What is a Polyimide PCB?
A polyimide PCB is a printed circuit board that uses polyimide as the base material (substrate) instead of the more common FR-4 (flame retardant-4) material. Polyimide is a synthetic polymer that belongs to a class of materials called thermosetting plastics. It is formed by the reaction of a dianhydride with a diamine, resulting in a highly stable and heat-resistant material.
Polyimide PCBs are known for their ability to maintain their electrical and mechanical properties in extreme conditions, such as high temperatures, high pressure, and exposure to chemicals. This makes them suitable for applications where standard FR-4 PCBs would fail.
Types of Polyimide PCBs
There are several types of polyimide PCBs, each with its own unique properties and applications. The most common types are:
Kapton® PCBs
Kapton® is a registered trademark of DuPont™ for its polyimide film. Kapton® PCBs are made using this film as the substrate material. They are known for their excellent thermal stability, with a continuous operating temperature range of -269°C to 400°C. Kapton® PCBs also have high dielectric strength and good chemical resistance.
Pyralux® PCBs
Pyralux® is another DuPont™ product that combines Kapton® polyimide film with copper foil to create a flexible circuit material. Pyralux® PCBs are highly flexible and can be bent, twisted, or folded without damaging the circuits. They are often used in applications that require compact packaging or dynamic flexing.
Rigid-flex PCBs
Rigid-flex PCBs combine the benefits of both rigid and Flexible PCBs. They consist of rigid PCB sections connected by flexible polyimide sections. This allows for three-dimensional packaging and reduces the need for connectors and wiring. Rigid-flex PCBs are commonly used in aerospace, military, and medical applications.
High Density Interconnect (HDI) Polyimide PCBs
HDI polyimide PCBs are designed to accommodate a high density of components and interconnections in a small area. They use thin polyimide substrates, fine-pitch traces, and micro-vias to achieve high routing density. HDI polyimide PCBs are used in applications that require miniaturization and high-performance, such as smartphones, wearables, and medical implants.
Applications of Polyimide PCBs
Polyimide PCBs are used in a wide range of industries and applications due to their unique properties. Some of the most common applications include:
Aerospace and Defense
Polyimide PCBs are extensively used in aerospace and defense applications because of their ability to withstand extreme temperatures, vibrations, and radiation. They are used in satellites, aircraft, missiles, and other military equipment. Polyimide PCBs are also used in space exploration missions, such as the Mars Perseverance Rover, which uses a polyimide PCB in its SHERLOC instrument.
Automotive Electronics
The automotive industry is increasingly using polyimide PCBs in high-temperature applications, such as engine control units, exhaust gas sensors, and brake systems. Polyimide PCBs can withstand the high temperatures generated by modern engines and provide reliable performance in harsh automotive environments.
Medical Devices
Polyimide PCBs are used in a variety of medical devices, including implantable devices, surgical instruments, and diagnostic equipment. They are biocompatible, chemically resistant, and can be sterilized using various methods. Polyimide PCBs are also used in medical wearables, such as smart patches and monitoring devices.
Industrial Electronics
Industrial applications often involve high temperatures, corrosive chemicals, and mechanical stress. Polyimide PCBs are well-suited for these conditions and are used in power electronics, oil and gas exploration, chemical processing, and other industrial settings. They are also used in sensors and actuators that operate in harsh environments.
Consumer Electronics
While polyimide PCBs are more commonly associated with high-end applications, they are also used in consumer electronics where high performance and reliability are required. Examples include smartphones, laptops, gaming consoles, and virtual reality headsets. Polyimide PCBs are particularly useful in applications that generate a lot of heat, such as high-performance processors and graphics cards.
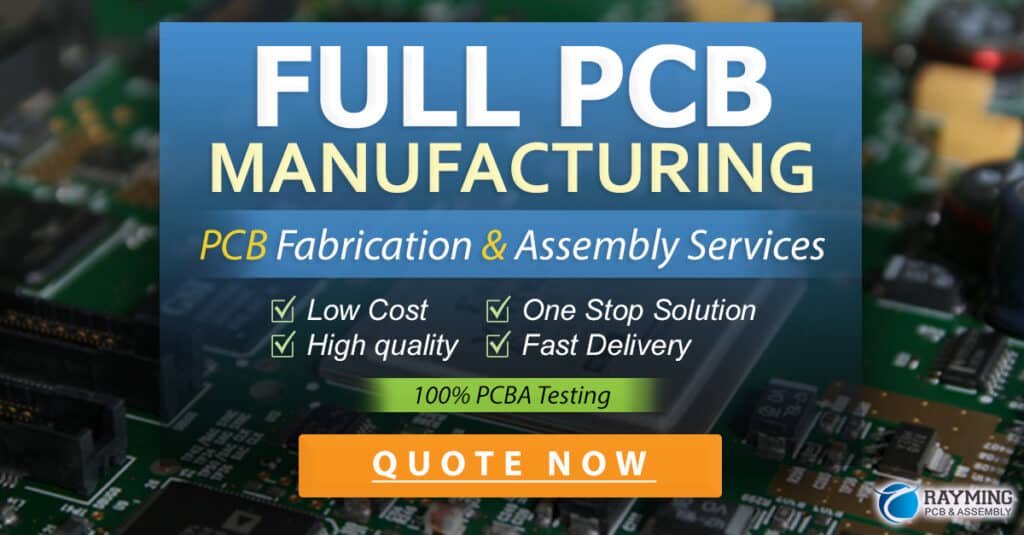
Benefits of Polyimide PCBs
Polyimide PCBs offer several benefits over traditional FR-4 PCBs, making them the preferred choice for demanding applications. Some of the key benefits include:
High Temperature Resistance
One of the most significant advantages of polyimide PCBs is their ability to withstand high temperatures. Polyimide has a glass transition temperature (Tg) of around 360°C and a decomposition temperature of over 500°C. This means that polyimide PCBs can operate at temperatures well beyond the limits of FR-4 PCBs, which typically have a Tg of around 130°C.
