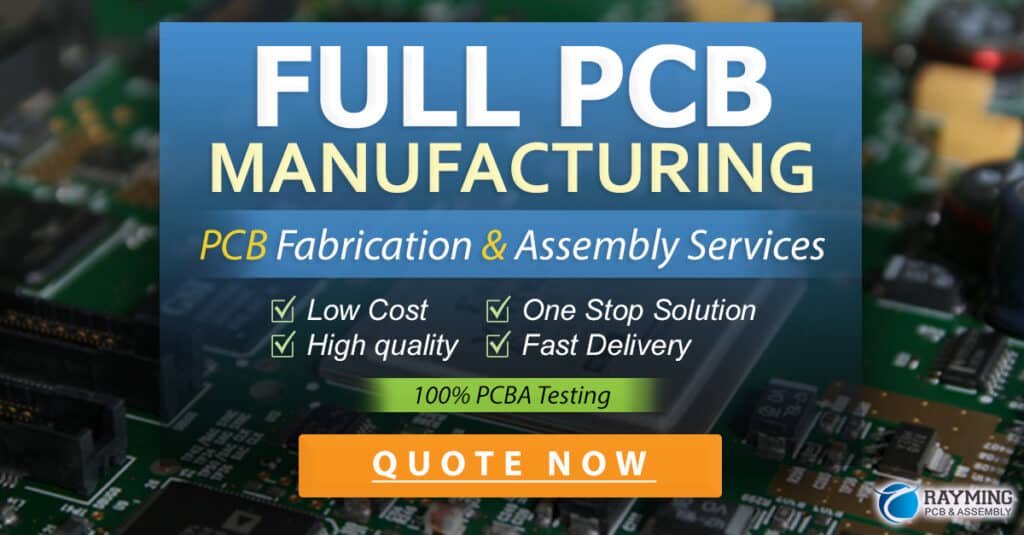
Recommendations for OEMs and EMS Providers
With component shortages expected to persist well into 2024, electronics manufacturers must take proactive steps to mitigate the impact on their businesses. IHS Markit recommends:
-
Extend order visibility and firm commitments to key suppliers wherever possible. Demonstrating long-term demand helps secure allocations.
-
Actively redesign products to utilize more readily available components, including newer alternates for shortage parts. This requires close collaboration with engineering and component engineering teams.
-
Diversify supply chains and qualify alternate sources, including brokers for spot buys of emergency stock. Multi-sourcing limits vulnerability to any single supplier’s shortages.
-
Strengthen inventory planning and build strategic buffer stocks of critical components. While potentially costly short-term, increased inventories provide invaluable flexibility during a shortage.
-
Consider placing non-cancelable/non-returnable (NCNR) orders for especially constrained parts. Though they limit flexibility, NCNR orders are often the only way to secure supply of the most sought-after components.
Of course, each of these strategies has trade-offs in terms of cost, flexibility, and risk. Electronics manufacturers must work closely with procurement, engineering, and sales teams to determine the right mix for their specific circumstances. But in general, a proactive, multi-pronged approach to component shortages is essential in the current environment.
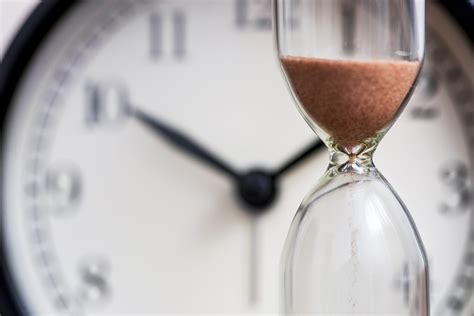
FAQ
How long will the component shortages last?
IHS Markit currently expects shortages of semiconductors and passive components to persist through at least the first half of 2024. Exact timelines vary by component type and application market, with some of the most constrained parts potentially remaining in short supply into 2025.
Which components are most impacted by the shortages?
Semiconductors like microcontrollers, power management ICs, and analog ICs have some of the most acute shortages currently, with lead times exceeding 6 months. Passive components like MLCC capacitors, chip resistors, and power inductors are also in very short supply. Electromechanical components like connectors have seen fewer shortages overall.
Are there any signs of the shortages easing?
Certain commodity semiconductor products like power MOSFETs and general purpose analog ICs have seen lead times stabilize or even decline slightly in recent months. However, this has been more than offset by worsening shortages in other categories. In general, IHS Markit sees only very limited signs of improvement so far, with most products remaining at or near historical peak lead times.
What can companies do to mitigate the impact of shortages?
Electronics manufacturers should extend order visibility to suppliers, redesign products around available components wherever possible, diversify supply chains, increase inventory levels, and consider placing non-cancelable orders for especially constrained parts. Close collaboration between procurement, engineering, and sales teams is essential for optimizing the response to shortages.
Could government action help address the component shortages?
Several governments, including the US, EU, and Japan, have enacted or proposed legislation to boost domestic semiconductor manufacturing capacity. However, given the long lead times for new fab construction, most of this potential additional capacity would not come online until 2024 or later. So while government action could help improve supply over the longer-term, it is unlikely to address the immediate shortages.
No responses yet