Understanding Power Requirements
Identifying Voltage and Current Needs
The first step in designing a power PCB is to understand the power requirements of your system. This involves identifying the voltage and current needs of each component in your design. You should consider the following factors:
- Supply voltage range
- Maximum current draw
- Voltage regulation accuracy
- Transient response requirements
Create a table that lists each component, its voltage requirement, and its maximum current draw. This will help you determine the total power consumption of your system and select appropriate power components.
Component | Voltage (V) | Max Current (A) |
---|---|---|
Microcontroller | 3.3 | 0.1 |
Sensors | 5 | 0.2 |
Motors | 12 | 2 |
LEDs | 3.3 | 0.05 |
Selecting the Right Power Supply
Based on your power requirements, you need to select the right power supply for your system. Consider the following options:
- Linear regulators
- Switching regulators
- DC-DC converters
- Battery management systems
Each power supply type has its advantages and limitations. Linear regulators are simple and low-noise but inefficient. Switching regulators are efficient but can introduce noise. DC-DC converters provide isolation and can step up or down voltages. Battery management systems are essential for portable devices.
Component Selection
Choosing the Right Components
Selecting the right components is crucial for the performance and reliability of your power PCB. Consider the following factors when choosing components:
- Voltage and current ratings
- Package size and thermal characteristics
- Efficiency and power dissipation
- Reliability and lifetime
- Cost and availability
Use reputable suppliers and manufacturers for your components. Read datasheets carefully and follow application notes and design guidelines.
Designing for Thermal Management
Power components generate heat, which can affect their performance and reliability. Proper thermal management is essential for power PCBs. Consider the following techniques:
- Provide adequate copper area for heat dissipation
- Use thermal vias to conduct heat to other layers
- Place components strategically to minimize thermal coupling
- Use heatsinks and fans for high-power components
Use thermal simulation tools to analyze your design and optimize component placement and copper layout.
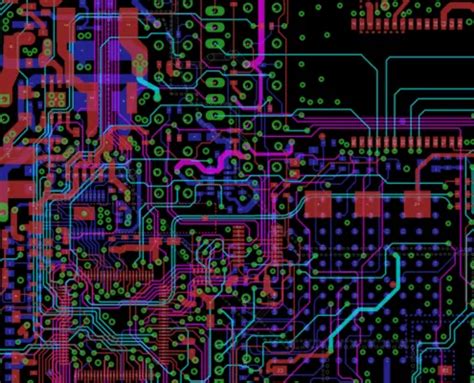
PCB Layout Techniques
Minimizing Noise and EMI
Power PCBs are susceptible to noise and electromagnetic interference (EMI), which can affect signal integrity and cause system malfunctions. To minimize noise and EMI, follow these layout techniques:
- Keep power and ground planes separate
- Use decoupling capacitors near power pins
- Minimize loop areas for high-current paths
- Route sensitive signals away from power traces
- Use ground shields for critical signals
Optimizing Power Distribution
Proper power distribution is essential for maintaining stable voltages and minimizing voltage drop. Follow these layout techniques for optimizing power distribution:
- Use wide traces for high-current paths
- Provide multiple vias for power and ground connections
- Use star or grid topology for power distribution
- Place power components close to their loads
- Use power planes for low-impedance distribution
Use PCB layout tools with Power Integrity analysis features to optimize your power distribution network.
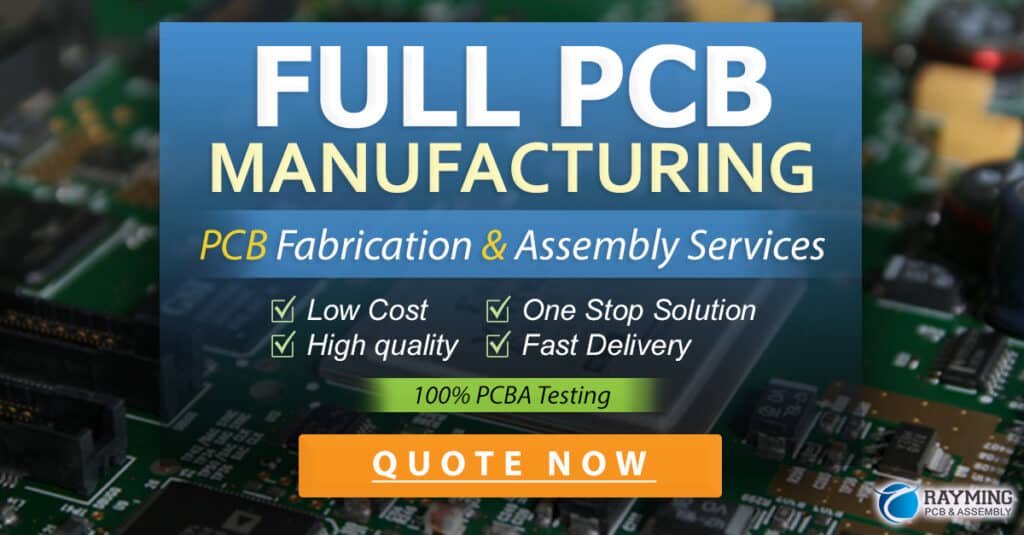
Safety Considerations
Designing for Overcurrent Protection
Overcurrent conditions can damage components and cause system failures. Design your power PCB with overcurrent protection mechanisms, such as:
- Fuses and Circuit Breakers
- Polymeric positive temperature coefficient (PPTC) devices
- Current-limiting circuits
- Overcurrent detection and shutdown mechanisms
Choose appropriate overcurrent protection devices based on your system’s current rating and transient response requirements.
