Introduction to Rigid-flex PCBs
Rigid-flex PCBs are a unique type of printed circuit board that combines the benefits of both rigid and flexible PCBs. These innovative boards consist of rigid and flexible substrates that are laminated together, allowing for a more compact and reliable design compared to traditional PCBs. Rigid-flex PCBs offer several advantages, such as reduced weight, improved electrical performance, and enhanced mechanical stability.
In this comprehensive guide, we will explore the world of rigid-flex PCBs and provide you with the essential information needed to choose the best rigid-flex PCB manufacturer for your project.
Benefits of Rigid-flex PCBs
Space Savings and Miniaturization
One of the primary advantages of rigid-flex PCBs is their ability to save space and enable miniaturization. By combining rigid and flexible sections, designers can create more compact and efficient layouts, reducing the overall size of the device. This is particularly beneficial for applications where space is limited, such as wearable devices, smartphones, and medical implants.
Improved Reliability and Durability
Rigid-flex PCBs offer enhanced reliability and durability compared to traditional PCBs. The flexible sections of the board allow for greater mechanical stability, as they can withstand repeated bending and flexing without compromising the electrical integrity of the circuit. Additionally, the reduced number of interconnects and solder joints in rigid-flex PCBs minimizes the potential for connection failures, resulting in a more robust and reliable product.
Enhanced Electrical Performance
The unique structure of rigid-flex PCBs also contributes to improved electrical performance. By eliminating the need for connectors and cables between rigid sections, signal integrity is maintained, and noise and interference are reduced. This is particularly important for high-speed and high-frequency applications, where signal quality is critical.
Cost Savings in the Long Run
Although the initial cost of rigid-flex PCBs may be higher than traditional PCBs, they offer significant cost savings in the long run. The reduced number of components, connectors, and assembly steps associated with rigid-flex PCBs leads to lower manufacturing and assembly costs. Furthermore, the improved reliability and durability of these boards translate to reduced maintenance and repair costs over the product’s lifetime.
Choosing the Right Rigid-flex PCB Manufacturer
Expertise and Experience
When selecting a rigid-flex PCB manufacturer, it is crucial to consider their expertise and experience in the field. Look for manufacturers with a proven track record of successfully producing high-quality rigid-flex PCBs for various industries and applications. Experienced manufacturers will have the knowledge and skills necessary to guide you through the design and fabrication process, ensuring optimal results.
Manufacturing Capabilities and Technology
Assess the manufacturing capabilities and technology offered by potential rigid-flex PCB manufacturers. State-of-the-art equipment, advanced manufacturing processes, and stringent quality control measures are essential for producing reliable and high-performance rigid-flex PCBs. Inquire about their ability to handle complex designs, multiple layers, and fine-pitch components.
Quality Certifications and Standards
Ensure that the rigid-flex PCB manufacturer you choose adheres to industry-recognized quality certifications and standards, such as ISO 9001, UL, and IPC. These certifications demonstrate the manufacturer’s commitment to quality and provide assurance that their processes and products meet international standards.
Customer Support and Communication
Effective communication and responsive customer support are vital when working with a rigid-flex PCB manufacturer. Look for a manufacturer that offers clear and prompt communication channels, such as dedicated account managers, technical support teams, and regular project updates. Good customer support can help streamline the design and manufacturing process, address any issues that may arise, and ensure timely delivery of your products.
Lead Times and Delivery
Consider the lead times and delivery options provided by the rigid-flex PCB manufacturer. In today’s fast-paced market, timely delivery is critical to the success of your project. Choose a manufacturer that can offer competitive lead times without compromising quality. Additionally, inquire about their ability to accommodate rush orders and provide flexible delivery options to meet your specific needs.
