What is a Relay Drive?
A relay drive is an electromechanical device that uses an electromagnet to open or close one or more sets of contacts. It allows a low power signal to control a higher power circuit, effectively acting as a switch. Relays are widely used in various electrical and electronic applications for switching, power control, and protection purposes.
The key components of a relay include:
- Electromagnet (coil)
- Armature
- Spring
- Contacts (normally open, normally closed, or changeover)
When current flows through the coil, it generates a magnetic field that attracts the armature. The armature is mechanically linked to the contacts, so when it moves, it either opens or closes the contacts, depending on the relay configuration.
How Does a Relay Drive Work?
The working principle of a relay drive can be broken down into the following steps:
-
Energizing the coil: When a voltage is applied to the relay coil, current flows through it, creating a magnetic field.
-
Attracting the armature: The magnetic field generated by the coil attracts the armature, which is usually made of a ferromagnetic material.
-
Switching the contacts: As the armature moves, it either closes or opens the contacts, depending on the relay’s configuration (normally open, normally closed, or changeover).
-
De-energizing the coil: When the voltage is removed from the coil, the magnetic field collapses, and the spring pulls the armature back to its original position, reversing the contact state.
The following table summarizes the relay drive’s operation:
Coil State | Normally Open (NO) Contacts | Normally Closed (NC) Contacts |
---|---|---|
Energized | Closed | Open |
De-energized | Open | Closed |
Types of Relay Drives
There are several types of relay drives, each with its own characteristics and applications:
Electromechanical Relays (EMRs)
Electromechanical relays are the most common type of relay drive. They use an electromagnet to actuate the contacts and are available in various sizes, contact configurations, and voltage/current ratings.
Advantages:
– Low cost
– Simple design
– Wide range of voltage and current ratings
– Galvanic isolation between control and load circuits
Disadvantages:
– Relatively slow switching speed
– Limited lifetime due to mechanical wear
– Susceptible to vibrations and shocks
– Requires more power to operate than solid-state relays
Solid-State Relays (SSRs)
Solid-state relays use semiconductor devices, such as thyristors or transistors, to switch the load. They offer faster switching speeds and longer lifetimes compared to electromechanical relays.
Advantages:
– Fast switching speed
– No mechanical wear, leading to longer lifetime
– Silent operation
– Resistant to vibrations and shocks
– Low power consumption for the control circuit
Disadvantages:
– Higher cost than electromechanical relays
– Limited voltage and current ratings
– No galvanic isolation (unless optically coupled)
– Susceptible to voltage transients and surges
Reed Relays
Reed relays use a pair of ferromagnetic contacts sealed in a glass envelope. The contacts are actuated by an external magnetic field, typically generated by a coil wound around the glass envelope.
Advantages:
– Fast switching speed
– Low contact resistance
– High isolation between control and load circuits
– Long lifetime due to sealed contacts
Disadvantages:
– Limited current carrying capacity
– Fragile glass envelope
– Susceptible to external magnetic fields
– Higher cost than electromechanical relays
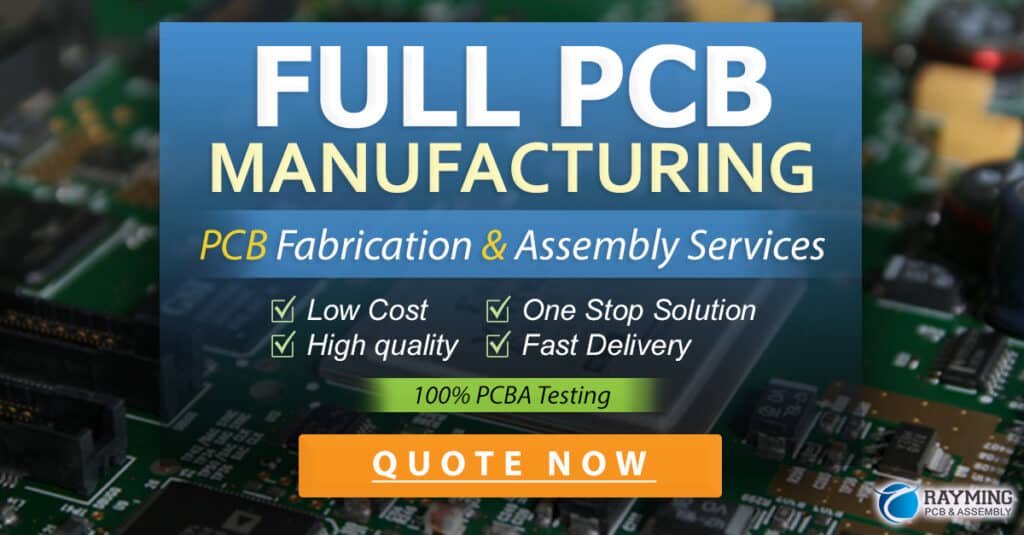
Relay Drive Application Circuits
Relay drives find applications in various electrical and electronic circuits. Some common application circuits include:
Motor Control
Relays are frequently used to control motors in industrial and automotive applications. They can switch high currents required by motors and provide isolation between the control and power circuits.