Designing for Electrostatic Discharge (ESD) Protection
Electrostatic discharge (ESD) can damage sensitive electronic components and cause system failures. Design your power PCB with ESD protection mechanisms, such as:
- ESD protection diodes
- Transient voltage suppression (TVS) devices
- Grounding and shielding techniques
- ESD-safe handling procedures
Use ESD simulation tools to analyze your design and optimize component placement and layout.
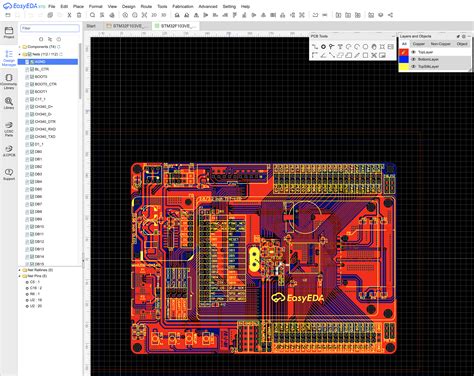
Testing and Verification
Conducting Power Integrity Simulations
Before fabricating your power PCB, conduct power integrity simulations to verify your design. Use simulation tools to analyze the following:
- Voltage drop and regulation
- Current density and thermal effects
- Transient response and stability
- Noise and EMI performance
Optimize your design based on simulation results and iterate until you achieve satisfactory performance.
Building and Testing Prototypes
After finalizing your design, build prototypes and conduct thorough testing to verify functionality and reliability. Test your prototypes under various operating conditions, such as:
- Different load scenarios
- Temperature extremes
- Vibration and shock
- ESD and EMI exposure
Use test equipment, such as oscilloscopes, power analyzers, and thermal cameras, to monitor and diagnose issues.
Frequently Asked Questions (FAQ)
Q1: What is the difference between linear and switching regulators?
A1: Linear regulators provide a simple and low-noise solution for voltage regulation but are inefficient and generate significant heat. Switching regulators are more efficient and can handle higher power levels but can introduce noise and require more complex designs.
Q2: How do I select the right decoupling capacitors for my power PCB?
A2: Select decoupling capacitors based on their capacitance value, voltage rating, and equivalent series resistance (ESR). Place them close to the power pins of components to minimize loop area and provide effective noise suppression.
Q3: What is the purpose of ground planes in power PCBs?
A3: Ground planes provide a low-impedance return path for currents and help minimize noise and EMI. They also serve as a reference for signal routing and can help with heat dissipation.
Q4: How can I minimize voltage drop in my power distribution network?
A4: To minimize voltage drop, use wide traces for high-current paths, provide multiple vias for power and ground connections, and place power components close to their loads. Use power planes for low-impedance distribution and consider using voltage sense lines for feedback control.
Q5: What are some common mistakes to avoid when designing power PCBs?
A5: Some common mistakes to avoid include:
– Underestimating power requirements and selecting inadequate components
– Neglecting thermal management and component placement
– Overlooking noise and EMI issues in layout and routing
– Failing to provide proper overcurrent and ESD protection
– Skipping power integrity simulations and thorough testing
By understanding these five major aspects of power PCB design – power requirements, component selection, PCB layout techniques, safety considerations, and testing – beginners can lay a strong foundation for creating robust and reliable power circuits. As with any complex engineering task, designing power PCBs requires practice, attention to detail, and continuous learning. By staying updated with industry best practices and leveraging the wealth of resources available, beginners can navigate the challenges of power PCB design and create successful projects.
No responses yet