What are PCBs?
PCBs, or Printed Circuit Boards, are the backbone of modern electronics. They are flat boards made of insulating materials, such as fiberglass or plastic, with conductive copper traces etched onto their surface. These traces connect various electronic components, such as resistors, capacitors, and integrated circuits, to create a functional electronic circuit.
PCBs have revolutionized the electronics industry by providing a reliable, compact, and cost-effective way to manufacture electronic devices. They are used in a wide range of applications, from simple consumer electronics to complex industrial equipment and aerospace systems.
Types of PCBs
There are several types of PCBs, each with its own unique characteristics and applications:
-
Single-sided PCBs: These PCBs have conductive traces on only one side of the board. They are the simplest and most cost-effective type of PCB, suitable for low-complexity circuits.
-
Double-sided PCBs: These PCBs have conductive traces on both sides of the board, allowing for more complex circuits and higher component density. The two sides are connected using vias, which are small holes drilled through the board and plated with conductive material.
-
Multi-layer PCBs: These PCBs consist of multiple layers of insulating material and conductive traces, allowing for even higher component density and more complex circuits. They are used in advanced electronic devices, such as smartphones, computers, and medical equipment.
-
Flexible PCBs: These PCBs are made of flexible materials, such as polyimide, allowing them to bend and conform to various shapes. They are used in applications where space is limited or where the PCB needs to flex during operation, such as in wearable devices or automotive electronics.
-
Rigid-flex PCBs: These PCBs combine the benefits of both rigid and flexible PCBs, with rigid sections for mounting components and flexible sections for connecting them. They are used in applications where both high component density and flexibility are required, such as in aerospace and military systems.
PCB Type | Layers | Complexity | Cost | Applications |
---|---|---|---|---|
Single-sided | 1 | Low | Low | Simple consumer electronics |
Double-sided | 2 | Medium | Medium | More complex consumer electronics |
Multi-layer | 3+ | High | High | Advanced electronics (smartphones, computers) |
Flexible | 1-2 | Low-Medium | Medium | Wearable devices, automotive electronics |
Rigid-Flex | 2+ | High | High | Aerospace, military systems |
PCB Design Process
The PCB design process involves several key steps:
1. Schematic Design
The first step in PCB design is creating a schematic diagram of the electronic circuit. This diagram shows the interconnections between the various components and helps to ensure that the circuit will function as intended. Schematic design software, such as EagleCAD or KiCad, is commonly used for this purpose.
2. Component Selection
Once the schematic is complete, the next step is to select the appropriate components for the PCB. This involves choosing components that meet the required specifications, such as voltage rating, current handling capacity, and package size. Component libraries in PCB design software can help streamline this process.
3. PCB Layout
After the components are selected, the PCB layout can be created. This involves arranging the components on the board and routing the conductive traces to connect them. PCB layout software, such as Altium Designer or OrCAD, is used for this purpose. The layout must take into account various design rules, such as minimum trace width, spacing between traces, and via size, to ensure manufacturability and reliability.
4. Design Rule Check (DRC)
Once the PCB layout is complete, a Design Rule Check (DRC) is performed to ensure that the design meets all the necessary requirements. The DRC checks for issues such as short circuits, open circuits, and violations of the design rules. Any issues identified by the DRC must be resolved before proceeding to the next step.
5. Gerber File Generation
After the DRC is passed, the PCB design software generates Gerber files, which are the industry-standard format for PCB manufacturing. These files contain all the necessary information for the PCB manufacturer to fabricate the board, including the copper layer patterns, drill holes, and silkscreen markings.
6. PCB Fabrication
The Gerber files are sent to a PCB manufacturer, who uses them to fabricate the physical PCB. The fabrication process involves several steps, such as copper etching, hole drilling, and solder mask application. The completed PCB is then inspected for quality and shipped to the customer.
PCB Assembly
Once the PCB is fabricated, the next step is to assemble the electronic components onto the board. This process can be done manually or using automated assembly machines, depending on the complexity of the PCB and the production volume.
Manual Assembly
For low-volume production or prototyping, manual assembly is often used. This involves hand-soldering the components onto the PCB using a soldering iron and solder wire. Manual assembly requires skill and attention to detail to ensure that the components are properly aligned and soldered.
Automated Assembly
For high-volume production, automated assembly machines are used to place and solder the components onto the PCB. These machines use pick-and-place technology to rapidly and accurately place the components, and reflow soldering to melt the solder and create a strong electrical and mechanical connection. Automated assembly is faster and more consistent than manual assembly, but requires a higher initial investment in equipment.
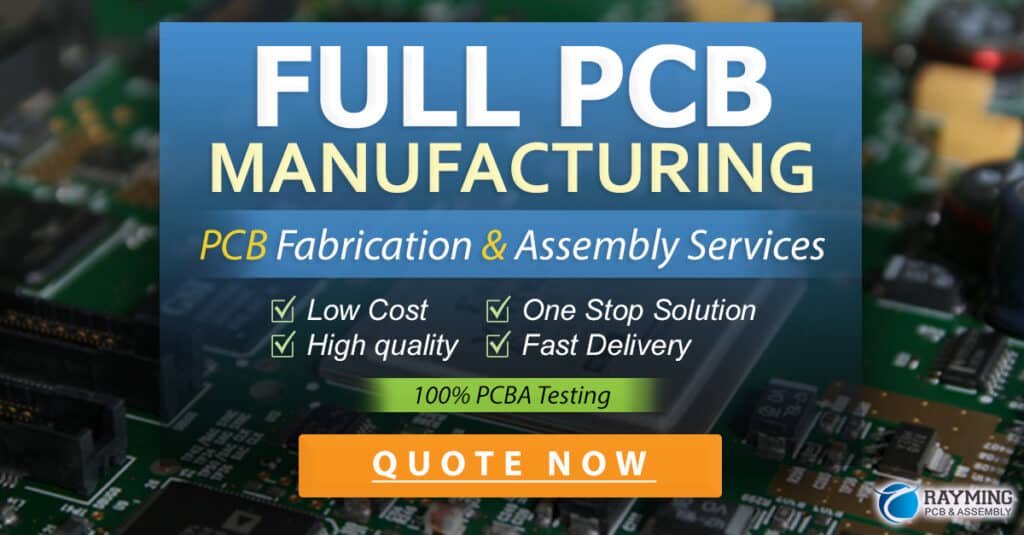
Testing and Inspection
After the PCB is assembled, it must be tested and inspected to ensure that it functions as intended and meets all the necessary quality standards. There are several types of tests that can be performed, depending on the application and the level of reliability required:
-
Visual Inspection: This involves visually examining the PCB for any obvious defects, such as misaligned components, solder bridges, or damaged traces.
