Understanding High-Frequency Effects
Transmission Line Effects
At RF and microwave frequencies, PCB traces no longer behave as simple electrical connections but rather as transmission lines. The characteristic impedance of these transmission lines becomes a critical design parameter, as impedance mismatches can lead to signal reflections, degraded signal integrity, and reduced power transfer efficiency.
The characteristic impedance of a microstrip transmission line, a common PCB trace geometry, is given by:
Z₀ = 87 / √(ε_r + 1.41) * ln(5.98h / (0.8w + t))
Where:
– Z₀ is the characteristic impedance in ohms
– ε_r is the relative dielectric constant of the PCB substrate
– h is the substrate thickness
– w is the trace width
– t is the trace thickness
To maintain a consistent impedance throughout the signal path, designers must carefully control the trace geometry and substrate properties. Common target impedances for RF and microwave systems include 50Ω, 75Ω, and 100Ω.
Dielectric Losses
As frequencies increase, the dielectric losses in the PCB substrate become more significant. These losses are caused by the interaction between the electromagnetic fields and the substrate material, resulting in signal attenuation and reduced quality factor (Q) of passive components.
The dielectric loss tangent (tan δ) is a key parameter that quantifies the loss in a substrate material. Lower loss tangents are desirable for RF and microwave applications. Some common PCB substrate materials and their properties are shown in the table below:
Material | Dielectric Constant (ε_r) | Loss Tangent (tan δ) @ 10 GHz |
---|---|---|
FR-4 | 4.3-4.7 | 0.02 |
Rogers RO4003C | 3.38 | 0.0027 |
Rogers RT/duroid 5880 | 2.20 | 0.0009 |
PTFE (Teflon) | 2.1 | 0.0002 |
Choosing a low-loss substrate is essential for minimizing dielectric losses and maintaining signal integrity in RF and Microwave PCBs.
Skin Effect
The skin effect is a phenomenon where high-frequency currents tend to flow primarily on the surface of a conductor rather than uniformly throughout its cross-section. This effective reduction in conductor cross-sectional area leads to increased resistance and losses at higher frequencies.
The skin depth (δ) is the distance from the surface of a conductor at which the current density has decreased to 1/e (about 37%) of its value at the surface. It is given by:
δ = √(ρ / (π * f * μ))
Where:
– ρ is the resistivity of the conductor material
– f is the frequency
– μ is the permeability of the conductor material
To minimize skin effect losses, designers should use wider traces, thicker copper layers, or multiple parallel traces for high-current paths. Additionally, using conductors with lower resistivity, such as copper or silver, can help reduce losses.
PCB Layout Considerations
Grounding and Shielding
Proper grounding and shielding techniques are crucial for maintaining signal integrity and reducing electromagnetic interference (EMI) in RF and microwave PCBs. A solid, low-impedance ground plane is essential for providing a stable reference for signals and minimizing ground loops.
Techniques for effective grounding and shielding include:
- Using a continuous ground plane on one or more layers of the PCB
- Connecting ground planes on different layers using multiple vias
- Placing ground vias near signal vias to reduce inductance
- Using guard rings or via fences around sensitive traces or components
- Implementing compartmentalized shielding for isolating high-frequency sections of the design
By carefully designing the grounding and shielding structures, designers can minimize unwanted coupling between signals and reduce the impact of external EMI sources.
Component Placement and Routing
The placement and routing of components in an RF or microwave PCB can significantly impact performance. Designers should follow these guidelines to optimize the layout:
- Place components to minimize the length of high-frequency signal paths
- Route sensitive traces away from potential sources of interference, such as power supplies or digital circuits
- Avoid sharp bends or discontinuities in high-frequency traces to minimize reflections
- Use mitered bends or curved traces to reduce the impact of discontinuities
- Maintain consistent trace impedance by controlling trace geometry and avoiding abrupt changes in width
- Provide adequate spacing between components and traces to minimize coupling and crosstalk
By carefully considering component placement and routing, designers can minimize signal integrity issues and optimize the overall performance of the RF or microwave circuit.
Impedance Matching and Terminations
Impedance matching is essential for maximizing power transfer and minimizing signal reflections in RF and microwave circuits. Designers must ensure that the impedances of the source, transmission line, and load are matched to prevent standing waves and signal distortion.
