Introduction to Flexible PCB LED Technology
Flexible PCB LED technology has revolutionized the lighting industry by offering a versatile and adaptable solution for various applications. Unlike traditional Rigid PCBs, flexible PCBs can bend and conform to different shapes and surfaces, making them ideal for creating unique and dynamic lighting designs. In this article, we will explore the key aspects of flexible PCB LED technology and provide a comprehensive guide on how to turn your flexible PCB LED strip design into reality.
What is a Flexible PCB LED?
A flexible PCB LED is a type of printed circuit board that uses a flexible substrate material, such as polyimide or polyester, instead of the traditional rigid FR-4 substrate. This flexibility allows the PCB to bend and twist without damaging the electronic components or the connections between them. LEDs are mounted on the flexible PCB, creating a light strip that can be easily shaped and molded to fit various applications.
Advantages of Flexible PCB LED Technology
Flexible PCB LED technology offers several advantages over traditional rigid PCBs:
- Versatility: Flexible PCBs can be bent and shaped to fit various surfaces and designs, making them suitable for a wide range of applications.
- Space-saving: The thin and flexible nature of flexible PCBs allows for more compact designs, saving valuable space in electronic devices.
- Durability: Flexible PCBs are resistant to vibrations and shocks, making them more durable than rigid PCBs in certain applications.
- Cost-effective: The manufacturing process for flexible PCBs is often more cost-effective than rigid PCBs, especially for high-volume production.
Designing Your Flexible PCB LED Strip
Determining Your Application Requirements
Before starting your flexible PCB LED strip design, it is crucial to determine your application requirements. Consider the following factors:
- Lighting purpose: What is the primary purpose of your LED strip? Is it for decorative lighting, task lighting, or backlighting?
- Dimensions: What are the desired dimensions of your LED strip, including length, width, and thickness?
- Flexibility: How much flexibility does your application require? Will the LED strip need to bend around sharp corners or conform to curved surfaces?
- Power consumption: What is the expected power consumption of your LED strip, and how will it be powered?
Choosing the Right Components
Once you have determined your application requirements, the next step is to choose the right components for your flexible PCB LED strip. The main components to consider are:
- LEDs: Select the appropriate type of LEDs based on factors such as color, brightness, viewing angle, and power consumption. Common types include SMD LEDs and COB LEDs.
- Flexible PCB substrate: Choose a suitable flexible PCB substrate material that meets your application requirements. Polyimide and polyester are popular choices for their flexibility and durability.
- Connectors: Determine the type of connectors needed for your LED strip, such as wire-to-board connectors or board-to-board connectors.
- Power supply: Select a power supply that can provide the necessary voltage and current for your LED strip. Consider factors such as efficiency, size, and cost.
Creating Your Circuit Design
With your components selected, the next step is to create your circuit design. Use a PCB design software to layout your components and create the necessary connections. Keep in mind the following considerations:
- Component placement: Arrange your components in a way that optimizes space and minimizes the length of connections.
- Trace width: Ensure that your trace widths are appropriate for the current flowing through them to avoid overheating and potential failures.
- Flexibility: Design your circuit to accommodate the desired level of flexibility, avoiding sharp bends or stress points that could damage the components or connections.
Prototyping and Testing
Before finalizing your design, it is essential to create a prototype and test it thoroughly. This process allows you to identify any potential issues and make necessary adjustments before moving into full-scale production. Consider the following steps:
- Create a prototype: Manufacture a small batch of your flexible PCB LED strip based on your circuit design.
- Functional testing: Test your prototype to ensure that it functions as intended, including lighting performance, power consumption, and flexibility.
- Stress testing: Subject your prototype to various stress tests, such as bending, twisting, and temperature cycling, to evaluate its durability and reliability.
- Revisions: Based on the results of your testing, make any necessary revisions to your design to improve performance and reliability.
Manufacturing Your Flexible PCB LED Strip
Choosing a Manufacturing Partner
Once your design is finalized and tested, the next step is to choose a manufacturing partner to produce your flexible PCB LED strip. When selecting a manufacturer, consider the following factors:
- Experience: Look for a manufacturer with experience in producing flexible PCBs and LED strips to ensure they have the necessary expertise and capabilities.
- Quality control: Choose a manufacturer with robust quality control processes to ensure consistent and reliable production.
- Lead time: Consider the manufacturer’s lead time and production capacity to ensure they can meet your demand and delivery requirements.
- Cost: Evaluate the manufacturer’s pricing and compare it with other options to ensure you are getting a competitive price without compromising quality.
Manufacturing Process
The manufacturing process for flexible PCB LED strips typically involves the following steps:
- PCB fabrication: The flexible PCB substrate is manufactured based on your circuit design, including etching, drilling, and plating processes.
- Component placement: The LEDs and other components are placed on the flexible PCB using automated pick-and-place machines.
- Soldering: The components are soldered onto the flexible PCB using reflow or wave soldering processes.
- Cutting and finishing: The flexible PCB LED strip is cut to the desired length and any necessary finishing processes, such as adding connectors or encapsulation, are performed.
- Quality control: The finished product undergoes various quality control tests to ensure it meets the required specifications and performance standards.
Quality Control and Testing
To ensure the quality and reliability of your flexible PCB LED strip, it is essential to implement thorough quality control and testing procedures throughout the manufacturing process. This may include:
- Visual inspection: Visually inspecting the PCBs and components for any defects or irregularities.
- Electrical testing: Testing the electrical properties of the LED strip, such as voltage, current, and resistance, to ensure they meet the specified requirements.