A simple motor control circuit using a relay drive is shown below:
(Insert a diagram of a relay-based motor control circuit)
Lighting Control
Relays can be used to control lighting circuits, allowing a low-voltage control signal to switch high-voltage lamps or LEDs.
A relay-based lighting control circuit is illustrated below:
(Insert a diagram of a relay-based lighting control circuit)
Power Switching
Relays are used in power switching applications to connect or disconnect loads from a power source. They can handle high currents and provide isolation between the control and load circuits.
A power switching circuit using a relay drive is shown below:
(Insert a diagram of a relay-based power switching circuit)
Automotive Applications
Relays are extensively used in automotive electrical systems for various purposes, such as controlling headlights, horn, starter motor, and other electrical loads.
An example of a relay-based automotive headlight control circuit is shown below:
(Insert a diagram of a relay-based automotive headlight control circuit)
Relay Drive Selection Considerations
When selecting a relay drive for a specific application, consider the following factors:
-
Voltage and current ratings: Ensure that the relay’s coil voltage and contact current ratings are compatible with the application’s requirements.
-
Contact configuration: Choose the appropriate contact configuration (normally open, normally closed, or changeover) based on the circuit’s needs.
-
Switching speed: Consider the required switching speed and select a relay drive (electromechanical, solid-state, or reed) that meets the application’s demands.
-
Environmental factors: Take into account the operating environment, including temperature, humidity, vibrations, and shocks, and select a relay drive that can withstand these conditions.
-
Lifetime: Estimate the expected number of switching cycles and choose a relay drive with an appropriate lifetime rating.
-
Cost: Consider the cost of the relay drive in relation to the overall system cost and the required performance.
Frequently Asked Questions (FAQ)
1. What is the difference between a relay and a contactor?
A relay and a contactor are both electromechanical switches, but they differ in terms of their intended application and construction. Relays are typically used for switching lower currents and have smaller, more compact designs. Contactors, on the other hand, are designed for switching higher currents and have more robust construction with larger contacts.
2. Can a solid-state relay be used for AC and DC loads?
Yes, solid-state relays are available for both AC and DC loads. However, it is essential to select the appropriate SSR based on the load type and the required voltage and current ratings.
3. How do I protect a relay drive from voltage transients and surges?
To protect a relay drive from voltage transients and surges, you can use the following techniques:
- Install transient voltage suppressors (TVS) or Varistors across the relay coil and contacts.
- Use RC Snubber Circuits across the contacts to suppress voltage spikes during switching.
- Implement proper grounding and shielding techniques to minimize the impact of electromagnetic interference (EMI).
4. What is the purpose of a flyback diode in a relay drive circuit?
A flyback diode, also known as a freewheeling diode or snubber diode, is connected across the relay coil to protect the switching device (e.g., transistor) from voltage spikes generated when the coil is de-energized. The diode provides a path for the coil’s stored energy to dissipate safely, preventing damage to the switching device.
5. How do I extend the life of a relay drive?
To extend the life of a relay drive, consider the following practices:
- Ensure that the relay is operated within its specified voltage and current ratings.
- Use appropriate contact protection circuits, such as RC snubbers or varistors, to minimize contact wear and arcing.
- Implement proper heat management techniques to prevent overheating of the relay and its components.
- Regularly inspect and maintain the relay, replacing it if signs of wear or damage are observed.
Conclusion
Relay drives are essential components in many electrical and electronic systems, providing a means to switch higher power loads using lower power control signals. By understanding the working principle, types, and applications of relay drives, engineers and technicians can select the appropriate relay for their specific needs and design reliable, efficient, and safe control circuits. Proper selection, protection, and maintenance of relay drives ensure optimal performance and extended lifetime in various industrial, automotive, and consumer applications.
No responses yet