What is a Rigid-flex PCB?
A Rigid-Flex PCB is a hybrid printed circuit board that combines rigid and flexible substrates, allowing for enhanced design flexibility and improved product performance. This unique combination enables the creation of compact, lightweight, and highly reliable electronic devices that can withstand harsh environments and repeated flexing.
Advantages of Rigid-Flex PCBs
-
Space Savings: Rigid-Flex PCBs allow for the consolidation of multiple rigid boards into a single, compact design, reducing the overall size and weight of the final product.
-
Enhanced Reliability: By eliminating the need for connectors and cables between rigid boards, Rigid-Flex PCBs minimize the risk of connection failures and improve overall system reliability.
-
Improved Signal Integrity: The seamless integration of rigid and flexible sections reduces signal loss and interference, resulting in improved signal integrity and performance.
-
Design Flexibility: Rigid-Flex PCBs enable designers to create complex, three-dimensional structures that can be folded, bent, or twisted to fit within confined spaces or unique product configurations.
-
Cost Reduction: Although the initial cost of Rigid-Flex PCBs may be higher than traditional rigid boards, the overall cost savings from reduced assembly time, fewer components, and improved reliability can be significant.
RAYPCB’s Rigid-Flex PCB Manufacturing Capabilities
RAYPCB offers a comprehensive range of Rigid-Flex PCB manufacturing capabilities to meet the diverse needs of our customers. Our state-of-the-art facilities are equipped with the latest technology and staffed by experienced professionals who are dedicated to delivering the highest quality products and services.
Layer Stack-up Options
We offer a variety of layer stack-up options to suit your specific design requirements:
Layers | Rigid | Flex | Rigid-Flex |
---|---|---|---|
1-2 | ✓ | ✓ | ✓ |
3-4 | ✓ | ✓ | ✓ |
5-8 | ✓ | ✓ | ✓ |
9-12 | ✓ | ✓ | ✓ |
13-16 | ✓ | ✓ | ✓ |
17-20 | ✓ | – | ✓ |
Material Options
RAYPCB works with a wide range of materials to ensure optimal performance and reliability for your Rigid-Flex PCBs:
- FR-4
- Polyimide (PI)
- Liquid Crystal Polymer (LCP)
- PTFE
- Rogers Materials
Surface Finishes
We offer a variety of surface finishes to meet your specific needs:
- HASL (Hot Air Solder Leveling)
- ENIG (Electroless Nickel Immersion Gold)
- OSP (Organic Solderability Preservative)
- Immersion Silver
- Immersion Tin
Controlled Impedance
RAYPCB has extensive experience in designing and manufacturing Rigid-Flex PCBs with controlled impedance requirements. Our advanced manufacturing processes and strict quality control measures ensure that your boards meet the most demanding specifications.
Rigid-Flex PCB Design Considerations
Designing Rigid-Flex PCBs requires careful consideration of several factors to ensure optimal performance, reliability, and manufacturability. Some key design considerations include:
Bend Radius
The bend radius is a critical factor in Rigid-Flex PCB design, as it determines the minimum distance around which the flexible portion of the board can be bent without causing damage or degradation in performance. The bend radius is typically specified as a multiple of the flexible substrate thickness, with a minimum of 6 times the thickness being a common guideline.
Flexible Substrate Thickness
The thickness of the flexible substrate is another important consideration in Rigid-Flex PCB design. Thinner substrates allow for tighter bend radii and more compact designs, but may be more susceptible to damage during handling and assembly. Thicker substrates provide greater durability but may limit design flexibility.
Coverlay and Stiffener Placement
Coverlay and stiffeners are used to protect and reinforce the flexible portions of Rigid-Flex PCBs. Proper placement of these components is essential for ensuring the reliability and longevity of the board. Coverlay is typically applied to both sides of the flexible substrate, while stiffeners are used to reinforce specific areas, such as the transitions between rigid and flexible sections.
Copper Balancing
Copper balancing is the process of ensuring that the copper distribution on the Rigid-Flex PCB is as even as possible. Uneven copper distribution can lead to warping, twisting, and other manufacturing defects that can compromise the reliability and performance of the board. To achieve proper copper balancing, designers should use symmetrical layer stacks and avoid large copper pours or uneven trace widths.