Common techniques for impedance matching include:
- Using quarter-wave transformers to match different impedance levels
- Implementing stub matching networks, such as open or short stubs
- Employing lumped element matching networks with capacitors and inductors
- Utilizing tapered transmission lines for broadband impedance matching
In addition to matching, proper termination of transmission lines is crucial to prevent reflections. Common termination techniques include:
- Parallel resistive termination: A resistor is placed in parallel with the load, matching the characteristic impedance of the transmission line.
- Series resistive termination: A resistor is placed in series with the source, matching the characteristic impedance of the transmission line.
- RC termination: A resistor and capacitor network is used to provide a broadband termination and reduce reflections.
By implementing appropriate impedance matching and termination techniques, designers can ensure optimal signal integrity and power transfer in RF and microwave PCBs.
Simulation and Verification
Electromagnetic Simulation
Electromagnetic (EM) simulation tools play a crucial role in the design and verification of RF and microwave PCBs. These tools allow designers to model the electromagnetic behavior of the PCB and its components, helping to identify potential issues and optimize performance before fabrication.
Common EM simulation techniques include:
- Method of Moments (MoM): A numerical technique for solving Maxwell’s equations in the frequency domain, well-suited for simulating planar structures like PCBs.
- Finite Element Method (FEM): A method for solving partial differential equations by dividing the problem domain into smaller elements, useful for modeling complex 3D structures.
- Finite-Difference Time-Domain (FDTD): A time-domain method that discretizes Maxwell’s equations in both space and time, allowing for broadband simulations.
EM simulation tools can help designers analyze key performance metrics, such as S-parameters, insertion loss, return loss, and radiation patterns. By iterating on the design based on simulation results, designers can optimize the PCB layout for best performance before committing to fabrication.
Network Analysis and Measurement
Network analysis is essential for characterizing the performance of RF and microwave PCBs and components. Scattering parameters (S-parameters) are commonly used to describe the input-output relationships of multi-port networks, such as filters, amplifiers, and antennas.
S-parameters are typically measured using a vector network analyzer (VNA), which applies a known stimulus to the device under test (DUT) and measures the reflected and transmitted signals. By comparing the measured S-parameters to the simulated or desired values, designers can validate the performance of the PCB and identify any discrepancies.
Other important network parameters for RF and microwave PCBs include:
- Insertion loss: The attenuation of a signal as it passes through a device or transmission line.
- Return loss: The ratio of reflected power to incident power, indicating the degree of impedance mismatch.
- Group delay: The rate of change of phase with respect to frequency, a measure of signal dispersion.
- Isolation: The degree of signal leakage between adjacent channels or ports.
By carefully analyzing network parameters and comparing them to simulation results, designers can ensure that the RF or microwave PCB meets the required specifications and performance targets.
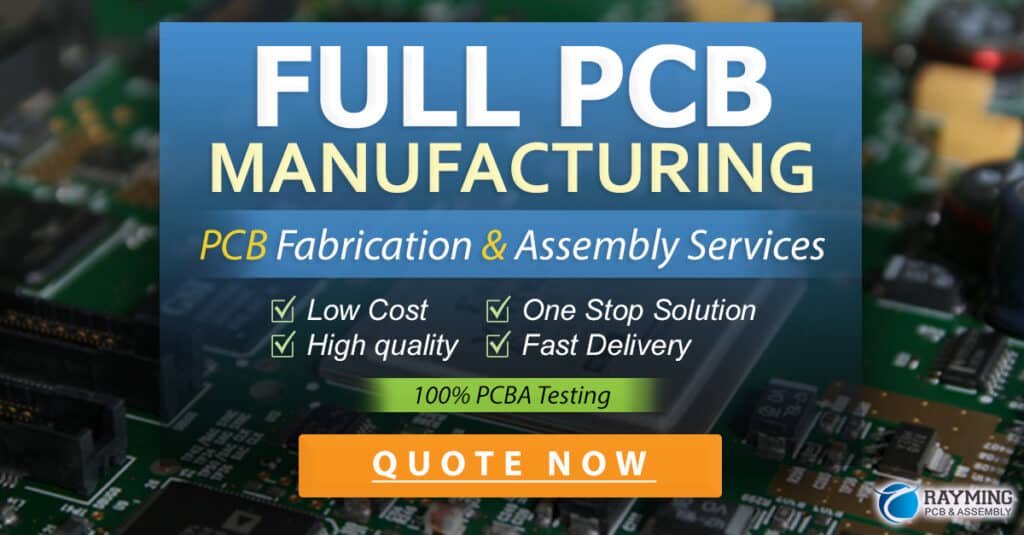
FAQ
Q1: What are some common PCB substrate materials for RF and microwave applications?
