What is a Reed Relay?
A reed relay is a type of electromagnetic switch that uses a reed switch operated by an electromagnet to control the opening and closing of the switch contacts. The reed switch consists of a pair of ferromagnetic contacts hermetically sealed in a glass envelope. When a magnetic field is applied, the reeds become magnetized and attract each other, closing the switch contacts. When the magnetic field is removed, the reeds demagnetize and spring back to their original positions, opening the switch contacts.
Reed relays offer several advantages over other types of relays:
– Hermetically sealed contacts are protected from environmental contamination
– No moving parts except the reed switch contacts, leading to long operational life
– Capable of switching very low level signals, down to nanovolts/nanoamps
– Fast switching speeds, typically 0.5-2 ms operate time
– Low power consumption to operate the coil
– Small size and lightweight
– Inexpensive compared to other relay technologies
Reed Relay Construction
A reed relay consists of an electromagnet coil wound around one or more reed switches. The coil generates a magnetic field when energized with a current, which magnetizes the reed switch contacts and causes them to attract and close. A diode is often placed across the coil to suppress voltage spikes generated by the collapsing magnetic field when the coil is de-energized.
The reed switch itself consists of two or more ferromagnetic reed elements hermetically sealed in a glass envelope filled with inert gas. The reeds are typically made of a nickel-iron alloy that becomes magnetized in the presence of a magnetic field. The end portions of the reeds are flattened and coated with a precious metal like rhodium or ruthenium to form the switch contacts. Non-ferromagnetic leads, usually made of copper, are attached to the reeds and brought out through the glass envelope to form the switch terminals.
Reed switches come in various configurations as shown in this table:
Configuration | Description | Schematic Symbol |
---|---|---|
Form A (SPST-NO) | Single Pole Single Throw, Normally Open. One reed used as a simple on-off switch. | |
Form B (SPST-NC) | Single Pole Single Throw, Normally Closed. One reed that opens when activated. | |
Form C (SPDT) | Single Pole Double Throw (changeover). Two reeds, one normally open and one normally closed. |
Other less common configurations include:
– DPST – Double Pole Single Throw
– DPDT – Double Pole Double Throw
– 3PST – Three Pole Single Throw
Depending on the coil voltage and power requirements, reed relays can be driven directly by digital logic circuits like TTL or CMOS. Larger reed relays may require additional driver circuitry like transistors or buffers to provide sufficient coil current.
Reed Relay Parameters and Specifications
When selecting a reed relay for a particular application, several key parameters need to be considered:
Coil Voltage and Current
The reed relay coil voltage (Vdc) specifies the normal operating voltage of the electromagnetic coil. Common coil voltages are 5V, 12V and 24V. The coil resistance determines the current draw at the rated voltage according to Ohm’s law:
I = V / R
Where:
I = coil current
V = rated coil voltage
R = coil resistance
For example, a 12V reed relay with a 500 ohm coil will draw 24mA at the rated voltage.
Energizing the coil with significantly more than the rated current risks overheating and damage to the coil windings. Applying too little coil current may result in failure to fully close the reed switch contacts or hold them in the closed position.
Must Operate/Release Voltage
The Must Operate Voltage (MOV) specifies the minimum coil voltage at which the relay is guaranteed to operate – that is, changing from the normal (unenergized) state to the operated (energized) state. The MOV is typically 75% of the rated coil voltage.
The Must Release Voltage (MRV) specifies the maximum coil voltage at which the relay is guaranteed to release – that is, changing from the operated state back to the normal state. The MRV is typically around 10% of the rated coil voltage.
For example, a 12V reed relay may have a MOV of 9V and a MRV of 1.2V. As long as the applied coil voltage remains between these limits, the relay should function reliably.
Switching Current and Voltage
The switching current is the maximum current the reed switch contacts are rated to carry in the closed state. This is usually specified for resistive loads. Inductive loads can draw significantly higher transient currents at turn-on/off due to the inductive “kick”, possibly damaging or welding the contacts if not limited by external circuitry like diodes or snubbers.
The switching voltage is the maximum open-circuit voltage the reed switch can withstand in the open state without risking arc-over or damage. Exceeding the switching current or voltage can lead to premature failure of the reed relay.
