What are Vias and Why are They Used in PCB Design?
Vias are small holes drilled in a printed circuit board (PCB) that allow electrical connections between different layers of the board. They are an essential component in multi-layer PCB designs, enabling the routing of signals and power between layers. Vias come in different types, such as through-hole vias, blind vias, and buried vias, each serving specific purposes in PCB design.
Via Type | Description |
---|---|
Through-hole Via | Extends through all layers of the PCB |
Blind Via | Connects an outer layer to an inner layer, but does not go through the entire board |
Buried Via | Connects inner layers without reaching either outer layer |
The primary reasons for using vias in PCB design include:
-
Interconnecting layers: Vias allow signals and power to be routed between different layers of the PCB, enabling more complex designs and better utilization of board space.
-
Reducing signal interference: By strategically placing vias, designers can minimize crosstalk and electromagnetic interference (EMI) between signals on different layers.
-
Providing thermal relief: Vias can be used to dissipate heat from high-power components, preventing thermal stress and ensuring reliable operation.
What are Plugged Vias?
Plugged vias, also known as filled vias or capped vias, are vias that have been filled with a conductive or non-conductive material to seal the hole. The filling material can be a conductive paste, such as copper or silver, or a non-conductive epoxy. Plugged vias offer several advantages over standard vias, which we will discuss in the following sections.
Advantages of Plugged Vias
1. Improved Signal Integrity
One of the primary benefits of using plugged vias is the improvement in signal integrity. When a via is left open, it can act as a small antenna, radiating electromagnetic energy and causing signal distortion. By filling the via with a conductive material, this radiation is minimized, leading to cleaner signals and reduced electromagnetic interference (EMI).
2. Enhanced Mechanical Strength
Plugged vias also provide enhanced mechanical strength to the PCB. Unfilled vias can be weak points in the board, especially when subjected to thermal stress or mechanical strain. By filling the vias, the overall structural integrity of the PCB is improved, reducing the risk of via breakage and delamination.
3. Better Thermal Management
In high-power applications, thermal management is crucial for ensuring reliable operation and preventing component failure. Plugged vias can help dissipate heat more effectively than standard vias by providing a larger cross-sectional area for thermal conduction. This is particularly important for vias that are used to connect thermal pads of power components to ground planes or heatsinks.
4. Increased Manufacturability
Plugged vias can also improve the manufacturability of PCBs. During the soldering process, solder can wick through unfilled vias, causing shorts or insufficient solder joints on the opposite side of the board. By plugging the vias, this issue is eliminated, resulting in more reliable solder connections and fewer manufacturing defects.
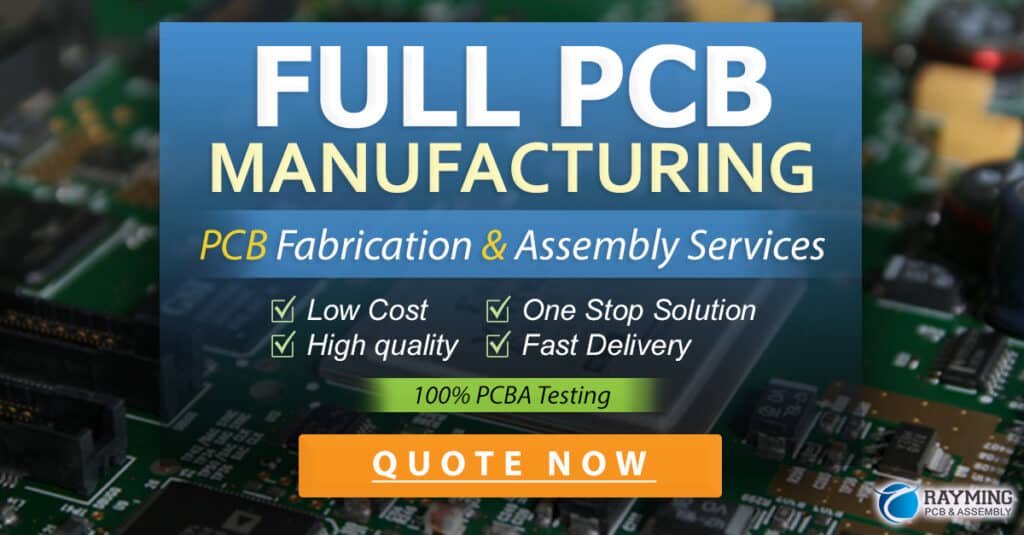
Disadvantages of Plugged Vias
Despite their numerous benefits, plugged vias also have some drawbacks that designers should consider.