A1: Common PCB substrate materials for RF and microwave applications include:
– Rogers RO4000 series: Low-loss, high-frequency laminates with stable dielectric constants.
– PTFE (Teflon): Very low-loss material with excellent high-frequency performance.
– Ceramic-filled PTFE: Combines the low-loss properties of PTFE with the mechanical stability of ceramic fillers.
– Low-loss FR-4: A variant of the standard FR-4 material with lower dielectric losses at high frequencies.
Q2: What is the purpose of impedance matching in RF and microwave PCBs?
A2: Impedance matching is essential for ensuring maximum power transfer and minimizing signal reflections in RF and microwave circuits. When the impedances of the source, transmission line, and load are matched, energy can be efficiently transmitted without causing standing waves or signal distortion. Proper impedance matching helps to optimize signal integrity and overall system performance.
Q3: Why is grounding important in RF and microwave PCB design?
A3: Proper grounding is crucial in RF and microwave PCB design for several reasons:
1. It provides a low-impedance return path for high-frequency currents.
2. It helps to minimize ground loops and reduce electromagnetic interference (EMI).
3. It acts as a reference plane for controlling the characteristic impedance of transmission lines.
4. It helps to isolate sensitive circuits from potential sources of interference.
A well-designed grounding scheme is essential for maintaining signal integrity and reducing noise in RF and microwave PCBs.
Q4: What are some common challenges in RF and microwave PCB layout?
A4: Some common challenges in RF and microwave PCB layout include:
1. Maintaining consistent transmission line impedance: Trace geometry and substrate properties must be carefully controlled to ensure a uniform characteristic impedance.
2. Minimizing signal integrity issues: High-frequency effects like reflections, crosstalk, and losses can degrade signal quality and must be mitigated through proper layout techniques.
3. Managing electromagnetic interference (EMI): Careful component placement, routing, and shielding are necessary to minimize EMI and ensure compliance with regulatory standards.
4. Optimizing component placement and routing: High-frequency components must be placed and routed to minimize signal path lengths and avoid potential sources of interference.
Addressing these challenges requires a combination of experience, simulation tools, and adherence to best practices in RF and microwave PCB design.
Q5: What role does electromagnetic simulation play in RF and microwave PCB design?
A5: Electromagnetic (EM) simulation is a valuable tool for designing and verifying RF and microwave PCBs before fabrication. EM simulation allows designers to:
1. Model the electromagnetic behavior of the PCB and its components.
2. Analyze key performance metrics, such as S-parameters, insertion loss, and return loss.
3. Identify potential signal integrity issues and optimize the layout for best performance.
4. Verify compliance with design specifications and regulatory requirements.
By using EM simulation to iterate on the design and optimize performance, designers can save time and cost by catching issues early in the development process and avoiding multiple fabrication runs.
Conclusion
Designing PCBs for RF and microwave applications presents a unique set of challenges due to the high-frequency effects that come into play. From managing transmission line impedances and dielectric losses to optimizing component placement and routing, designers must consider a wide range of factors to ensure optimal performance and signal integrity.
By understanding the key concepts, such as skin effect, grounding, and impedance matching, and leveraging powerful simulation and measurement tools, designers can tackle these challenges and create robust, high-performance RF and microwave PCBs. Following best practices and staying up-to-date with the latest design techniques and technologies is essential for success in this demanding field.
As the demand for high-speed wireless communication and radar systems continues to grow, the importance of skilled RF and microwave PCB designers will only increase. By mastering the art and science of high-frequency PCB design, engineers can play a crucial role in driving innovation and enabling the next generation of wireless technologies.
No responses yet