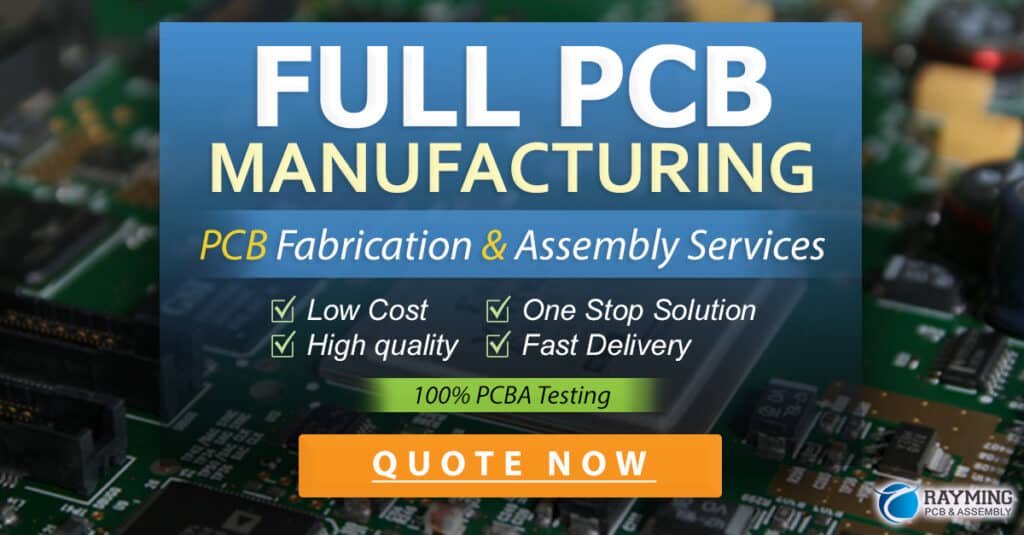
Design Considerations for Rigid-flex PCBs
Material Selection
Selecting the appropriate materials for your rigid-flex PCB is crucial for ensuring optimal performance and reliability. The choice of materials will depend on factors such as the intended application, environmental conditions, and required flexibility. Common materials used in rigid-flex PCBs include:
Material | Characteristics | Applications |
---|---|---|
FR-4 | Rigid, cost-effective, good electrical properties | General-purpose, consumer electronics |
Polyimide | Flexible, high-temperature resistance, excellent mechanical properties | Aerospace, military, medical devices |
Polyester | Flexible, cost-effective, good electrical properties | Consumer electronics, wearables |
Layer Stack-up and Thickness
The layer stack-up and thickness of a rigid-flex PCB play a significant role in its performance and reliability. A well-designed layer stack-up ensures proper signal integrity, power distribution, and mechanical stability. Consider the number of layers required for your design, as well as the thickness of the rigid and flexible sections. Work closely with your chosen manufacturer to optimize the layer stack-up for your specific application.
Bend Radius and Flexibility Requirements
When designing a rigid-flex PCB, it is essential to consider the bend radius and flexibility requirements of the flexible sections. The bend radius refers to the minimum radius at which the flexible section can be bent without causing damage or compromising performance. Consult with your manufacturer to determine the appropriate bend radius for your design, taking into account the materials used and the thickness of the flexible layers.
Component Placement and Routing
Careful component placement and routing are critical for the success of a rigid-flex PCB design. Consider the placement of components on both the rigid and flexible sections, ensuring proper clearance and accessibility for assembly and maintenance. Optimize the routing of traces to minimize signal interference and maintain signal integrity. Your chosen manufacturer should have the expertise to guide you through the component placement and routing process, offering recommendations based on best practices and their experience.
FAQs
1. What is the typical turnaround time for rigid-flex PCBs?
The turnaround time for rigid-flex PCBs varies depending on the complexity of the design, the chosen manufacturer, and the production volume. Typically, lead times range from 2 to 6 weeks, but some manufacturers may offer expedited services for urgent projects.
2. Can rigid-flex PCBs be used in harsh environments?
Yes, rigid-flex PCBs can be designed to withstand harsh environments, such as extreme temperatures, vibrations, and moisture. The choice of materials, coatings, and manufacturing techniques will determine the board’s ability to perform reliably in challenging conditions.
3. How do I ensure the reliability of my rigid-flex PCB design?
To ensure the reliability of your rigid-flex PCB design, consider the following factors:
– Choose appropriate materials for your application
– Optimize the layer stack-up and thickness
– Adhere to recommended bend radius and flexibility requirements
– Carefully plan component placement and routing
– Work with an experienced and reputable manufacturer
4. Are rigid-flex PCBs more expensive than traditional PCBs?
Initially, rigid-flex PCBs may have a higher cost compared to traditional PCBs due to the specialized materials and manufacturing processes involved. However, they offer long-term cost savings through reduced assembly steps, improved reliability, and lower maintenance costs.
5. Can rigid-flex PCBs be reworked or repaired?
Reworking or repairing rigid-flex PCBs can be more challenging than traditional PCBs due to their unique structure and the presence of flexible sections. However, experienced manufacturers and repair technicians can often successfully rework or repair rigid-flex PCBs, depending on the nature and extent of the issue.
Conclusion
Choosing the right rigid-flex PCB manufacturer is crucial for the success of your project. By understanding the benefits, design considerations, and key factors to consider when selecting a manufacturer, you can make an informed decision that meets your specific needs.
When evaluating potential rigid-flex PCB manufacturers, consider their expertise, manufacturing capabilities, quality certifications, customer support, and delivery options. Work closely with your chosen manufacturer throughout the design and production process to ensure optimal results.
By leveraging the advantages of rigid-flex PCBs and partnering with a reliable manufacturer, you can create innovative, compact, and high-performance products that stand out in today’s competitive market.
No responses yet