Mechanical Strength and Flexibility
Polyimide PCBs have excellent mechanical properties, including high tensile strength, elongation, and tear resistance. This makes them highly durable and resistant to mechanical stress and vibrations. Polyimide films, such as Kapton® and Pyralux®, are also highly flexible, allowing for the design of flexible circuits that can be bent, twisted, or folded without damaging the traces.
Chemical Resistance
Polyimide PCBs are resistant to a wide range of chemicals, including acids, bases, solvents, and fuels. This makes them suitable for applications where exposure to harsh chemicals is expected, such as in chemical processing plants, oil and gas exploration, and aerospace.
Dimensional Stability
Polyimide PCBs have low coefficients of thermal expansion (CTE) compared to FR-4 PCBs. This means that they experience minimal dimensional changes when exposed to temperature fluctuations. This dimensional stability is crucial in applications where precise alignment and positioning of components are required, such as in optoelectronics and high-frequency circuits.
Dielectric Properties
Polyimide has excellent dielectric properties, including high dielectric strength and low dielectric loss. This makes polyimide PCBs suitable for high-voltage and high-frequency applications. The low dielectric constant of polyimide also allows for faster signal propagation and reduced signal loss, which is essential in high-speed digital circuits.
FAQ
1. Are polyimide PCBs more expensive than FR-4 PCBs?
Yes, polyimide PCBs are generally more expensive than FR-4 PCBs due to the higher cost of polyimide materials and the specialized manufacturing processes required. However, the higher cost is often justified by the superior performance and reliability offered by polyimide PCBs in demanding applications.
2. Can polyimide PCBs be manufactured using the same processes as FR-4 PCBs?
While some of the manufacturing processes for polyimide PCBs are similar to those used for FR-4 PCBs, there are several key differences. Polyimide PCBs require specialized equipment and processes to handle the unique properties of polyimide materials, such as high-temperature lamination, laser drilling of micro-vias, and advanced surface treatments.
3. How do I choose between different types of polyimide PCBs for my application?
The choice of polyimide PCB type depends on the specific requirements of your application. Factors to consider include the operating temperature range, mechanical stress, chemical exposure, flexibility requirements, and signal integrity. Consulting with a PCB manufacturer or materials expert can help you select the most suitable polyimide PCB type for your needs.
4. Can polyimide PCBs be recycled?
Recycling polyimide PCBs can be challenging due to the high thermal stability and chemical resistance of polyimide materials. However, some recycling methods have been developed, such as pyrolysis and solvent-based processes, which can recover valuable metals and other materials from polyimide PCBs. Research into more efficient and environmentally friendly recycling methods for polyimide PCBs is ongoing.
5. Are there any disadvantages to using polyimide PCBs?
The main disadvantages of polyimide PCBs are their higher cost compared to FR-4 PCBs and the specialized manufacturing processes required. Additionally, polyimide PCBs may not be suitable for all applications, particularly those that do not require high-temperature resistance or mechanical stability. In some cases, the use of polyimide PCBs may result in overengineering and unnecessary costs.
Conclusion
Polyimide PCBs are a high-performance alternative to traditional FR-4 PCBs, offering exceptional thermal stability, mechanical strength, and chemical resistance. With various types available, such as Kapton® PCBs, Pyralux® PCBs, rigid-flex PCBs, and HDI polyimide PCBs, designers can select the most suitable option for their specific application requirements.
The unique properties of polyimide PCBs make them invaluable in demanding industries, such as aerospace, defense, automotive, medical, and industrial electronics. As technology continues to advance and push the boundaries of performance and reliability, the use of polyimide PCBs is expected to grow further.
While polyimide PCBs may have a higher initial cost compared to FR-4 PCBs, their superior performance and longevity often make them a cost-effective choice in the long run. As research and development in polyimide materials and manufacturing processes continue, we can expect to see even more innovative applications and benefits of polyimide PCBs in the future.
Property | Polyimide PCB | FR-4 PCB |
---|---|---|
Glass Transition Temperature (Tg) | 360°C | 130°C |
Decomposition Temperature | >500°C | ~300°C |
Dielectric Constant (1 MHz) | 3.5 | 4.5 |
Dielectric Strength (kV/mm) | 200 | 50 |
Tensile Strength (MPa) | 231 | 415 |
Elongation at Break (%) | 72 | 1.5 |
CTE (ppm/°C) | 20 | 14 |
Chemical Resistance | Excellent | Good |
Typical Applications | Aerospace, Defense, Automotive, Medical | Consumer Electronics, General Purpose |
This table compares some key properties of polyimide PCBs and FR-4 PCBs, highlighting the superior performance of polyimide in terms of thermal stability, dielectric properties, and chemical resistance. However, it also shows that FR-4 PCBs have higher tensile strength and lower CTE, making them suitable for general-purpose applications.
No responses yet