Typical reed relays are rated for switching currents from a few milliamps up to around 3 amps, with switching voltages up to 200V DC or 400V AC. The switching capacity is often expressed as Volt-Amps (VA), the product of the switching current and voltage. For example, a relay rated for 1A at 30V has a switching capacity of 30VA.
Operate/Release Time
The operate time specifies how quickly the reed relay switches from the normal to the operated state when the rated coil voltage is applied. The release time specifies how quickly the relay returns to the normal state when the coil voltage is removed.
Operate and release times for reed relays are very fast compared to electromechanical relays, typically in the range of 0.5 to 2 milliseconds. This makes them suitable for applications requiring high speed switching.
Contact Resistance
The contact resistance is the total resistance of the closed reed switch contacts, leads and terminals. A lower contact resistance allows the switched current to flow with less loss and power dissipation.
The contact resistance of a new, clean reed switch is very low, typically 50-100 millohms. However, contact resistance can rise over the life of the relay due to contact wear or build-up of contaminants like oxidation or polymerization of organic vapors. A higher contact resistance also reduces the switching capacity of the relay. Manufacturers often specify a maximum or end-of-life contact resistance at which point the relay should be replaced.
Reed Relay Applications
Reed relays are used in a wide variety of low power switching applications, including:
Instrumentation and Test Equipment
The small size, fast switching speed, and low contact resistance of reed relays make them ideal for switching low-level analog signals and high speed digital data in test and measurement equipment like multimeters, data loggers, and oscilloscopes. Multiplexers and matrix switches built with reed relays allow different signals to be routed to the measuring circuitry under microprocessor/software control.
Telecommunications
Reed relays are used extensively in telephone exchanges and switching equipment for routing analog voice and digital data signals. Their hermetically sealed contacts provide high reliability and long service life even with continuous switching duty cycles.
Industrial Control
Reed relays can provide input/output (I/O) interfacing between industrial sensors, actuators, and programmable logic controllers (PLCs). Their fast switching speeds allow them to be used for high speed counting and timing functions. Compared to solid state relays (SSRs), reed relays generate very little electromagnetic interference (EMI) and have higher isolation voltage ratings.
Medical Electronics
Reed relays are used in medical devices like defibrillators, patient monitors, and analytical instruments for switching sensor signals and activating alarms. Their high reliability and resistance to shock and vibration are important in these critical applications.
Automotive Electronics
Under-hood and under-dash control modules in vehicles use reed relays for switching loads like lights, motors, and solenoids. The ability of reed relays to switch relatively high currents in a small package makes them well suited for these space-constrained applications.
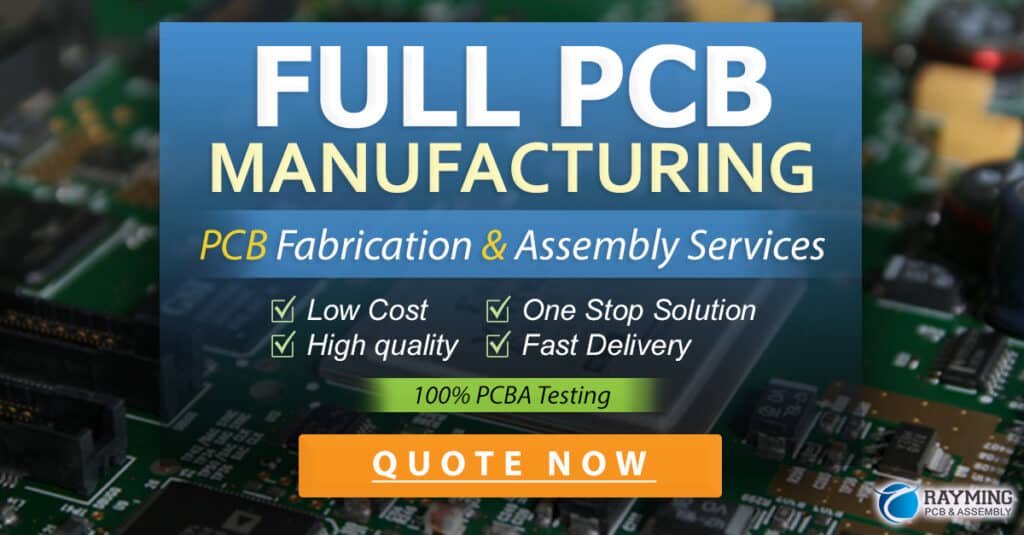
Interfacing Reed Relays with Digital Circuits
The electromagnet coil in a reed relay requires more current than a logic gate or microcontroller output can directly provide. Some form of driver circuit is needed as an interface.