- Functional testing: Testing the LED strip’s lighting performance, including brightness, color consistency, and uniformity.
- Environmental testing: Subjecting the LED strip to various environmental conditions, such as temperature, humidity, and vibration, to evaluate its durability and reliability.
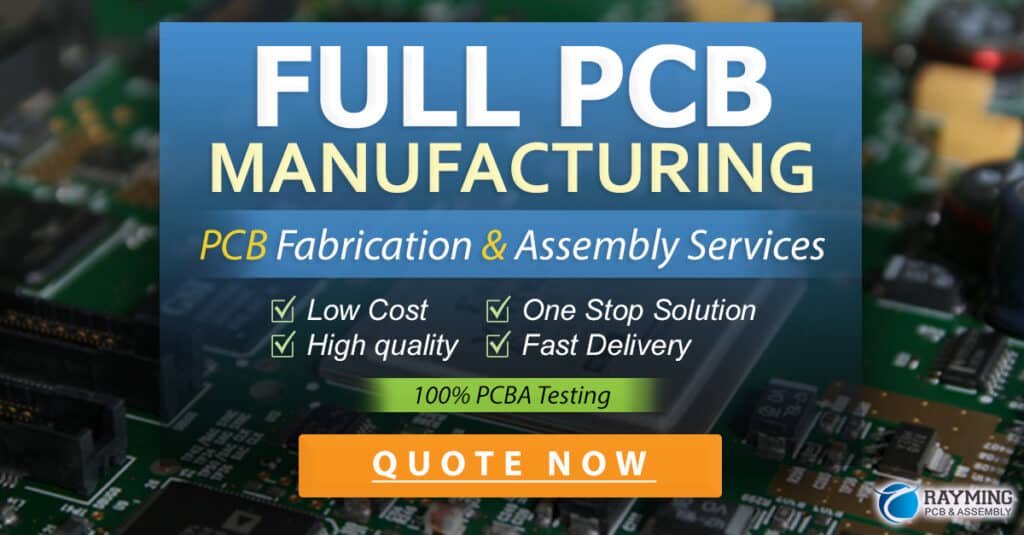
Applications of Flexible PCB LED Strips
Flexible PCB LED strips have a wide range of applications across various industries, including:
- Automotive: Used for interior and exterior lighting, such as ambient lighting, dashboard lighting, and headlights.
- Architecture and construction: Used for decorative lighting, accent lighting, and backlighting in buildings and structures.
- Consumer electronics: Used for backlighting in displays, keyboards, and other electronic devices.
- Signs and displays: Used for illuminated signs, digital displays, and advertising boards.
- Wearable Technology: Used for lighting in smart clothing, accessories, and medical devices.
Future Trends in Flexible PCB LED Technology
As technology continues to advance, we can expect to see several trends in flexible PCB LED technology, including:
- Increased efficiency: Advancements in LED technology will lead to higher lumens per watt, resulting in more energy-efficient LED strips.
- Improved color rendering: The development of new LED phosphors and color mixing techniques will enable LED strips to produce more accurate and vibrant colors.
- Thinner and more flexible designs: Advances in materials science will lead to thinner and more flexible PCB Substrates, allowing for even more versatile and adaptable LED strip designs.
- Integration with smart technology: The integration of flexible PCB LED strips with smart sensors, controllers, and wireless connectivity will enable more intelligent and automated lighting solutions.
Frequently Asked Questions (FAQ)
-
What is the difference between flexible and rigid PCBs?
Flexible PCBs use a flexible substrate material, such as polyimide or polyester, which allows them to bend and conform to different shapes and surfaces. Rigid PCBs, on the other hand, use a rigid substrate material, such as FR-4, which makes them more suitable for applications that require a stable and fixed structure. -
Can flexible PCB LED strips be cut to size?
Yes, most flexible PCB LED strips can be cut to the desired length using scissors or a cutting tool. However, it is essential to cut the strip along the designated cutting lines to avoid damaging the components or connections. -
How do I power my flexible PCB LED strip?
Flexible PCB LED strips typically require a DC Power Supply that matches the voltage and current requirements of the LEDs. The power supply can be connected to the LED strip using wire-to-board connectors or soldered directly to the PCB. -
What is the lifespan of a flexible PCB LED strip?
The lifespan of a flexible PCB LED strip depends on various factors, such as the quality of the components, the operating conditions, and the manufacturing process. High-quality LED strips can last up to 50,000 hours or more when operated within their specified parameters. -
Can flexible PCB LED strips be waterproofed?
Yes, flexible PCB LED strips can be waterproofed using various methods, such as conformal coating, encapsulation, or using waterproof housings. Waterproofing is essential for applications where the LED strip may be exposed to moisture or humidity, such as outdoor lighting or marine applications.
Application | Advantages of Flexible PCB LED Strips |
---|---|
Automotive | Versatile interior and exterior lighting, space-saving, durable |
Architecture | Decorative and accent lighting, adaptable to various surfaces, energy-efficient |
Consumer Electronics | Thin and compact backlighting, cost-effective, easy to integrate |
Signs and Displays | Bright and uniform illumination, flexible designs, long lifespan |
Wearable Technology | Lightweight and conformable, low power consumption, integrates with sensors |
Conclusion
Flexible PCB LED technology offers a versatile and adaptable solution for creating innovative and dynamic lighting designs. By understanding the key aspects of flexible PCB LED strips, from design and manufacturing to quality control and testing, you can turn your vision into reality. As technology continues to advance, we can expect to see even more exciting applications and trends in flexible PCB LED technology, leading to more efficient, intelligent, and visually stunning lighting solutions.
No responses yet