Introduction to Piezo Circuits
Piezo circuits are electronic circuits that utilize the piezoelectric effect to generate or detect mechanical strain or pressure. The piezoelectric effect is a phenomenon where certain materials, such as quartz crystals or certain ceramics, generate an electric charge when subjected to mechanical stress. Conversely, these materials can also deform or change shape when an electric field is applied to them. This unique property of piezoelectric materials has led to the development of various sensors, actuators, and transducers used in a wide range of applications.
What are Piezoelectric Materials?
Piezoelectric materials are a class of materials that exhibit the piezoelectric effect. Some common piezoelectric materials include:
- Quartz (SiO2)
- Lead Zirconate Titanate (PZT)
- Barium Titanate (BaTiO3)
- Polyvinylidene Fluoride (PVDF)
These materials have a crystalline structure that allows them to generate an electric charge when subjected to mechanical stress or strain. The piezoelectric effect is reversible, meaning that applying an electric field to these materials causes them to deform or change shape.
Applications of Piezo Circuits
Piezo circuits find applications in various fields, including:
- Sensors
- Pressure sensors
- Accelerometers
- Strain gauges
- Ultrasonic Sensors
- Actuators
- Piezoelectric motors
- Micro-positioning stages
- Ultrasonic transducers
- Inkjet printer heads
- Energy Harvesting
- Piezoelectric energy harvesters
- Vibration-based power generation
- Medical Devices
- Ultrasonic imaging transducers
- Dental scalers
- Surgical instruments
- Automotive
- Fuel injectors
- Knock sensors
- Tire pressure monitoring systems
Types of Piezo Circuits
Piezo circuits can be categorized into two main types based on their function: sensors and actuators.
Piezo Sensor Circuits
Piezo sensor circuits are designed to detect and measure mechanical stress, strain, or pressure applied to a piezoelectric material. When the piezoelectric material is subjected to mechanical stress, it generates an electric charge proportional to the applied stress. This charge can be converted into a voltage signal using a charge amplifier or a voltage amplifier circuit.
Charge Amplifier Circuit
A charge amplifier circuit is commonly used in piezo sensor applications to convert the charge generated by the piezoelectric material into a voltage signal. The basic structure of a charge amplifier circuit consists of an operational amplifier (op-amp) with a feedback capacitor.
The feedback capacitor (Cf) integrates the charge generated by the piezoelectric sensor (Cp), producing an output voltage (Vout) proportional to the applied stress or strain. The output voltage can be expressed as:
Vout = -Q / Cf
where Q is the charge generated by the piezoelectric sensor.
Voltage Amplifier Circuit
In some cases, a voltage amplifier circuit can be used instead of a charge amplifier to amplify the voltage signal generated by the piezoelectric sensor. The voltage amplifier circuit consists of an op-amp with a high input impedance to minimize loading effects on the sensor.
The gain of the voltage amplifier circuit is determined by the ratio of the feedback resistor (Rf) to the input resistor (Rin):
Gain = Vout / Vin = -Rf / Rin
Piezo Actuator Circuits
Piezo actuator circuits are designed to drive piezoelectric materials to generate mechanical motion or deformation. When an electric field is applied to a piezoelectric material, it expands or contracts, depending on the polarity of the applied field. This property can be exploited to create various types of actuators, such as piezoelectric motors, micro-positioning stages, and ultrasonic transducers.
Piezoelectric Motor Driver Circuit
Piezoelectric motors are compact, high-precision actuators that use the inverse piezoelectric effect to generate linear or rotary motion. A typical piezoelectric motor driver circuit consists of a high-voltage amplifier and a waveform generator to drive the piezoelectric elements.
The waveform generator produces the necessary driving signals, such as sine waves or square waves, which are amplified by the high-voltage amplifier to drive the piezoelectric elements. The frequency and amplitude of the driving signals determine the speed and displacement of the piezoelectric motor.
Ultrasonic Transducer Driver Circuit
Ultrasonic transducers are piezoelectric devices that generate and detect high-frequency sound waves. They are used in various applications, such as ultrasonic cleaning, welding, and imaging. An ultrasonic transducer driver circuit typically consists of a power amplifier and a matching network to efficiently transfer energy to the transducer.
