Introduction to ESD and Its Impact on PCBs
Electrostatic discharge (ESD) is a sudden flow of electricity between two electrically charged objects caused by contact, an electrical short, or dielectric breakdown. In the context of printed circuit boards (PCBs), ESD can cause significant damage to sensitive electronic components, leading to immediate failure or latent defects that may affect the long-term reliability of the device.
ESD events can generate high voltages and currents that can exceed the maximum ratings of electronic components, causing permanent damage. Some common effects of ESD on PCBs include:
- Gate oxide breakdown in MOSFET devices
- Junction damage in transistors and diodes
- Thermal damage due to high current density
- Dielectric breakdown in capacitors and insulators
To mitigate the risk of ESD damage, it is essential to implement effective ESD protection measures during PCB handling, assembly, and packaging processes. One of the most critical aspects of ESD protection is proper grounding techniques.
The Role of Grounding in ESD Protection
Grounding plays a crucial role in ESD protection by providing a low-impedance path for electrostatic charges to dissipate safely, preventing the buildup of high voltages that can damage electronic components. Effective grounding techniques involve establishing a common ground reference for all conductive objects in the environment, including personnel, equipment, and work surfaces.
Some key benefits of proper grounding in ESD protection include:
-
Equalizing potential differences: By connecting all conductive objects to a common ground, potential differences between them are minimized, reducing the risk of ESD events.
-
Dissipating electrostatic charges: Grounding provides a safe path for electrostatic charges to flow away from sensitive components, preventing charge accumulation and reducing the severity of ESD events.
-
Improving ESD event detection: Grounded ESD monitoring systems can detect and alert personnel to the presence of electrostatic fields, enabling timely corrective actions.

ESD Grounding Techniques for PCB Protection
1. Personnel Grounding
One of the primary sources of ESD events in PCB handling and assembly is the human body. Personnel grounding is essential to prevent the accumulation of electrostatic charges on the body and transfer them to sensitive components. Some common personnel grounding techniques include:
-
Wrist straps: Wrist straps are conductive bands worn around the wrist, connected to ground through a coiled cord and a resistor (typically 1 MΩ). They provide a continuous ground path for the operator, dissipating electrostatic charges safely.
-
ESD footwear and flooring: Conductive or dissipative footwear and flooring systems help ground personnel by providing a low-resistance path between the operator’s body and the ground. ESD footwear includes shoes, heel grounders, and toe grounders, while ESD flooring options include conductive tiles, mats, and carpets.
-
ESD garments: ESD garments, such as lab coats, smocks, and coveralls, are made from conductive or dissipative materials that help ground the operator’s body and prevent charge accumulation on clothing.
Personnel Grounding Method | Advantages | Disadvantages |
---|---|---|
Wrist Straps | – Continuous grounding – Easy to use and monitor |
– Restricted mobility – Discomfort with prolonged use |
ESD Footwear and Flooring | – Allows for greater mobility – Suitable for larger areas |
– Higher installation and maintenance costs – Requires regular testing |
ESD Garments | – Covers a larger portion of the body – Comfortable to wear |
– May require additional grounding methods – Limited durability |
2. Equipment Grounding
Electronic equipment, tools, and machinery used in PCB handling and assembly can also generate and accumulate electrostatic charges. Equipment grounding ensures that these charges are safely dissipated to ground, minimizing the risk of ESD events. Some equipment grounding techniques include:
-
Grounded work surfaces: Conductive or dissipative work surfaces, such as ESD mats and tabletops, provide a grounded area for placing PCBs and components during handling and assembly. These surfaces are connected to ground through a resistor and a grounding cord.
-
Grounded tools and fixtures: Conductive or dissipative tools, jigs, and fixtures used in PCB assembly should be grounded to prevent charge accumulation. This can be achieved by using grounded wrist straps or connecting the tools directly to a grounded work surface.
-
Grounded equipment chassis: Electronic equipment used in PCB manufacturing, such as soldering stations, reflow ovens, and test instruments, should have their chassis grounded to dissipate any accumulated charges safely.