1. Increased Cost
One of the main disadvantages of using plugged vias is the increased cost of manufacturing. The process of filling vias requires additional materials and production steps, which can add to the overall cost of the PCB. This cost increase may be justified for high-performance or mission-critical applications, but it may not be necessary for simpler designs.
2. Potential for Voiding
Another issue with plugged vias is the potential for voiding. Voids are small air pockets that can form within the filling material during the plugging process. These voids can reduce the effectiveness of the via in terms of signal integrity, thermal conductivity, and mechanical strength. To minimize voiding, precise process control and specialized equipment are required, further adding to the cost and complexity of manufacturing.
3. Limited Repairability
Plugged vias can also limit the repairability of PCBs. If a component needs to be replaced or a trace needs to be repaired, it may be more difficult to access the necessary connections if the vias are filled. In some cases, the filling material may need to be removed before repairs can be made, which can be a time-consuming and delicate process.
When to Use Plugged Vias
Given the advantages and disadvantages of plugged vias, designers must carefully consider when to use them in their PCB designs. Here are some scenarios where plugged vias are commonly used:
-
High-speed digital circuits: In applications involving high-speed digital signals, such as high-performance computing or telecommunications, plugged vias can help maintain signal integrity and reduce EMI.
-
RF and microwave circuits: Plugged vias are often used in radio frequency (RF) and Microwave PCB designs to minimize signal loss and radiation leakage.
-
High-power electronics: In power electronics applications, plugged vias can improve thermal management and prevent thermal stress on components.
-
Aerospace and military applications: PCBs used in aerospace and military systems often require plugged vias to meet stringent reliability and performance requirements.
-
Medical devices: Medical electronics, particularly implantable devices, may use plugged vias to ensure reliable operation and prevent moisture ingress.
Alternatives to Plugged Vias
For applications where plugged vias are not strictly necessary or cost-effective, designers can consider alternative techniques to address signal integrity and thermal management issues.
-
Via stitching: This technique involves placing vias in a dense pattern around signal traces to create a shielding effect, reducing EMI and crosstalk.
-
Differential signaling: By using differential pairs for high-speed signals, designers can minimize the impact of via stubs and reduce electromagnetic radiation.
-
Thermal vias: Instead of plugging vias, designers can use a larger number of smaller vias to improve thermal conductivity and dissipate heat more effectively.
-
High-performance laminates: Using PCB materials with lower dielectric constants and dissipation factors can help reduce signal loss and improve overall performance without the need for plugged vias.
Frequently Asked Questions (FAQ)
-
Q: Are plugged vias always necessary for multi-layer PCBs?
A: No, plugged vias are not always necessary for multi-layer PCBs. The decision to use plugged vias depends on the specific requirements of the application, such as signal integrity, thermal management, and reliability. -
Q: Can plugged vias be used in combination with other via types?
A: Yes, plugged vias can be used in combination with other via types, such as blind and buried vias, depending on the design requirements and PCB manufacturing capabilities. -
Q: How does the choice of filling material affect the performance of plugged vias?
A: The choice of filling material can impact the electrical, thermal, and mechanical properties of plugged vias. Conductive materials, such as copper or silver, provide better electrical and thermal conductivity, while non-conductive epoxies offer improved mechanical strength and moisture resistance. -
Q: Are there any specific design guidelines for using plugged vias?
A: When using plugged vias, designers should follow best practices such as maintaining appropriate via-to-pad ratios, avoiding via-in-pad configurations, and ensuring proper clearance between vias and other components. It is also important to work closely with the PCB manufacturer to ensure compatibility with their processes and capabilities. -
Q: Can plugged vias be used in high-volume production?
A: Yes, plugged vias can be used in high-volume production, but the added cost and complexity of the plugging process should be considered. Designers should work with their PCB manufacturer to optimize the design and process for high-volume manufacturing, minimizing the impact on cost and lead times.
Conclusion
Plugged vias offer numerous benefits for PCB designers, including improved signal integrity, enhanced mechanical strength, better thermal management, and increased manufacturability. However, these advantages come with trade-offs, such as increased cost, potential for voiding, and limited repairability. When deciding whether to use plugged vias in a PCB design, engineers must carefully weigh the specific requirements of the application against the costs and limitations of the technology.
By understanding the advantages and disadvantages of plugged vias, as well as the alternative techniques available, designers can make informed decisions that balance performance, reliability, and cost-effectiveness. As PCB technologies continue to evolve, the use of plugged vias will likely remain an important tool for addressing the challenges of high-speed, high-density, and high-reliability electronic systems.
No responses yet