Introduction to Rigid-flex PCBs
Rigid-flex PCBs are a unique type of printed circuit board that combines the benefits of both rigid and flexible substrates. These boards consist of rigid PCB sections connected by flexible PCB sections, allowing for three-dimensional packaging and improved reliability in applications that require flexibility, vibration resistance, and space savings.
The demand for rigid-flex PCBs has grown significantly in recent years, driven by the increasing complexity and miniaturization of electronic devices in various industries, such as:
- Aerospace and defense
- Medical devices
- Automotive electronics
- Consumer electronics
- Industrial automation
However, choosing the right rigid-flex PCB manufacturer can be a challenging task, as the design and fabrication process is more complex compared to traditional rigid PCBs. In this article, we will discuss nine essential tips to help you select the best rigid-flex PCB manufacturer for your project.
Tip 1: Look for Experience and Expertise in Rigid-flex PCB Manufacturing
When searching for a rigid-flex PCB manufacturer, it is crucial to consider their experience and expertise in this specific area. Rigid-flex PCB design and fabrication require specialized knowledge and skills that not all PCB manufacturers possess. Look for a manufacturer with a proven track record of successfully producing high-quality rigid-flex PCBs for various applications and industries.
An experienced rigid-flex PCB manufacturer should have:
- In-depth understanding of rigid-flex PCB design guidelines and best practices
- Expertise in material selection and stack-up design
- Advanced manufacturing capabilities, such as laser cutting and micro-via drilling
- Stringent quality control processes to ensure product reliability and consistency
Tip 2: Evaluate the Manufacturer’s Design Support Capabilities
Designing a rigid-flex PCB can be a complex and iterative process that requires close collaboration between the customer and the manufacturer. A good rigid-flex PCB manufacturer should offer comprehensive design support services to help you optimize your design for manufacturability, reliability, and cost-effectiveness.
Design support services may include:
- Design rule checks (DRC) and design for manufacturability (DFM) analysis
- Stack-up design and material selection guidance
- Signal integrity and power integrity analysis
- 3D modeling and mechanical integration support
- Prototype development and testing
By working with a manufacturer that provides strong design support, you can minimize design iterations, reduce time-to-market, and ensure the success of your rigid-flex PCB project.
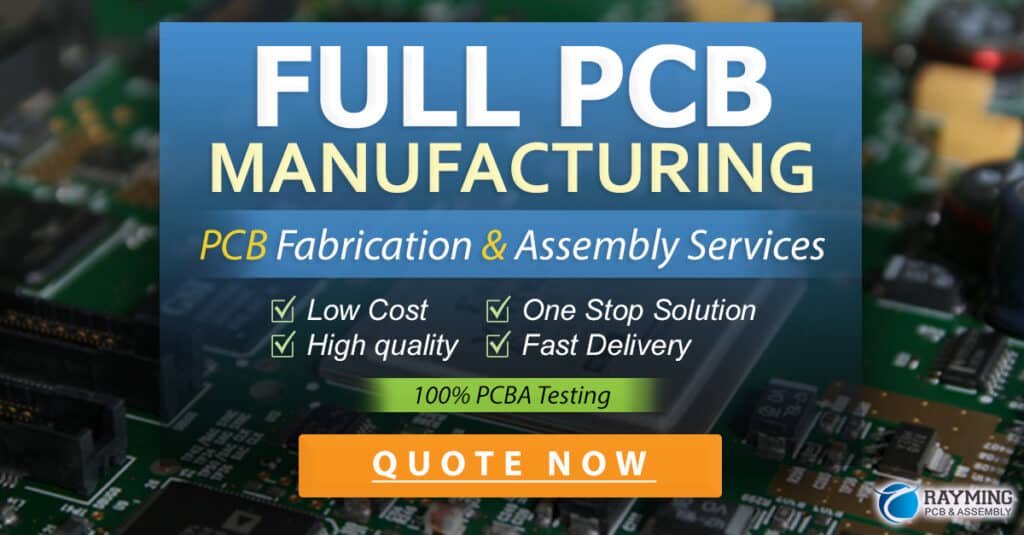
Tip 3: Assess the Manufacturer’s Quality Management System
The quality of your rigid-flex PCBs is critical to the performance and reliability of your end product. When evaluating potential manufacturers, assess their quality management system to ensure they have robust processes in place to maintain high standards throughout the manufacturing process.