Equipment Grounding Method | Advantages | Disadvantages |
---|---|---|
Grounded Work Surfaces | – Provides a safe area for PCB handling – Easy to clean and maintain |
– Limited coverage area – May require frequent replacement |
Grounded Tools and Fixtures | – Ensures grounding of specific tools and components – Customizable for different applications |
– Requires regular testing and maintenance – May limit tool flexibility |
Grounded Equipment Chassis | – Protects sensitive internal components – Integrates with facility ground |
– May require additional grounding for external surfaces – Potential for ground loops |
3. Environmental Grounding
The environment in which PCBs are handled and assembled can also contribute to ESD risks. Proper environmental grounding helps reduce the generation and accumulation of electrostatic charges in the workspace. Some environmental grounding techniques include:
-
Humidity control: Maintaining relative humidity levels between 40% and 60% helps reduce the generation of electrostatic charges by increasing the conductivity of the air. This can be achieved through the use of humidifiers or humidity control systems.
-
Ionization: Air ionizers generate positive and negative ions that neutralize electrostatic charges in the environment. Ionizers can be used in conjunction with other grounding methods to provide an additional layer of ESD protection.
-
Shielding and grounding of ESD-sensitive areas: ESD-sensitive areas, such as clean rooms and PCB assembly lines, should be shielded from external ESD sources and grounded to prevent the buildup of electrostatic charges. This can be achieved using conductive partitions, curtains, and flooring materials.
Environmental Grounding Method | Advantages | Disadvantages |
---|---|---|
Humidity Control | – Reduces charge generation – Improves comfort for personnel |
– May require additional equipment and maintenance – Limited effectiveness in very dry environments |
Ionization | – Neutralizes charges in the air – Covers a large area |
– Requires regular maintenance and calibration – May generate ozone |
Shielding and Grounding | – Isolates ESD-sensitive areas – Integrates with facility ground |
– Higher installation and maintenance costs – May restrict access and mobility |
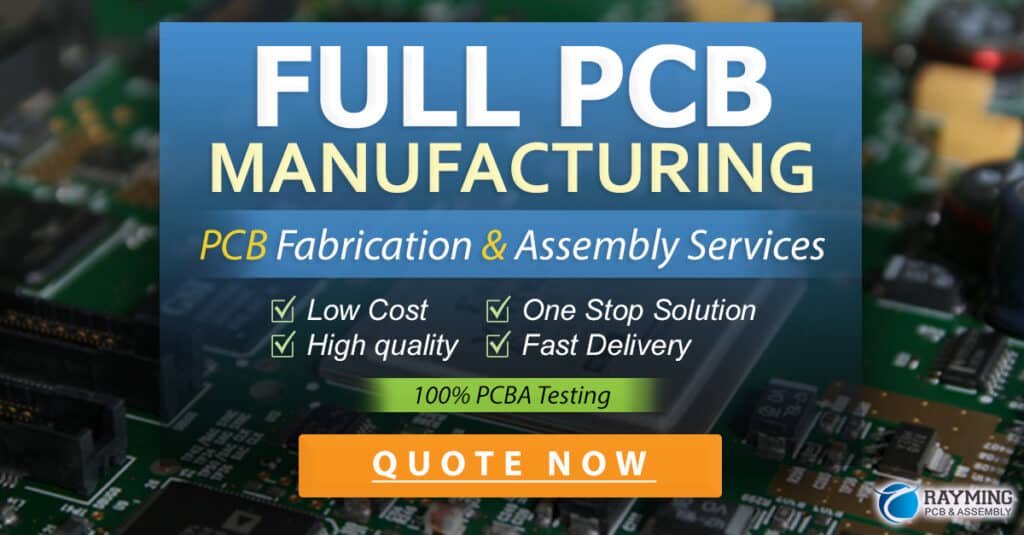
Implementing an ESD Grounding Plan
To effectively protect PCBs from ESD damage, it is essential to develop and implement a comprehensive ESD grounding plan. The plan should address all aspects of PCB handling, assembly, and packaging processes, and involve all personnel working in ESD-sensitive areas.
Key steps in implementing an ESD grounding plan include:
-
Assess ESD risks: Conduct an ESD risk assessment to identify potential sources of ESD events and evaluate the vulnerability of PCBs and components to ESD damage.
-
Establish ESD control areas: Designate ESD-protected areas (EPAs) for handling and assembling PCBs, and clearly mark the boundaries of these areas using signs, floor markings, or barriers.
-
Implement grounding measures: Select and implement appropriate grounding techniques for personnel, equipment, and the environment based on the ESD risk assessment and the specific requirements of the PCB assembly process.
-
Train personnel: Provide ESD awareness and grounding technique training to all personnel working in ESD-sensitive areas, including proper use of wrist straps, ESD footwear, and grounded work surfaces.
-
Monitor and maintain ESD controls: Regularly monitor and test ESD grounding equipment and systems to ensure their effectiveness, and maintain records of ESD events, equipment maintenance, and personnel training.