Transistor Drivers
A bipolar or MOSFET transistor can be used to switch the larger coil current under the control of the logic signal. The base/gate resistor limits the base/gate current to a safe value for the logic output. The coil suppression diode protects the transistor from inductive voltage spikes when the relay is switched off.
Example bipolar transistor driver circuit:
Example MOSFET transistor driver circuit:
Integrated Drivers
Special purpose relay driver chips are available that include the power switching devices and suppression diodes in a single package. Some also incorporate logic-level translation, allowing direct interfacing with different logic families like TTL or CMOS.
An example is the Toshiba TLP627 relay driver octal photocoupler, which can interface 5V logic signals to eight reed relays with coil voltages up to 350V:
Using an integrated driver can simplify the circuit design and reduce component count compared to discrete transistor drivers.
Reed Relay Selection Guide
When selecting a reed relay for a particular application, consider the following steps:
-
Determine the required switching current and voltage for the load. Make sure to select a relay with contacts rated for the expected load current and voltage, with some safety margin.
-
Determine the required coil voltage, considering the available power supply voltages in the system. If possible, choose a relay with a standard coil voltage (5V, 12V, 24V) to simplify the driver design.
-
Estimate the expected switching frequency and duty cycle. This will affect the power dissipation in the coil and contacts. Make sure the chosen relay can handle the expected switching rate without overheating.
-
Consider the operating environment, including factors like ambient temperature, humidity, vibration and shock. Select a relay with suitable environmental ratings.
-
Determine any size constraints based on the available board space and layout. Reed relays are available in a variety of package styles including DIP, SIP and SMT.
-
Compare prices from different manufacturers, considering both the relay cost and any additional driver components that may be needed.
Some popular reed relay series to consider include:
Series | Manufacturer | Switching Current | Coil Voltages | Package |
---|---|---|---|---|
DIP05-1A | Coto Technology | 1A | 3, 5, 12, 24 VDC | DIP |
IM03 | TE Connectivity | 0.5A | 3, 5, 12, 24 VDC | SMD |
RTS-11xx | Meder | 1A | 3-24 VDC, custom | DIP, SMD |
DRC-I | Standex-Meder | 1A | 3-24 VDC, custom | SIP |
FAQ
What is the difference between a reed relay and a regular relay?
A reed relay uses a hermetically sealed reed switch operated by an electromagnet coil. A regular electromechanical relay uses open contacts on a movable armature operated by an electromagnet. Reed relays are generally smaller, faster, and more reliable than regular relays, but have lower current and voltage ratings.
Can reed relays switch AC loads?
Yes, reed relays can switch AC loads as long as the switching voltage and current ratings are not exceeded. However, AC loads are more stressful on the contacts than DC loads due to the higher peak voltages and currents. It’s important to use a relay rated for AC switching and to provide proper contact protection.
How long do reed relays last?
The service life of a reed relay depends on factors like the switching load, frequency, and environment. Under ideal conditions with low-level loads, a reed relay may be able to perform over a billion operations. With heavier loads, the contact life will be reduced. Consult the manufacturer’s datasheets for estimated life expectations under different operating conditions.
Can reed relays be used to switch high voltages?
Reed relays are available with switching voltage ratings up to several kilovolts. However, these are specialized types in larger packages with longer contact gaps. Most standard reed relays are rated for 200V DC or 400V AC switching at most. For higher voltages, use a high-voltage relay or switch with the appropriate ratings.
How do you protect a reed relay from inductive kick?
When switching an inductive load like a motor or solenoid, the collapsing magnetic field can generate high voltage spikes that may damage the relay contacts or driver. To suppress these spikes, a diode should be placed across the load, with the cathode to the positive side. For AC loads, a bi-directional TVS (transient voltage suppressor) or varistor should be used instead.
No responses yet