What is PCB Thermal Conductivity?
PCB (Printed Circuit Board) thermal conductivity refers to the ability of a PCB material to conduct heat. It is a measure of how efficiently heat can transfer through the PCB material from a high-temperature region to a low-temperature region. The thermal conductivity of a PCB is crucial because it determines how well the board can dissipate heat generated by the electronic components mounted on it.
The thermal conductivity of a material is expressed in terms of watts per meter-kelvin (W/mK). The higher the thermal conductivity value, the better the material is at conducting heat. For PCBs, the thermal conductivity is influenced by several factors, including:
- Material composition
- Thickness of the PCB
- Copper coverage
- Number of layers
- Presence of thermal vias
Typical PCB materials and their thermal conductivity values are shown in the table below:
Material | Thermal Conductivity (W/mK) |
---|---|
FR-4 | 0.3 – 0.4 |
High Tg FR-4 | 0.4 – 0.7 |
Polyimide | 0.2 – 0.3 |
Aluminum Backed PCB | 1.0 – 2.0 |
Copper Backed PCB | 50 – 400 |
Ceramic PCB | 20 – 150 |
Why is PCB Thermal Conductivity Important?
PCB thermal conductivity is essential for several reasons:
1. Component reliability
Electronic components generate heat during operation. If this heat is not effectively dissipated, it can lead to component failure or reduced lifespan. High temperatures can cause components to drift out of their specified operating parameters, leading to decreased performance and reliability.
2. System performance
Excessive heat can also affect the overall performance of an electronic system. As components heat up, their electrical characteristics can change, leading to signal integrity issues and reduced system performance. Effective heat dissipation through the PCB can help maintain optimal system performance.
3. Safety
In extreme cases, poor heat dissipation can lead to safety hazards such as fire or burns. If a component overheats and fails catastrophically, it can cause damage to the surrounding components and even start a fire. Ensuring proper thermal management through PCB design can help mitigate these safety risks.
Factors Affecting PCB Thermal Conductivity
Several factors can influence the thermal conductivity of a PCB:
1. Material selection
The choice of PCB material greatly impacts its thermal conductivity. Standard FR-4 PCBs have relatively low thermal conductivity, while metal-backed PCBs (such as aluminum or copper) offer much higher thermal conductivity. Ceramic PCBs also provide excellent thermal performance but at a higher cost.
2. Thickness
The thickness of the PCB can also affect its thermal conductivity. Thicker boards generally have better thermal conductivity than thinner boards due to the increased cross-sectional area for heat transfer. However, thicker boards also increase the overall weight and size of the PCB.
3. Copper coverage
The amount of copper on the PCB, both on the surface and within the layers, can influence its thermal conductivity. Copper is an excellent conductor of heat, so increasing the copper coverage can improve the PCB’s ability to dissipate heat. This can be achieved through techniques such as using thicker copper traces, increasing the number of copper layers, or using larger copper pours.
4. Number of layers
Multi-layer PCBs generally have better thermal conductivity than single-layer boards. This is because the additional layers provide more paths for heat to transfer through the board. However, the type of material used for the insulating layers between the copper layers also plays a role in the overall thermal conductivity.
5. Thermal vias
Thermal vias are small holes drilled through the PCB and plated with copper. They provide a direct path for heat to transfer from one side of the board to the other. By strategically placing thermal vias near heat-generating components, the thermal conductivity of the PCB can be improved.
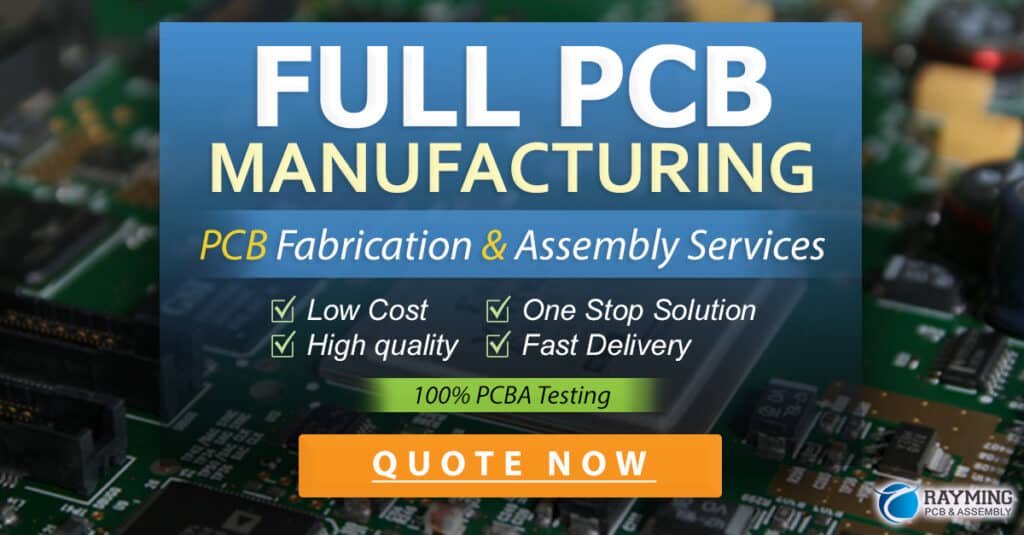
Techniques for Improving PCB Thermal Conductivity
There are several techniques that can be used to improve the thermal conductivity of a PCB:
1. Use of high thermal conductivity materials
Selecting PCB materials with high thermal conductivity, such as metal-backed or ceramic substrates, can significantly improve heat dissipation. These materials offer better thermal performance than standard FR-4 but come at a higher cost.