The power amplifier provides the necessary driving voltage and current to the ultrasonic transducer. The matching network, which usually consists of inductors and capacitors, ensures maximum power transfer and minimizes reflections between the amplifier and the transducer.
Piezo Circuit Design Considerations
When designing piezo circuits, several key factors must be considered to ensure optimal performance and reliability.
Impedance Matching
Impedance matching is crucial in piezo circuits to maximize power transfer and minimize signal reflections. The impedance of the piezoelectric element should be matched to the impedance of the driving or sensing circuit to achieve the best performance.
In piezo sensor circuits, the input impedance of the charge amplifier or voltage amplifier should be much higher than the impedance of the piezoelectric sensor to minimize loading effects. In piezo actuator circuits, the output impedance of the driving amplifier should be matched to the impedance of the piezoelectric element to ensure maximum power transfer.
Frequency Response
Piezoelectric materials have a specific resonant frequency at which they exhibit maximum sensitivity or displacement. The frequency response of the piezo circuit should be designed to match the resonant frequency of the piezoelectric element to achieve the best performance.
In piezo sensor circuits, the bandwidth of the amplifier should be wide enough to capture the desired frequency range of the sensor. In piezo actuator circuits, the driving frequency should be close to the resonant frequency of the piezoelectric element to maximize the displacement or motion.
Noise Reduction
Piezo circuits are sensitive to noise, which can degrade the signal-to-noise ratio (SNR) and limit the resolution of the system. Proper noise reduction techniques should be employed to minimize the impact of noise on the piezo circuit.
Some common noise reduction techniques include:
- Shielding: Using shielded cables and enclosures to minimize electromagnetic interference (EMI).
- Grounding: Proper grounding techniques, such as using a single-point ground or a ground plane, can help reduce ground loops and common-mode noise.
- Filtering: Implementing low-pass, high-pass, or band-pass filters to attenuate unwanted noise frequencies.
- Differential Signaling: Using differential amplifiers or balanced transmission lines to cancel out common-mode noise.
Temperature Stability
Piezoelectric materials are sensitive to temperature variations, which can cause changes in their properties and performance. Temperature compensation techniques should be employed to minimize the impact of temperature fluctuations on the piezo circuit.
Some common temperature compensation techniques include:
- Temperature-Compensated Oscillators: Using temperature-compensated Crystal Oscillators (TCXOs) or oven-controlled crystal oscillators (OCXOs) to provide a stable reference frequency.
- Temperature Sensors: Incorporating temperature sensors, such as thermistors or RTDs, to measure the temperature and compensate for temperature-induced changes in the piezoelectric element.
- Active Temperature Control: Implementing active temperature control systems, such as Peltier elements or heating elements, to maintain a stable operating temperature for the piezoelectric element.
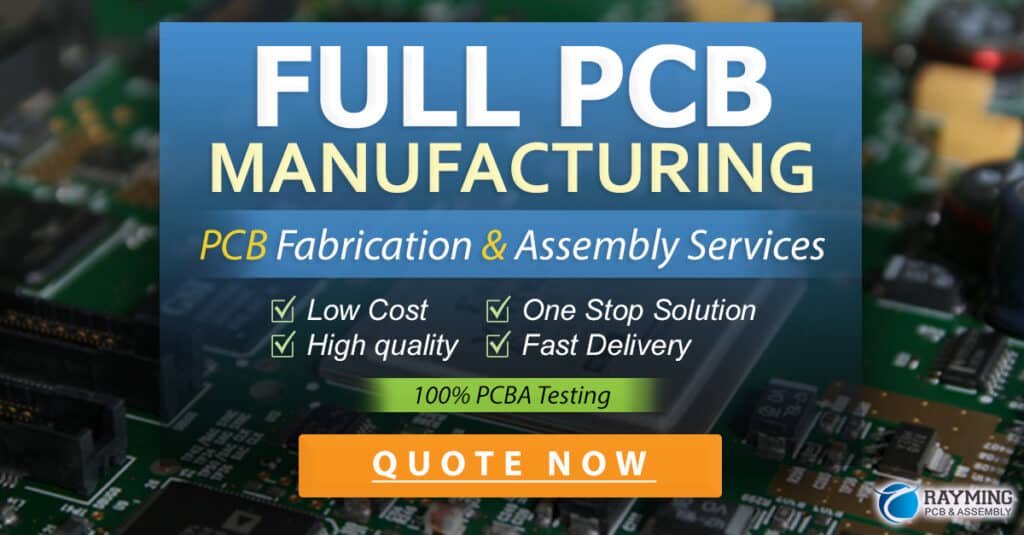
Piezo Circuit Applications
Piezo circuits find applications in various fields, ranging from industrial automation to medical devices. Some notable applications of piezo circuits include:
Pressure Sensors
Piezo pressure sensors are widely used in various industries to measure static and dynamic pressures. They offer high sensitivity, wide dynamic range, and fast response times, making them suitable for applications such as:
- Automotive: Measuring fuel injection pressure, tire pressure, and engine knock.