By implementing a comprehensive ESD grounding plan, PCB manufacturers and assemblers can significantly reduce the risk of ESD damage, improve product quality, and increase customer satisfaction.
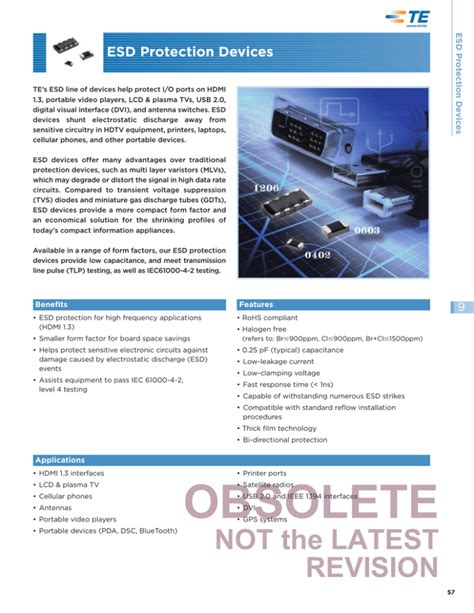
Frequently Asked Questions (FAQ)
- What is the difference between conductive and dissipative materials in ESD grounding?
-
Conductive materials have a surface resistance of less than 10^5 ohms, allowing electrostatic charges to flow easily and dissipate quickly. Dissipative materials have a surface resistance between 10^5 and 10^12 ohms, providing a controlled discharge of electrostatic charges. Conductive materials are typically used for grounding personnel and equipment, while dissipative materials are used for work surfaces and packaging materials to prevent rapid discharge that could cause ESD damage.
-
How often should ESD grounding equipment be tested?
-
The frequency of testing ESD grounding equipment depends on the specific equipment and the ESD risk level of the environment. Generally, wrist straps and foot grounders should be tested daily before use, while work surfaces and flooring should be tested monthly or quarterly. In high-risk environments, more frequent testing may be necessary. Always refer to the manufacturer’s recommendations and industry standards for specific testing requirements.
-
Can ESD damage occur even with proper grounding measures in place?
-
While implementing proper ESD grounding techniques significantly reduces the risk of ESD damage, it is not a complete guarantee against ESD events. Other factors, such as the sensitivity of the components, the magnitude of the ESD event, and the effectiveness of the grounding measures, can influence the occurrence and severity of ESD damage. Therefore, it is essential to use a combination of grounding techniques and other ESD control measures, such as shielding and ionization, to provide comprehensive protection against ESD.
-
How do I select the right ESD grounding equipment for my PCB assembly process?
-
Selecting the right ESD grounding equipment depends on various factors, including the ESD sensitivity of the components, the size and layout of the work area, the mobility requirements of the personnel, and the compatibility with existing equipment and processes. Consider conducting an ESD risk assessment and consulting with ESD control experts or equipment manufacturers to determine the most suitable grounding solutions for your specific needs.
-
What are the industry standards for ESD grounding in PCB manufacturing?
- Several industry standards provide guidelines and requirements for ESD grounding in PCB manufacturing, including:
- ANSI/ESD S20.20: Protection of Electrical and Electronic Parts, Assemblies, and Equipment (Excluding Electrically Initiated Explosive Devices)
- IEC 61340-5-1: Electrostatics – Part 5-1: Protection of electronic devices from electrostatic phenomena – General requirements
- JEDEC JESD625B: Requirements for Handling Electrostatic-Discharge-Sensitive (ESDS) Devices
These standards outline the recommended practices for ESD control, including grounding techniques, equipment specifications, and testing procedures. Adhering to these standards can help ensure the effectiveness of your ESD grounding plan and demonstrate compliance with industry best practices.
Conclusion
Implementing effective ESD grounding techniques is crucial for protecting PCBs from electrical damage during handling, assembly, and packaging processes. By understanding the role of grounding in ESD protection and applying appropriate grounding methods for personnel, equipment, and the environment, PCB manufacturers and assemblers can significantly reduce the risk of ESD events and improve the overall quality and reliability of their products.
Developing and implementing a comprehensive ESD grounding plan, along with regular training, monitoring, and maintenance, is essential for ensuring the long-term effectiveness of ESD control measures. By staying informed about industry standards and best practices, and continuously improving their ESD grounding techniques, PCB manufacturers and assemblers can stay ahead of the curve in protecting their products from the damaging effects of electrostatic discharge.
No responses yet