A reputable rigid-flex PCB manufacturer should have:
- ISO 9001 certification for their quality management system
- IPC class 2 or 3 manufacturing capabilities, depending on your application requirements
- Automated optical inspection (AOI) and X-ray inspection systems for defect detection
- Electrical testing capabilities, such as flying probe and boundary scan testing
- Traceability and documentation controls for materials and processes
Tip 4: Consider the Manufacturer’s Technology Roadmap and Investment in Innovation
The rigid-flex PCB industry is constantly evolving, with new materials, processes, and design tools emerging to address the growing demands of advanced electronic applications. When choosing a rigid-flex PCB manufacturer, consider their technology roadmap and investment in innovation to ensure they can support your current and future needs.
A forward-thinking rigid-flex PCB manufacturer should:
- Invest in research and development to stay at the forefront of industry trends
- Continuously upgrade their manufacturing equipment and processes to improve capabilities and efficiency
- Collaborate with material suppliers and technology partners to introduce new solutions
- Provide value-added services, such as embedded components and 3D printed electronics
By partnering with a manufacturer that embraces innovation, you can benefit from the latest advancements in rigid-flex PCB technology and stay ahead of your competition.
Tip 5: Evaluate the Manufacturer’s Supply Chain Management and Lead Times
Effective supply chain management is critical to ensuring timely delivery and minimizing disruptions in your rigid-flex PCB production. When evaluating potential manufacturers, assess their supply chain management practices and lead times to ensure they can meet your project timelines and volume requirements.
A reliable rigid-flex PCB manufacturer should have:
- Strong relationships with raw material suppliers to ensure consistent quality and availability
- Robust inventory management systems to optimize stock levels and minimize lead times
- Flexible production scheduling to accommodate urgent orders and changes in demand
- Transparent communication regarding lead times and delivery status
- Contingency plans to mitigate potential supply chain risks
Tip 6: Assess the Manufacturer’s Environmental and Social Responsibility
As environmental and social concerns continue to grow, it is important to choose a rigid-flex PCB manufacturer that demonstrates a commitment to sustainability and ethical practices. Look for a manufacturer that actively works to minimize their environmental impact and ensures fair labor practices throughout their supply chain.
A socially and environmentally responsible rigid-flex PCB manufacturer should:
- Comply with international environmental standards, such as RoHS and REACH
- Implement eco-friendly manufacturing processes, such as lead-free soldering and waste reduction initiatives
- Conduct regular audits of their suppliers to ensure compliance with labor and environmental regulations
- Provide transparency regarding their environmental and social performance
- Actively participate in industry initiatives to promote sustainability and social responsibility
Tip 7: Evaluate the Manufacturer’s Customer Support and Communication
Effective communication and responsive customer support are essential for a successful rigid-flex PCB project. When choosing a manufacturer, evaluate their customer support infrastructure and communication channels to ensure they can provide the level of service you require.
A customer-centric rigid-flex PCB manufacturer should offer:
- Dedicated account management to serve as a single point of contact for your project
- Regular project updates and progress reports
- Prompt response to technical inquiries and design questions
- Seamless integration with your design team using collaborative tools and platforms
- Post-sales support for product performance and reliability issues
Tip 8: Consider the Manufacturer’s Geographical Location and Logistics Capabilities
The geographical location of your rigid-flex PCB manufacturer can have a significant impact on lead times, shipping costs, and communication efficiency. When selecting a manufacturer, consider their location and logistics capabilities to ensure they can meet your delivery requirements and provide cost-effective shipping options.
Factors to consider when evaluating a manufacturer’s location and logistics include:
- Proximity to your design and assembly facilities
- Availability of local support and technical resources
- Shipping options and transit times for prototype and production orders
- Customs and import/export regulations for international shipments
- Time zone differences and language barriers for effective communication
Tip 9: Compare Pricing and Cost-Benefit Analysis
While price is an important consideration when choosing a rigid-flex PCB manufacturer, it should not be the sole deciding factor. When comparing pricing, it is essential to conduct a comprehensive cost-benefit analysis that takes into account the manufacturer’s capabilities, quality, and value-added services.