- Aerospace: Monitoring air pressure in aircraft cabins and measuring aerodynamic pressures on wings and fuselages.
- Industrial: Monitoring pressure in hydraulic and pneumatic systems, as well as in process control applications.
Accelerometers
Piezo accelerometers are used to measure acceleration, vibration, and shock. They are compact, rugged, and have a wide frequency response, making them suitable for applications such as:
- Automotive: Detecting vehicle collisions for airbag deployment and measuring engine vibrations.
- Aerospace: Monitoring vibrations in aircraft engines and structures.
- Industrial: Monitoring machine vibrations for predictive maintenance and detecting seismic activity.
Ultrasonic Transducers
Piezo ultrasonic transducers are used to generate and detect high-frequency sound waves for various applications, such as:
- Medical: Ultrasonic imaging, dental scaling, and surgical cutting.
- Industrial: Ultrasonic cleaning, welding, and non-destructive testing.
- Automotive: Parking sensors and obstacle detection systems.
Energy Harvesting
Piezo energy harvesters convert ambient mechanical energy, such as vibrations or pressure fluctuations, into electrical energy. They are used in various applications, such as:
- Wireless Sensor Networks: Powering wireless sensor nodes in remote or inaccessible locations.
- Wearable Electronics: Harvesting energy from human motion to power wearable devices.
- Industrial: Harvesting energy from machine vibrations or fluid flow to power monitoring sensors.
Frequently Asked Questions (FAQ)
-
What is the piezoelectric effect?
The piezoelectric effect is a phenomenon where certain materials generate an electric charge when subjected to mechanical stress or strain. Conversely, these materials can also deform or change shape when an electric field is applied to them. -
What are some common piezoelectric materials?
Some common piezoelectric materials include quartz (SiO2), lead zirconate titanate (PZT), barium titanate (BaTiO3), and polyvinylidene fluoride (PVDF). -
What is the difference between a piezo sensor and a piezo actuator?
A piezo sensor uses the direct piezoelectric effect to convert mechanical stress or strain into an electrical signal, while a piezo actuator uses the inverse piezoelectric effect to convert an electrical signal into mechanical motion or deformation. -
How does a charge amplifier work in a piezo sensor circuit?
A charge amplifier converts the charge generated by a piezoelectric sensor into a voltage signal. It consists of an op-amp with a feedback capacitor that integrates the charge, producing an output voltage proportional to the applied stress or strain. -
What are some common noise reduction techniques used in piezo circuits?
Some common noise reduction techniques used in piezo circuits include shielding, proper grounding, filtering, and differential signaling. These techniques help minimize the impact of electromagnetic interference, ground loops, and common-mode noise on the piezo circuit.
Conclusion
Piezo circuits are essential components in various applications, from sensors and actuators to energy harvesting devices. By leveraging the unique properties of piezoelectric materials, these circuits enable the conversion between mechanical and electrical energy, opening up a wide range of possibilities in sensing, actuation, and power generation.
When designing piezo circuits, it is crucial to consider factors such as impedance matching, frequency response, noise reduction, and temperature stability to ensure optimal performance and reliability. By carefully addressing these design considerations, engineers can develop high-performance piezo circuits that meet the specific requirements of their applications.
As technology continues to advance, piezo circuits are expected to play an increasingly important role in fields such as the Internet of Things (IoT), wearable electronics, and smart manufacturing. With their compact size, high sensitivity, and energy harvesting capabilities, piezo circuits offer unique advantages that make them attractive for a wide range of innovative applications.
No responses yet