2. Increase copper coverage
Increasing the amount of copper on the PCB can improve its thermal conductivity. This can be achieved through:
- Using thicker copper traces
- Increasing the number of copper layers
- Using larger copper pours
- Placing copper fills in unused areas of the board
3. Optimize component placement
Strategically placing components on the PCB can help improve heat dissipation. Components that generate significant heat should be placed away from other heat-sensitive components and near areas of the board with better thermal conductivity, such as copper pours or thermal vias.
4. Use of thermal vias
Incorporating thermal vias into the PCB design can provide a direct path for heat to transfer from one side of the board to the other. Thermal vias should be placed near heat-generating components and in areas with poor thermal conductivity.
5. Consider external heat sinks
For components that generate significant amounts of heat, external heat sinks can be used to improve heat dissipation. Heat sinks are designed to efficiently transfer heat away from the component and into the surrounding air. They can be attached directly to the component or to the PCB near the component.
PCB Thermal Management Design Considerations
When designing a PCB with thermal management in mind, several key considerations should be taken into account:
1. Identify heat-generating components
The first step in PCB thermal management design is to identify the components that generate significant amounts of heat. These components may include power transistors, voltage regulators, microprocessors, and other high-power devices. By understanding which components are likely to generate the most heat, designers can focus their thermal management efforts on these areas.
2. Determine the maximum allowable temperature
Each component on the PCB will have a specified maximum operating temperature. It is essential to determine the maximum allowable temperature for each component to ensure that the PCB design can maintain temperatures within these limits. The maximum allowable temperature will depend on factors such as the component’s material properties, packaging, and expected lifespan.
3. Consider the operating environment
The environment in which the PCB will be operating can have a significant impact on its thermal performance. Factors such as ambient temperature, airflow, and humidity should be taken into account when designing for thermal management. For example, a PCB designed for use in a sealed enclosure with no airflow will require different thermal management strategies than a PCB designed for use in a well-ventilated environment.
4. Use thermal simulation software
Thermal simulation software can be a valuable tool in PCB thermal management design. These tools allow designers to model the thermal performance of a PCB and identify potential hot spots before the board is manufactured. By using thermal simulation, designers can optimize component placement, copper coverage, and other factors to improve the PCB’s overall thermal conductivity.
5. Plan for manufacturing and assembly
When designing a PCB for thermal management, it is important to consider the manufacturing and assembly processes. Some thermal management techniques, such as using thicker copper traces or incorporating thermal vias, may require specialized manufacturing capabilities. Designers should work closely with their PCB manufacturer to ensure that the design can be effectively manufactured and assembled.
FAQs
1. What is the difference between thermal conductivity and thermal resistance?
Thermal conductivity is a material property that describes how well a material conducts heat, while thermal resistance is a measure of how much a material opposes the flow of heat. Thermal resistance is the reciprocal of thermal conductivity and is often used to describe the thermal performance of a PCB or component package.
2. Can I use thermal paste on a PCB?
Thermal paste, also known as thermal interface material (TIM), is typically used to improve the thermal contact between a component and a heat sink. While thermal paste can be used on a PCB, it is not common practice. Instead, designers typically rely on techniques such as thermal vias, copper pours, and high thermal conductivity materials to improve the PCB’s thermal performance.
3. How do I know if my PCB has good thermal conductivity?
There are several ways to assess the thermal conductivity of a PCB:
- Use thermal simulation software to model the PCB’s thermal performance
- Measure the temperature of components on the PCB during operation using thermocouples or infrared cameras
- Compare the PCB material and design characteristics (such as copper coverage and thermal vias) to industry standards and best practices
4. Can I use a metal core PCB for all my designs?
Metal core PCBs (MCPCBs) offer excellent thermal conductivity but may not be suitable for all designs. MCPCBs are typically more expensive than standard FR-4 PCBs and may have limitations in terms of routing density and component compatibility. Designers should carefully consider the thermal requirements and cost constraints of their specific application before deciding to use an MCPCB.
5. How do I choose the right heat sink for my PCB?
When selecting a heat sink for a PCB, designers should consider factors such as:
- The amount of heat generated by the component
- The maximum allowable temperature of the component
- The available space on the PCB
- The airflow and environmental conditions in which the PCB will be operating
Heat sink manufacturers often provide thermal performance data and selection guides to help designers choose the right heat sink for their specific application.
Conclusion
PCB thermal conductivity is a critical factor in the design and performance of electronic systems. By understanding the factors that influence PCB thermal conductivity and using appropriate design techniques, designers can create PCBs that effectively dissipate heat and maintain optimal component temperatures. This, in turn, leads to improved system reliability, performance, and safety.
When designing for thermal management, it is essential to consider factors such as material selection, copper coverage, component placement, and the use of thermal vias. Thermal simulation software can be a valuable tool for optimizing PCB thermal performance, and designers should work closely with their PCB manufacturer to ensure that their designs can be effectively manufactured and assembled.
By prioritizing PCB thermal conductivity and thermal management in the design process, engineers can create electronic systems that are reliable, high-performing, and safe. As electronic systems continue to become more complex and power-dense, the importance of effective thermal management will only continue to grow. By staying up-to-date with the latest techniques and best practices in PCB thermal design, engineers can ensure that their products are well-positioned to meet the challenges of the future.
No responses yet