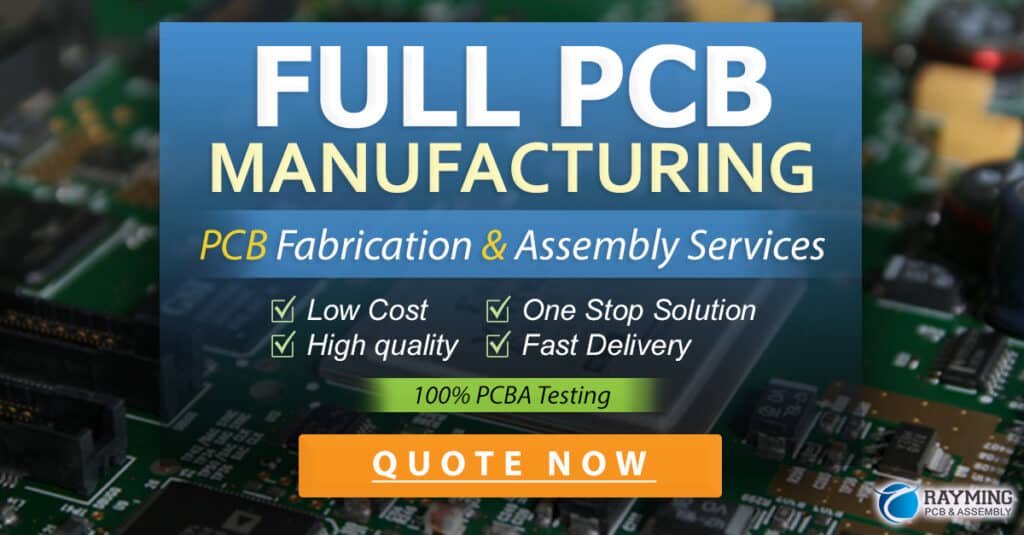
RAYPCB’s Rigid-Flex PCB Design Services
In addition to our manufacturing capabilities, RAYPCB offers comprehensive Rigid-Flex PCB design services to help you bring your ideas to life. Our experienced design team works closely with you to understand your unique requirements and develop a custom solution that meets your specific needs.
Design Review and Optimization
Our design review process includes a thorough analysis of your Rigid-Flex PCB design to identify potential issues and opportunities for optimization. We provide detailed feedback and recommendations to help you improve the manufacturability, reliability, and performance of your design.
DFM Analysis
RAYPCB conducts a comprehensive Design for Manufacturability (DFM) analysis to ensure that your Rigid-Flex PCB design is optimized for production. This includes checking for design rule violations, analyzing layer stack-ups, and verifying the compatibility of your design with our manufacturing processes.
Prototyping and Testing
We offer rapid prototyping services to help you validate your Rigid-Flex PCB design before committing to full-scale production. Our prototyping process includes the fabrication of functional prototypes, as well as comprehensive testing and validation to ensure that your design meets all necessary performance and reliability requirements.
RAYPCB’s Quality Assurance and Certifications
At RAYPCB, quality is our top priority. We maintain strict quality control measures throughout our entire manufacturing process to ensure that every Rigid-Flex PCB we produce meets the highest standards of quality and reliability.
Quality Assurance Process
Our quality assurance process includes:
- Incoming material inspection
- In-process quality control
- Final inspection and testing
- Traceability and record-keeping
Certifications
RAYPCB holds several industry certifications that demonstrate our commitment to quality and excellence:
- ISO 9001:2015
- IATF 16949:2016
- UL
- RoHS
- REACH
Frequently Asked Questions (FAQ)
-
What is the minimum bend radius for Rigid-Flex PCBs?
The minimum bend radius for Rigid-Flex PCBs depends on the thickness of the flexible substrate. A common guideline is to use a bend radius that is at least 6 times the thickness of the flexible substrate. However, this may vary depending on the specific materials and design requirements. -
How long does it take to manufacture a Rigid-Flex PCB?
The lead time for Rigid-Flex PCB manufacturing depends on several factors, including the complexity of the design, the materials used, and the quantity ordered. Typical lead times range from 2-4 weeks for prototypes and 4-8 weeks for production quantities. Rush services may be available for urgent projects. -
What file formats do you accept for Rigid-Flex PCB design submissions?
We accept a variety of industry-standard file formats for Rigid-Flex PCB design submissions, including Gerber files (RS-274X), ODB++, and IPC-2581. We also accept native CAD files from popular PCB design software, such as Altium Designer, Cadence Allegro, and Mentor Graphics PADS. -
Do you offer assembly services for Rigid-Flex PCBs?
Yes, RAYPCB offers turnkey assembly services for Rigid-Flex PCBs. Our assembly capabilities include SMT (Surface Mount Technology), THT (Through-Hole Technology), and mixed-technology assembly. We can also provide box build and final product assembly services. -
What is the maximum number of layers that can be incorporated into a Rigid-Flex PCB?
The maximum number of layers in a Rigid-Flex PCB depends on the specific design requirements and manufacturing capabilities. RAYPCB can produce Rigid-Flex PCBs with up to 20 layers in the rigid sections and up to 8 layers in the flexible sections. However, the total number of layers may be limited by factors such as the bend radius, overall thickness, and material selection.
Conclusion
RAYPCB is your trusted partner for high-quality Rigid-Flex PCB services. With our state-of-the-art facilities, experienced team, and commitment to quality, we deliver reliable and cost-effective solutions for your most challenging Rigid-Flex PCB projects. From design and prototyping to full-scale production, RAYPCB has the expertise and capabilities to meet your unique needs.
Contact us today to learn more about how RAYPCB can help bring your Rigid-Flex PCB ideas to life.
No responses yet