Factors to consider in your cost-benefit analysis include:
- Material and manufacturing costs for your specific design and volume requirements
- Design support and engineering services included in the price
- Quality assurance and testing procedures to minimize defects and rework costs
- Lead times and expedited production options for time-sensitive projects
- Total cost of ownership, including shipping, inventory, and post-sales support
By carefully evaluating the cost-benefit of each potential manufacturer, you can select the one that offers the best overall value for your rigid-flex PCB project.
Conclusion
Choosing the right rigid-flex PCB manufacturer is crucial to the success of your project. By following these nine tips and carefully evaluating potential manufacturers based on their experience, capabilities, quality, and customer support, you can find the ideal partner to bring your rigid-flex PCB design to life.
Remember to prioritize manufacturers that offer comprehensive design support, robust quality management systems, and a commitment to innovation and sustainability. By building a strong relationship with your chosen manufacturer and leveraging their expertise, you can create high-quality, reliable rigid-flex PCBs that meet the demanding requirements of your application.
FAQs
1. What are the benefits of using rigid-flex PCBs?
Rigid-flex PCBs offer several benefits, including:
– Reduced weight and size compared to traditional rigid PCBs
– Improved reliability and durability in applications with vibration or flexing
– Enhanced signal integrity and reduced EMI/RFI issues
– Increased design flexibility for 3D packaging and space-constrained applications
– Simplified assembly and reduced interconnect costs
2. What industries commonly use rigid-flex PCBs?
Rigid-flex PCBs are used in various industries, such as:
– Aerospace and defense
– Medical devices
– Automotive electronics
– Consumer electronics
– Industrial automation
– Telecommunications
3. How do I determine if a rigid-flex PCB is the right choice for my application?
Consider using a rigid-flex PCB if your application requires:
– Compact packaging and space savings
– Flexibility and resistance to vibration or mechanical stress
– High reliability and durability in harsh environments
– Complex 3D geometries or multi-plane designs
– Reduced weight and improved portability
4. What design considerations are unique to rigid-flex PCBs?
When designing rigid-flex PCBs, consider the following:
– Material selection and stack-up design for optimal flexibility and reliability
– Bend radius and flex zone design to minimize stress on the flexible layers
– Placement of components and traces to avoid areas of high stress
– Use of strain relief features, such as stiffeners and anchors, to protect the flex zones
– Adherence to manufacturer-specific design guidelines and constraints
5. How can I ensure the long-term reliability of my rigid-flex PCBs?
To ensure the long-term reliability of your rigid-flex PCBs:
– Choose a reputable manufacturer with experience in rigid-flex PCB design and fabrication
– Carefully select materials and stack-up design based on your application requirements
– Incorporate strain relief features and follow best practices for flex zone design
– Conduct thorough testing and validation, including thermal cycling and mechanical stress tests
– Establish a robust quality assurance process with your manufacturer to minimize defects and variability
Factor | Consideration |
---|---|
Experience and Expertise | Look for a manufacturer with a proven track record in rigid-flex PCB fabrication |
Design Support Capabilities | Evaluate the manufacturer’s design support services, such as DFM analysis and stack-up design guidance |
Quality Management System | Assess the manufacturer’s quality certifications, inspection capabilities, and testing processes |
Technology Roadmap and Innovation | Consider the manufacturer’s investment in new technologies and value-added services |
Supply Chain Management | Evaluate the manufacturer’s supply chain practices, lead times, and risk mitigation strategies |
Environmental and Social Responsibility | Choose a manufacturer that demonstrates a commitment to sustainability and ethical practices |
Customer Support and Communication | Assess the manufacturer’s customer support infrastructure and communication channels |
Geographical Location and Logistics | Consider the manufacturer’s location, shipping options, and logistics capabilities |
Pricing and Cost-Benefit Analysis | Conduct a comprehensive cost-benefit analysis that takes into account the manufacturer’s capabilities and value-added services |
By carefully evaluating these factors and following the tips outlined in this article, you can select the right rigid-flex PCB manufacturer for your project and ensure the success of your application.
No responses yet