-
Automated Optical Inspection (AOI): This uses cameras and image processing software to automatically detect and identify defects on the PCB, such as missing components or incorrect component placement.
-
In-Circuit Testing (ICT): This involves using a bed-of-nails fixture to make electrical contact with specific points on the PCB and test the functionality of individual components and circuits.
-
Functional Testing: This involves testing the complete assembled PCB to ensure that it performs its intended function, such as powering on, communicating with other devices, or processing data.
Any issues identified during testing and inspection must be resolved before the PCB can be considered complete and ready for use.
PCB Materials
PCBs are made from a combination of insulating and conductive materials. The most common materials used in PCB fabrication are:
-
FR-4: This is a glass-reinforced epoxy laminate material that is widely used as the base material for PCBs. It has good mechanical and electrical properties, and is relatively inexpensive.
-
Copper: This is the most common conductive material used in PCBs. It is used to create the conductive traces and pads on the board, and is typically plated onto the FR-4 substrate.
-
Solder Mask: This is a protective coating that is applied over the copper traces on the PCB. It helps to prevent short circuits and provides insulation between the traces.
-
Silkscreen: This is a printed layer on the PCB that contains text and symbols to help identify components and provide assembly instructions.
Other materials, such as aluminum, ceramic, and polyimide, may be used in specialized applications where specific properties, such as high thermal conductivity or flexibility, are required.
PCB Design Considerations
When designing a PCB, there are several key considerations to keep in mind:
-
Signal Integrity: This refers to the quality of the electrical signals transmitted through the PCB. Factors such as trace impedance, crosstalk, and electromagnetic interference (EMI) can affect signal integrity and must be carefully managed through proper PCB design.
-
Power Integrity: This refers to the quality of the power supply delivered to the components on the PCB. Factors such as voltage drop, current capacity, and power distribution network (PDN) design can affect power integrity and must be carefully managed to ensure reliable operation.
-
Thermal Management: This refers to the management of heat generated by the components on the PCB. Proper thermal management is essential to prevent overheating and ensure reliable operation, especially in high-power applications.
-
Manufacturability: The PCB design must be compatible with the manufacturing processes used to fabricate the board. This includes considerations such as minimum trace width and spacing, hole sizes, and component placement.
-
Cost: The cost of the PCB is a critical consideration in many applications. Factors such as board size, layer count, and component selection can all affect the cost of the PCB and must be carefully balanced against the required performance and reliability.
PCB Design Software
There are many PCB design software packages available, ranging from free open-source tools to high-end commercial solutions. Some of the most popular PCB design software packages include:
-
Altium Designer: This is a high-end commercial PCB design package that offers advanced features such as 3D modeling, signal integrity analysis, and automated design rule checking.
-
KiCad: This is a free and open-source PCB design package that offers a complete suite of tools for schematic capture, PCB layout, and Gerber file generation.
-
Eagle: This is a popular commercial PCB design package that offers a user-friendly interface and a large community of users and resources.
-
OrCAD: This is another high-end commercial PCB design package that offers advanced features such as constraint-driven design, signal integrity analysis, and manufacturing optimization.
When selecting a PCB design software package, it is important to consider factors such as ease of use, feature set, compatibility with other tools and processes, and cost.
Frequently Asked Questions (FAQ)
-
What is the difference between a PCB and a breadboard?
A PCB is a permanent, custom-designed board that is used to interconnect electronic components, while a breadboard is a temporary prototyping tool that allows components to be easily inserted and removed without soldering. -
How long does it take to design and manufacture a PCB?
The time required to design and manufacture a PCB can vary widely depending on the complexity of the design, the manufacturing process used, and the production volume. Simple PCBs can be designed and manufactured in a few days, while complex, high-volume PCBs may take several weeks or even months. -
What is the minimum trace width and spacing for a PCB?
The minimum trace width and spacing for a PCB depends on the manufacturing process and the design requirements. Typical minimum trace widths range from 0.1 mm to 0.2 mm, while minimum spacing ranges from 0.1 mm to 0.3 mm. However, these values can vary depending on the specific PCB fabricator and the design constraints. -
How much does it cost to manufacture a PCB?
The cost to manufacture a PCB depends on many factors, including the board size, layer count, component count, and production volume. Small, simple PCBs can cost as little as a few dollars each, while large, complex PCBs can cost hundreds or even thousands of dollars each. In general, higher production volumes result in lower per-unit costs. -
What is the difference between surface mount and through-hole components?
Surface mount components are mounted directly onto the surface of the PCB, while through-hole components have leads that are inserted through holes in the PCB and soldered on the opposite side. Surface mount components are smaller and allow for higher component density, while through-hole components are larger and easier to handle for manual assembly.
No responses yet